Fungi Studies
Fungi Studies
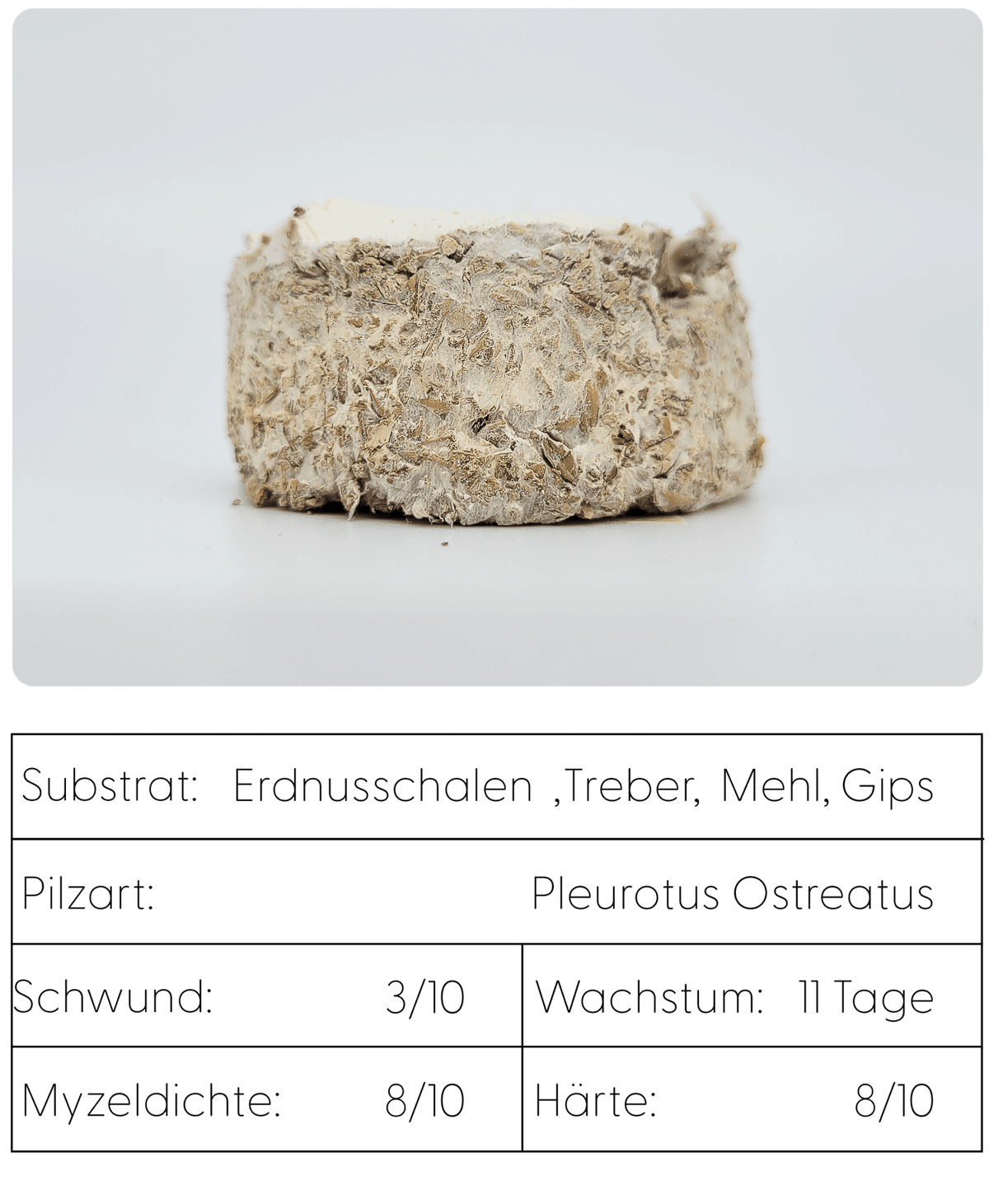
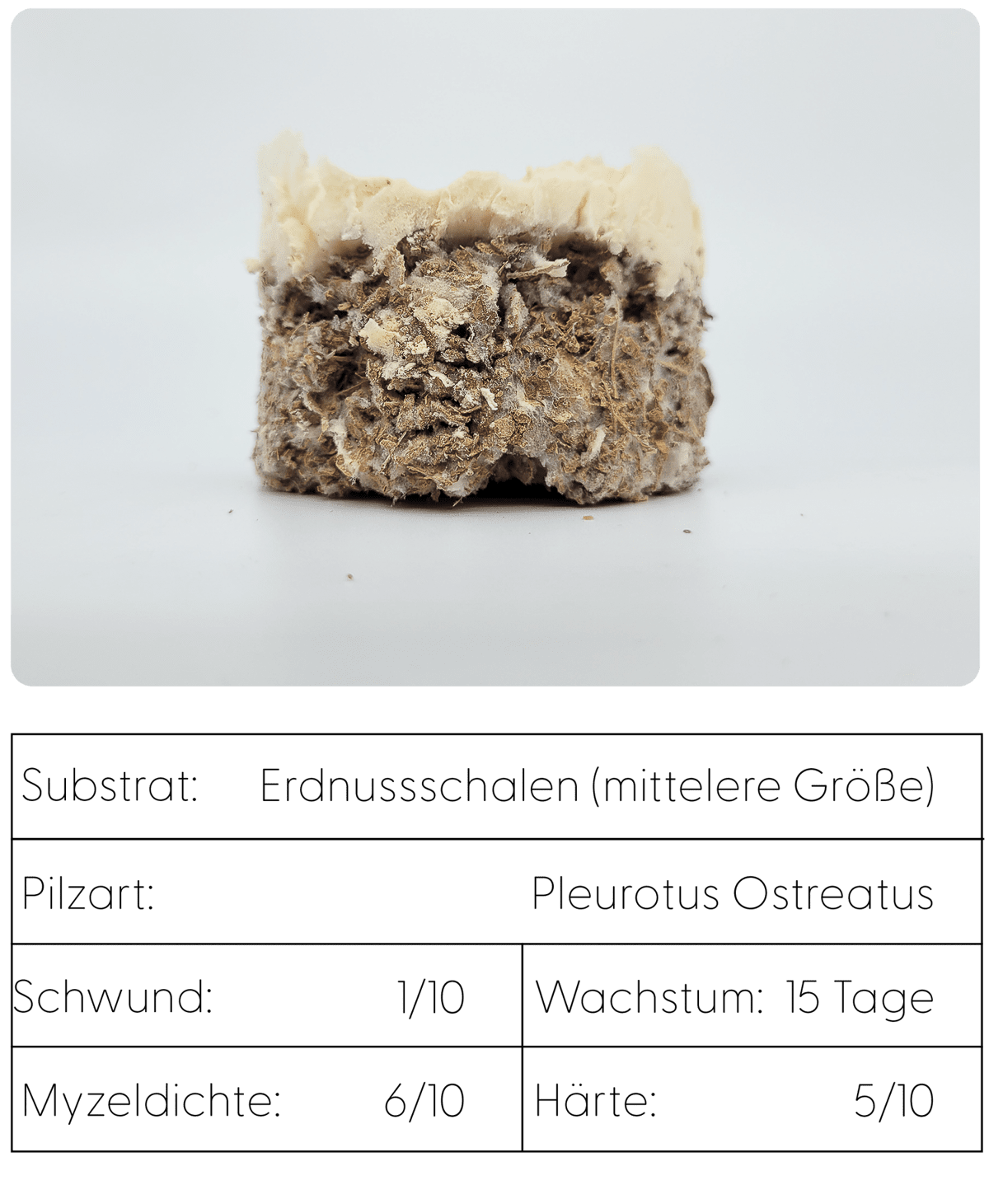
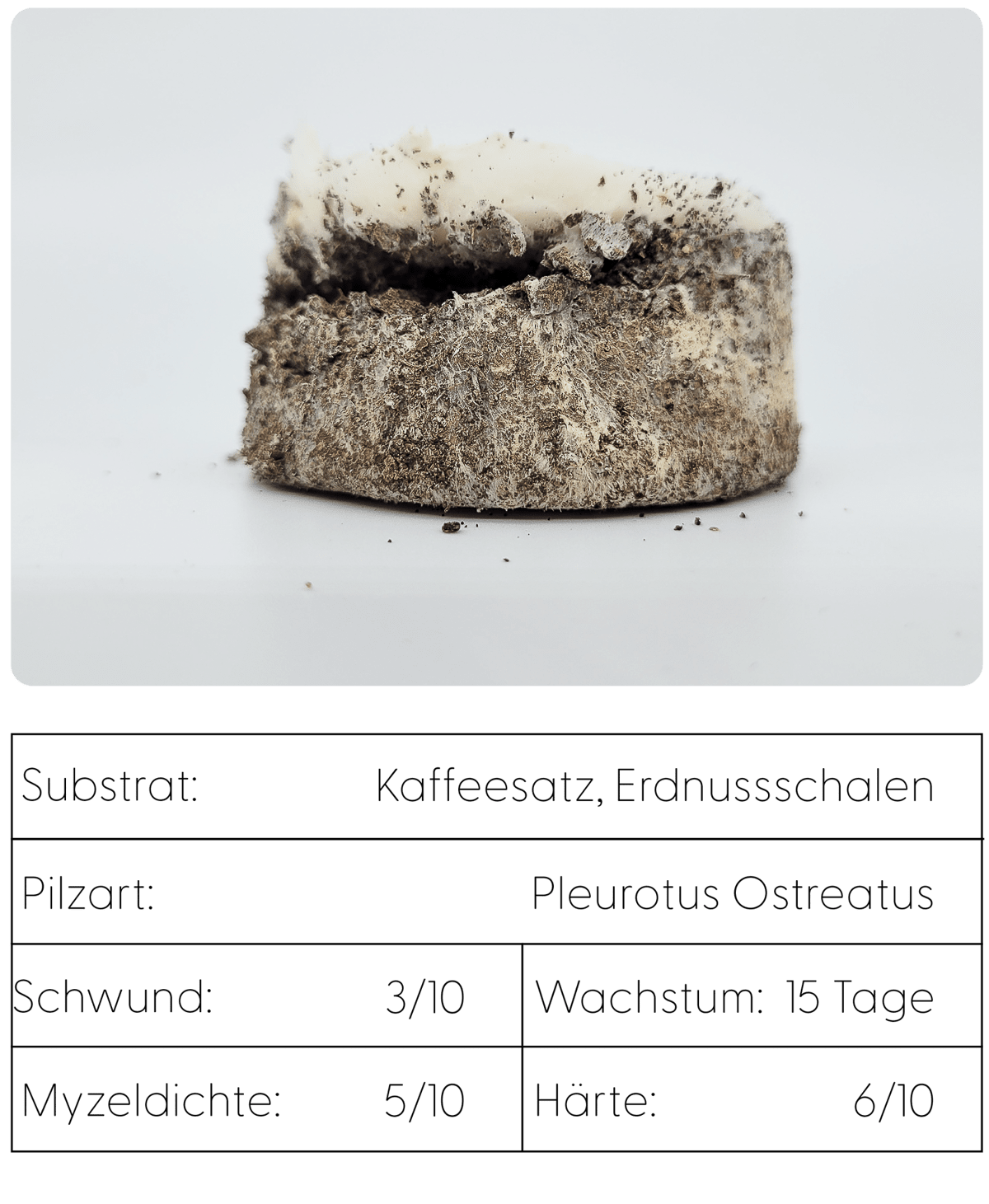
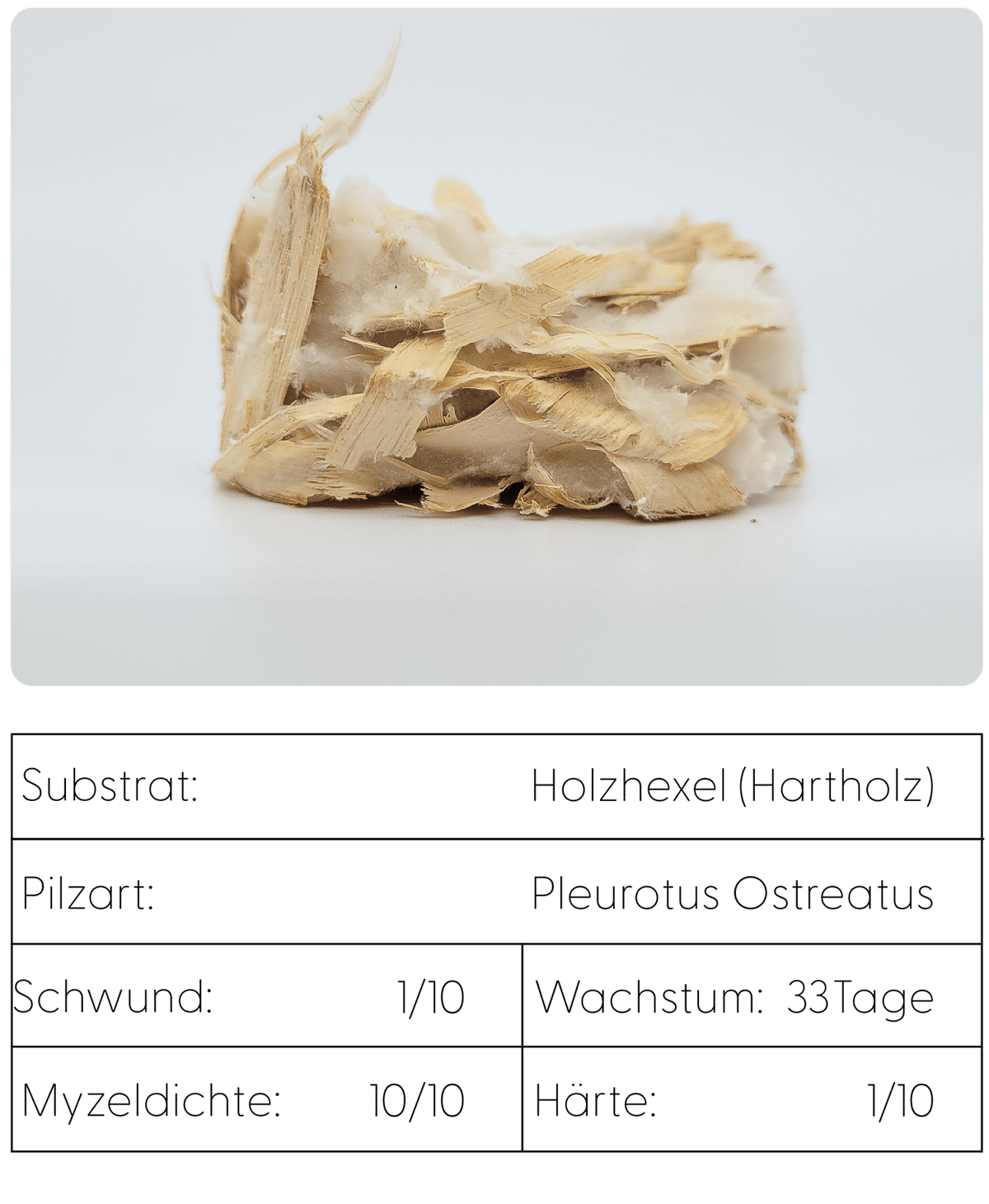
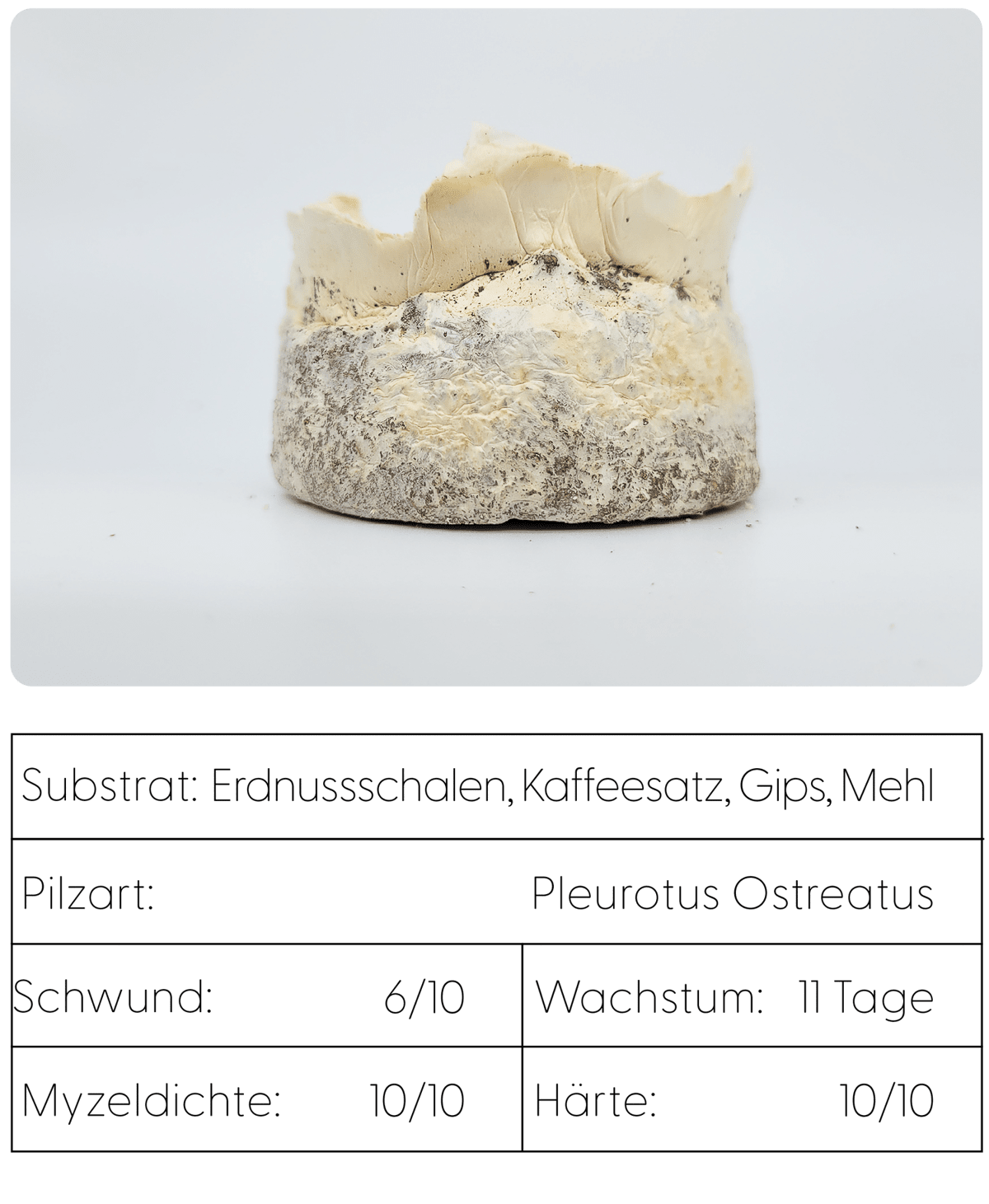
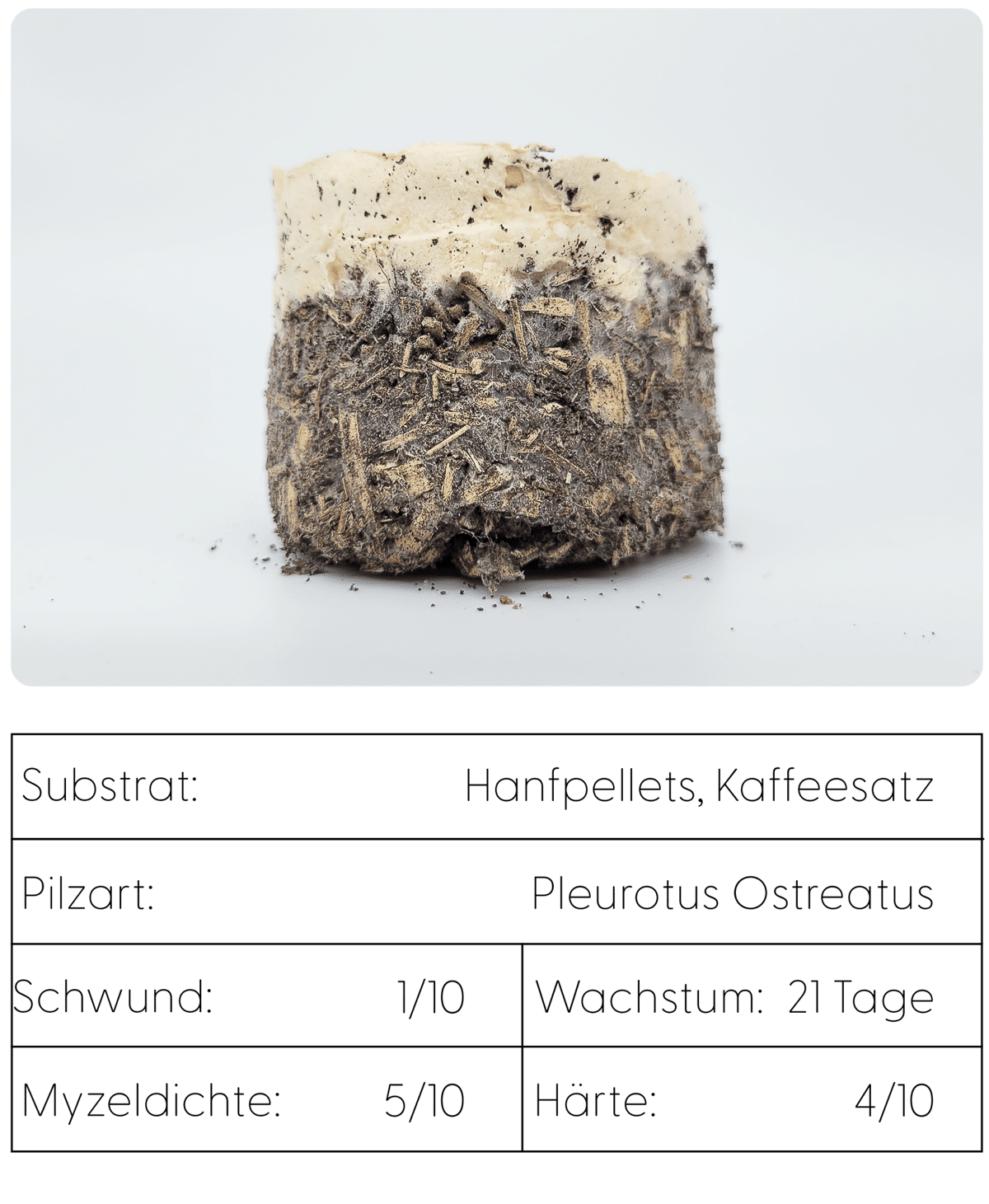
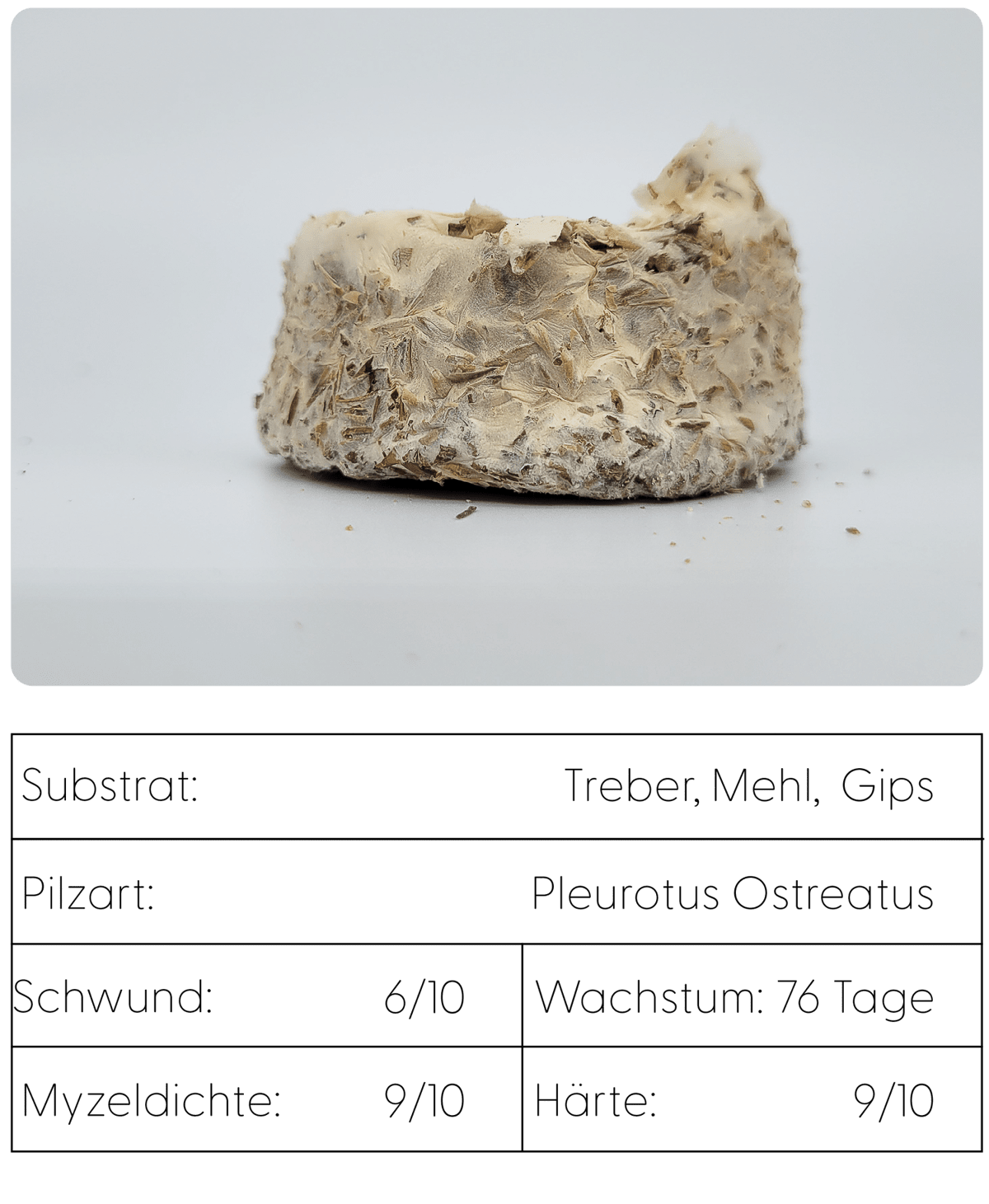
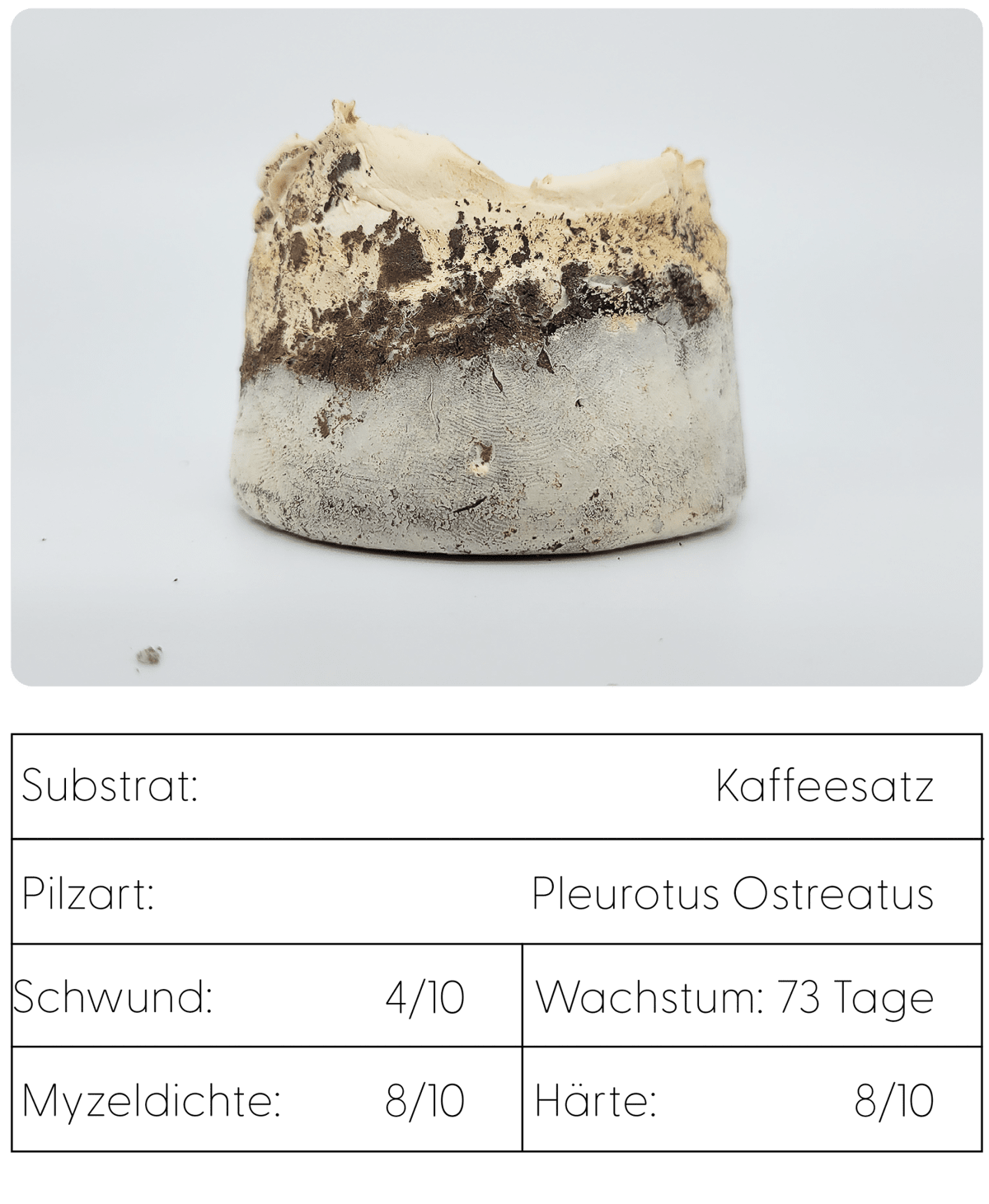
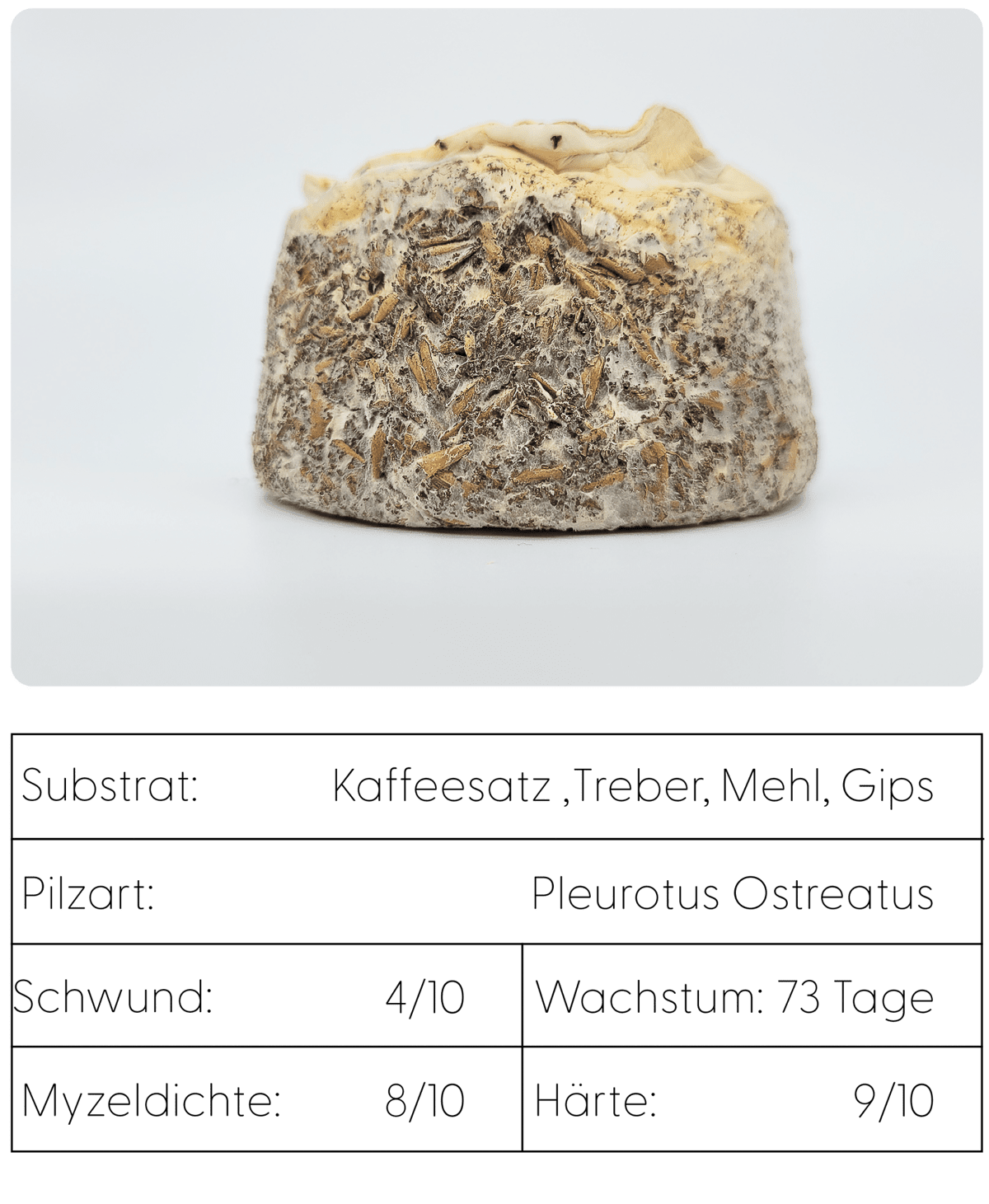
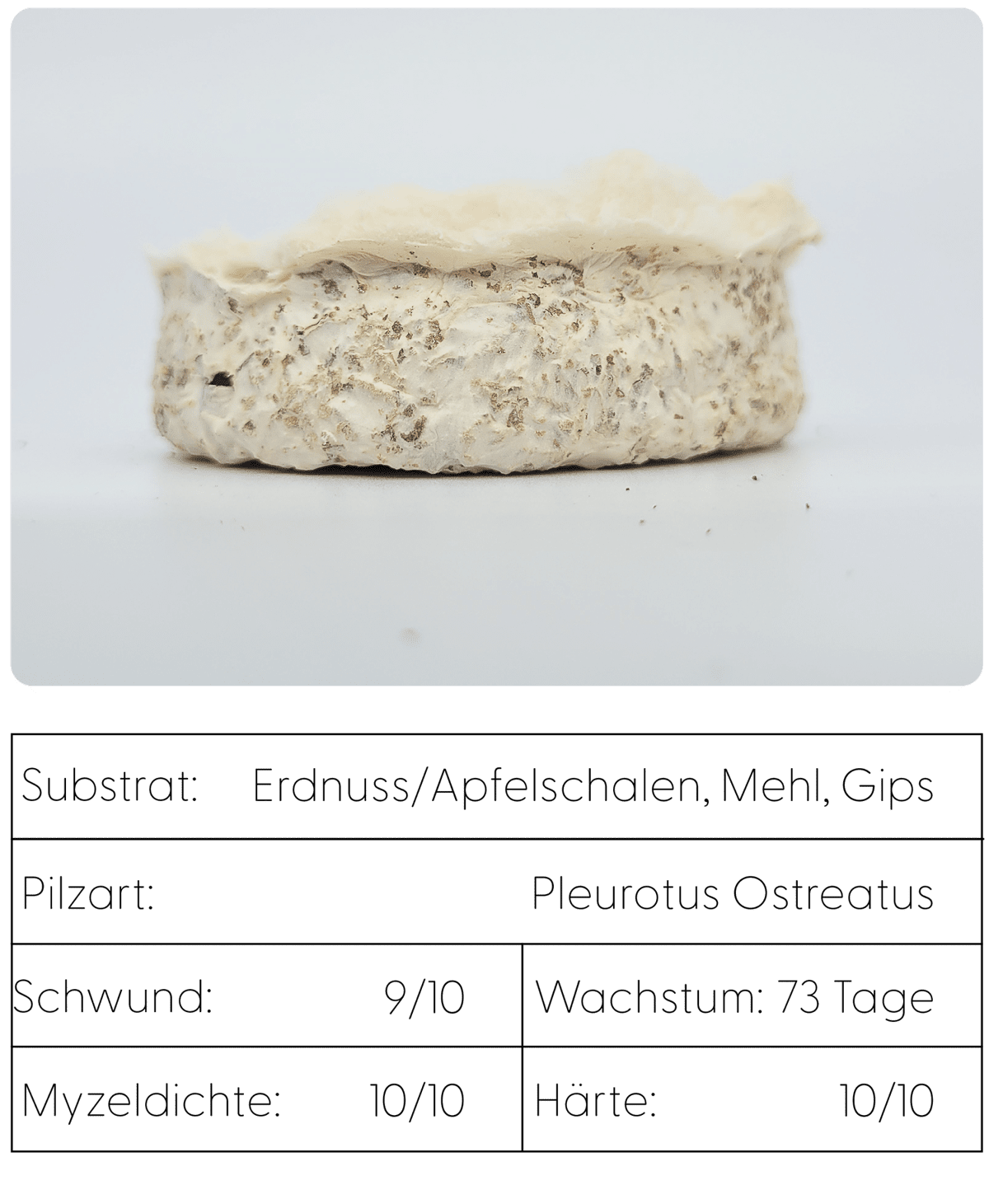
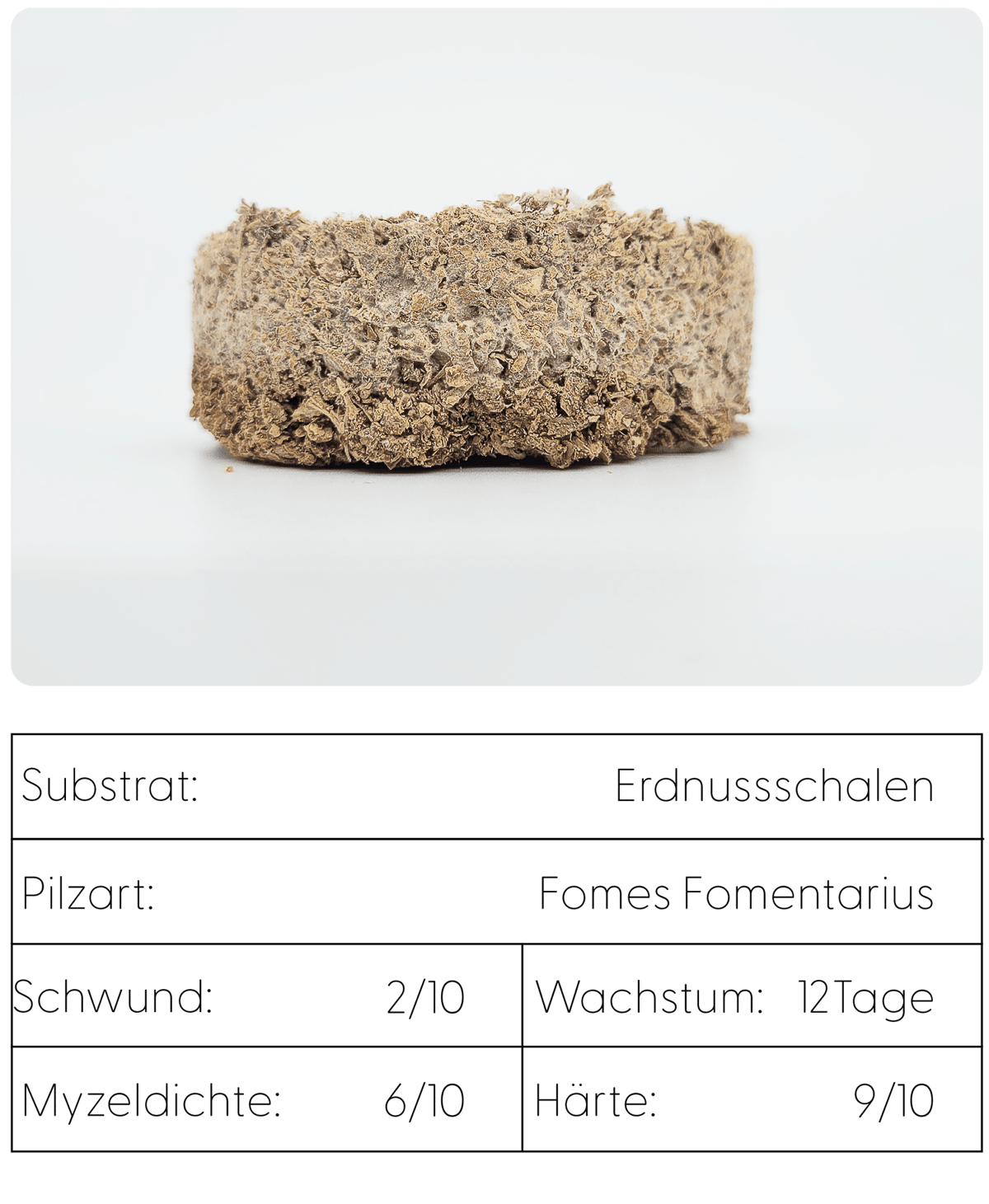
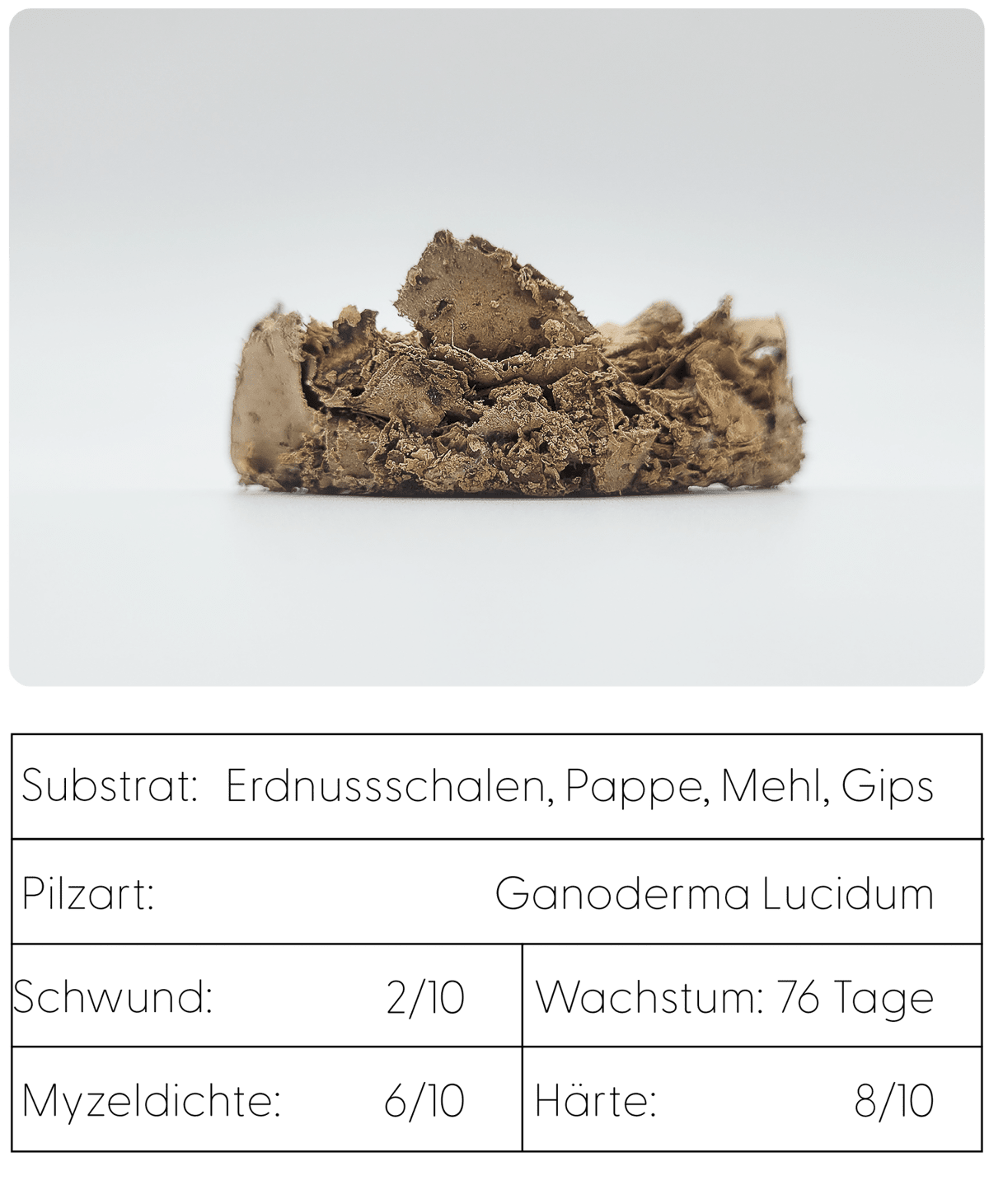
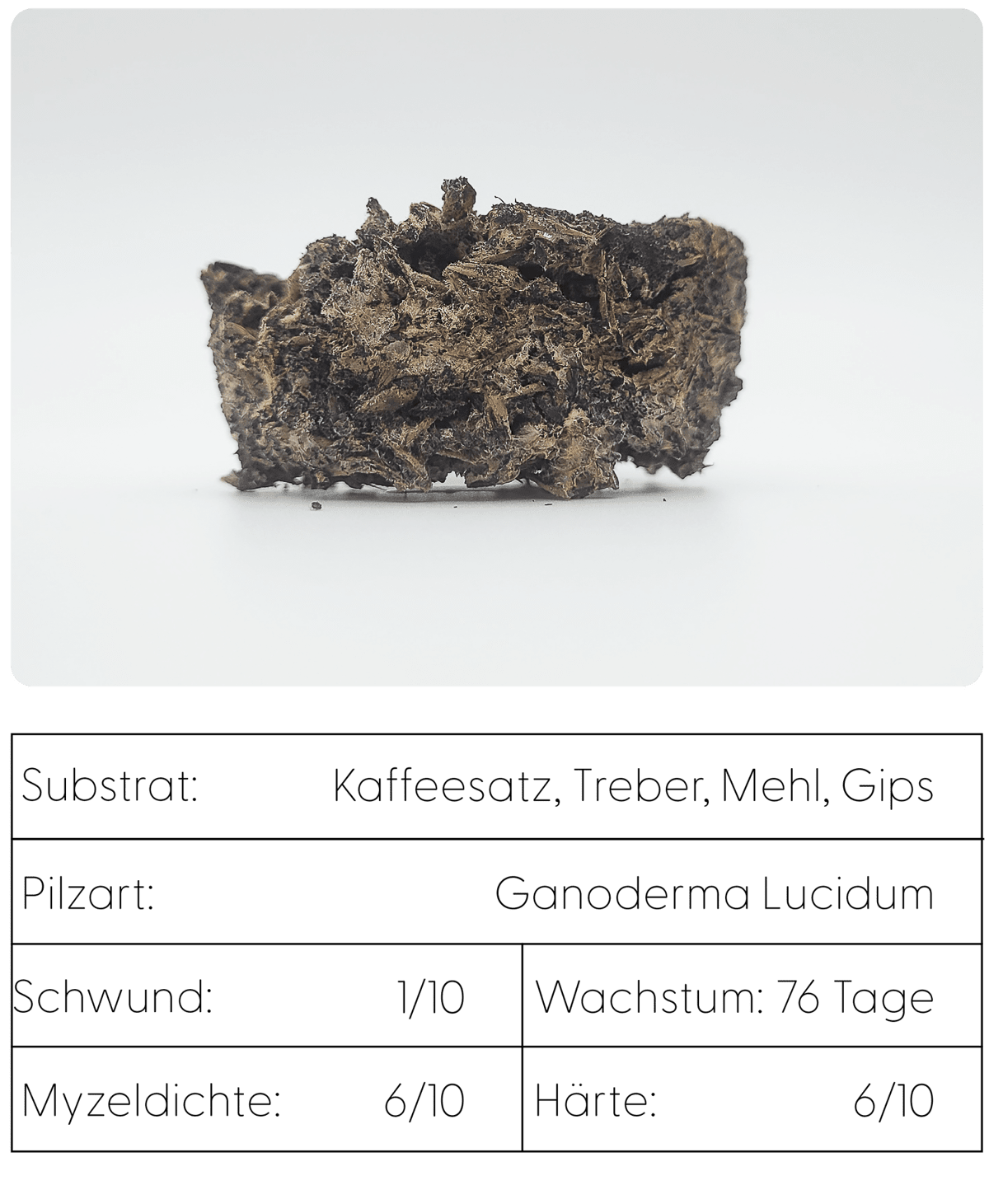
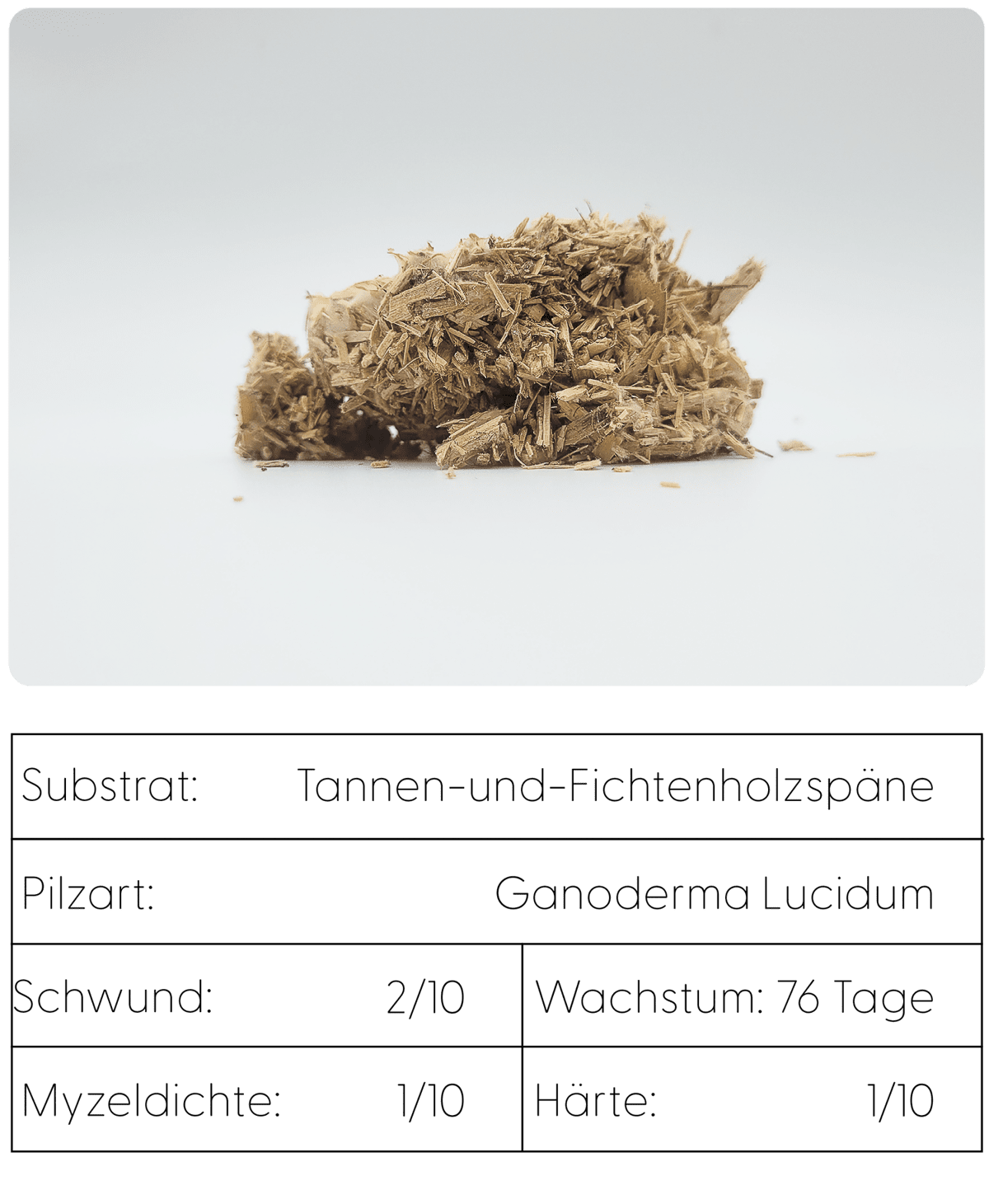
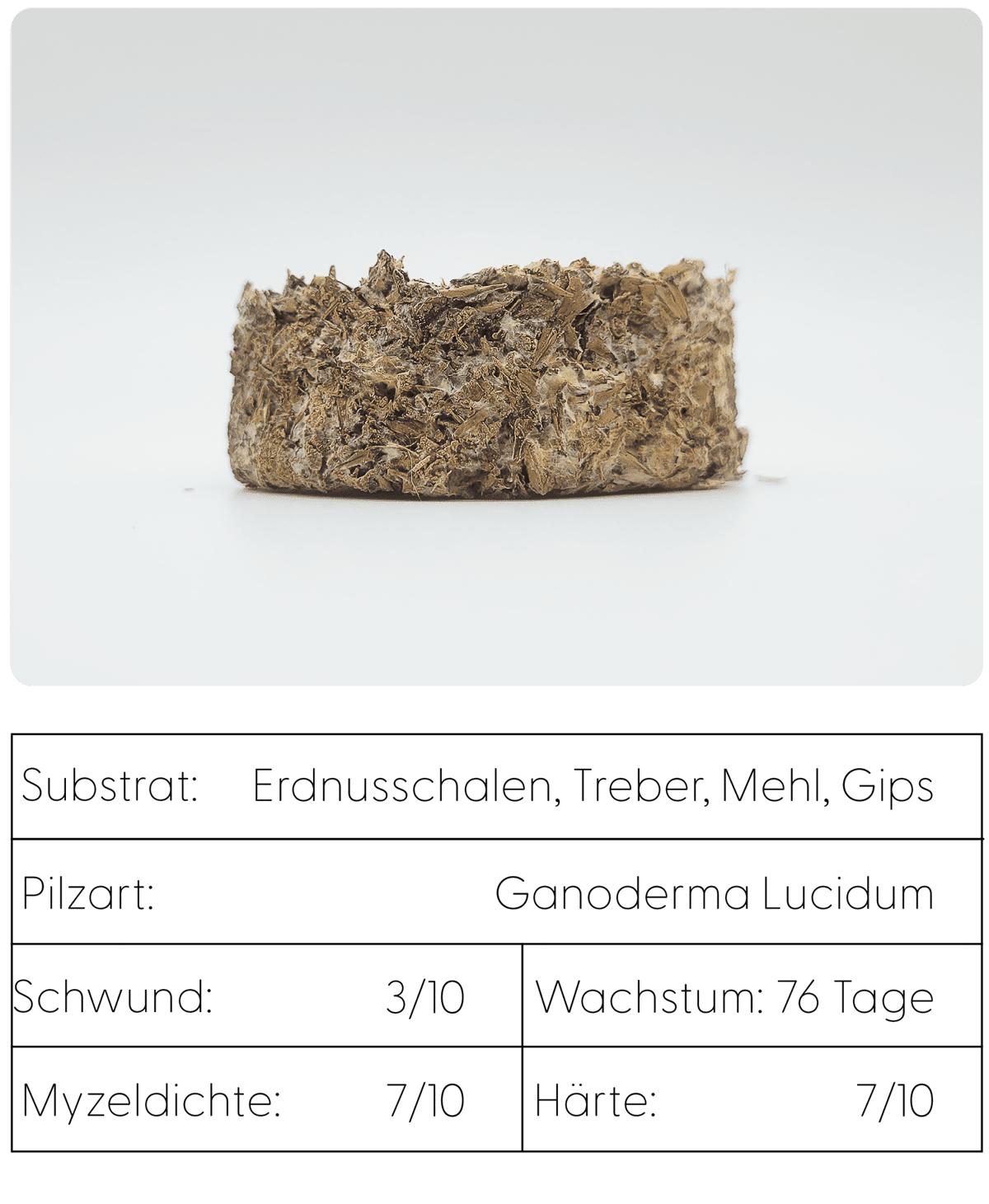
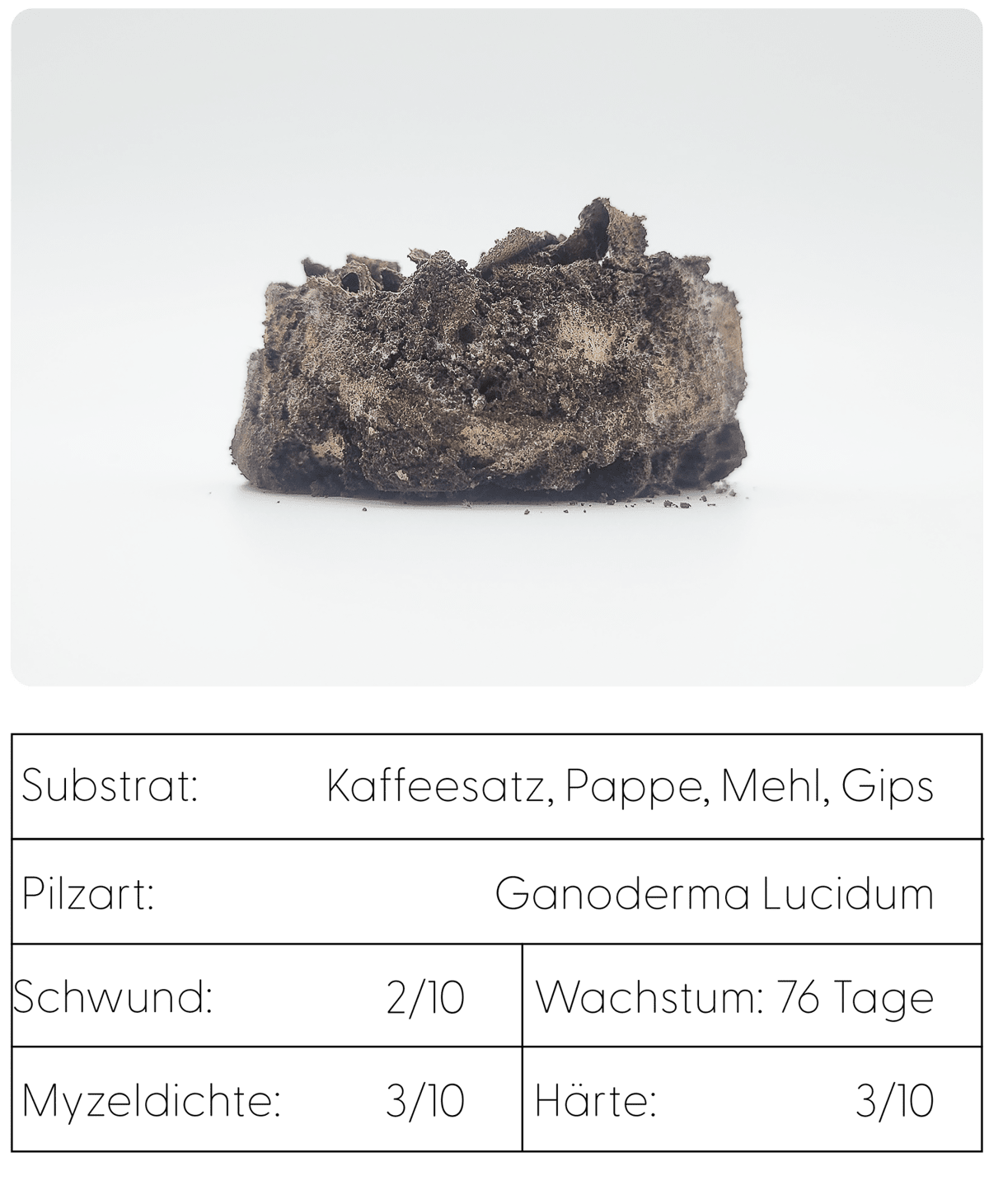
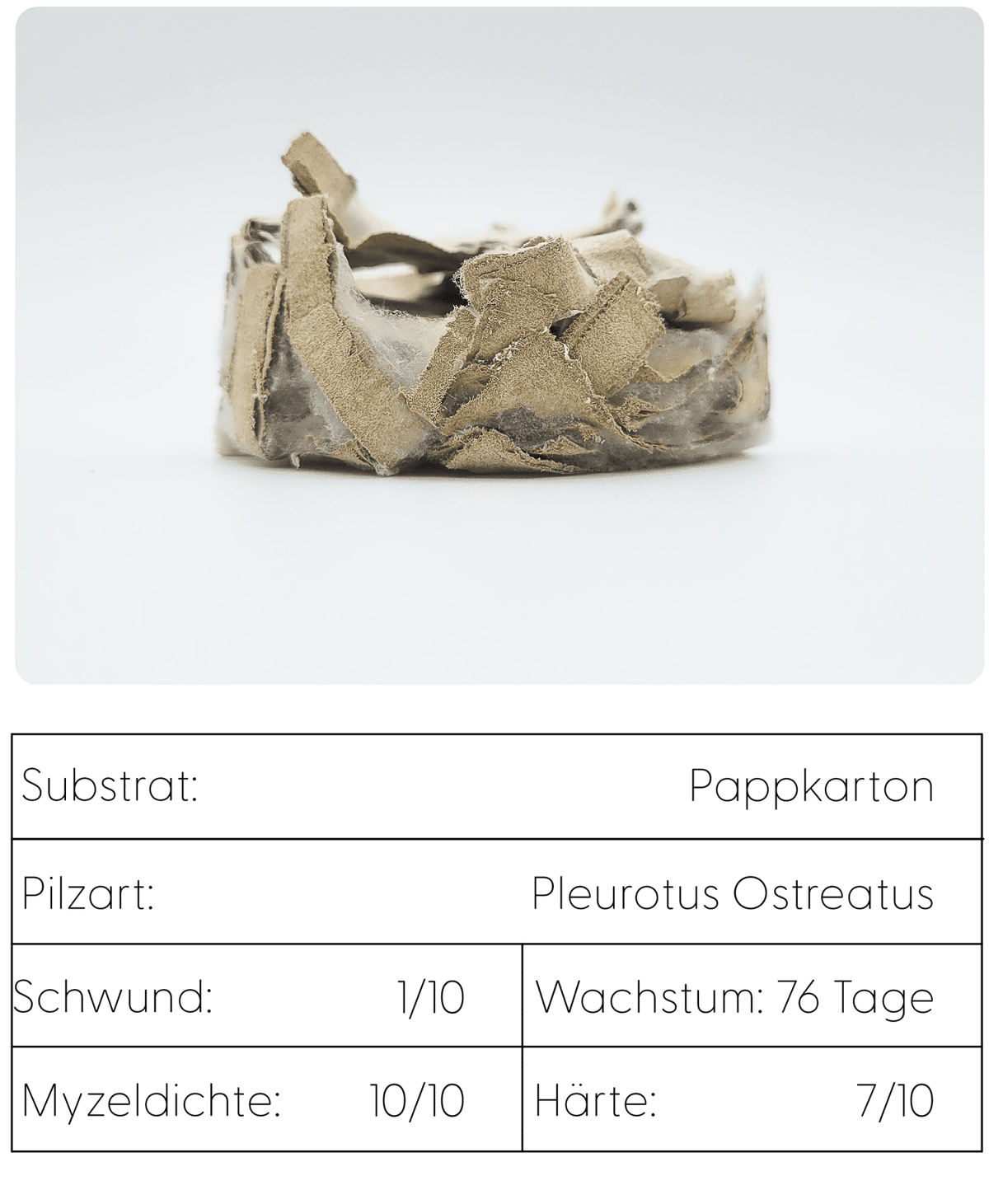
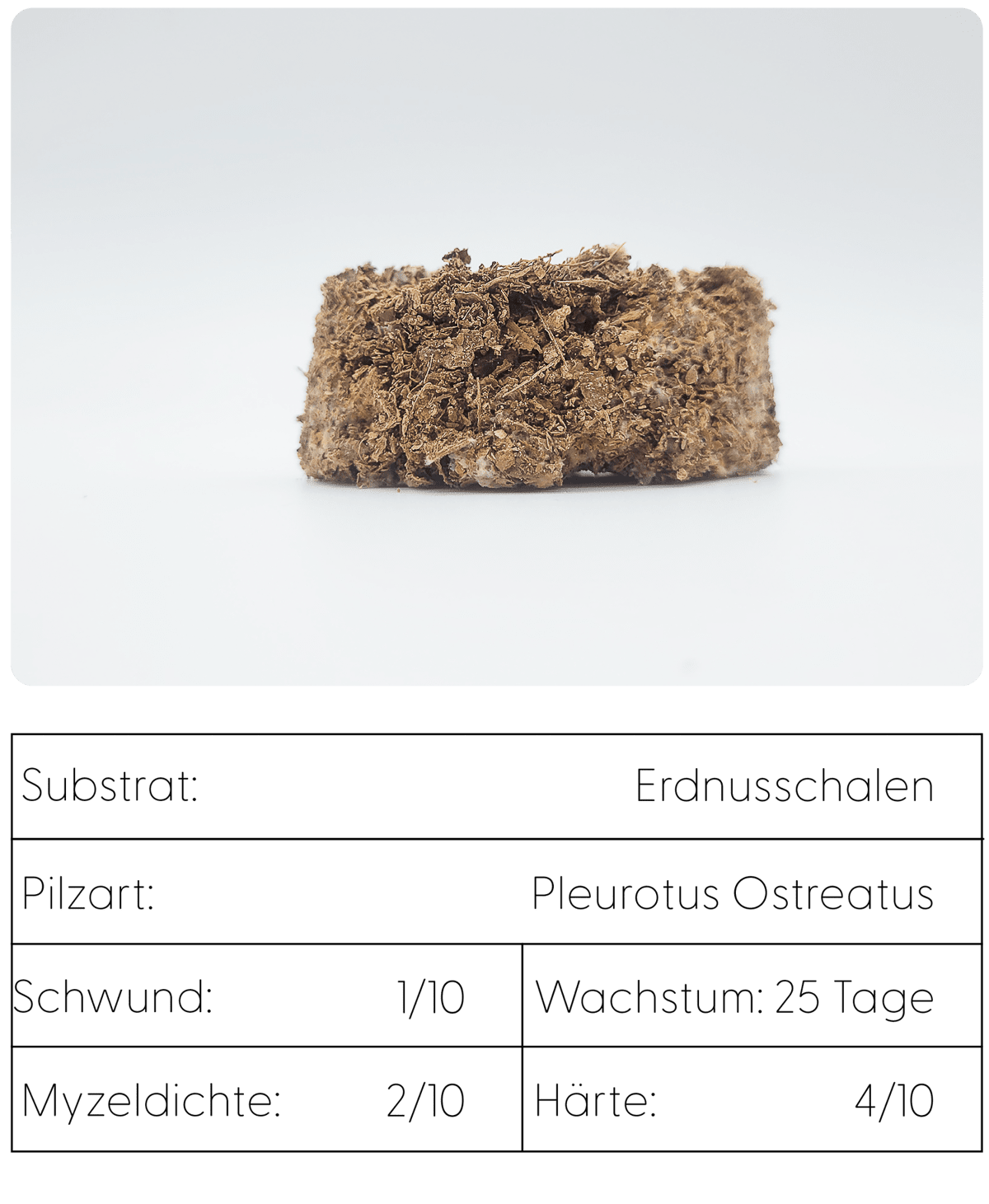
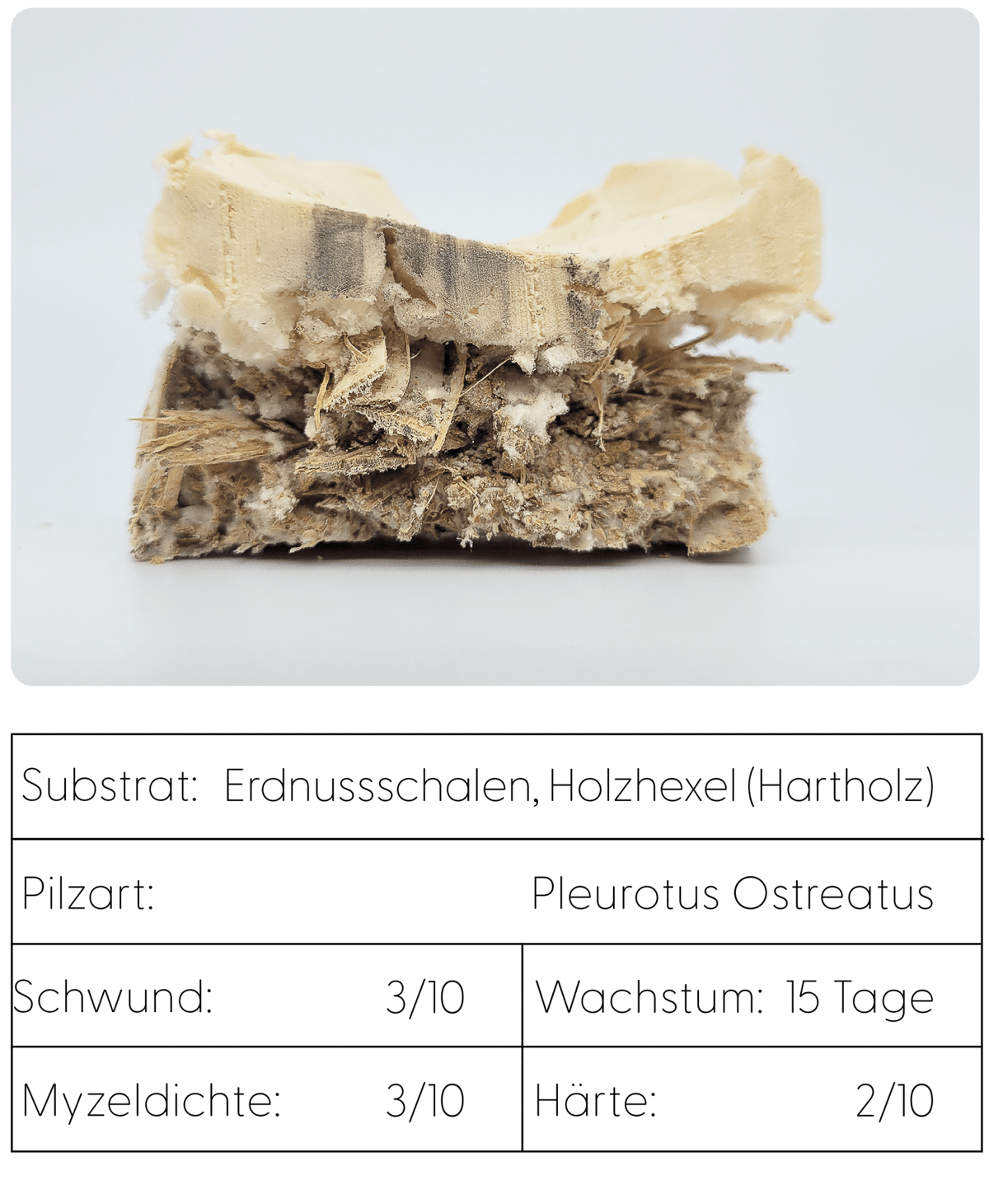
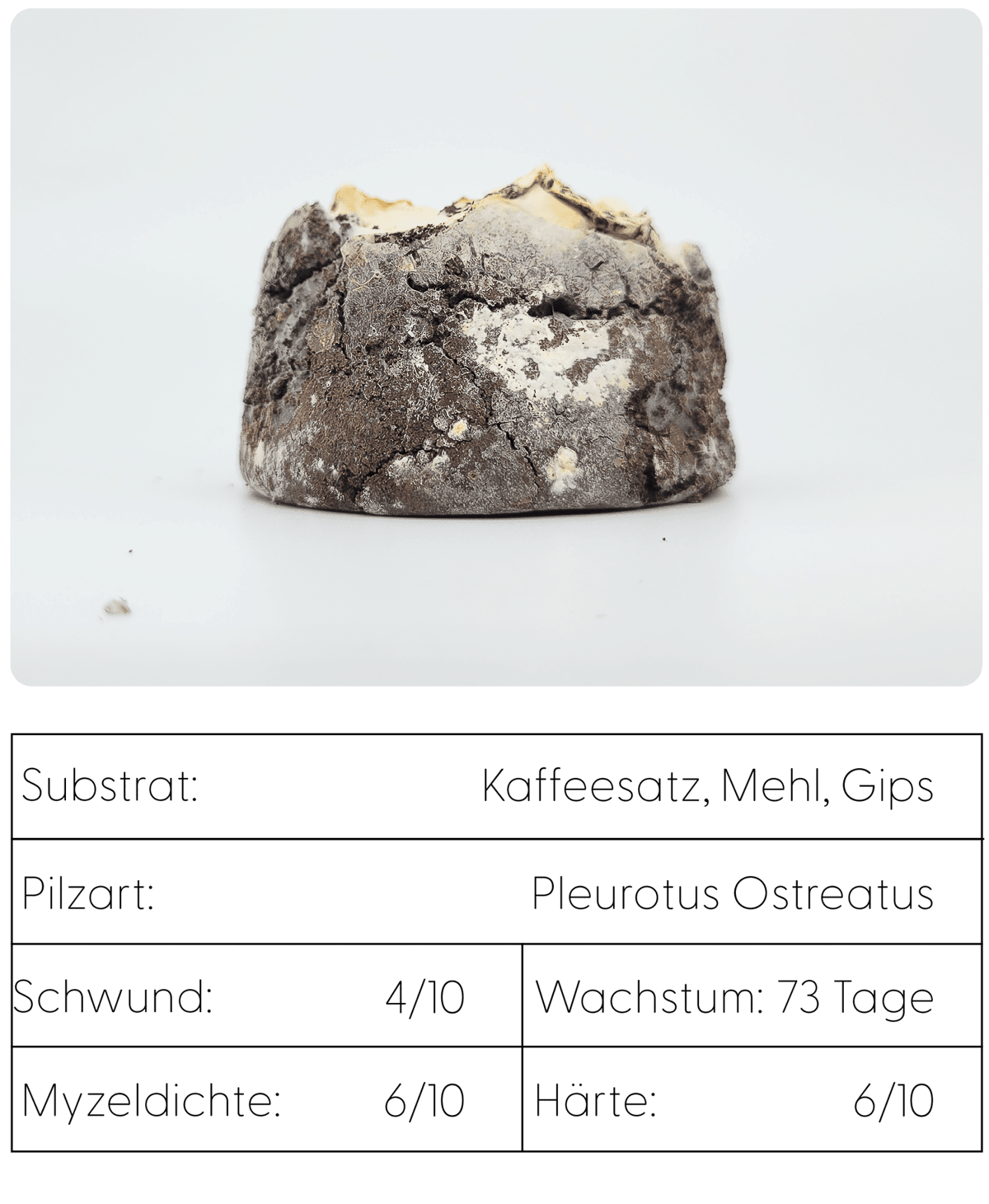
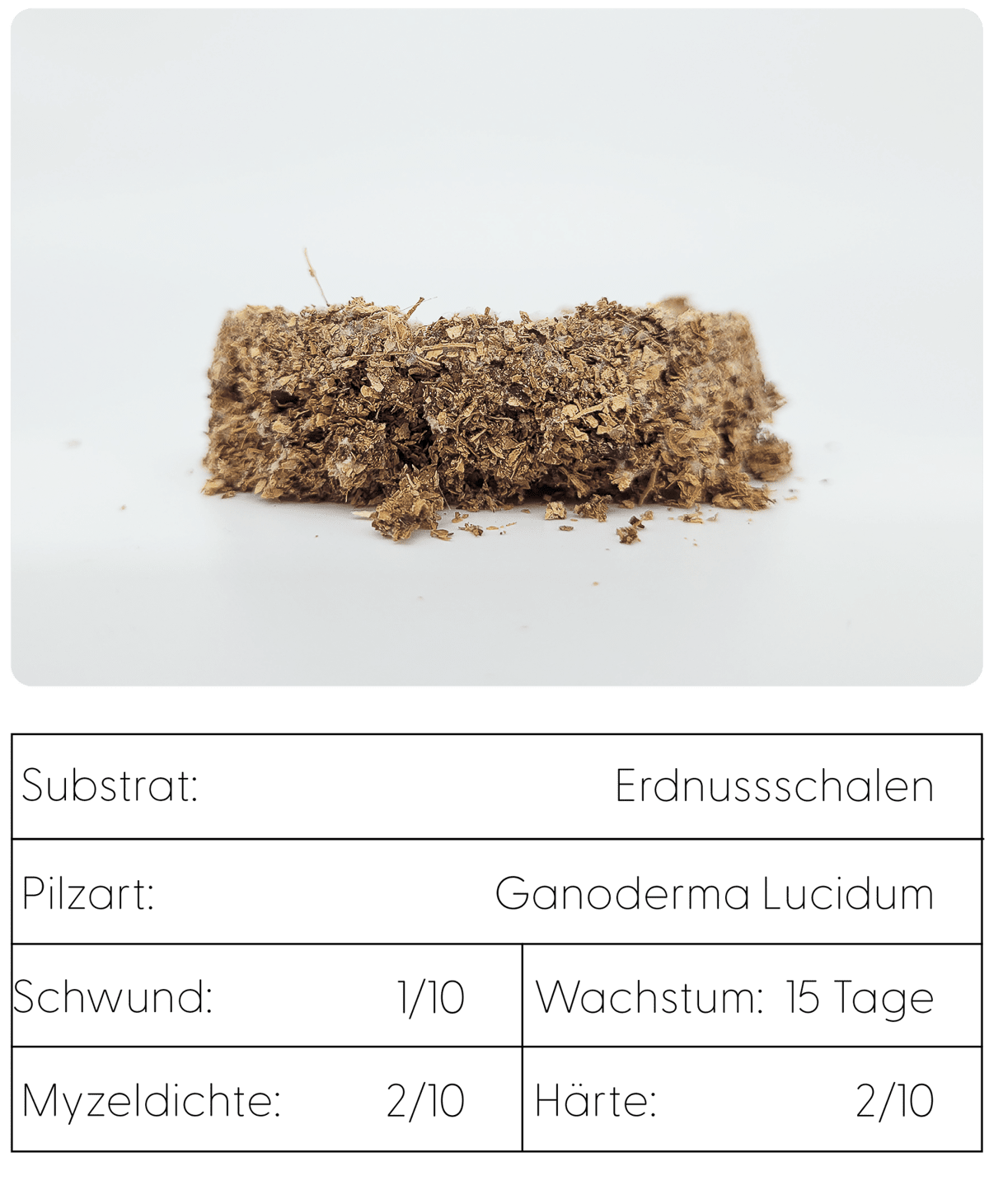
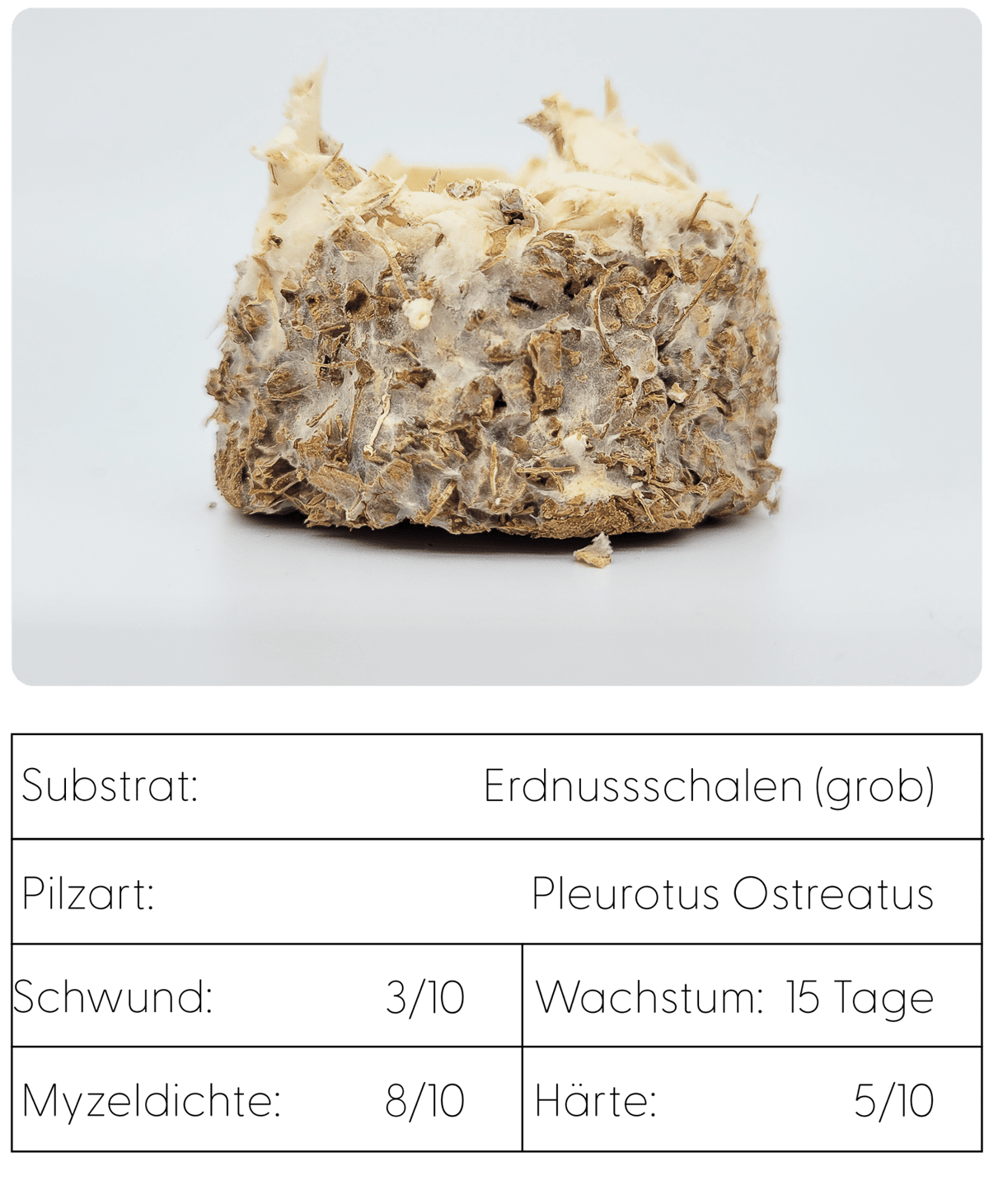
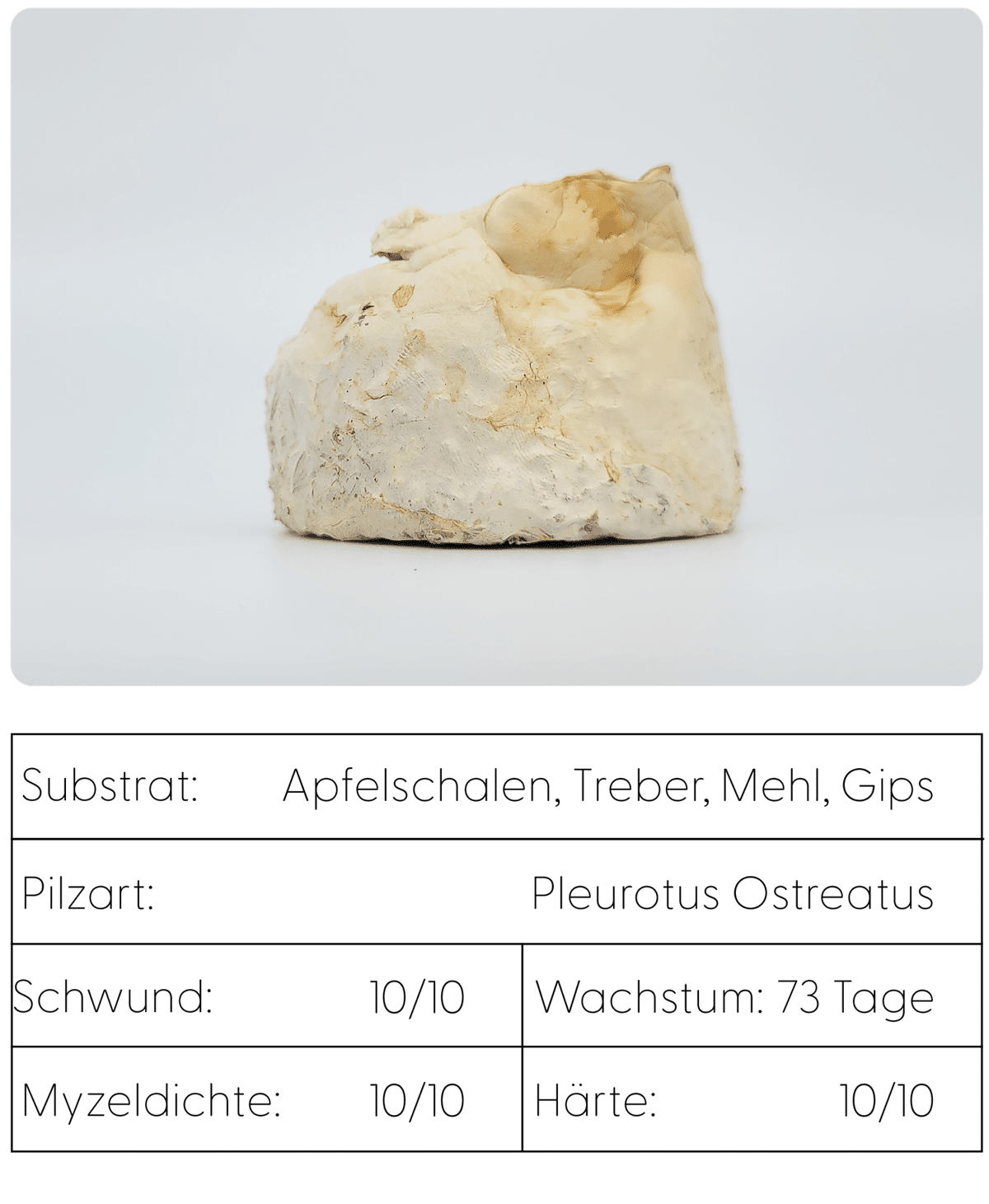
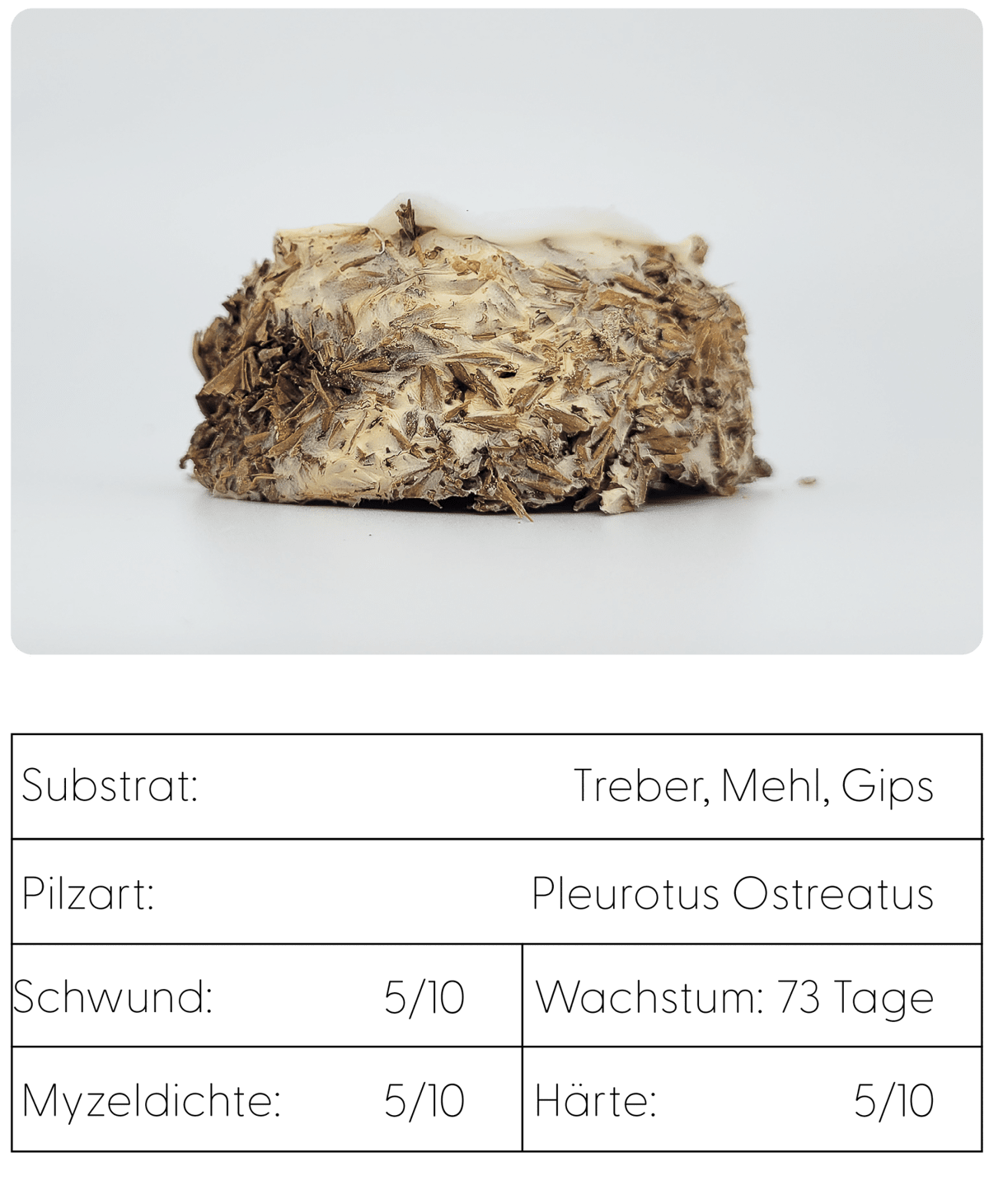
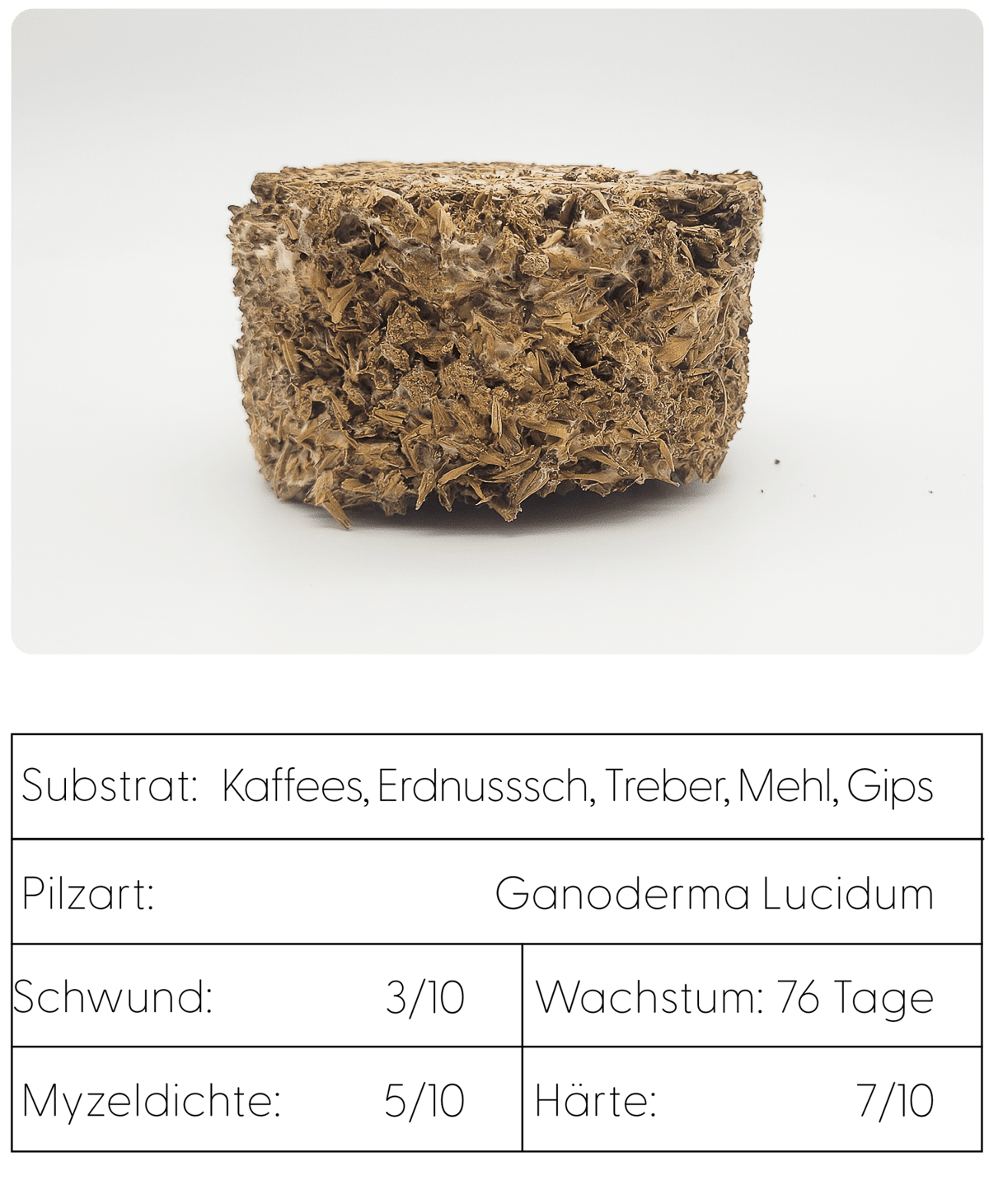
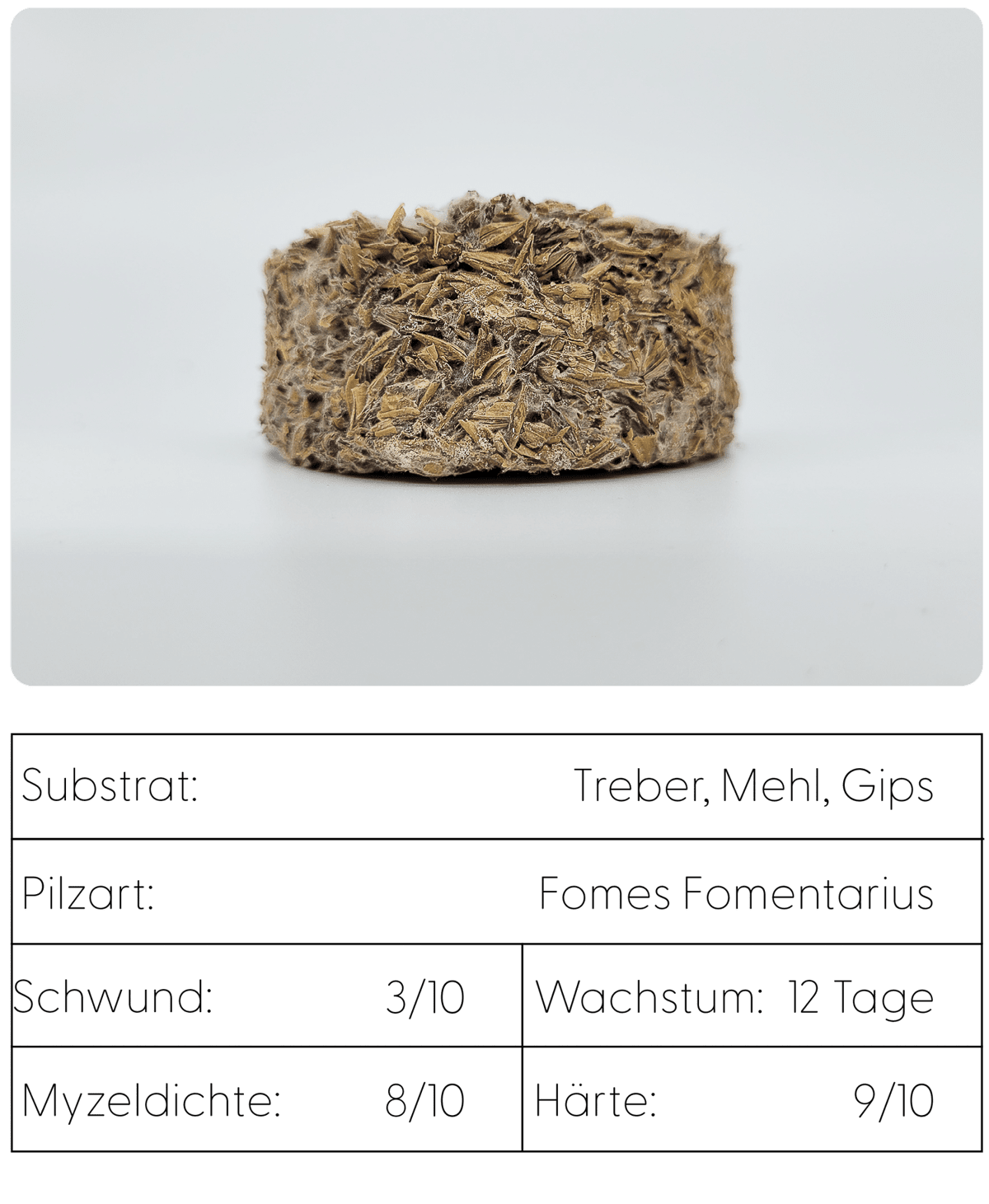
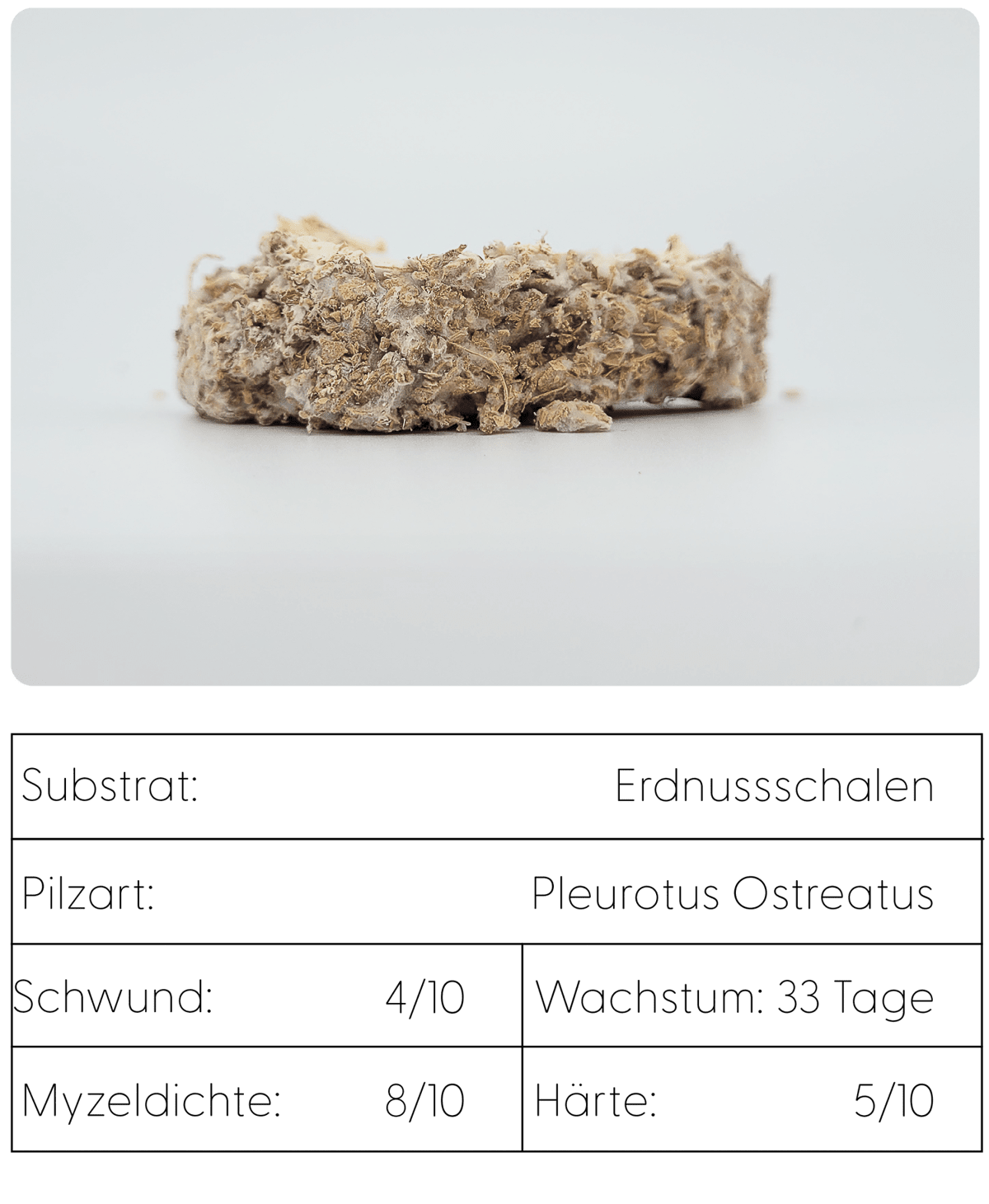
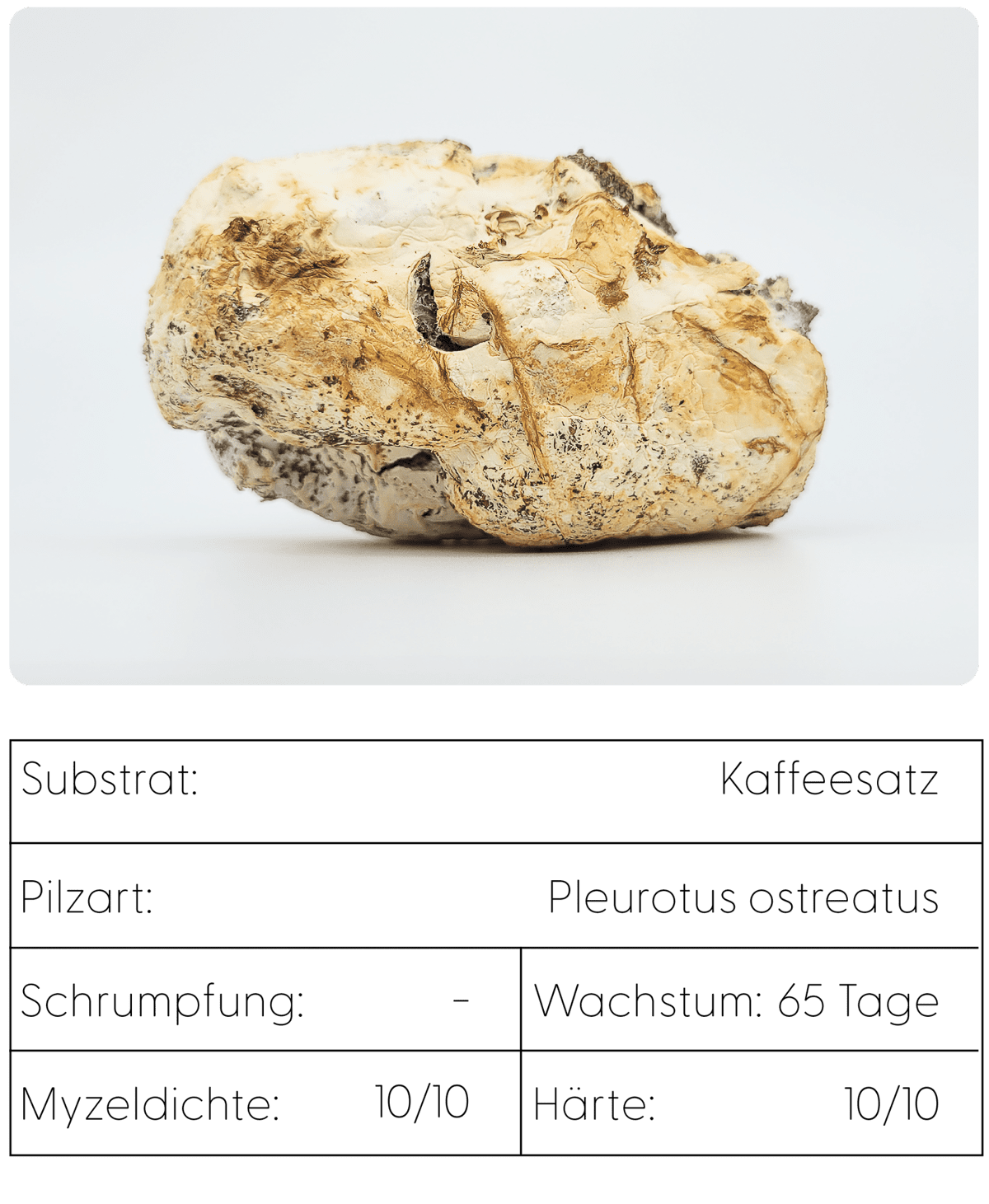
Intent
I started this project because I am fascinated by the idea of working with living, growing organisms to produce sustainable materials. As one of these materials, mycelium has gained popularity in recent years due to its awesome material abilities, such as temperature- and sound-insulation properties, its toughness compared to its low weight, and the fact that it is completely biodegradable. Because a good friend and fellow student of mine, Clemens Domsch, was interested in this topic too, we initiated it as a group project.
.png)
.png)
.png)
What is mycelium?
In general, the word fungus is used to describe the visible fruiting body of fungi. Mycelium is the sum of all hyphae (the thread-like cells) of a fungus. In addition to plants and animals, fungi form the third major kingdom of eukaryotic organisms (organisms with a cell nucleus). Unlike plants, they cannot perform synthesis. They therefore take up their food in dissolved form from their environment. The diversity of species ranges from complex, multicellular organisms to single-celled organisms like baker's yeast. In nature, fungi are essential for the maintenance of ecosystems. They form symbioses with plants and provide them with important nutrients, such as phosphate, which they need for their growth.
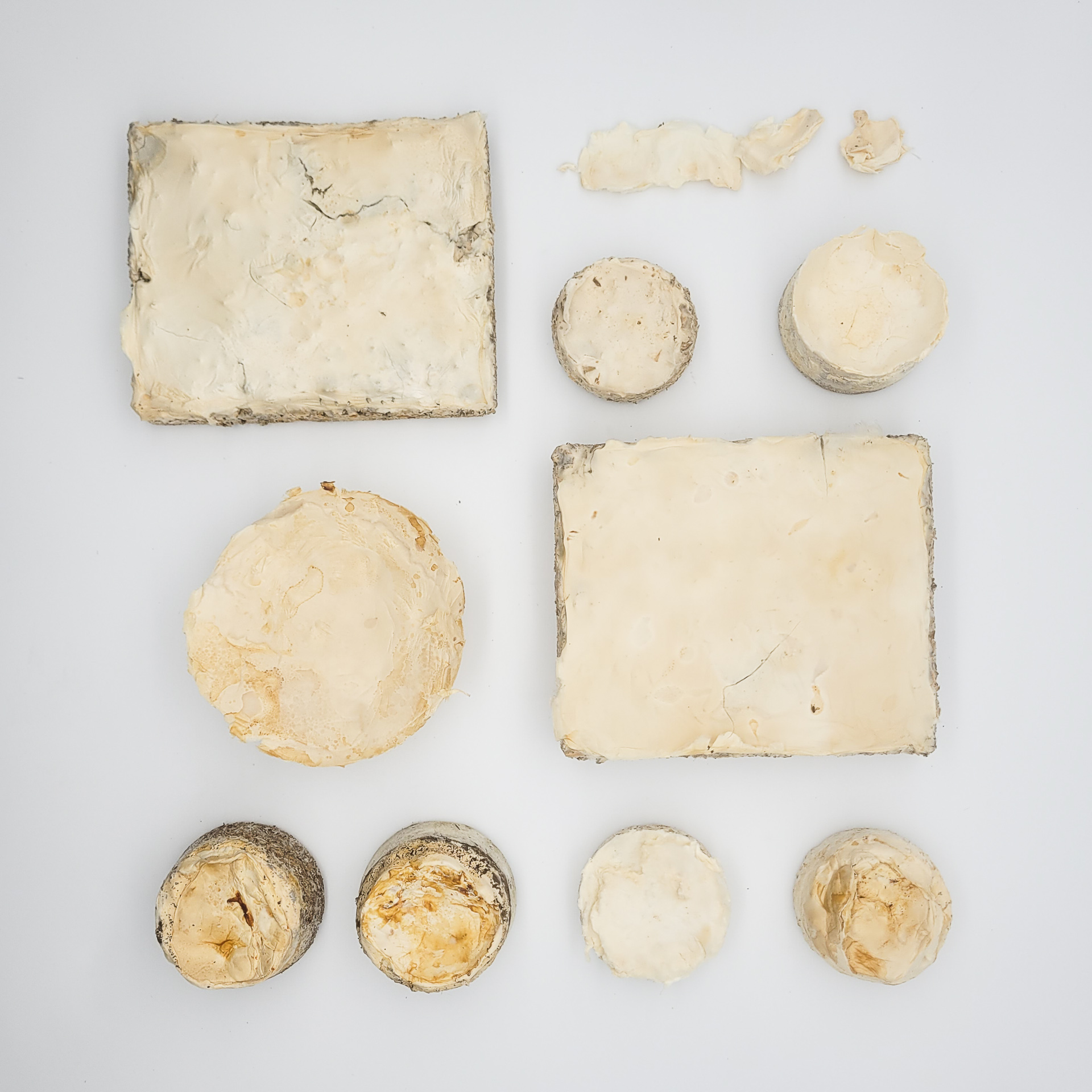
Evaluation
We evaluated the samples based on some basic properties we categorized as relevant when working with the materials. The most relevant to us were:
• the kind of fungus
• material it grew on
• material shrinkadge
• density with which the mycelium grew
• strength of the dried sample
• the Time the sample grew
However, our focus was heavily on the materials that we could use and the understanding of the workflow we needed to establish to grow mycelium-based materials. For this reason, we did document the amount of material and water we used for each sample, but didn't document the weight of the dry samples.The exact amounts of water, materials, and the way we worked are documented in two booklets.
Process
After our research, we started to grow the necessary mycelium according to the sources we found. We produced our own liquid mycelium from spores of fungi we purchased online in the form of mushroom dowels, collected right from nature, or even from mushrooms we bought at the grocery store. We bred:
• Oyster mushroom (Pleurotus ostreatus)
• Shii-Take (Lentinula edodes)
• Ganoderma lucidum
• Tinder fungus (Fomes fomentarius)
• king trumpet mushroom (Pleurotus eryngii)
• Pestalotiopsis microspora ( Decomposes Polyuretan)
After breeding the liquid mycelium, we filled a syringe to inject the mycelium into our prepared materials. Not all the samples we grew were successful; in fact, some of the samples with fungi like Lenticular erodes led to no successful results at all.
The best results came from the samples, which were bred from Pleurotus Ostreatus, Fomes Fomentarius, and Ganoderma Lucidum. Especially the samples with wood-decaying fungus were astonishingly hard after drying.
We documented the complete process behind growing the fungi and the samples we made in a protocol booklet, just like I documented the process of growing the fungi and preparations for every step.
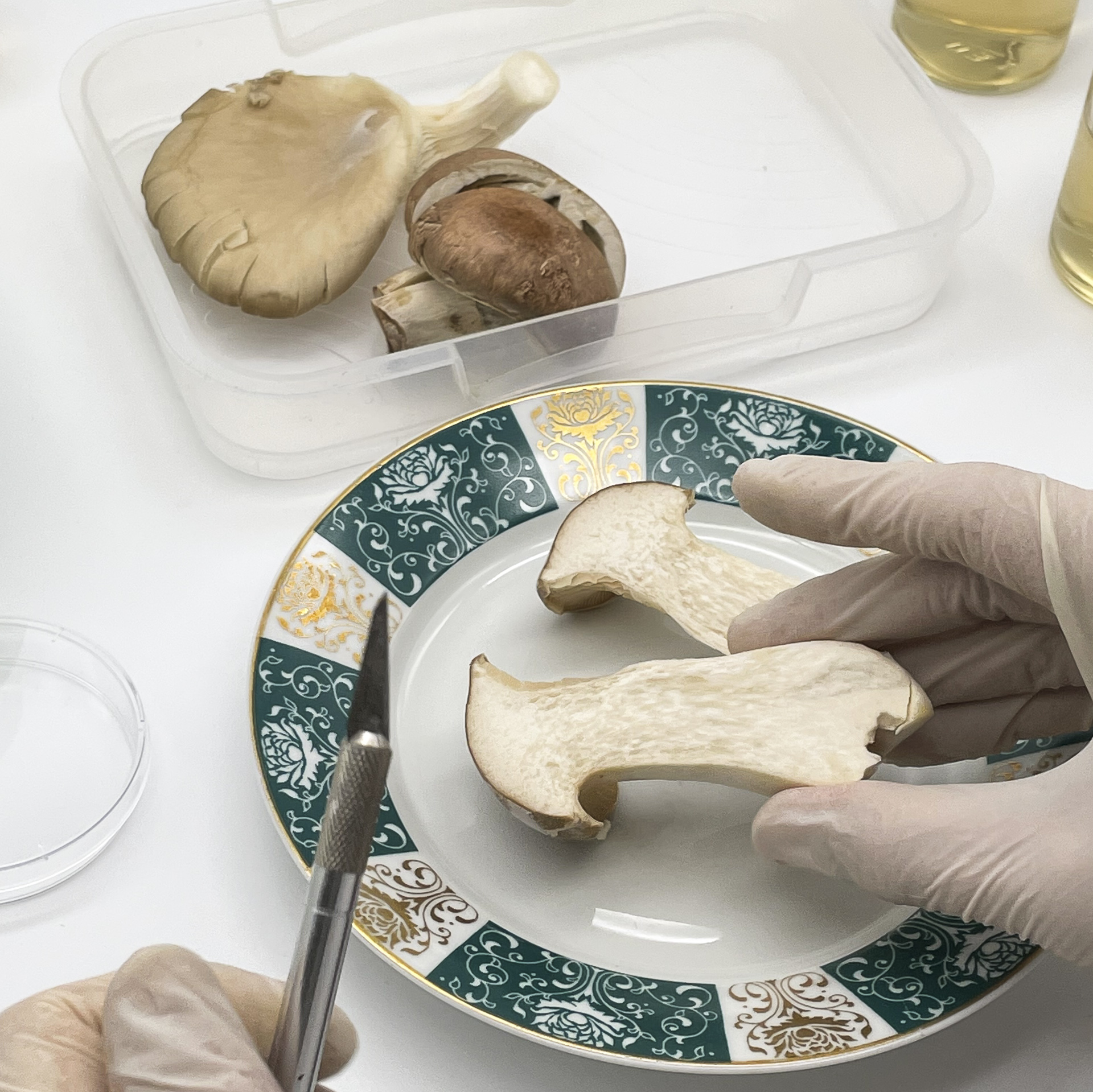
.jpg)
We tried growing mycelium on many different materials. Some of these were:
• Carrot-and-Apple peels
• Coffee grounds
• Tea
• Peanut hulls
• Avocado peels
• Beer spent grains
• Lime peels
• Banana peels
• Wood chips(different types)
And other. While doing our research, we have already found some information regarding a few of the materials and their potential, for example, about the wood chips. For other materials, we tested the percentage of water and dry mass that was necessary until we found the right balance.
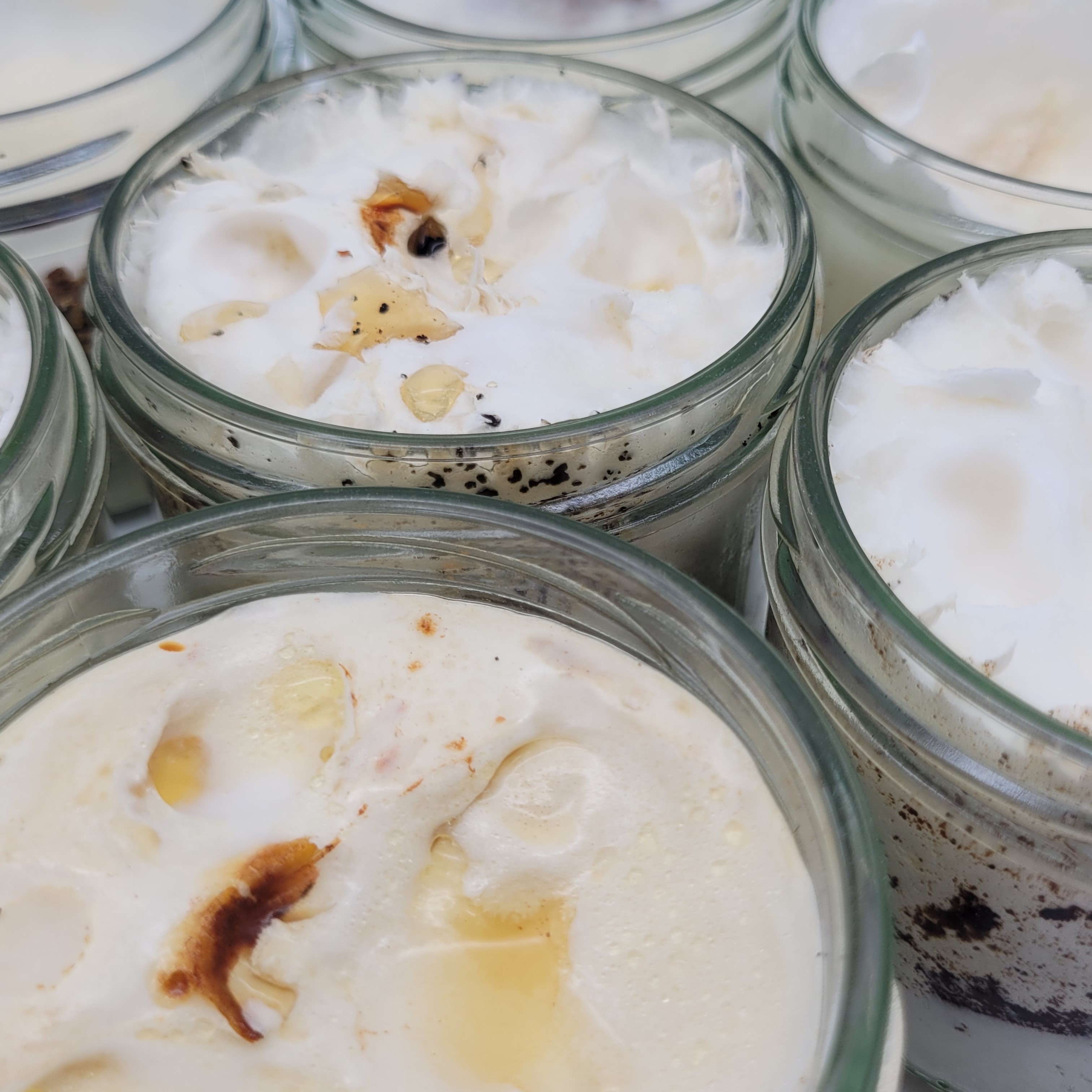
.JPG)
Thanks to my good friend Clemens Domsch
For this project, I worked together with my student and good friend Clemens Domsch, to whom I would like to express a special thanks at this point. It was nice and interesting to do a project together and to coordinate and divide the work, especially because it was the first real group project after the Corona crisis.
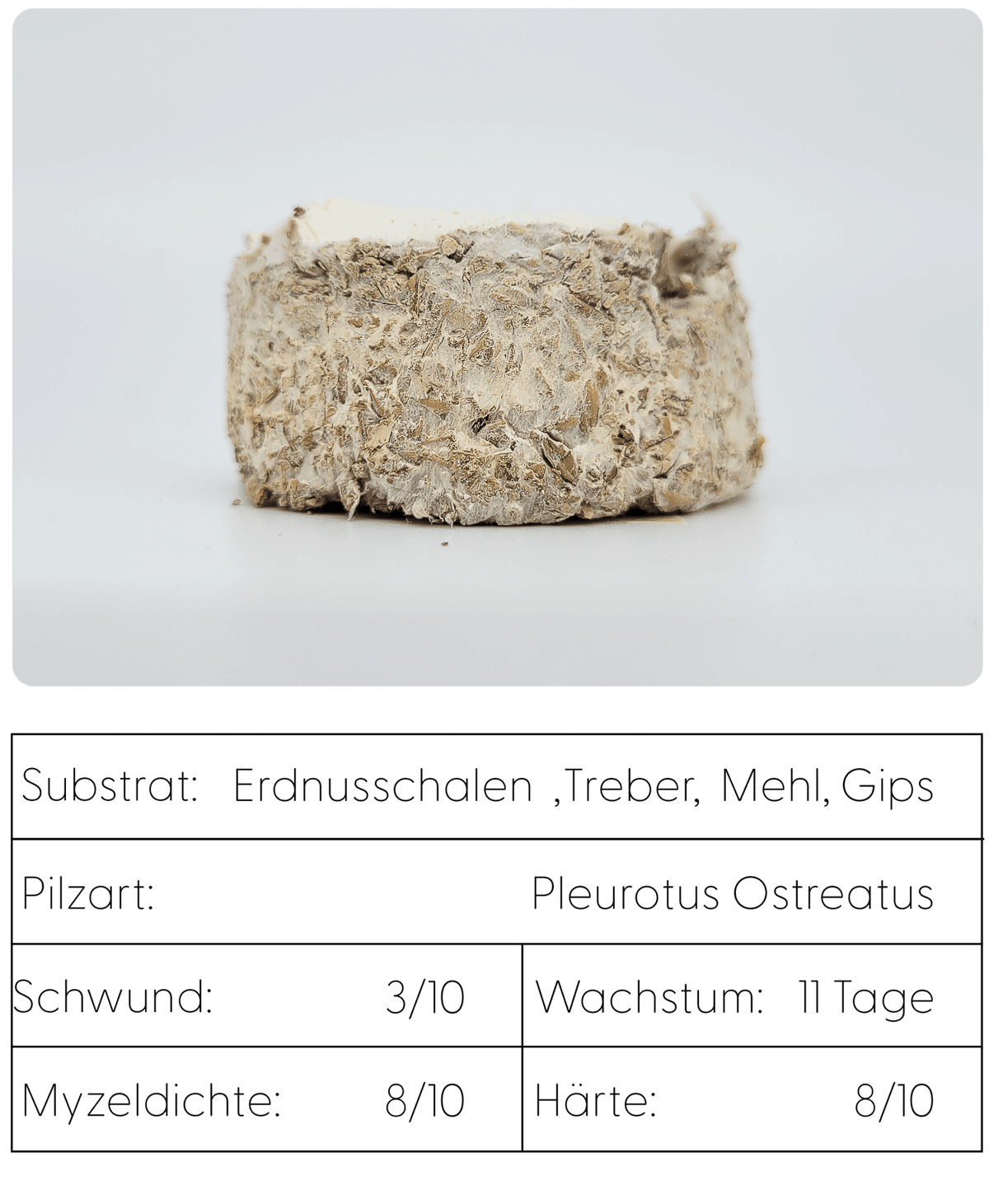
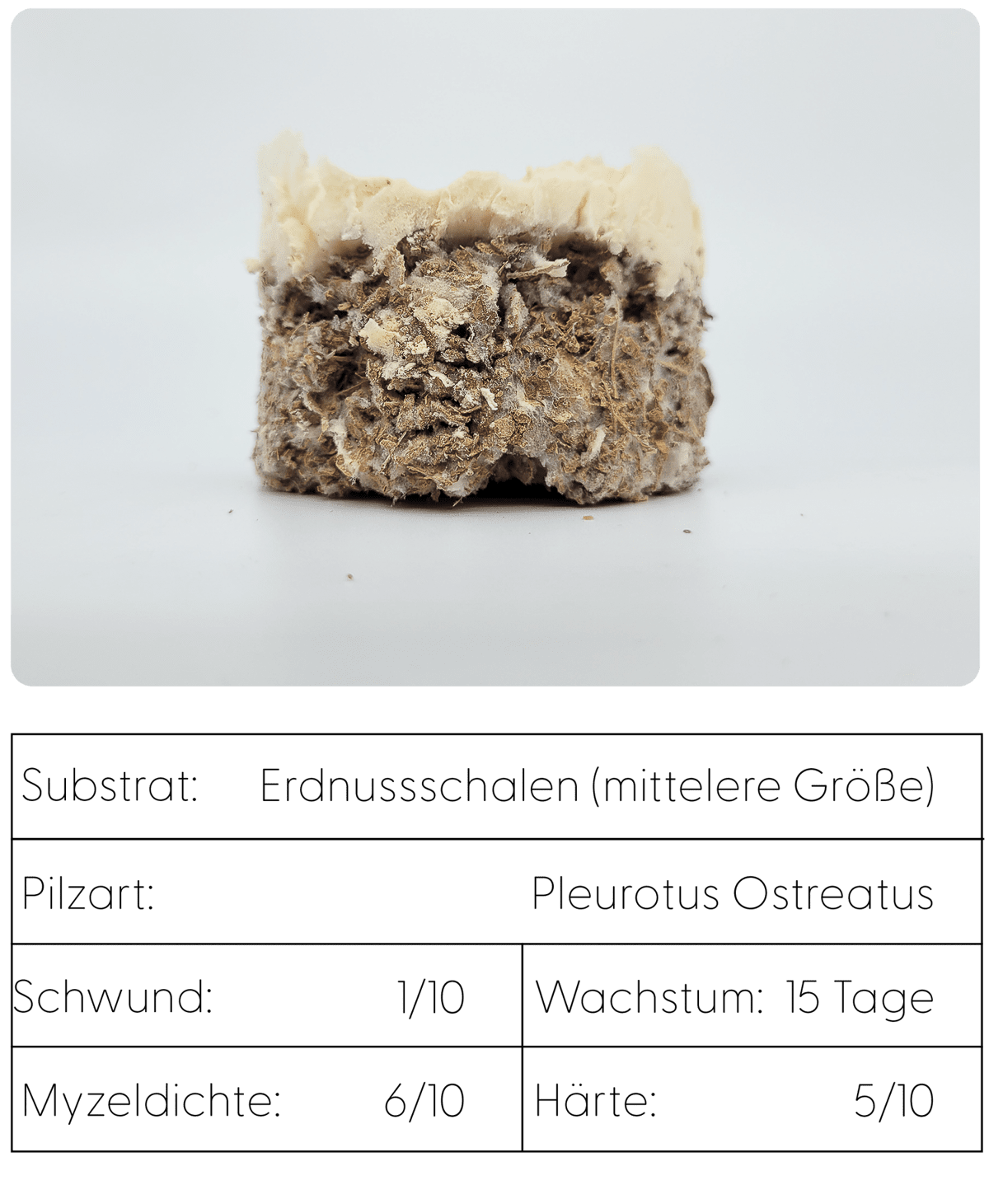
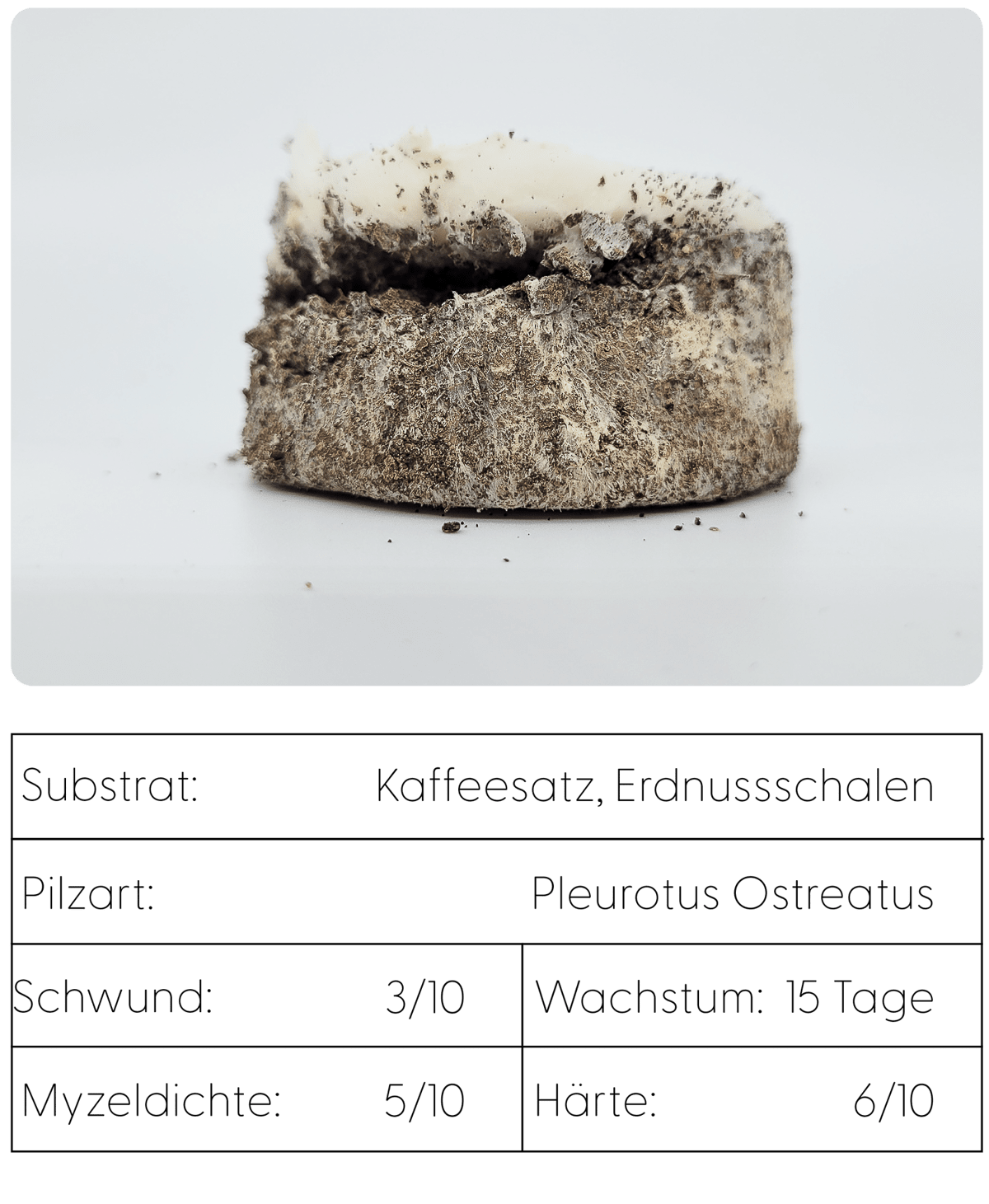
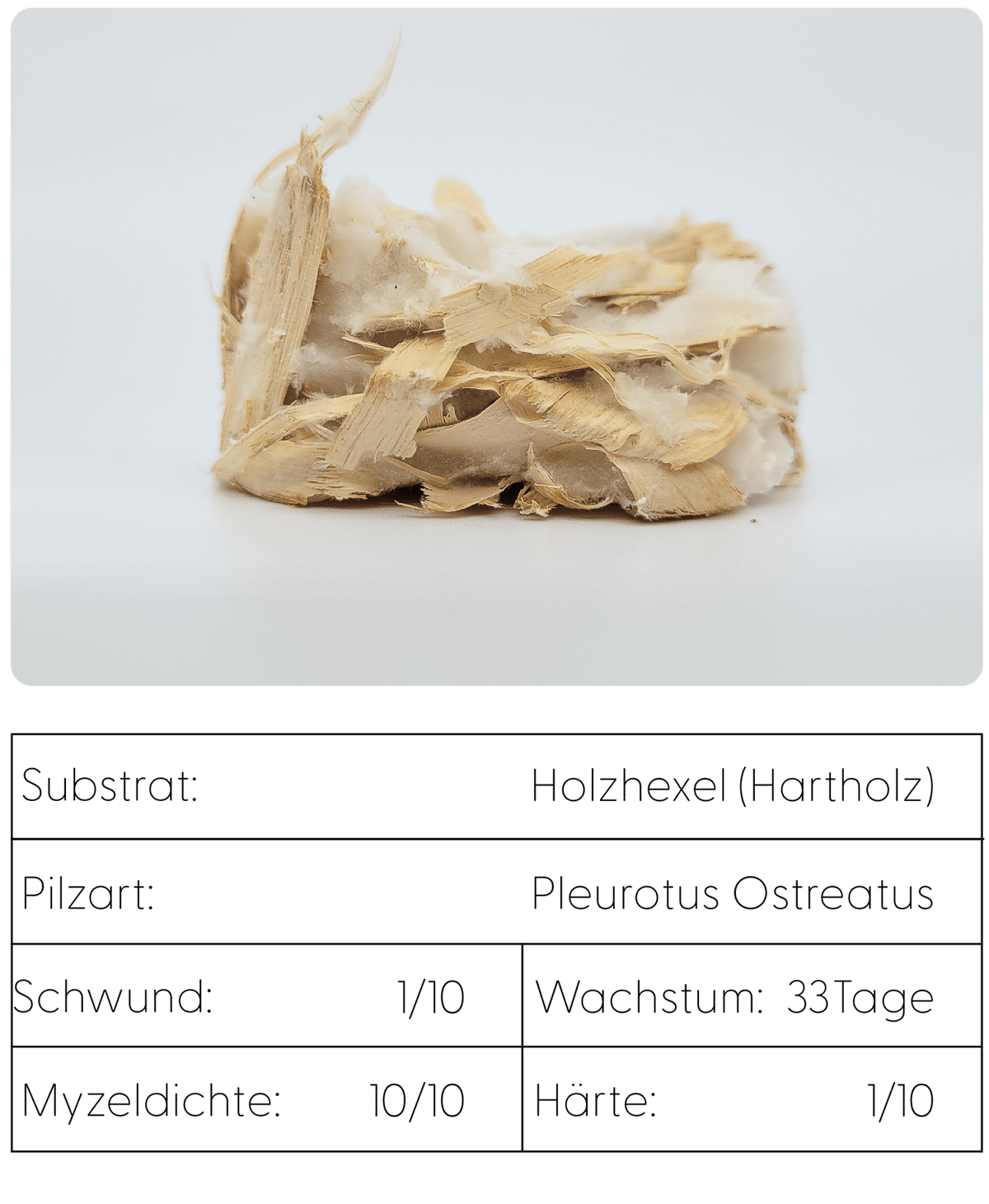
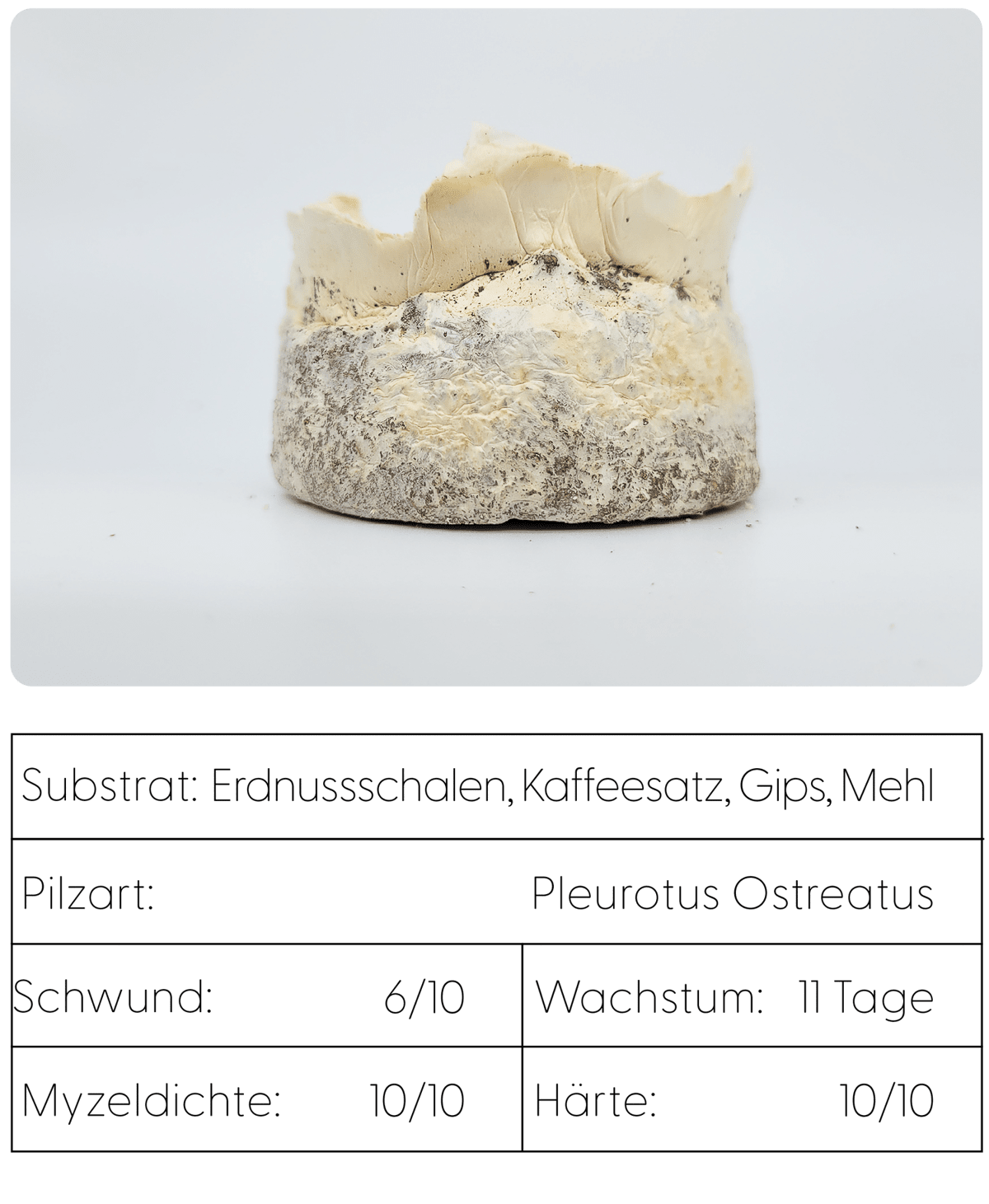
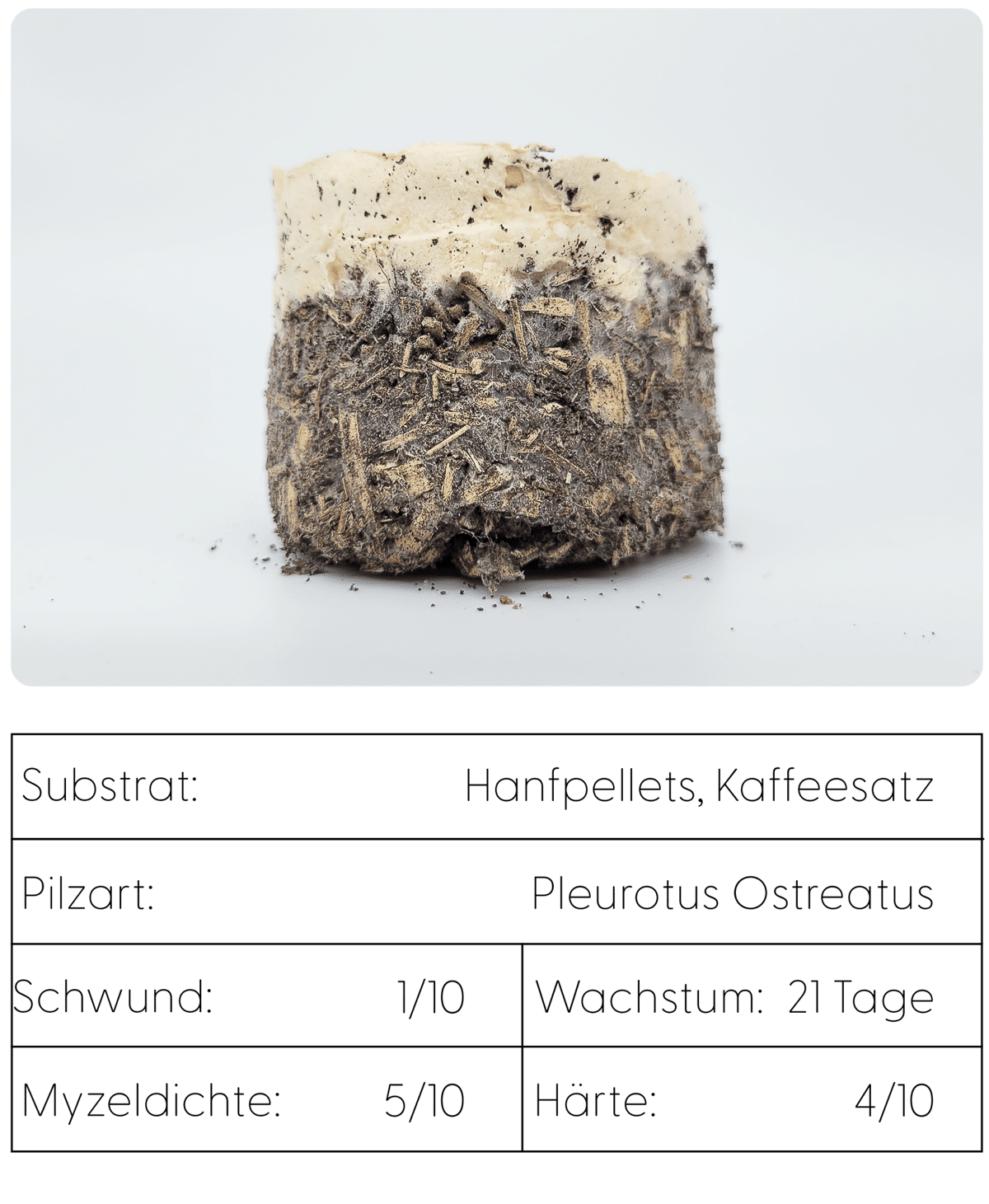
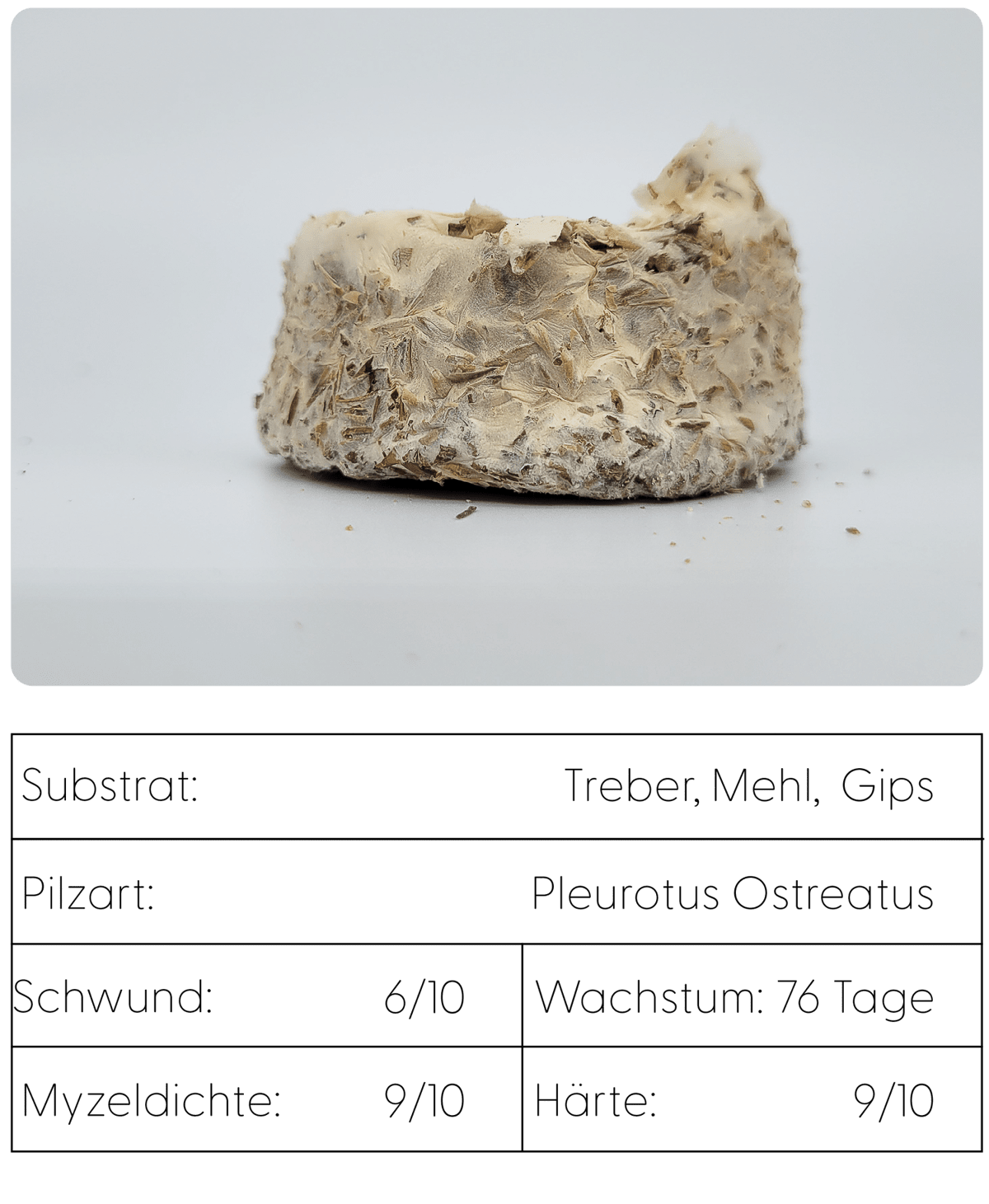
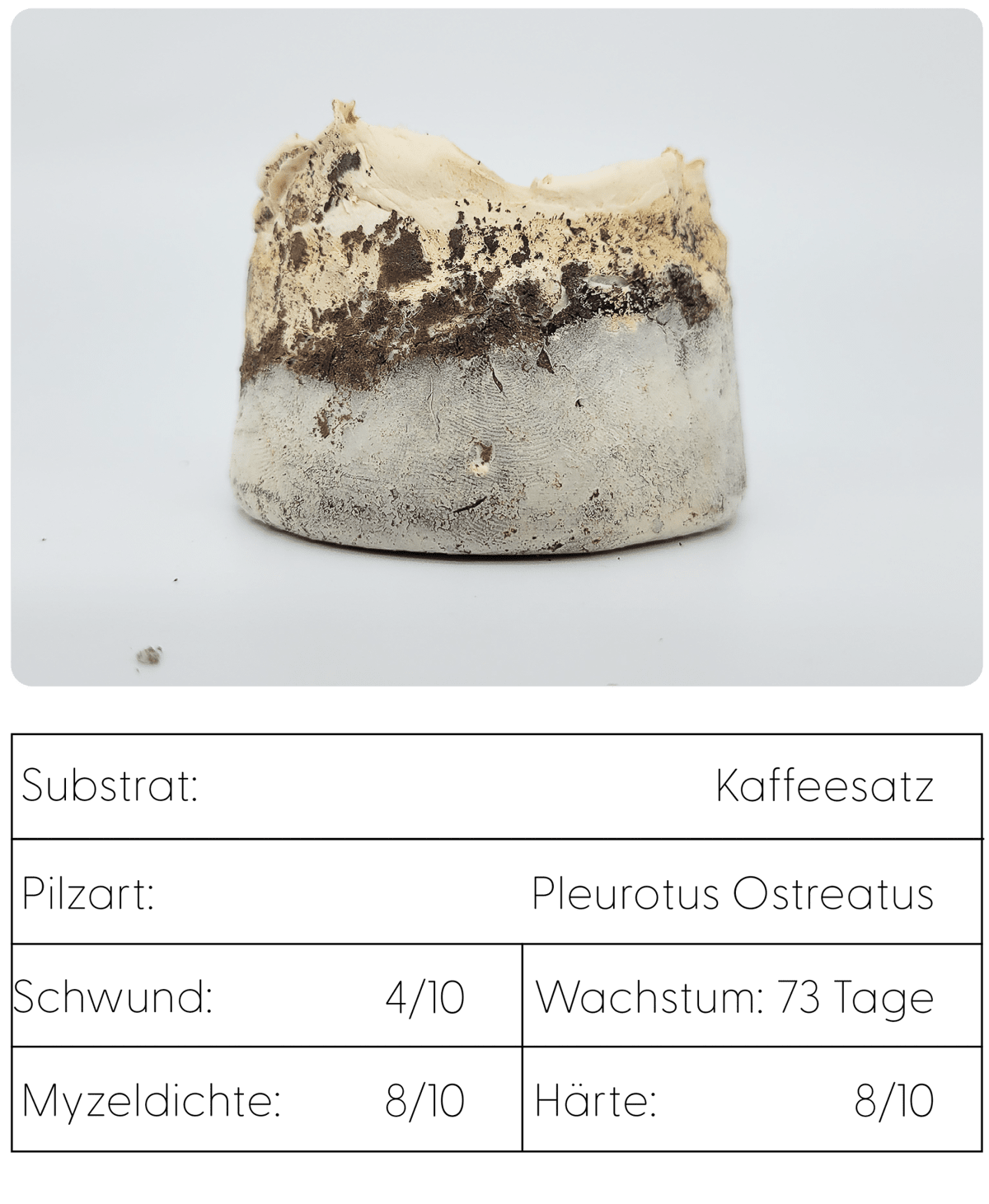
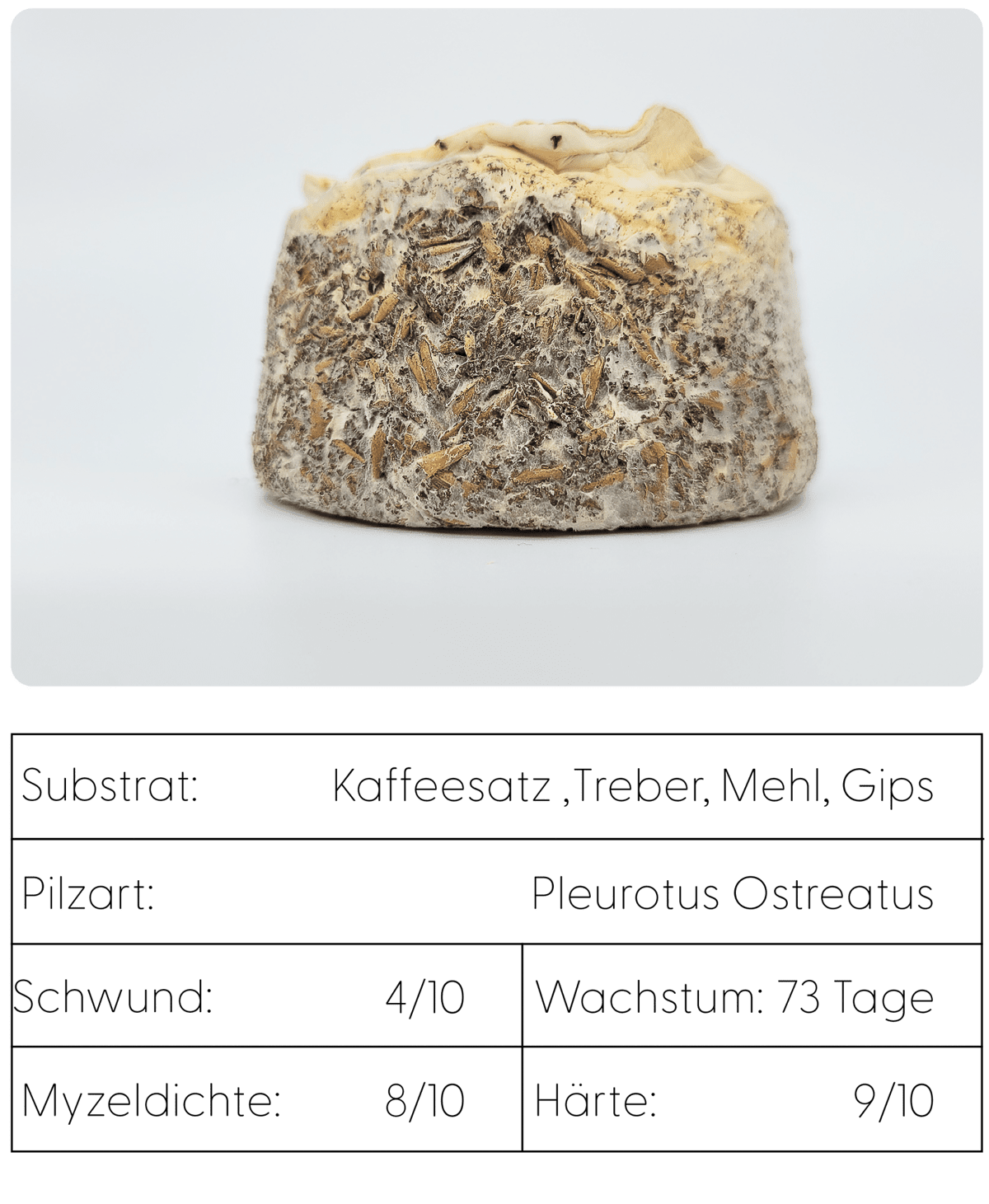
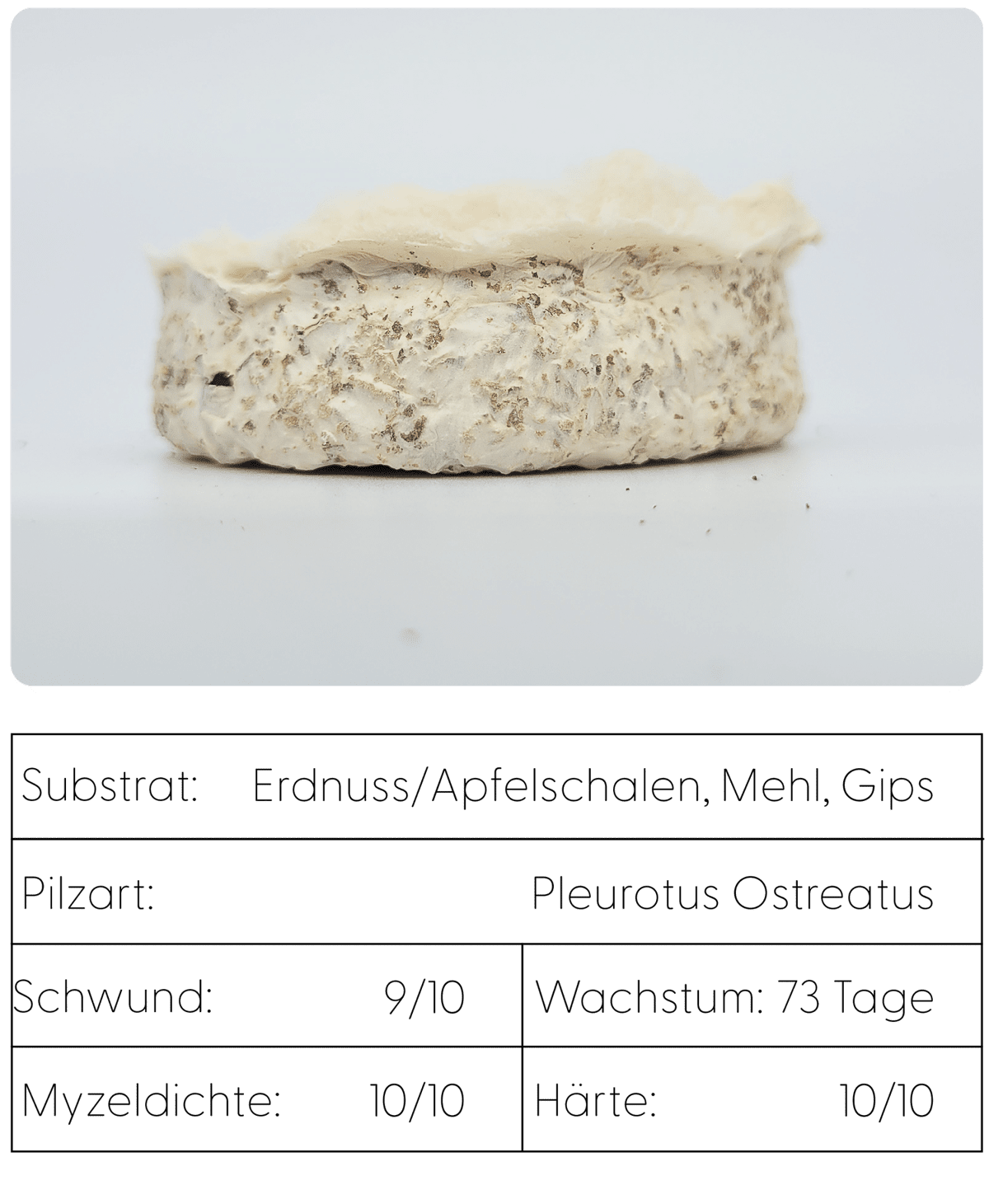
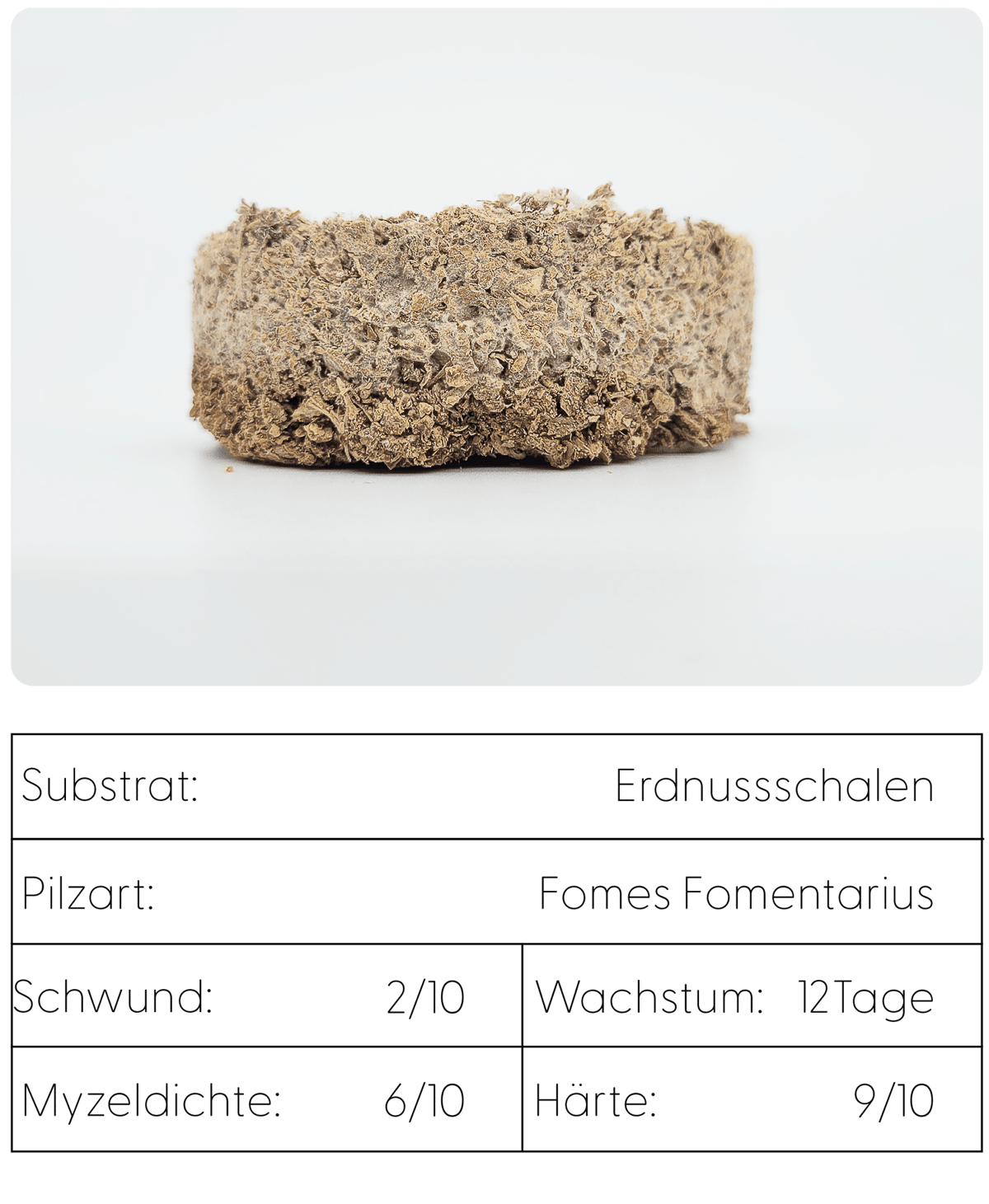
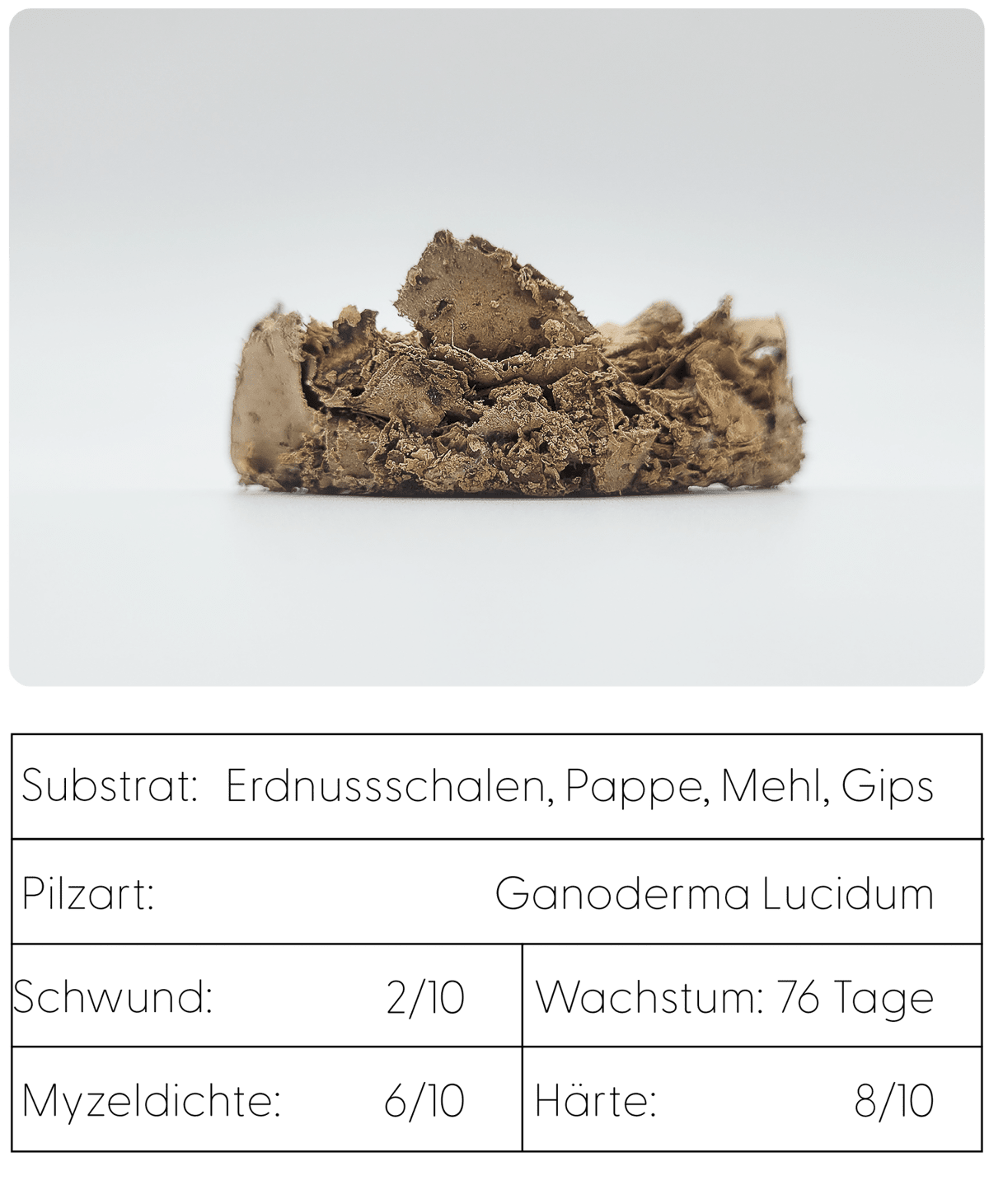
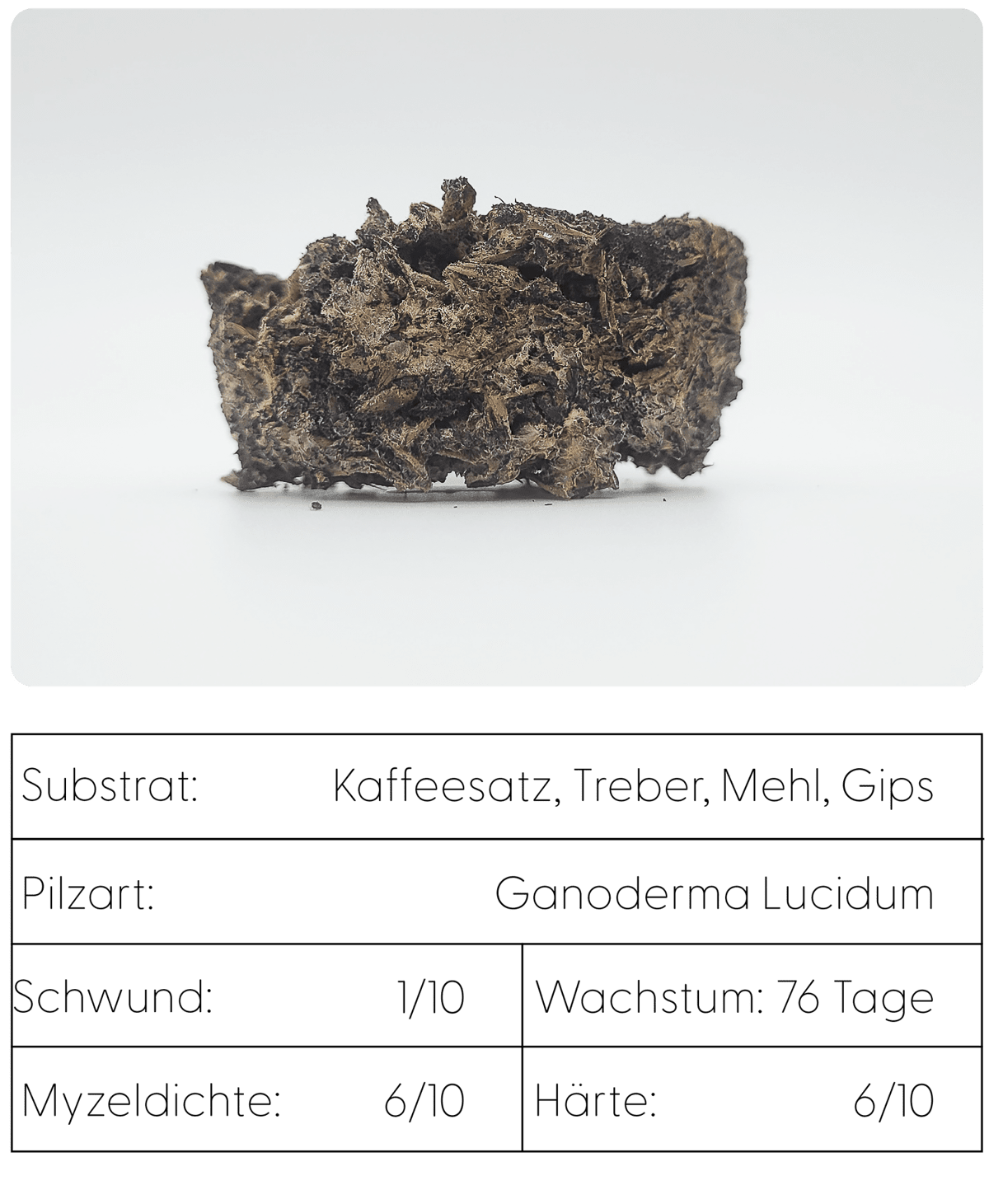
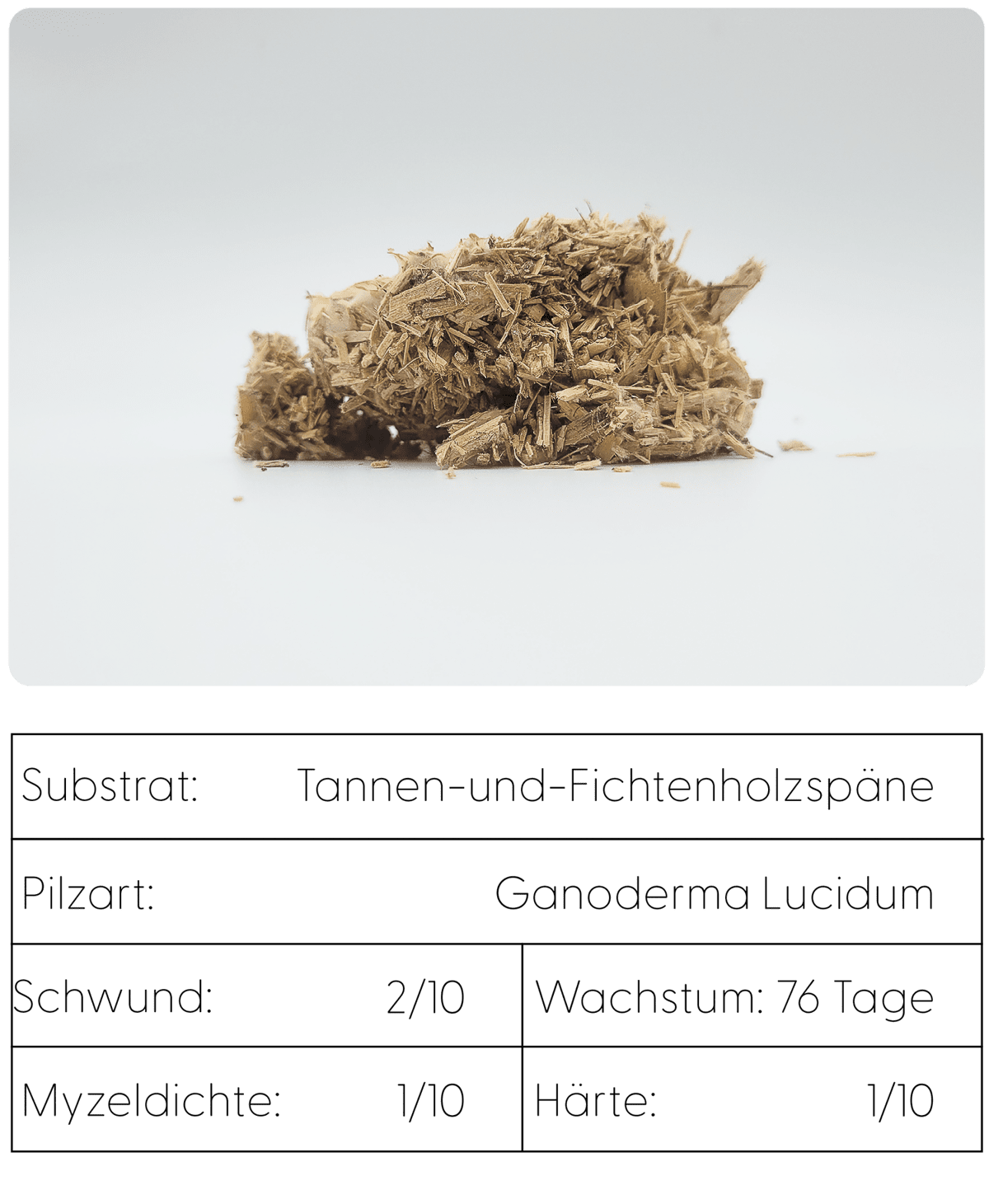
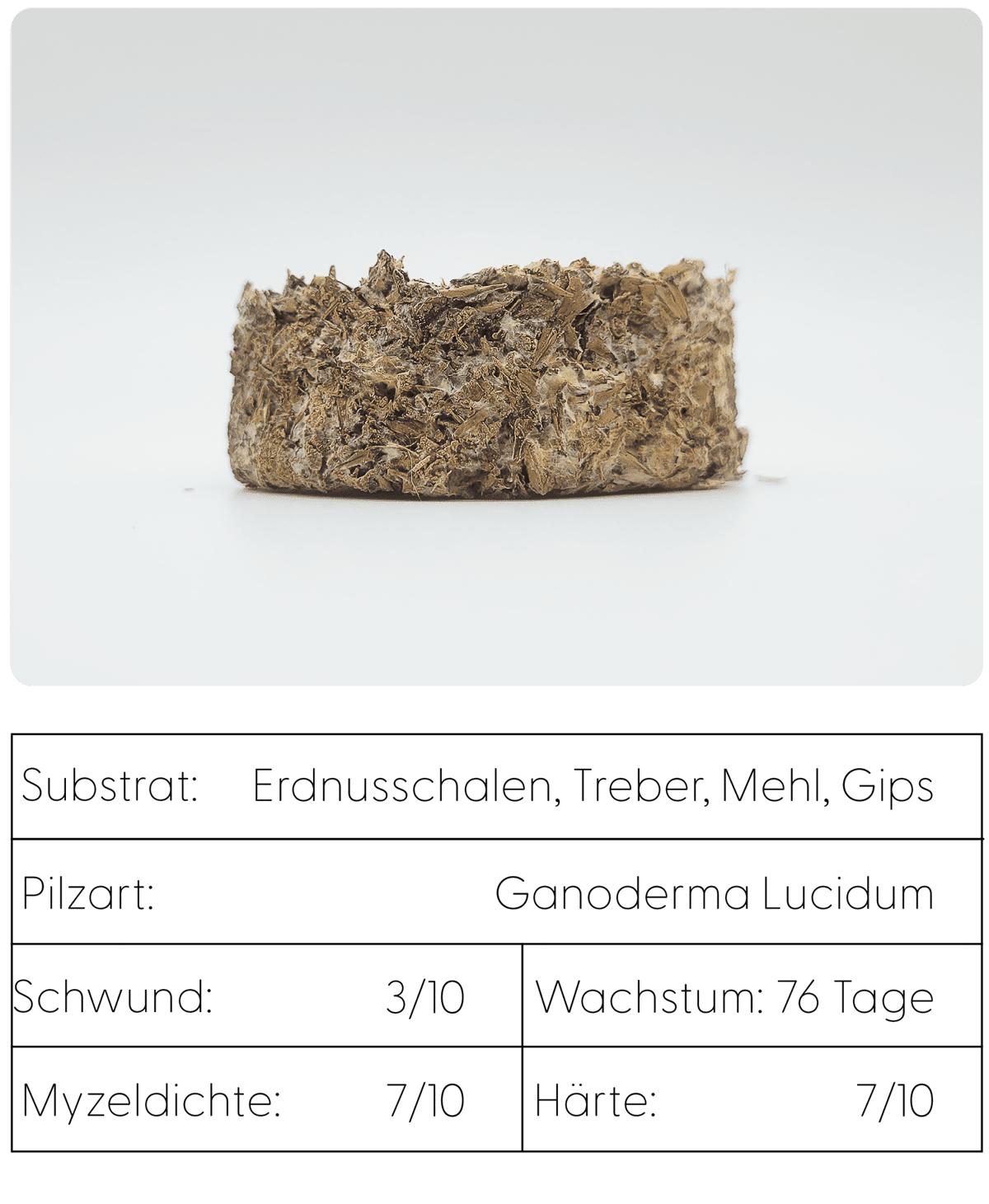
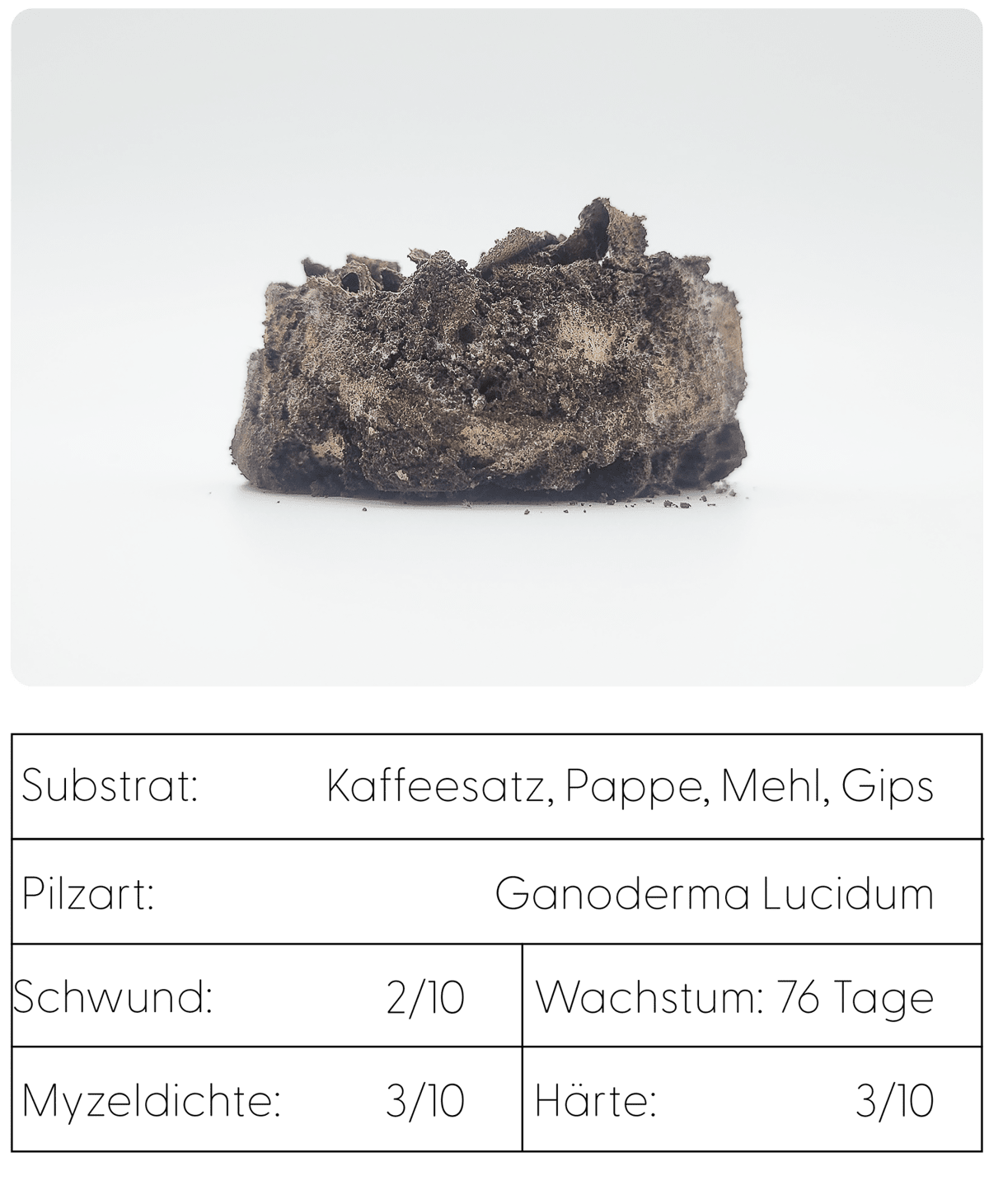
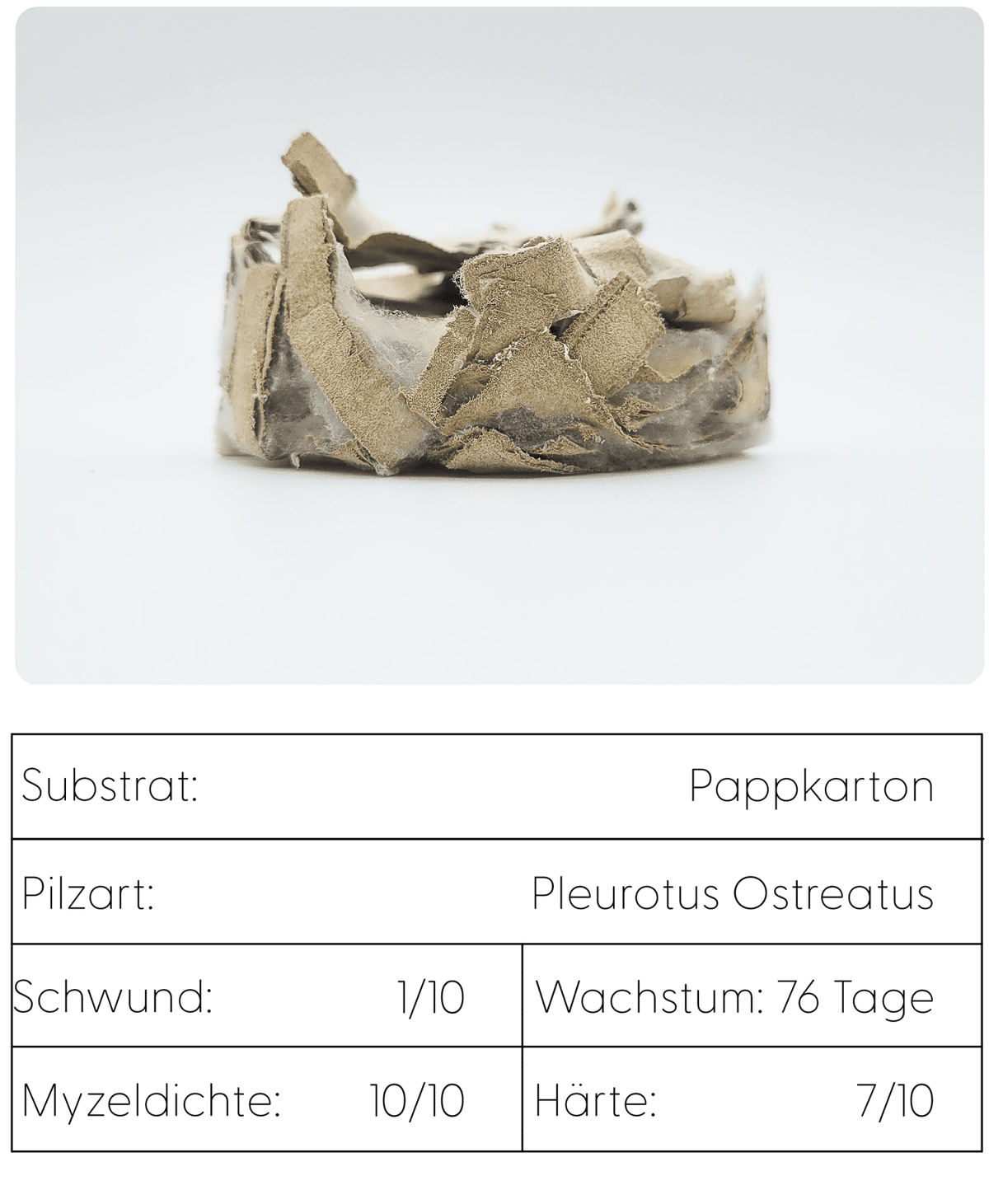
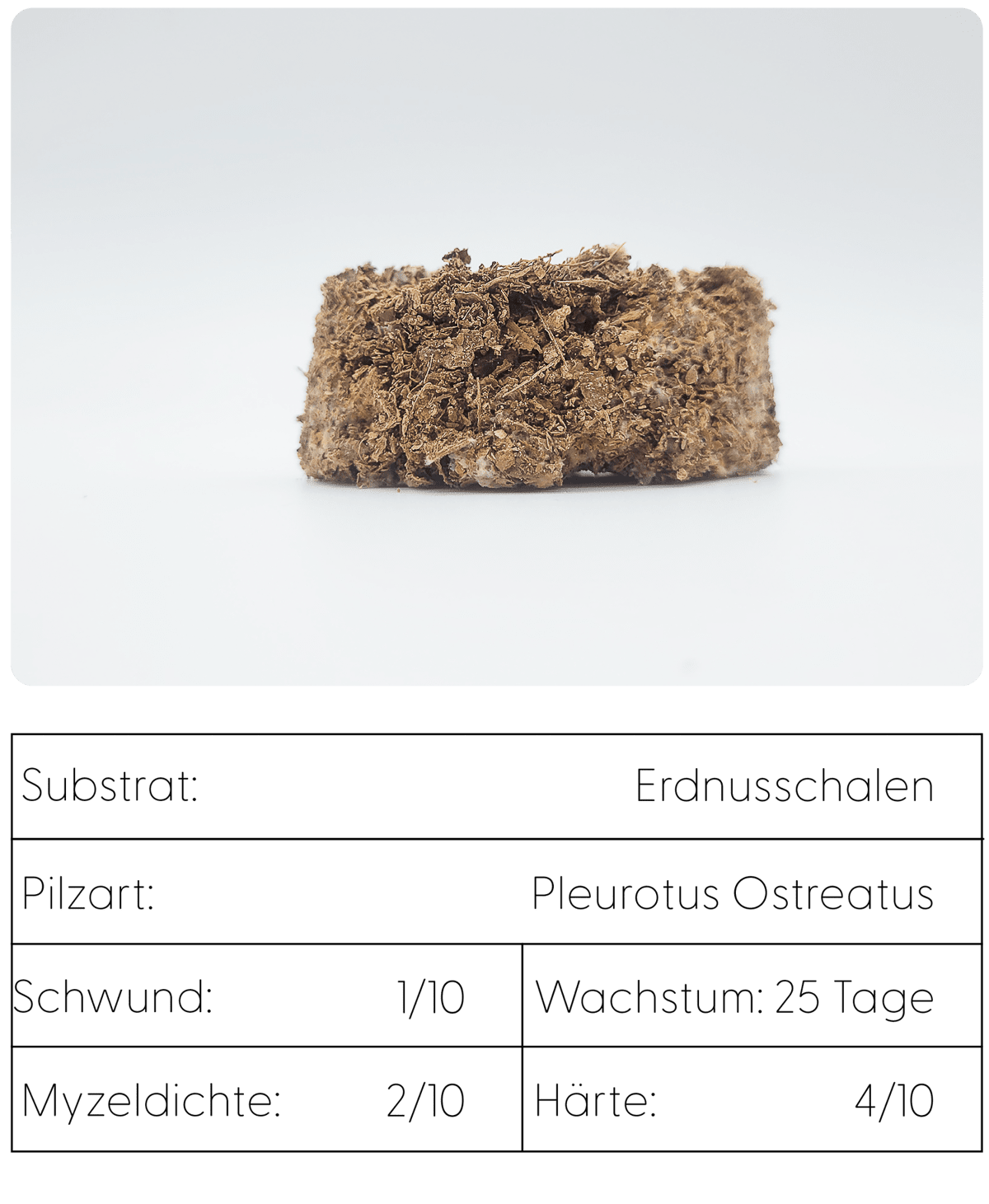
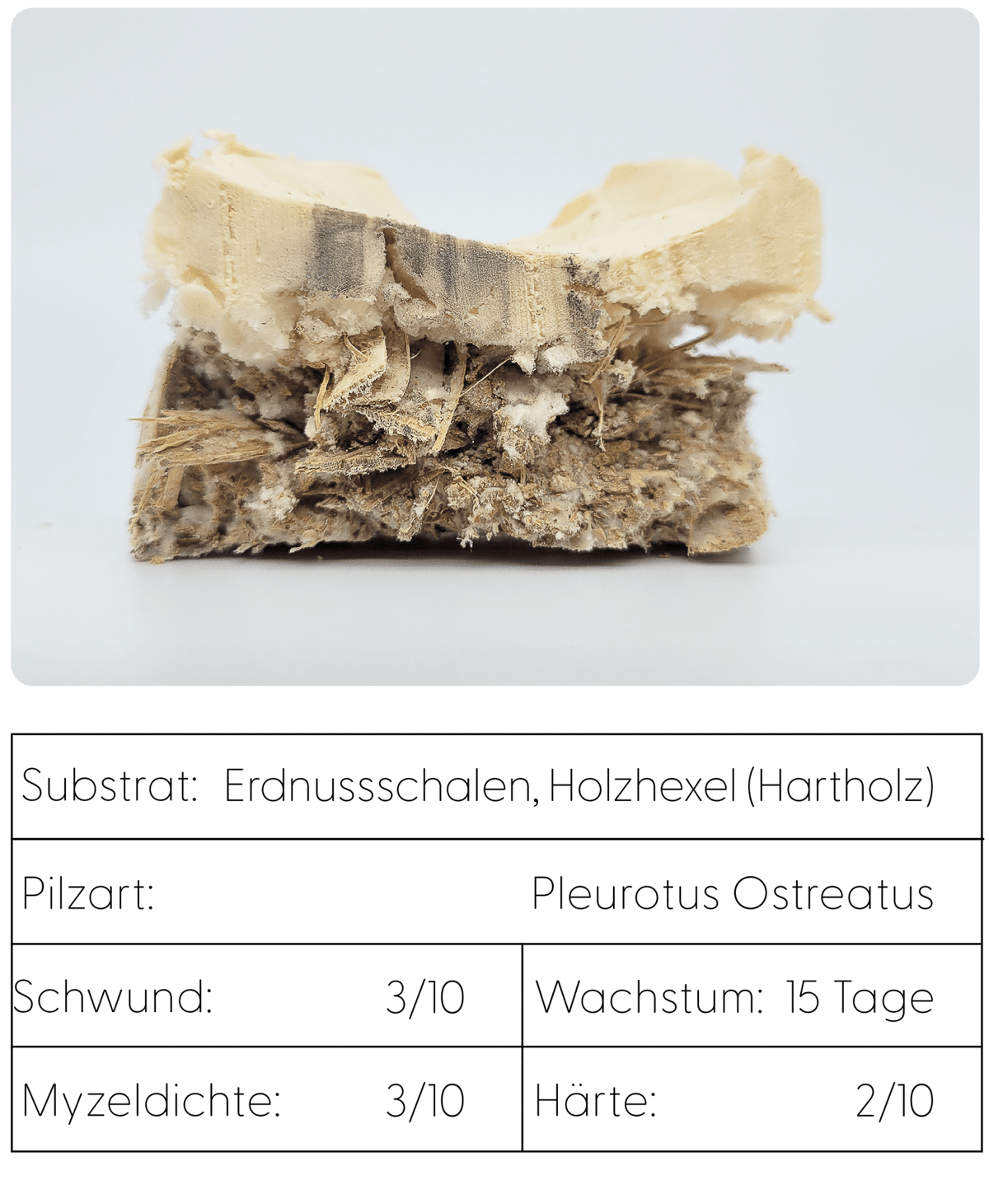
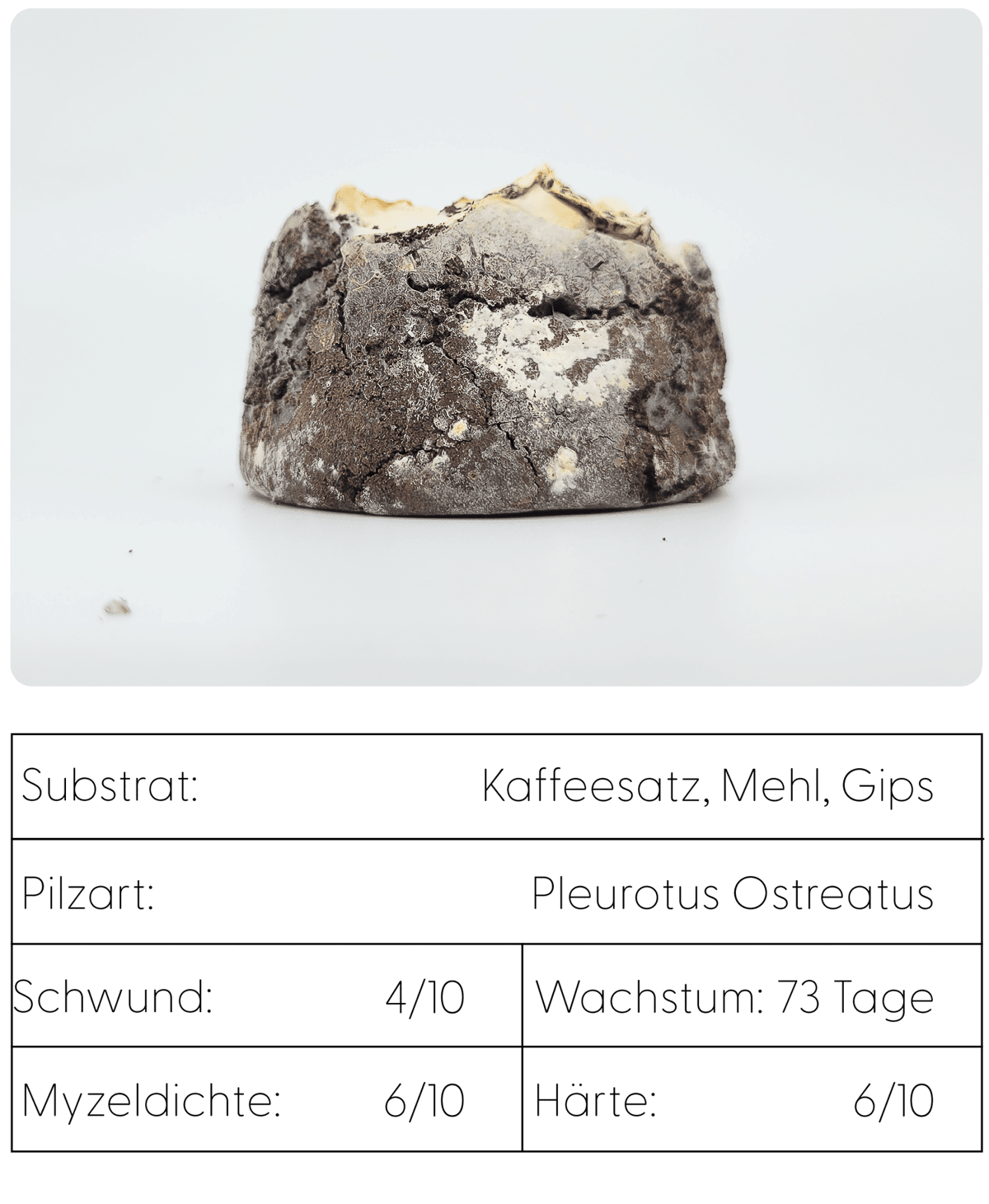
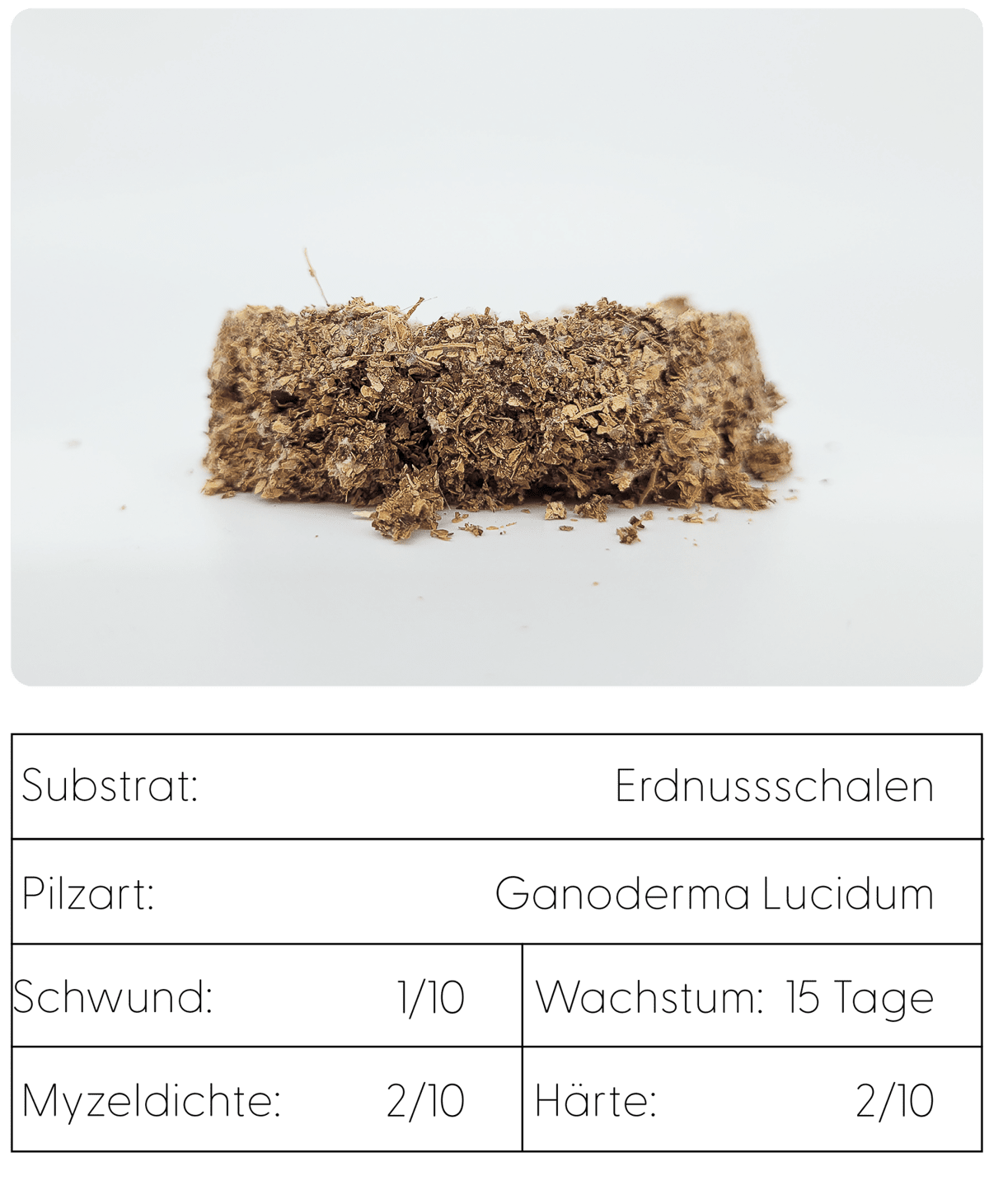
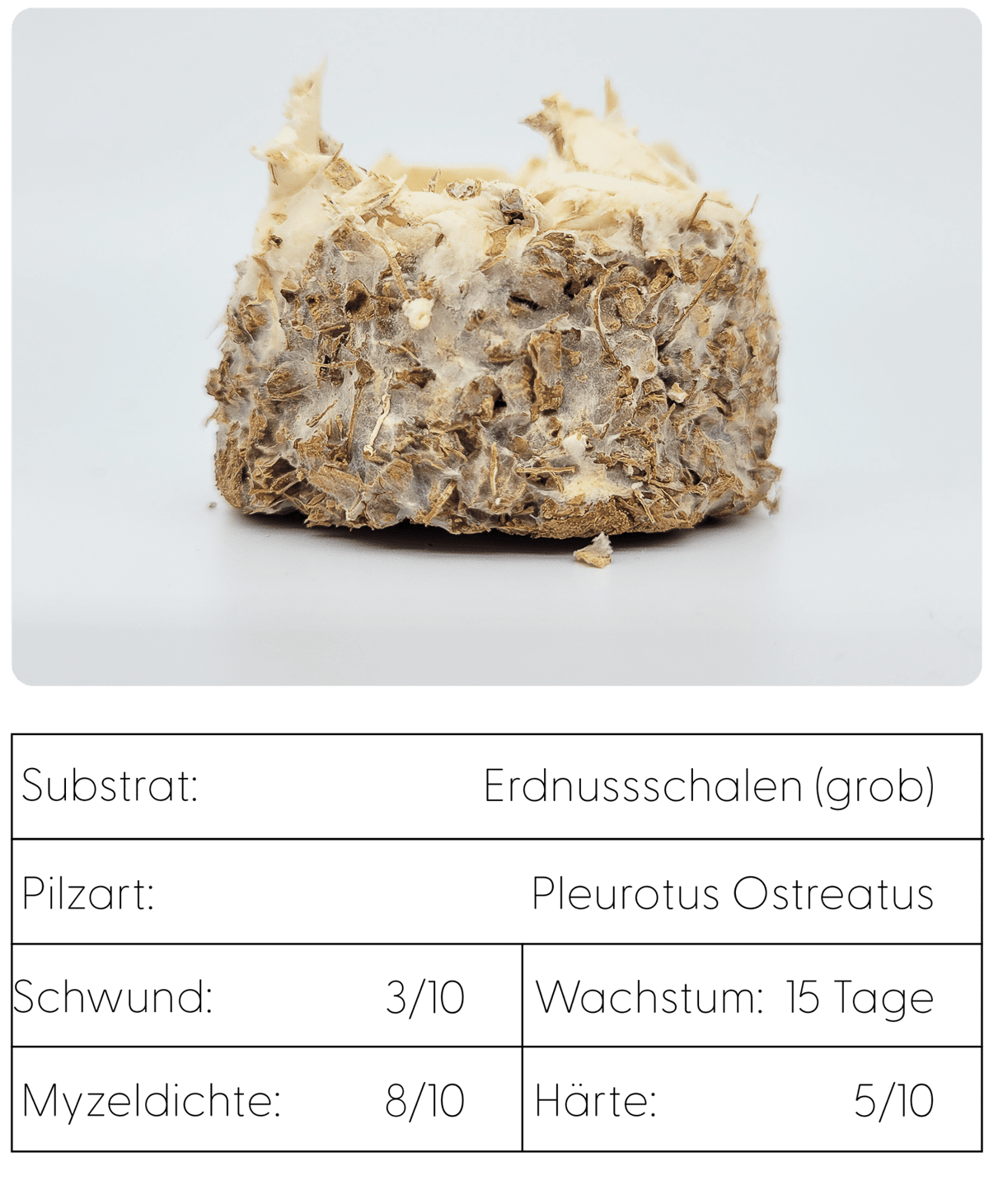
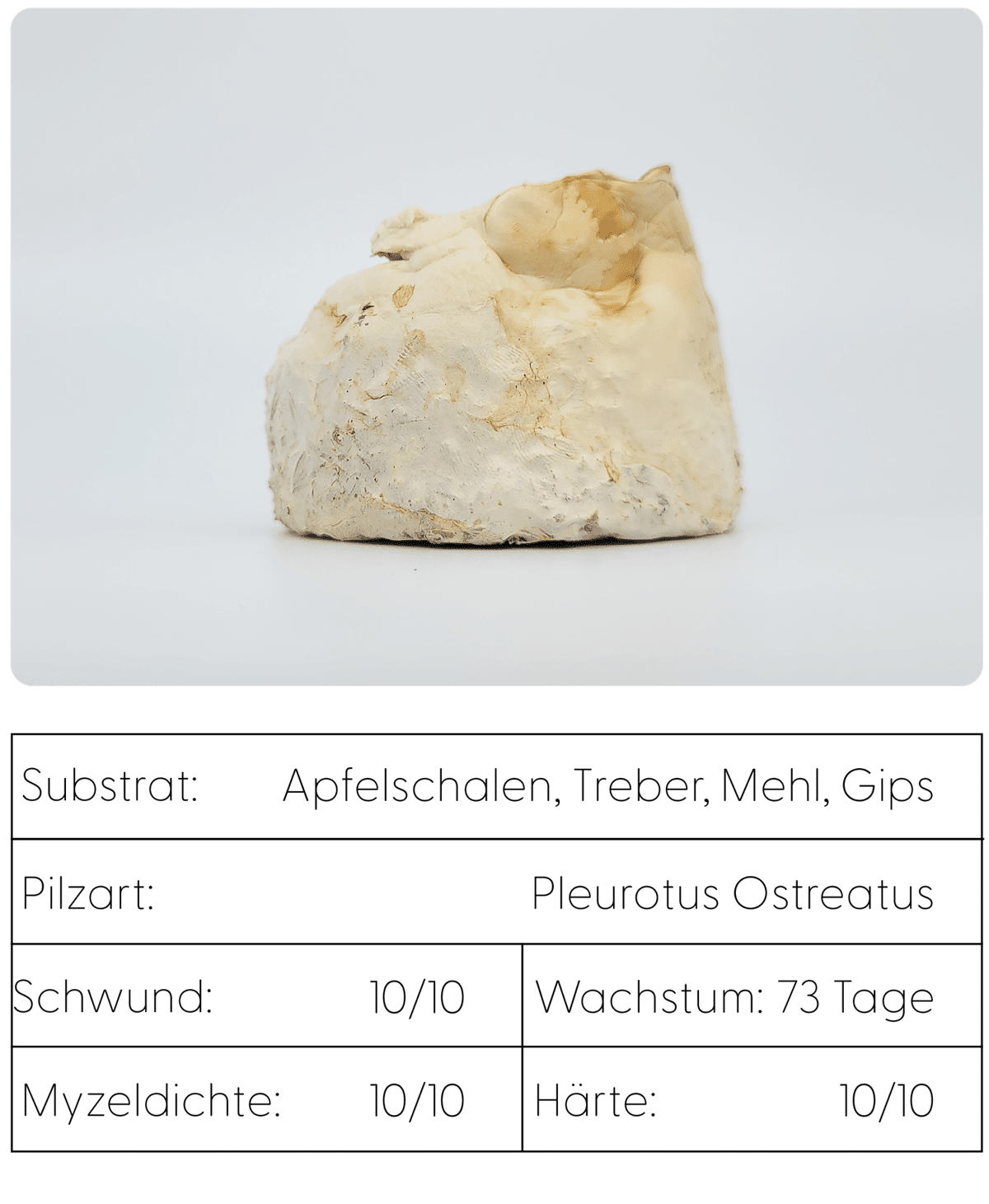
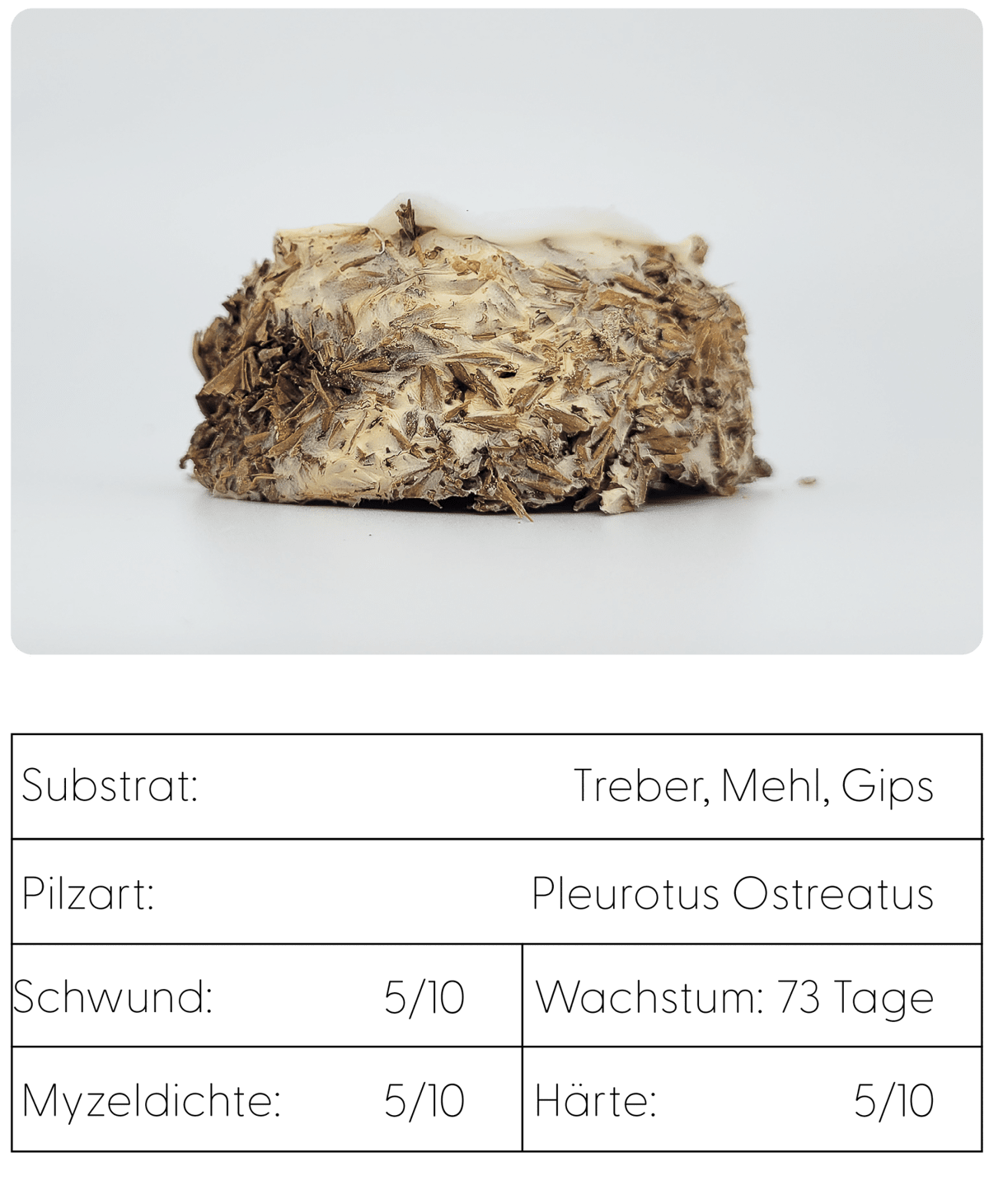
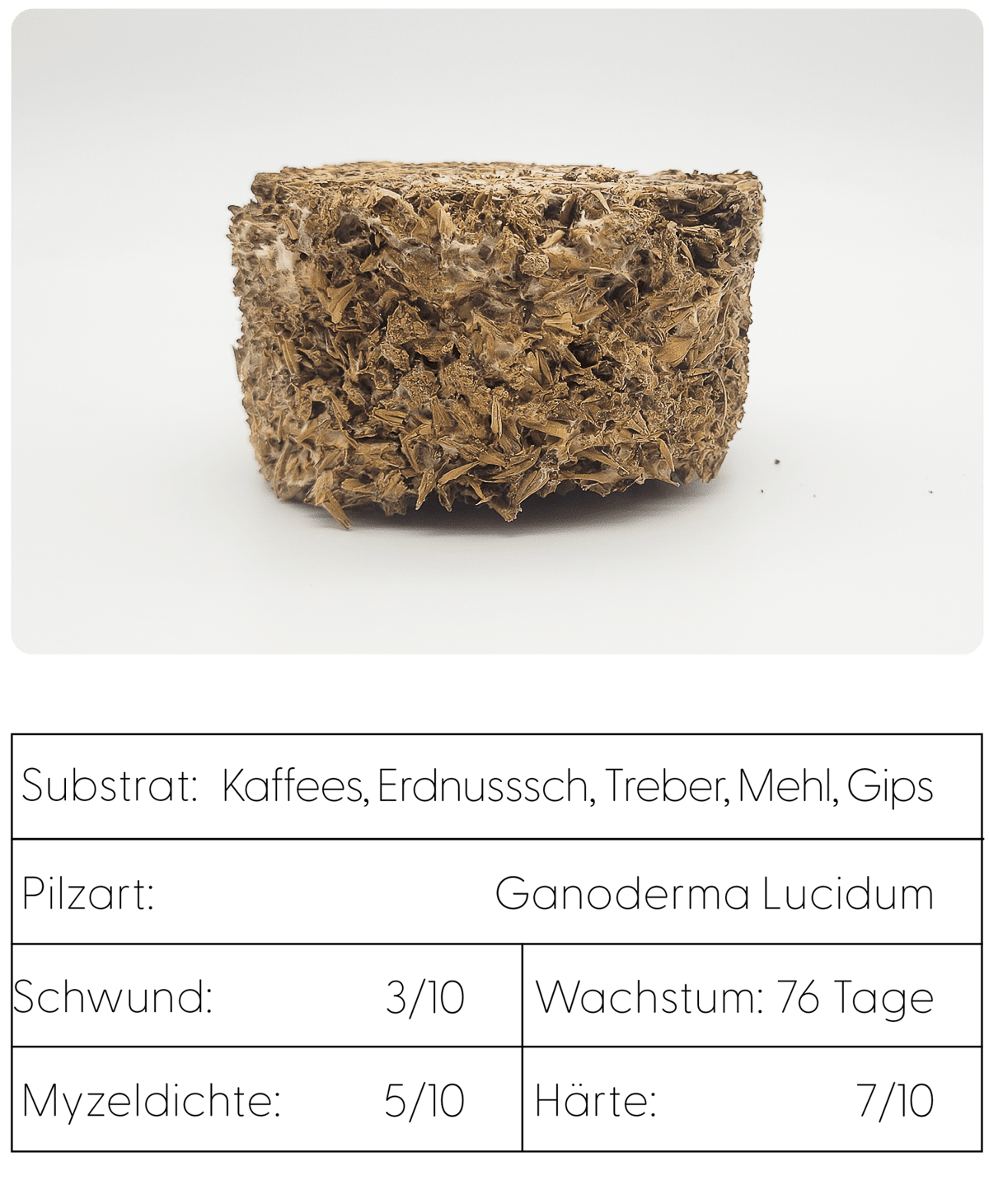
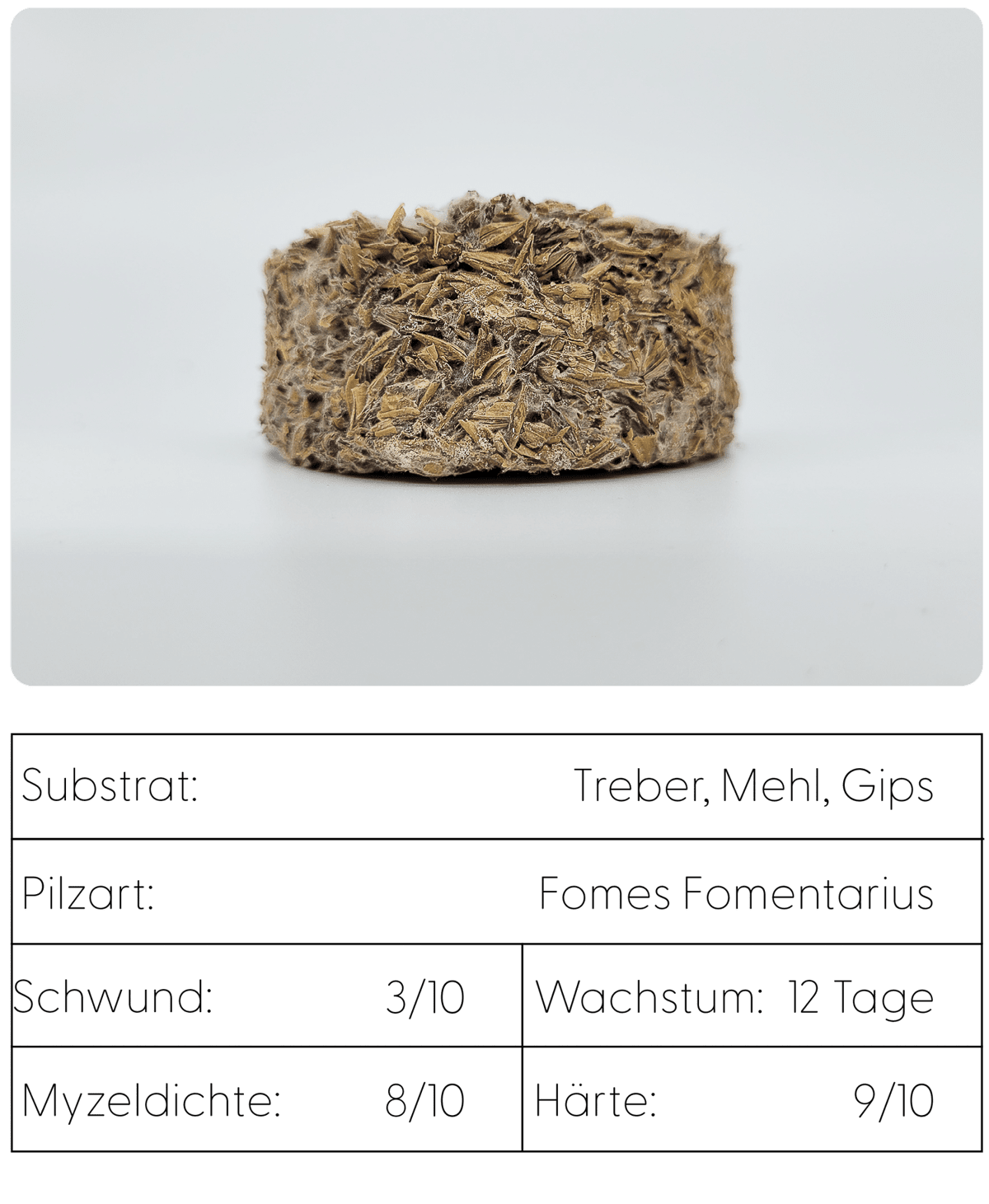
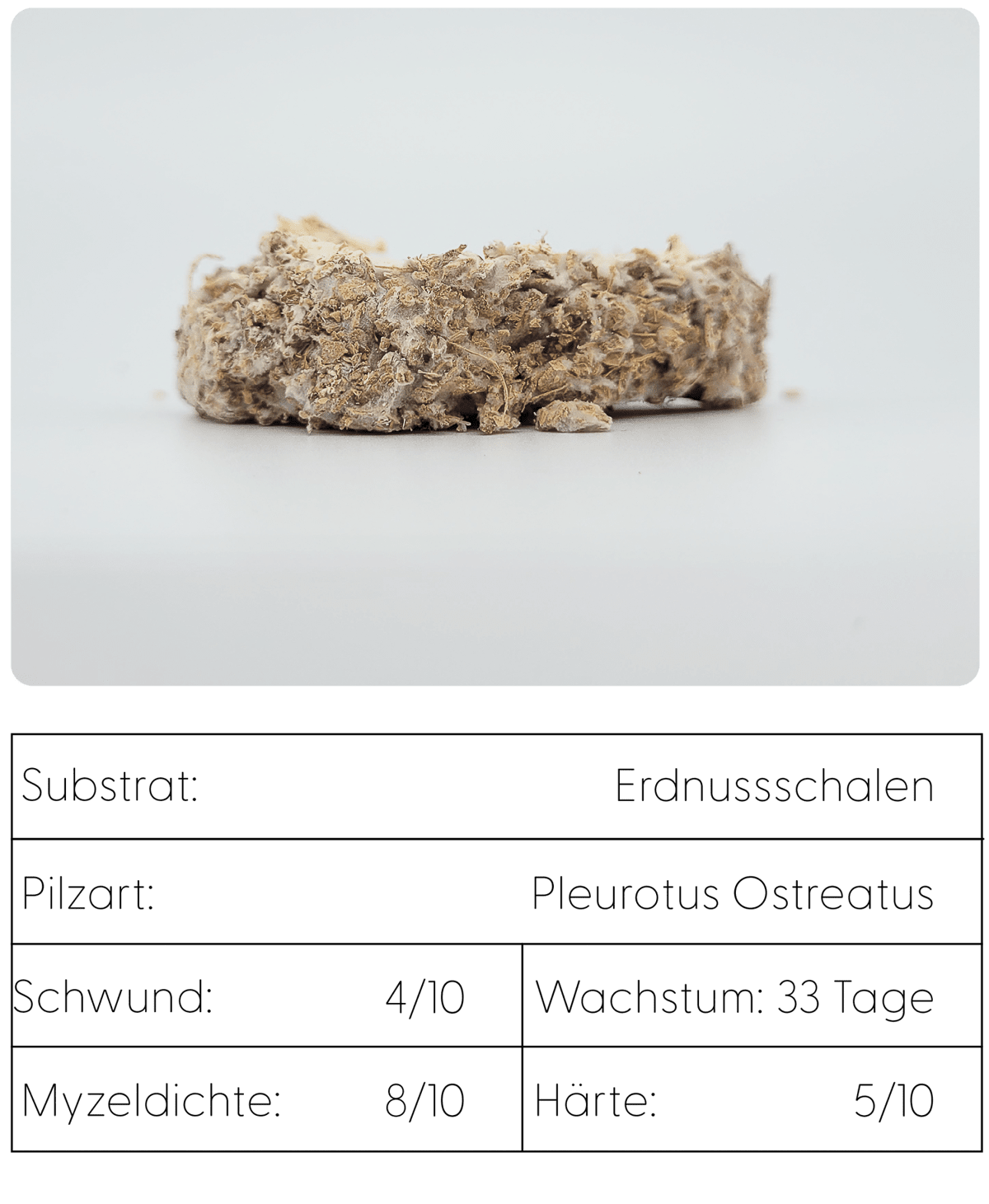
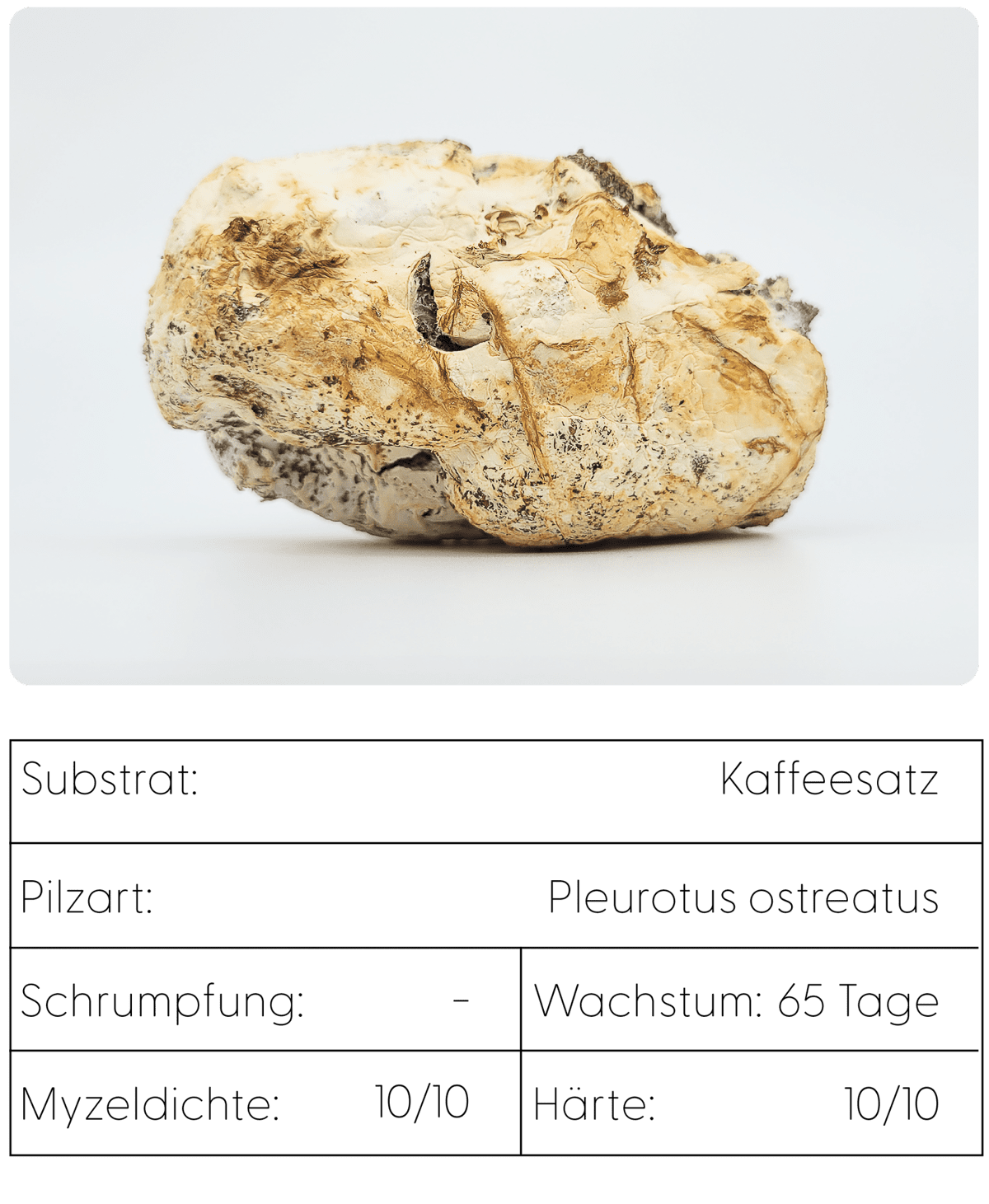
Intent
I started this project because I am fascinated by the idea of working with living, growing organisms to produce sustainable materials. As one of these materials, mycelium has gained popularity in recent years due to its awesome material abilities, such as temperature- and sound-insulation properties, its toughness compared to its low weight, and the fact that it is completely biodegradable. Because a good friend and fellow student of mine, Clemens Domsch, was interested in this topic too, we initiated it as a group project.
.png)
.png)
.png)
What is mycelium?
In general, the word fungus is used to describe the visible fruiting body of fungi. Mycelium is the sum of all hyphae (the thread-like cells) of a fungus. In addition to plants and animals, fungi form the third major kingdom of eukaryotic organisms (organisms with a cell nucleus). Unlike plants, they cannot perform synthesis. They therefore take up their food in dissolved form from their environment. The diversity of species ranges from complex, multicellular organisms to single-celled organisms like baker's yeast. In nature, fungi are essential for the maintenance of ecosystems. They form symbioses with plants and provide them with important nutrients, such as phosphate, which they need for their growth.
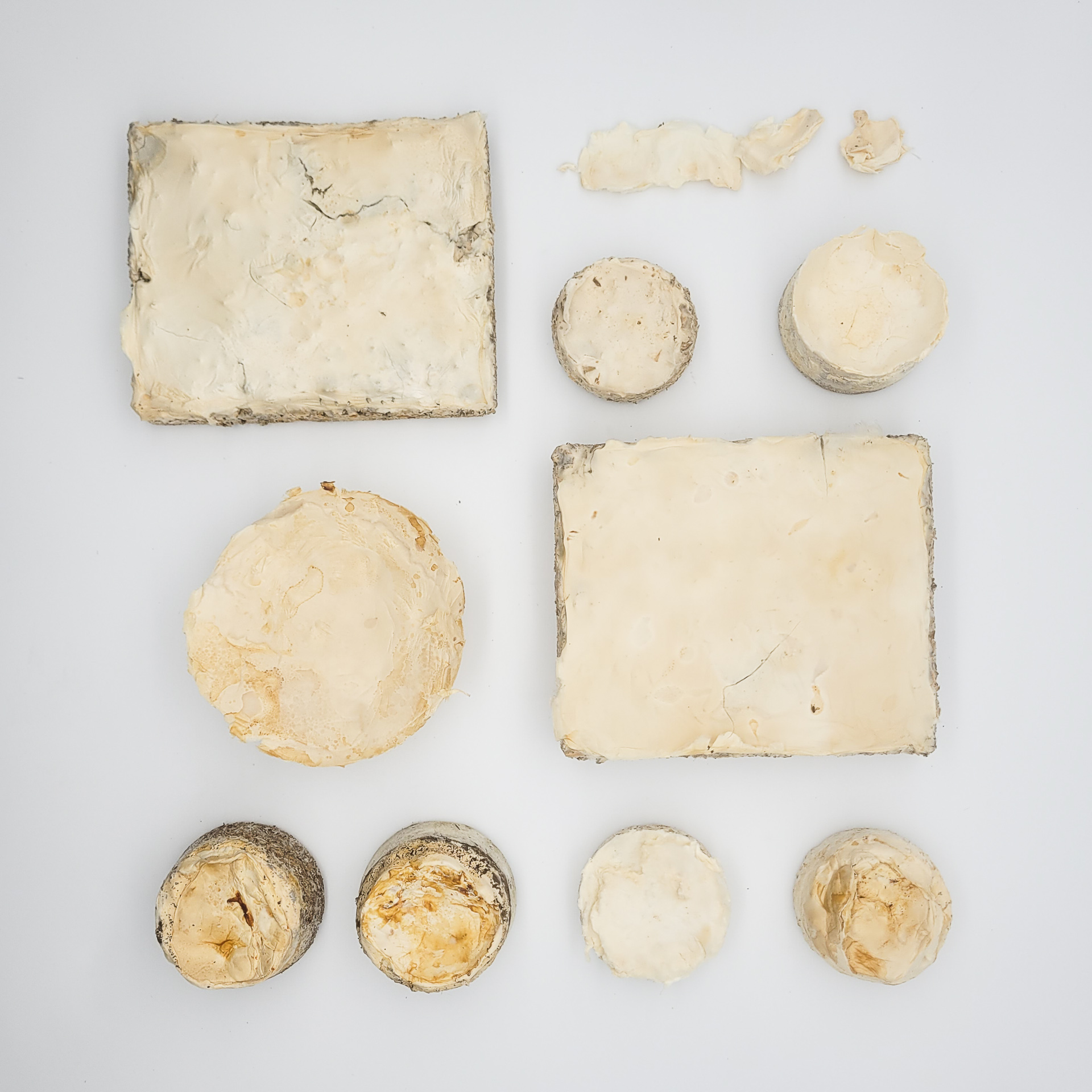
Evaluation
We evaluated the samples based on some basic properties we categorized as relevant when working with the materials. The most relevant to us were:
• the kind of fungus
• material it grew on
• material shrinkadge
• density with which the mycelium grew
• strength of the dried sample
• the Time the sample grew
However, our focus was heavily on the materials that we could use and the understanding of the workflow we needed to establish to grow mycelium-based materials. For this reason, we did document the amount of material and water we used for each sample, but didn't document the weight of the dry samples.The exact amounts of water, materials, and the way we worked are documented in two booklets.
Process
After our research, we started to grow the necessary mycelium according to the sources we found. We produced our own liquid mycelium from spores of fungi we purchased online in the form of mushroom dowels, collected right from nature, or even from mushrooms we bought at the grocery store. We bred:
• Oyster mushroom (Pleurotus ostreatus)
• Shii-Take (Lentinula edodes)
• Ganoderma lucidum
• Tinder fungus (Fomes fomentarius)
• king trumpet mushroom (Pleurotus eryngii)
• Pestalotiopsis microspora ( Decomposes Polyuretan)
After breeding the liquid mycelium, we filled a syringe to inject the mycelium into our prepared materials. Not all the samples we grew were successful; in fact, some of the samples with fungi like Lenticular erodes led to no successful results at all.
The best results came from the samples, which were bred from Pleurotus Ostreatus, Fomes Fomentarius, and Ganoderma Lucidum. Especially the samples with wood-decaying fungus were astonishingly hard after drying.
We documented the complete process behind growing the fungi and the samples we made in a protocol booklet, just like I documented the process of growing the fungi and preparations for every step.
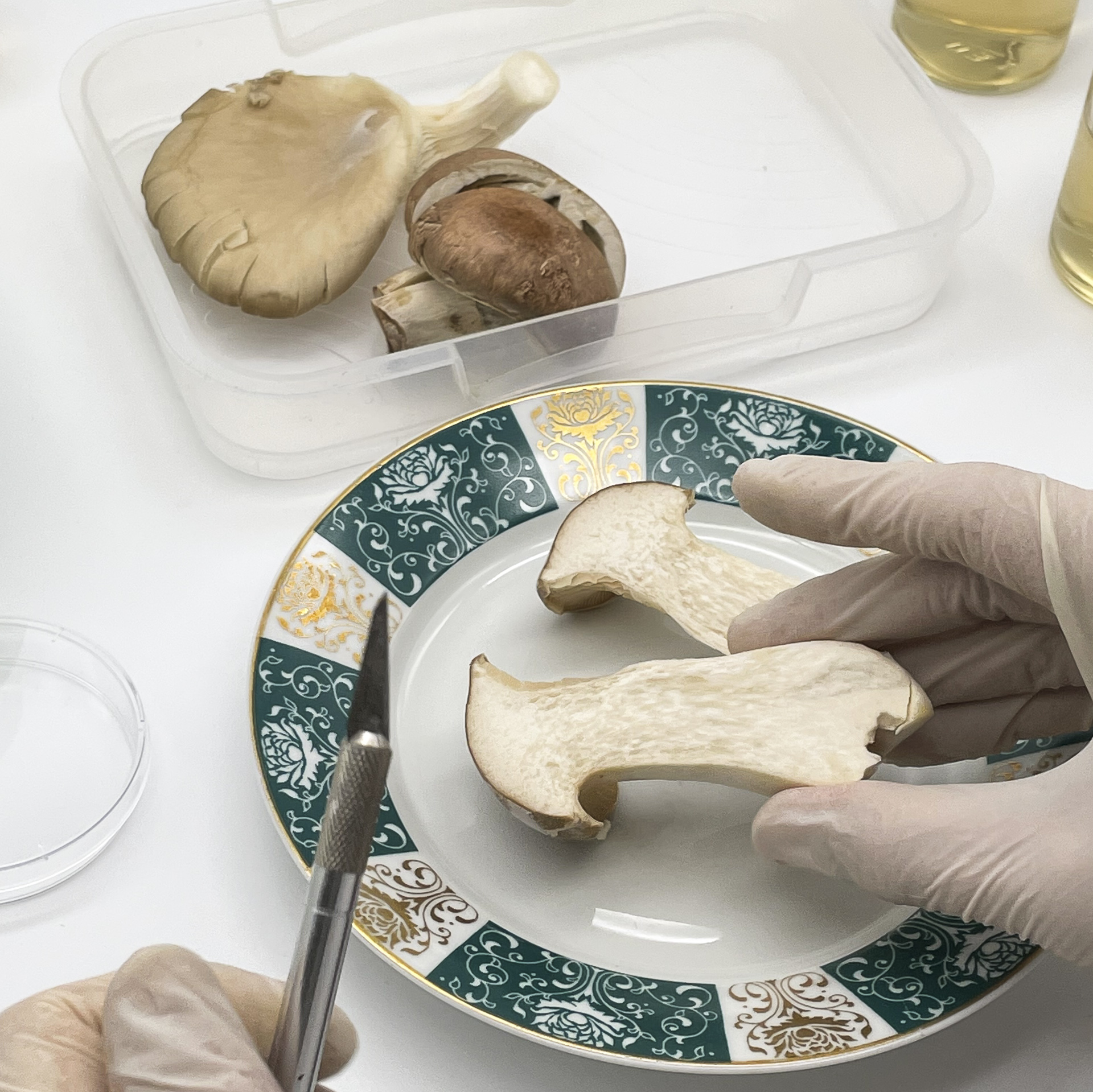
.jpg)
We tried growing mycelium on many different materials. Some of these were:
• Carrot-and-Apple peels
• Coffee grounds
• Tea
• Peanut hulls
• Avocado peels
• Beer spent grains
• Lime peels
• Banana peels
• Wood chips(different types)
And other. While doing our research, we have already found some information regarding a few of the materials and their potential, for example, about the wood chips. For other materials, we tested the percentage of water and dry mass that was necessary until we found the right balance.
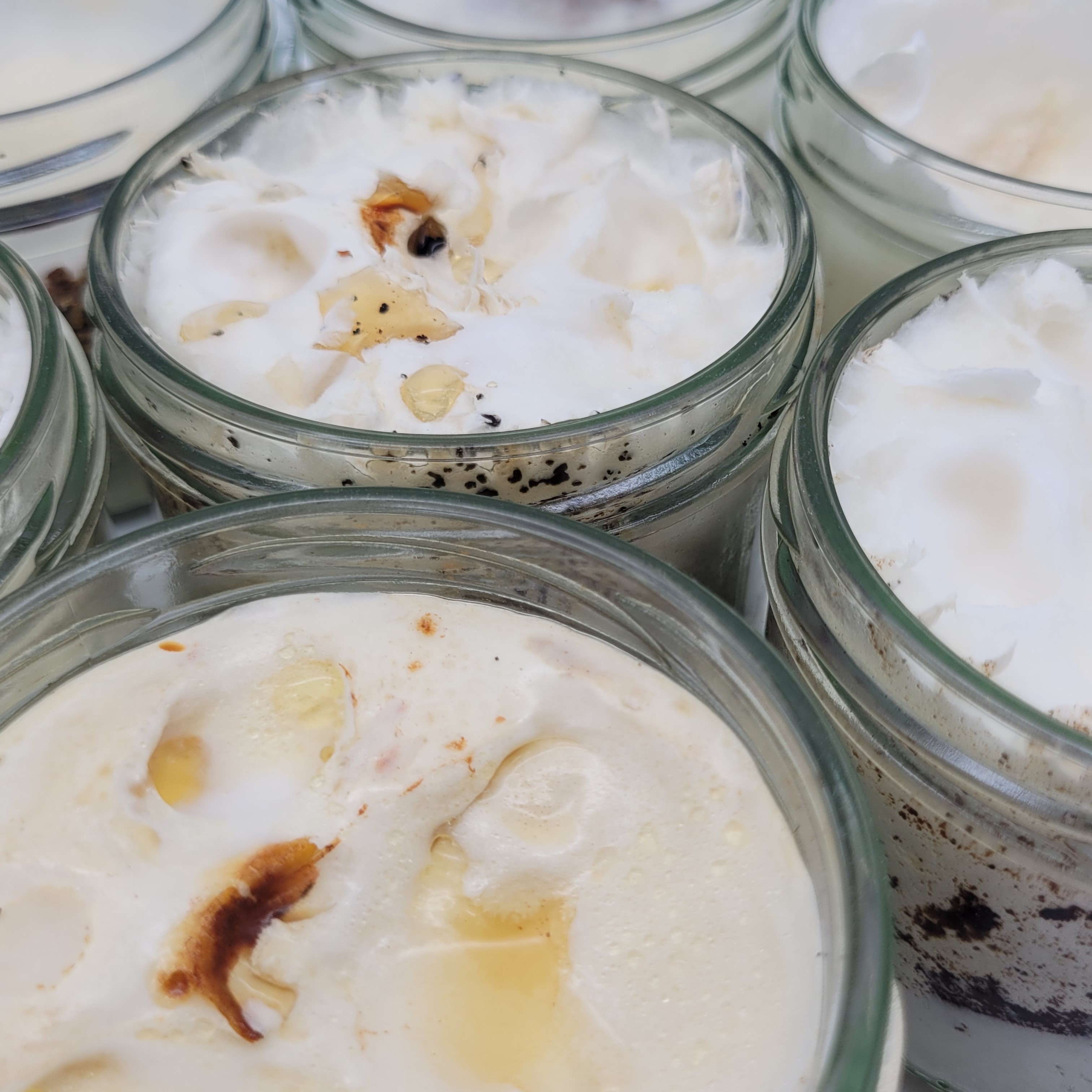
Thanks to my good friend Clemens Domsch
For this project, I worked together with my student and good friend Clemens Domsch, to whom I would like to express a special thanks at this point. It was nice and interesting to do a project together and to coordinate and divide the work, especially because it was the first real group project after the Corona crisis.
Remember Me
Remember Me
.png)
What is nitinol?
Nitinol was developed in 1958 at the Naval Ordnance Laboratory by William J. Buehler and Frederick Wang. The name is derived from the nickel and titanium, and from the initials of the Naval Ordnance Laboratory. Nitinol is a shape memory alloy, which consists of approx. 55% nickel, and the other part of titanium.
Normal nitinol has the ability to "remember" its shape, if its temperature is between -20 °C and 110 °C (depending on the percentage of the alloy). The original shape of the material can be changed by fixating it in the the desired "original shape" and heating it to over 500 °C.
Nitinol is used to produce surgical tools, stents or even inflatable, woven tires for aerospace concepts that need a long lifespan. Unfortunately, the manufacturing process of nitinol is very complex because the alloy must be produced in a vacuum, which causes the high price.
About "Remember me"
For this project, I had the intent to use as little of the material as possible to create a product concept that actually solves a problem. The problem I focused on was actually the increasing duration of drought periods. Due to climate change in Europe and the results for European woods. The result of my design process was an (almost) completely autonomous water collector that catches water when it is raining and dispenses it automatically over a long period of time. This is achieved by using the sunlight and warmth produced by it to open and close the nitinol vent.
.png)
.png)
.png)
An automatic watering system
I started out with a variety of ideas. Initially, I intended to build a big collector that would be placed on the ground to collect water. After some consultations, I chose to concentrate on an iteration that is actually hanging in the trees to collect water. However, the principle of the collector is basically the same for both of the concepts, so I consider the hanging one to be a general concept explanation for both concepts.
.png)
Prototyping
The video below shows the complete prototyping process, from sketches, over paper prototypes to molded lenses made from epoxy resin. However, the most important steps are documented again below, for better understanding.
Vent prototypes
The vent iterations show the simple mechanism that enables the autonomous functioning of the system. A feather steel spring is pushing down a nitinol spring underneath or above it. Both springs are positioned inside a cylinder, which is closed with a round converging lens. Between the springs, a plate is connected to a plug, which keeps the vent closed or open, by a thin rod. If sunlight shines onto the lens, the light is focused onto the springs, which causes the nitinol spring to expand. As aresult, the vent is opened, and water is flowing out of it. Some of the water floats down to the spring, which causes her to cool down and shrink. This causes the vent to close itself automatically. Once the sunlight reheats the nitinol again, the process restarts.
.png)
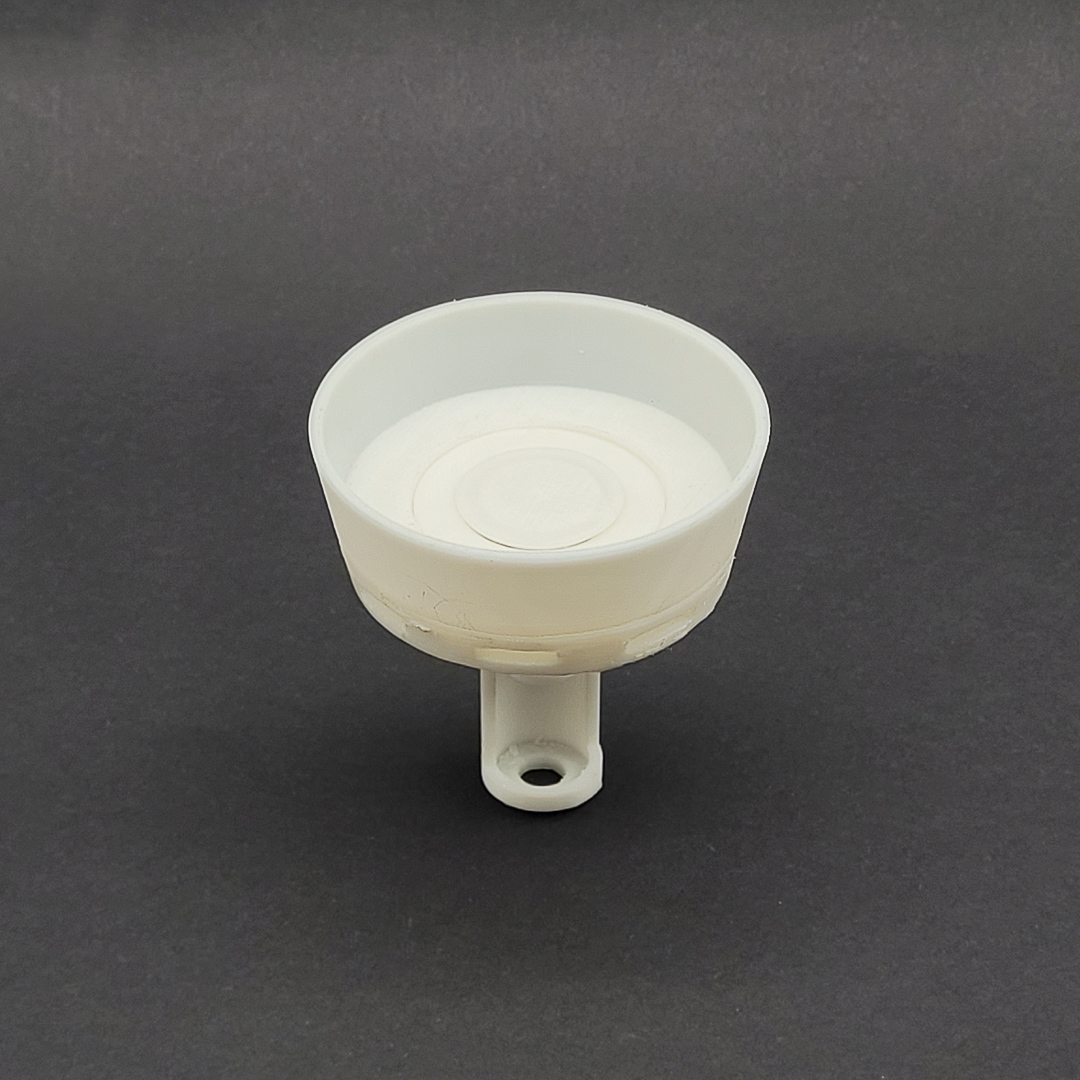
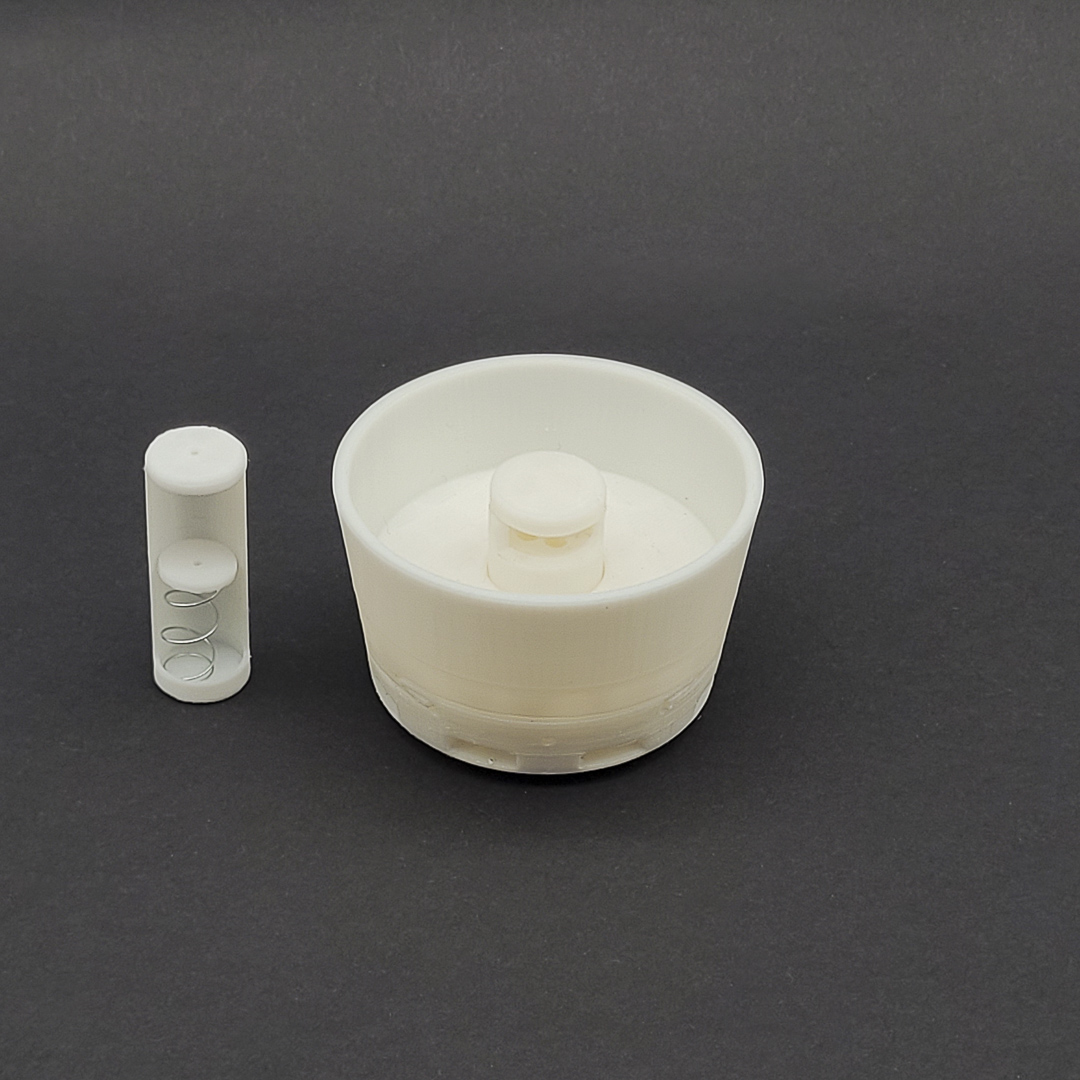
Final prototype
The video below shows my functioning prototype. The final design aims to catch as much sunlight as possible from below the water collector. Therefore, it extends from the body of the vent. In general, a longer period between the opening of the vent and the closing by the floating water needs to be achieved in the future, but the prototype proved my concept at least.
Water container
The containers for the water collection process aim to collect a lot of water if they are empty and lose as little water as possible, if they are full, to condensation. By increasing the weight that is carried by the containers if rain is collected inside of them, their shape is shifting from open and almost flat to a cocoon-like shape. The models below show my first attempts to implement this functionality by using nitinol wire.
.png)
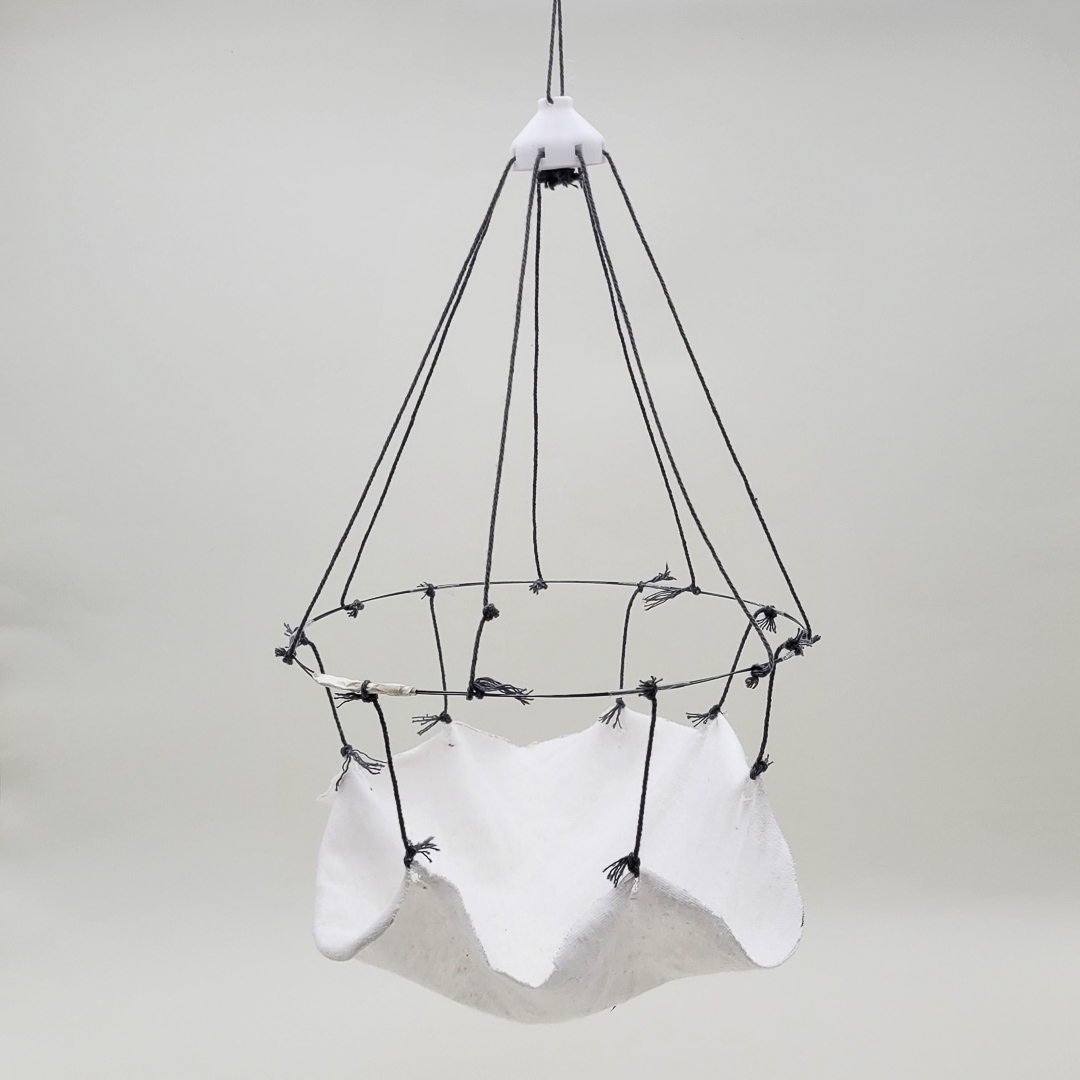
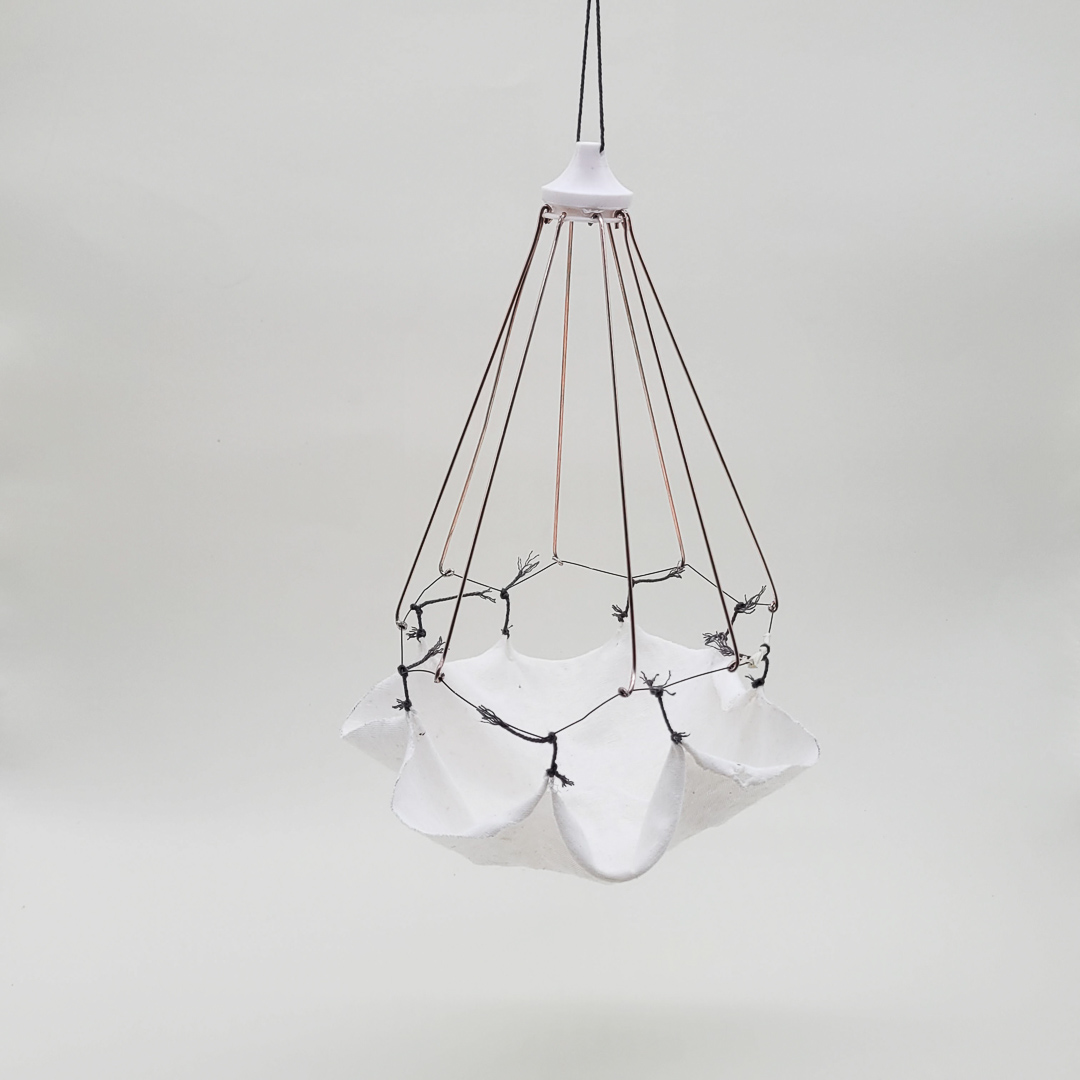
The complete prototype
After the first prototypes didn't work, the final water collector concept did by using tiny amounts of nitinol. This is achieved by using the extreme flexibility of small nitinol wires, which are positioned in the holding and flexing mechanism of the container, as seen in the pictures below.
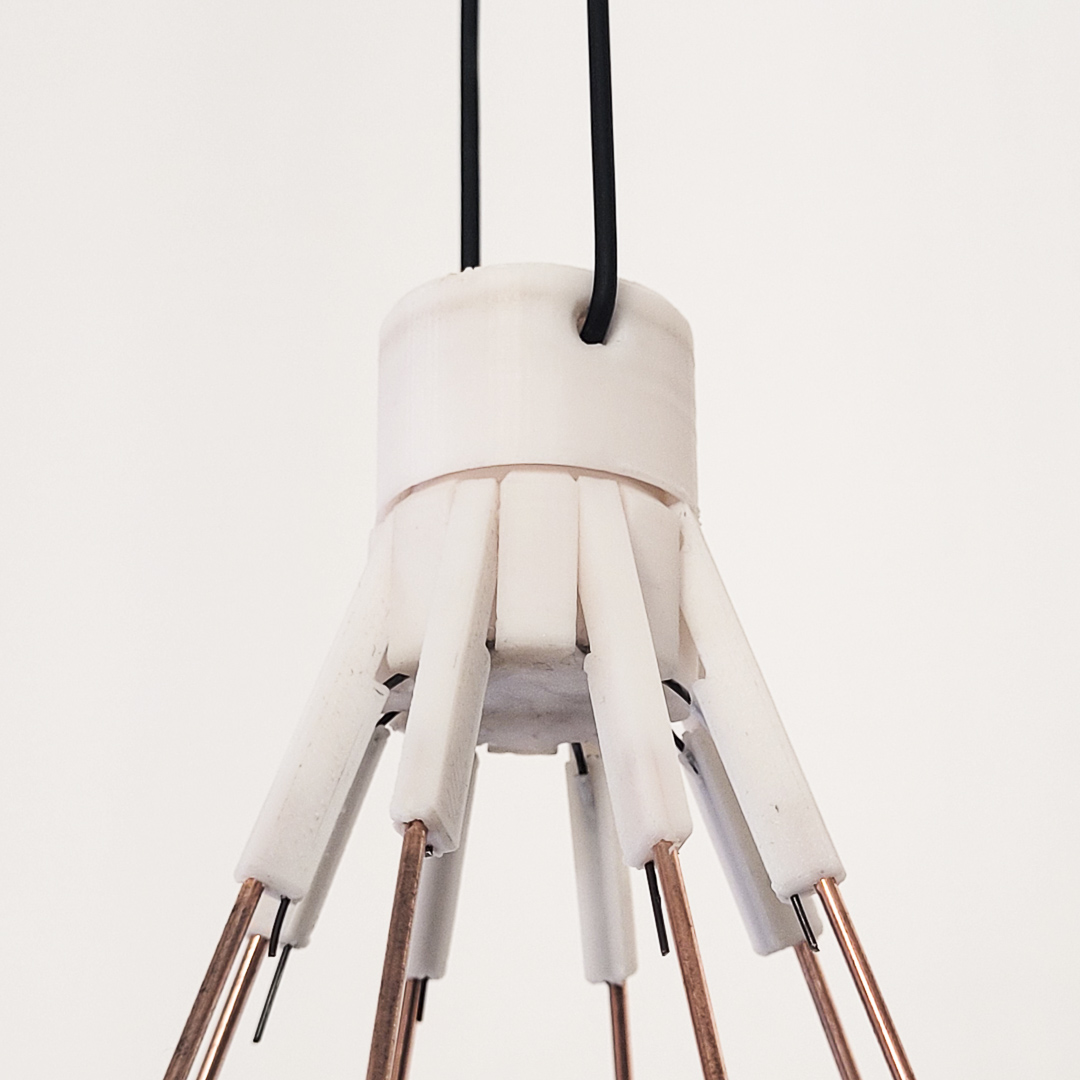
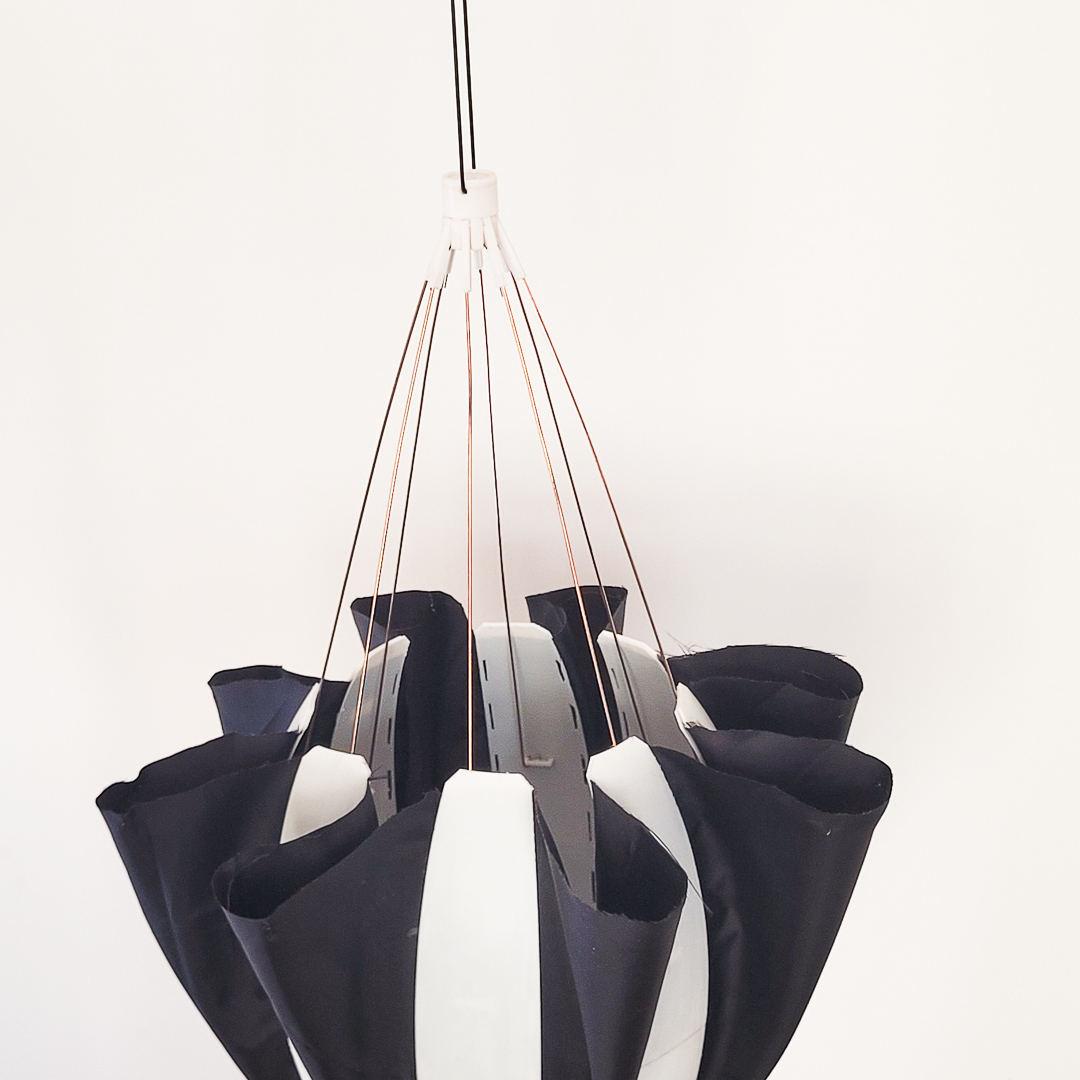
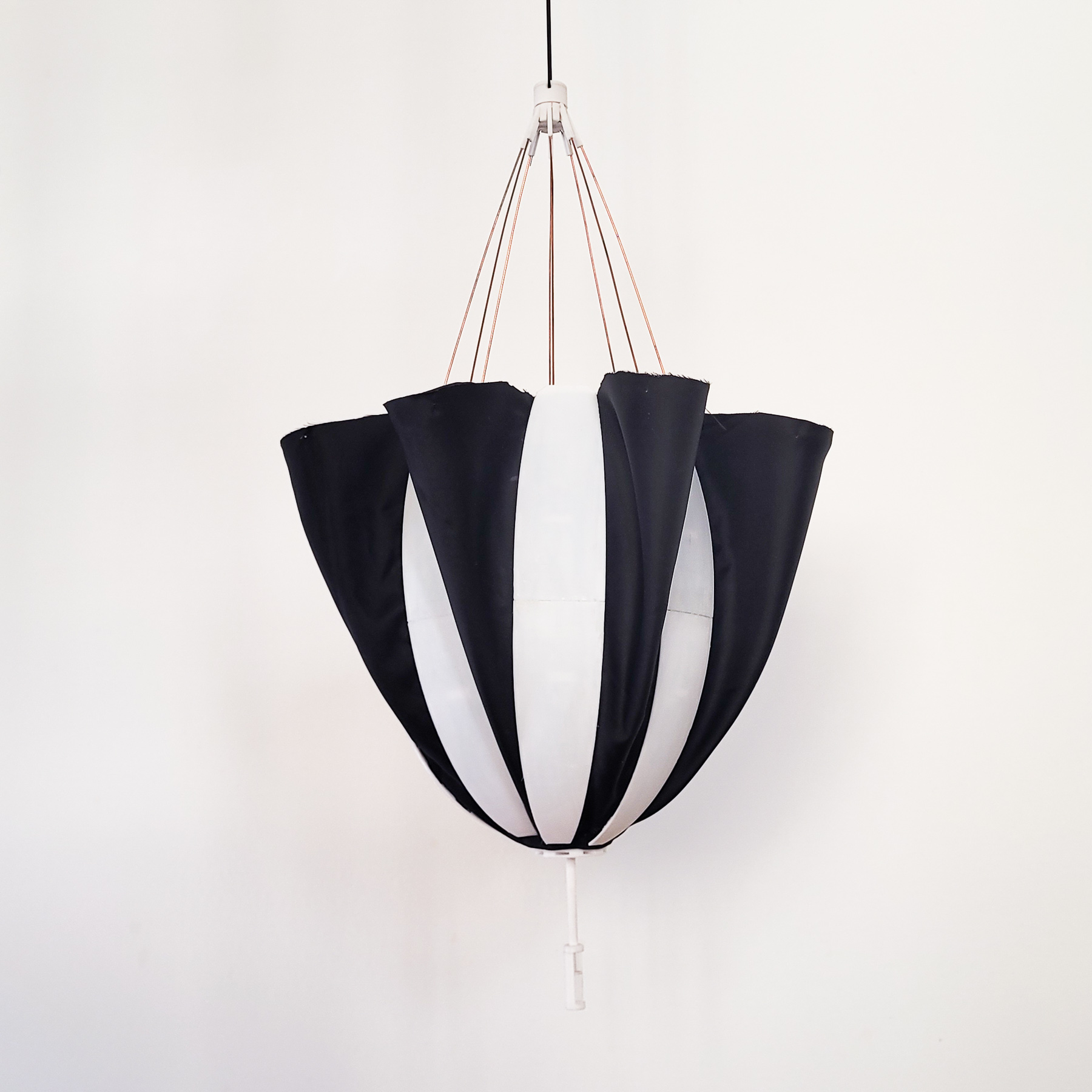
Product animation 01
The video shows the complete construction of the concept in the state it was in when finishing the project for presentation. For optimization, the vent mechanism would need to be refined, and the water container should be produced from much fewer parts than it is right now. But in general, the concept could be used to automated water collection and dispense in many cases, reducing the need for individual people to take care of watering in gardens or plantations, at least partially, without having to use high-tech equipment that uses even more rare and expensive materials and needs electricity to work.
.png)
What is nitinol?
Nitinol was developed in 1958 at the Naval Ordnance Laboratory by William J. Buehler and Frederick Wang. The name is derived from the nickel and titanium, and from the initials of the Naval Ordnance Laboratory. Nitinol is a shape memory alloy, which consists of approx. 55% nickel, and the other part of titanium.
Normal nitinol has the ability to "remember" its shape, if its temperature is between -20 °C and 110 °C (depending on the percentage of the alloy). The original shape of the material can be changed by fixating it in the the desired "original shape" and heating it to over 500 °C.
Nitinol is used to produce surgical tools, stents or even inflatable, woven tires for aerospace concepts that need a long lifespan. Unfortunately, the manufacturing process of nitinol is very complex because the alloy must be produced in a vacuum, which causes the high price.
About "Remember me"
For this project, I had the intent to use as little of the material as possible to create a product concept that actually solves a problem. The problem I focused on was actually the increasing duration of drought periods. Due to climate change in Europe and the results for European woods. The result of my design process was an (almost) completely autonomous water collector that catches water when it is raining and dispenses it automatically over a long period of time. This is achieved by using the sunlight and warmth produced by it to open and close the nitinol vent.
.png)
.png)
.png)
An automatic watering system
I started out with a variety of ideas. Initially, I intended to build a big collector that would be placed on the ground to collect water. After some consultations, I chose to concentrate on an iteration that is actually hanging in the trees to collect water. However, the principle of the collector is basically the same for both of the concepts, so I consider the hanging one to be a general concept explanation for both concepts.
.png)
Prototyping
The video below shows the complete prototyping process, from sketches, over paper prototypes to molded lenses made from epoxy resin. However, the most important steps are documented again below, for better understanding.
Vent prototypes
The vent iterations show the simple mechanism that enables the autonomous functioning of the system. A feather steel spring is pushing down a nitinol spring underneath or above it. Both springs are positioned inside a cylinder, which is closed with a round converging lens. Between the springs, a plate is connected to a plug, which keeps the vent closed or open, by a thin rod. If sunlight shines onto the lens, the light is focused onto the springs, which causes the nitinol spring to expand. As aresult, the vent is opened, and water is flowing out of it. Some of the water floats down to the spring, which causes her to cool down and shrink. This causes the vent to close itself automatically. Once the sunlight reheats the nitinol again, the process restarts.
.png)
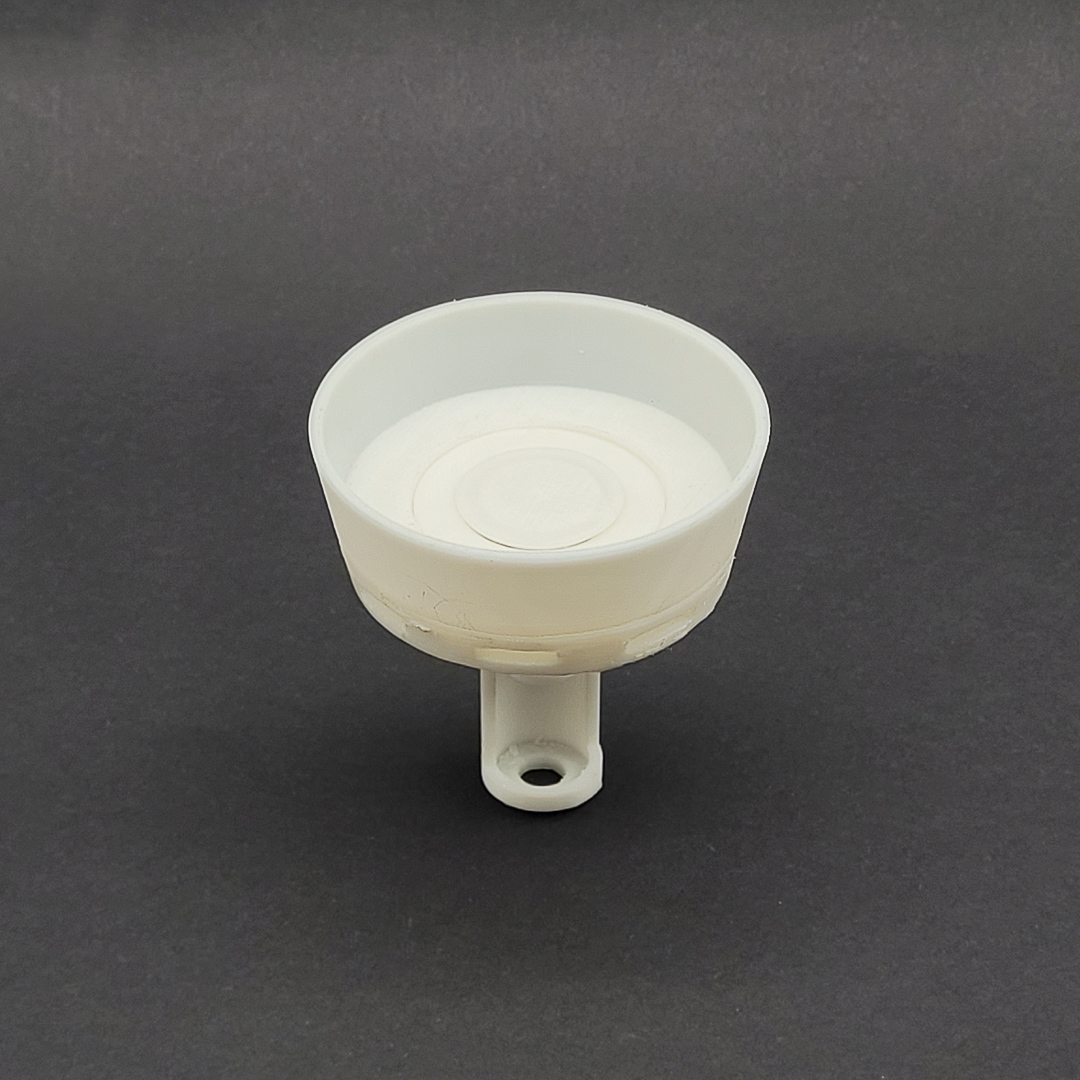
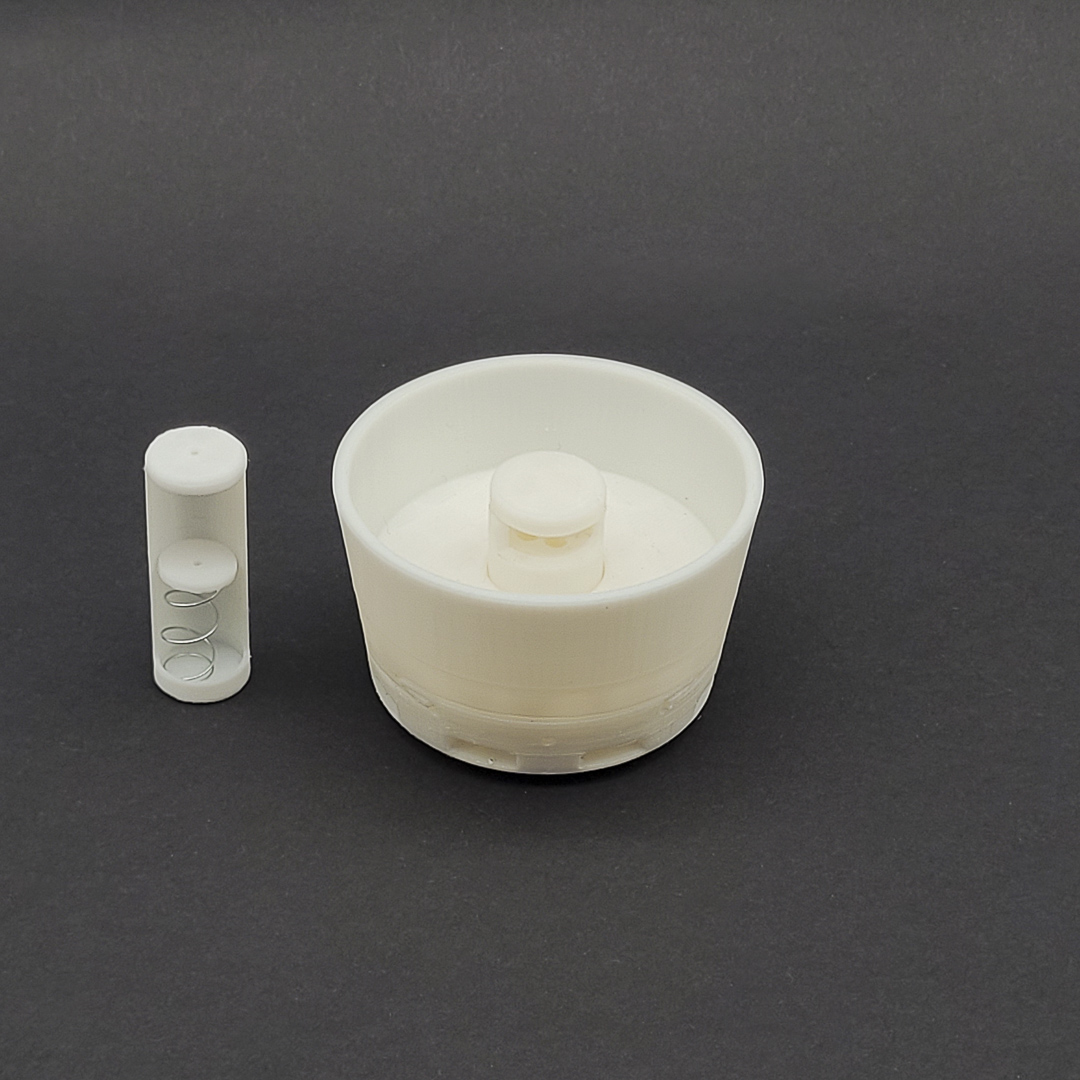
Final prototype
The video below shows my functioning prototype. The final design aims to catch as much sunlight as possible from below the water collector. Therefore, it extends from the body of the vent. In general, a longer period between the opening of the vent and the closing by the floating water needs to be achieved in the future, but the prototype proved my concept at least.
Water container
The containers for the water collection process aim to collect a lot of water if they are empty and lose as little water as possible, if they are full, to condensation. By increasing the weight that is carried by the containers if rain is collected inside of them, their shape is shifting from open and almost flat to a cocoon-like shape. The models below show my first attempts to implement this functionality by using nitinol wire.
.png)
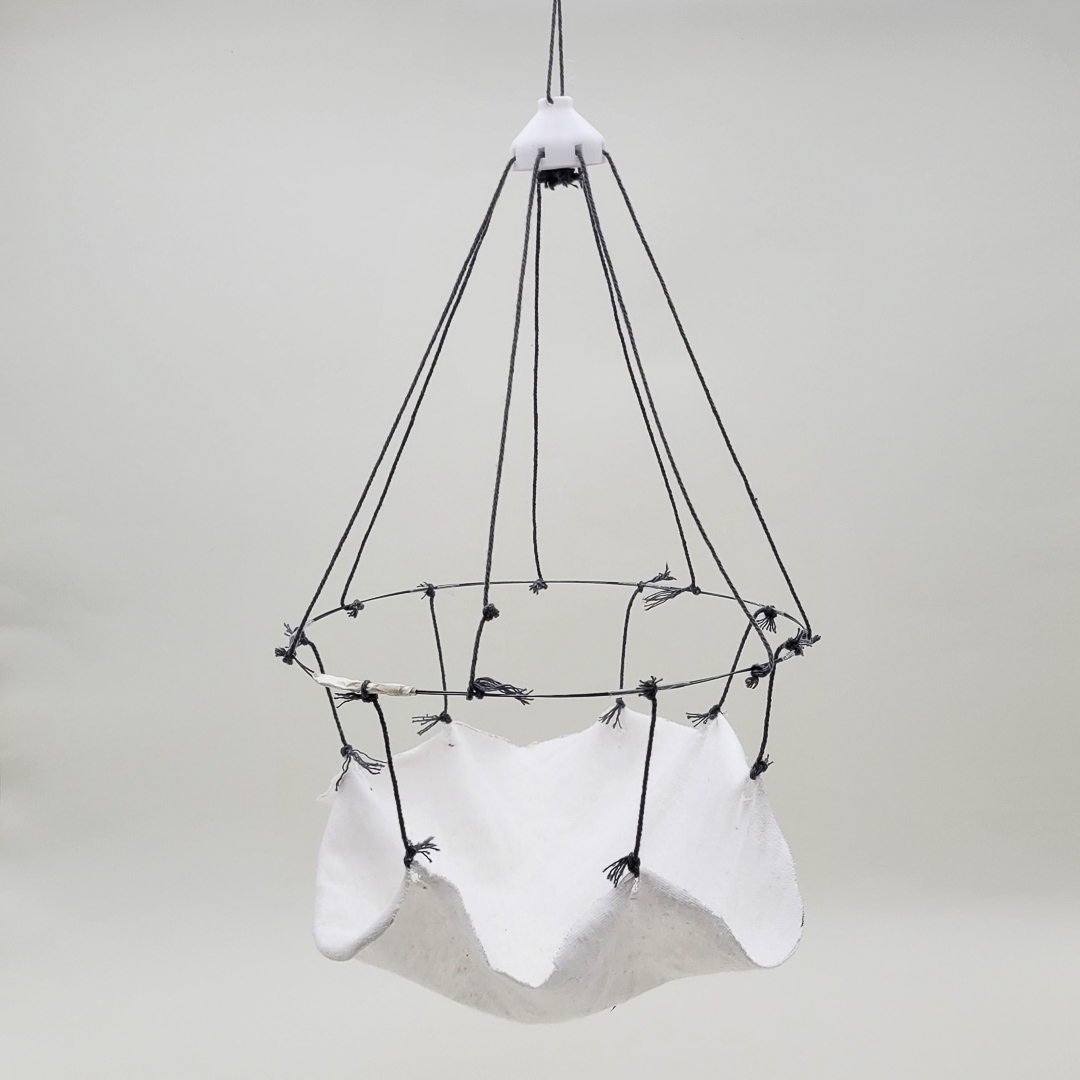
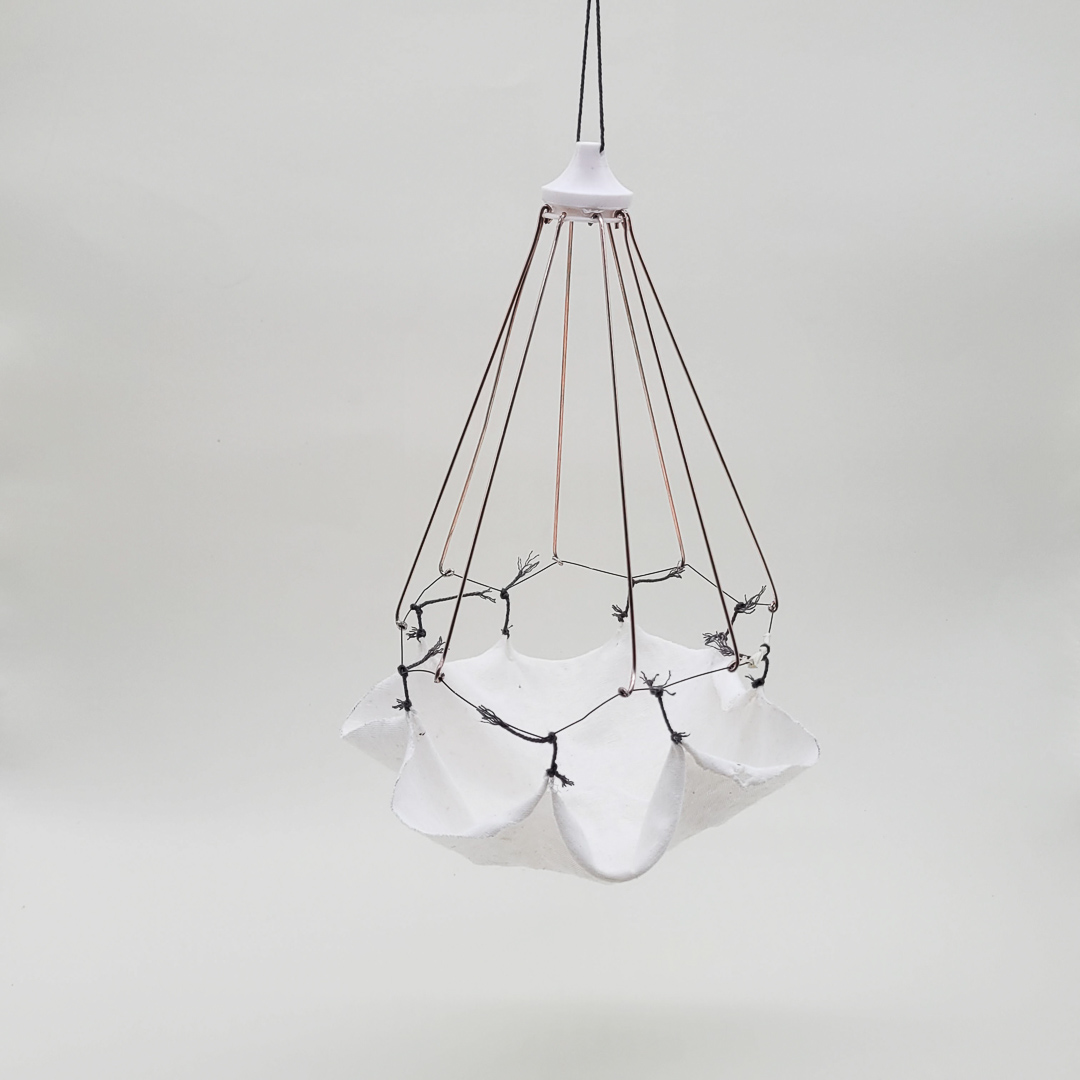
The complete prototype
After the first prototypes didn't work, the final water collector concept did by using tiny amounts of nitinol. This is achieved by using the extreme flexibility of small nitinol wires, which are positioned in the holding and flexing mechanism of the container, as seen in the pictures below.
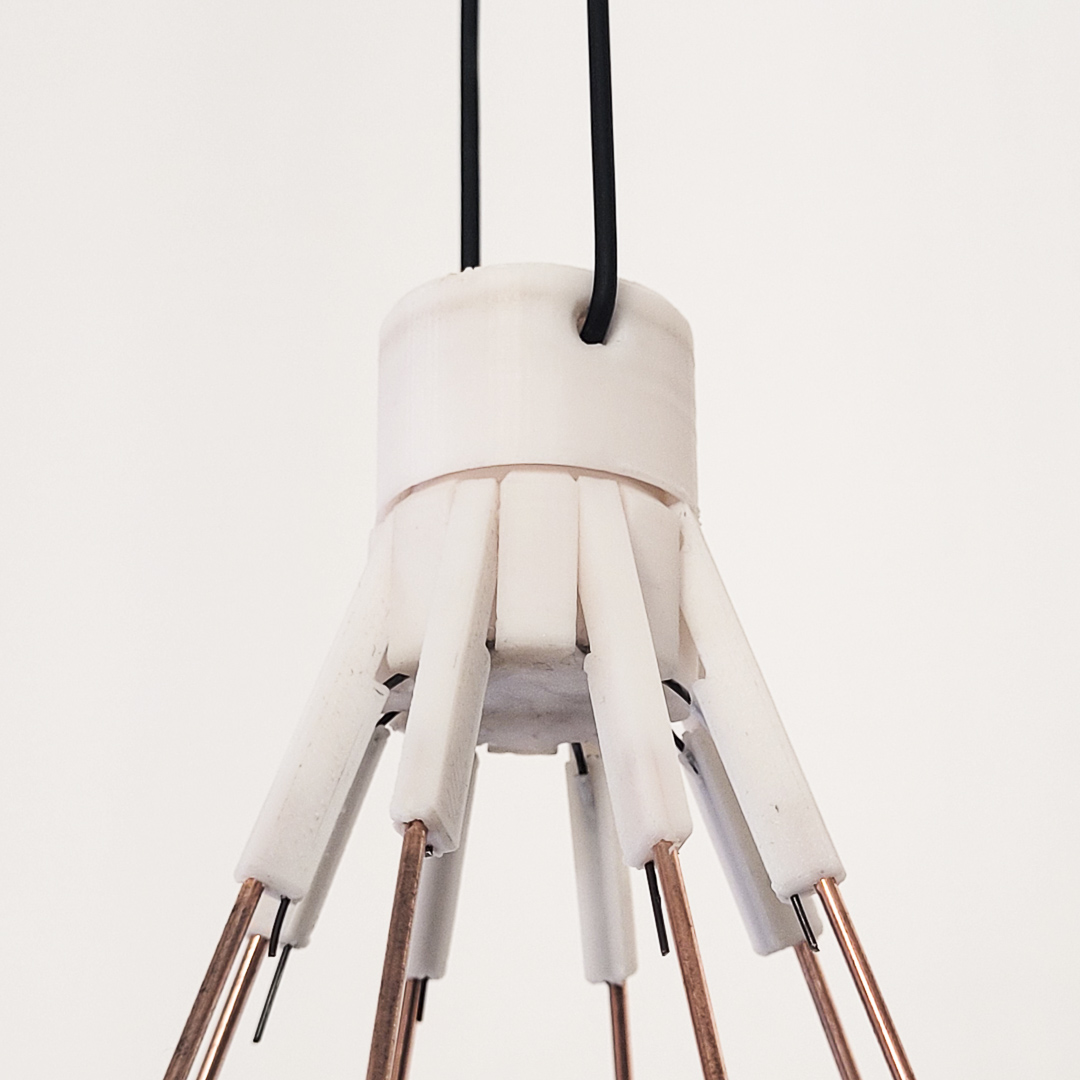
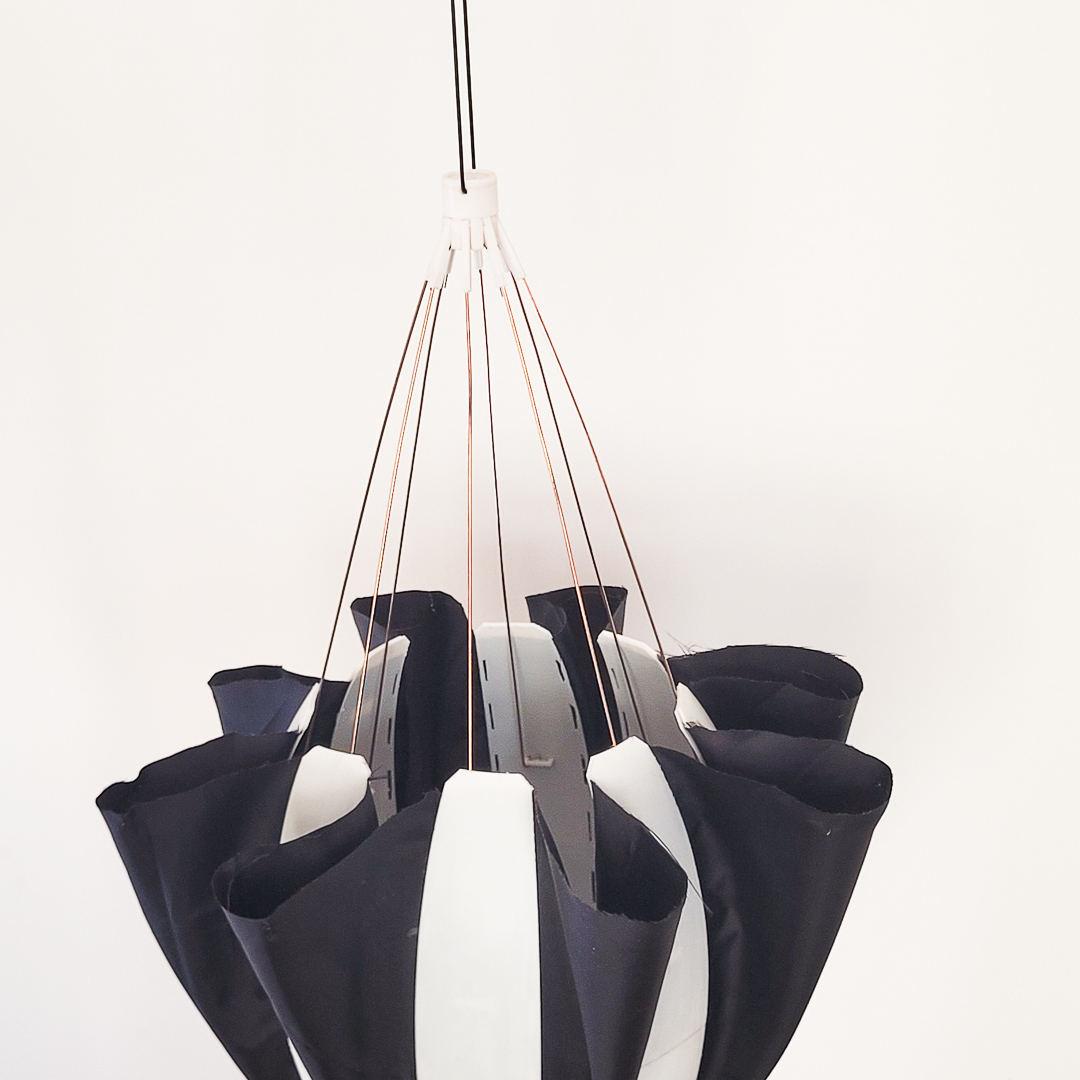
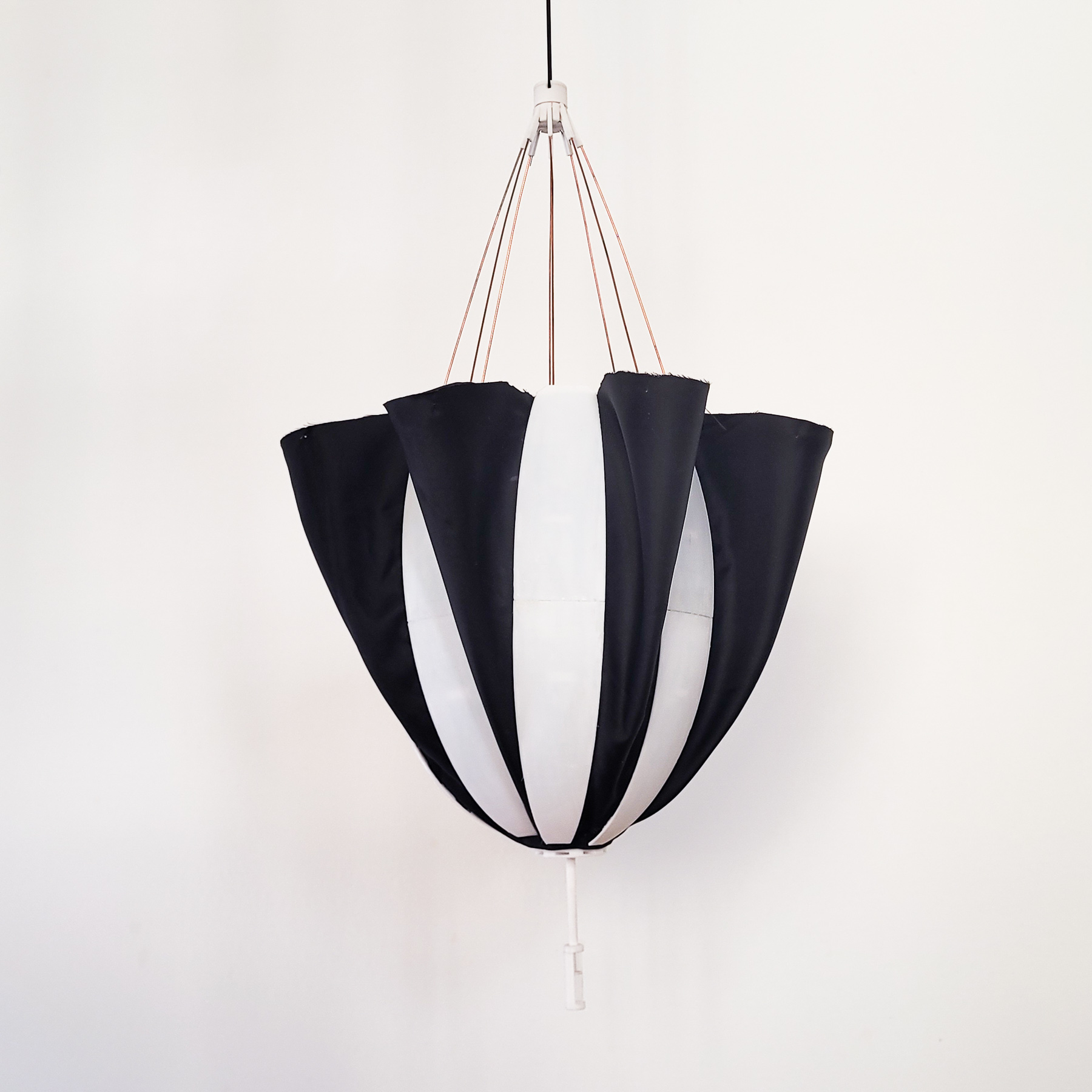
Product animation 01
The video shows the complete construction of the concept in the state it was in when finishing the project for presentation. For optimization, the vent mechanism would need to be refined, and the water container should be produced from much fewer parts than it is right now. But in general, the concept could be used to automated water collection and dispense in many cases, reducing the need for individual people to take care of watering in gardens or plantations, at least partially, without having to use high-tech equipment that uses even more rare and expensive materials and needs electricity to work.
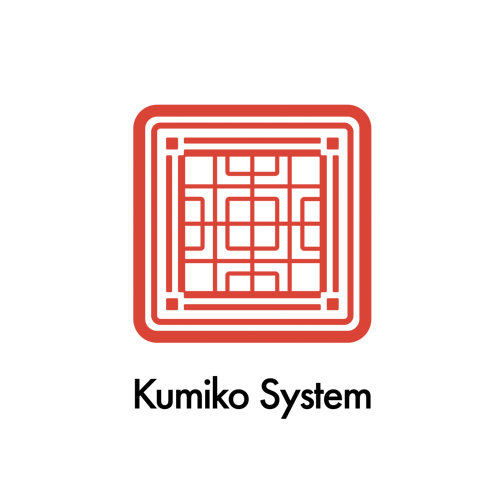
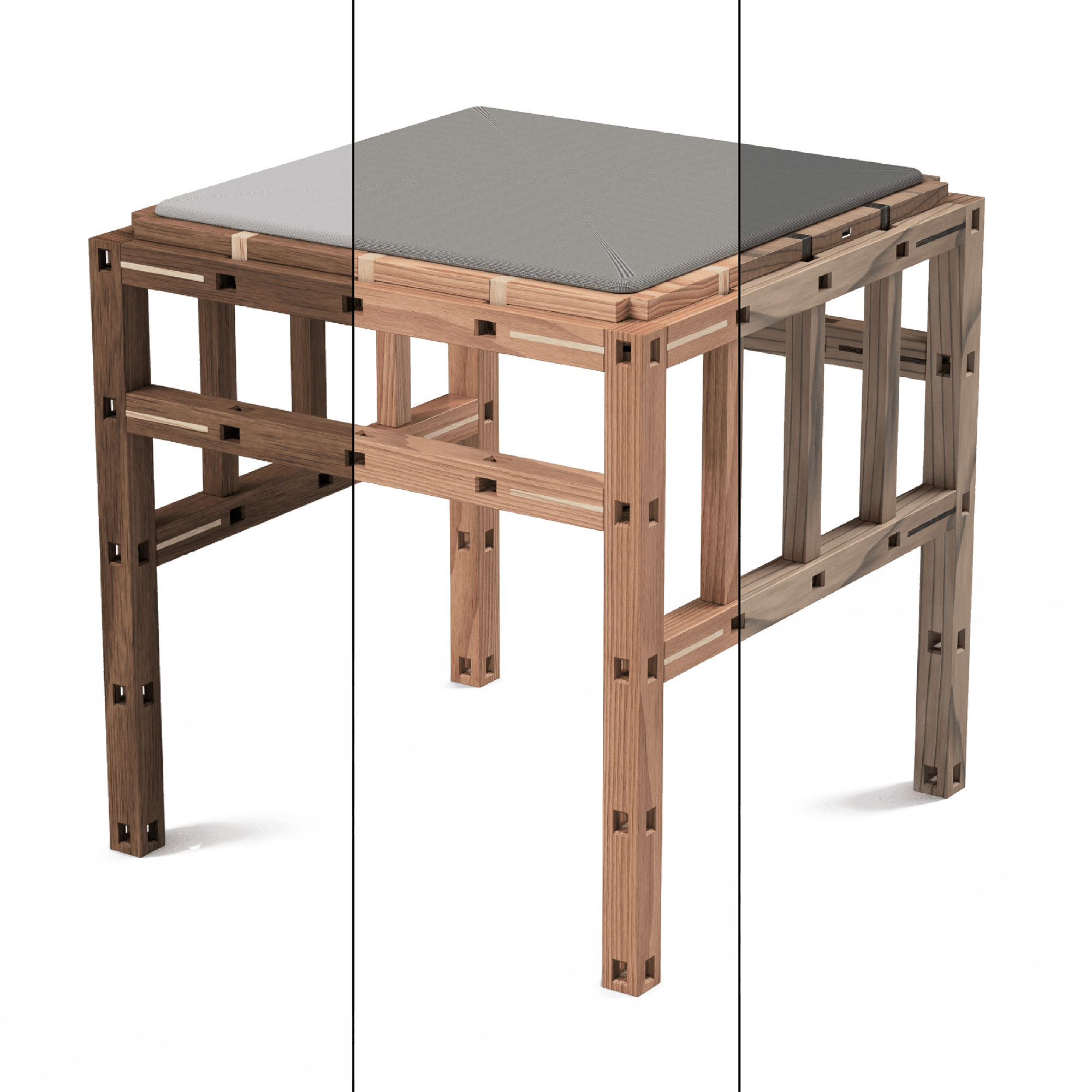
About washi ramie kumiko
The starting point for the project "Washi Rami kumiko" were the two materials washi and ramie and a Japanese woodworking technique called kumiko. The materials and woodworking techniques are deeply rooted in Japanese and Asian culture.
The starting point was the task of transferring the materials and craft techniques to the European cultural space.
I had the intent to design a modular furniture concept focused on the kumiko aspect of the project and on bringing the woodworking technique and effort connected to it closer to people that consume products originating from this craft. The project documented here focuses on only one possible design that originated from the modules, as an example.
Washi is a paper that is produced from mulberry fibers and has been used in Japanese craftsmanship for centuries. It's mostly known for its use in shoji doors (traditional Japanese sliding doors) or lanterns.
Ramie fiber, also called china linen or grass linen, is a fabric that strongly resembles linen in terms of materiality and is obtained from ramie plants, a plant belonging to the nettle family.
Kumiko or "kumiko zaiku" is a traditional woodworking technique from Asia that is based on the principle of sticking together wooden patterns without using any glue.
Prototyping
In the beginning, I decided to use a simple geometric form language, as it has been common in Japan for centuries. The prototypes are made on a small scale (4 cm to 10 cm), which made it possible for me to test numerous variations in three-dimensional space.
I used mat board for the models. Additionally, I used a small roll of fiber fleece tape to better represent the shape of the cushions.
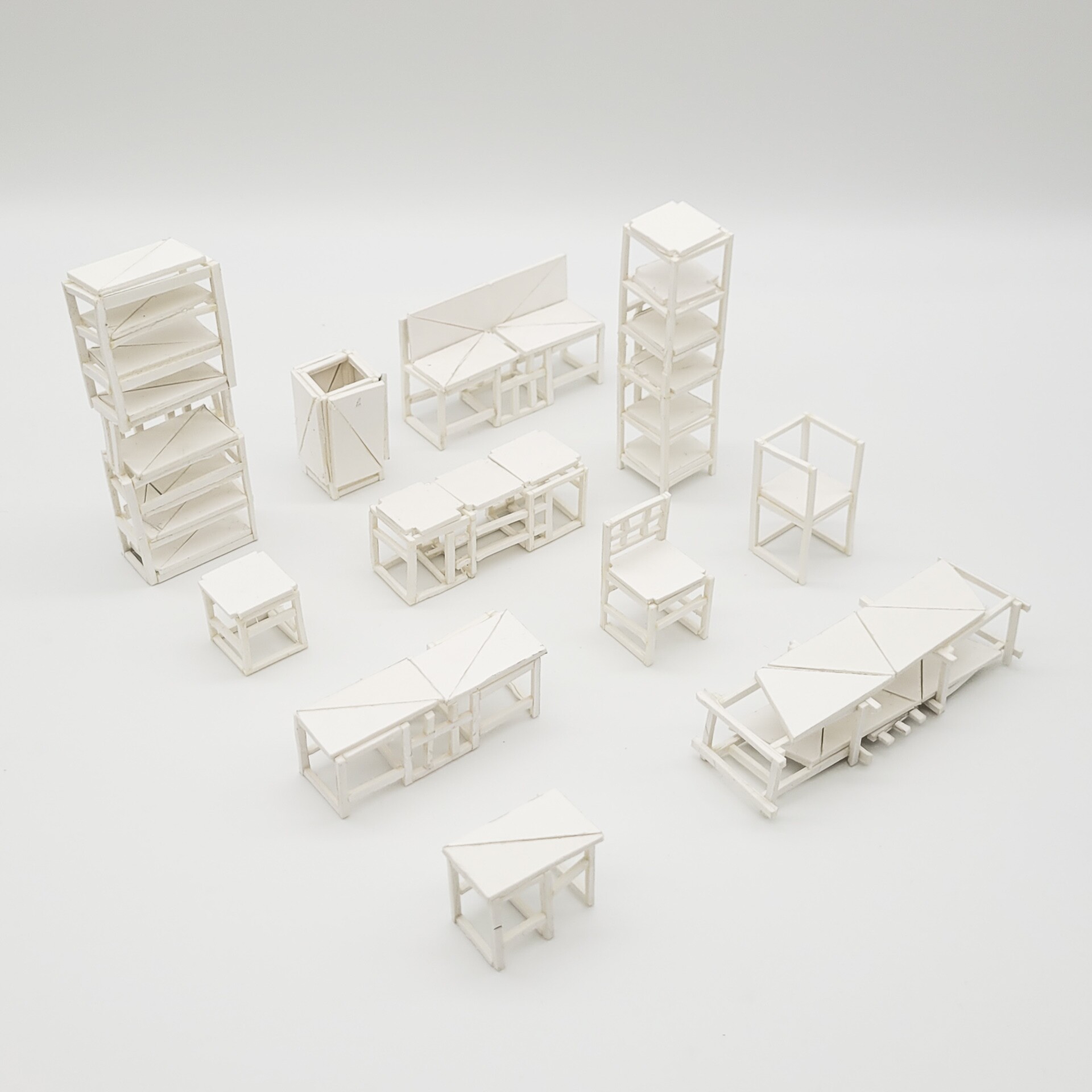
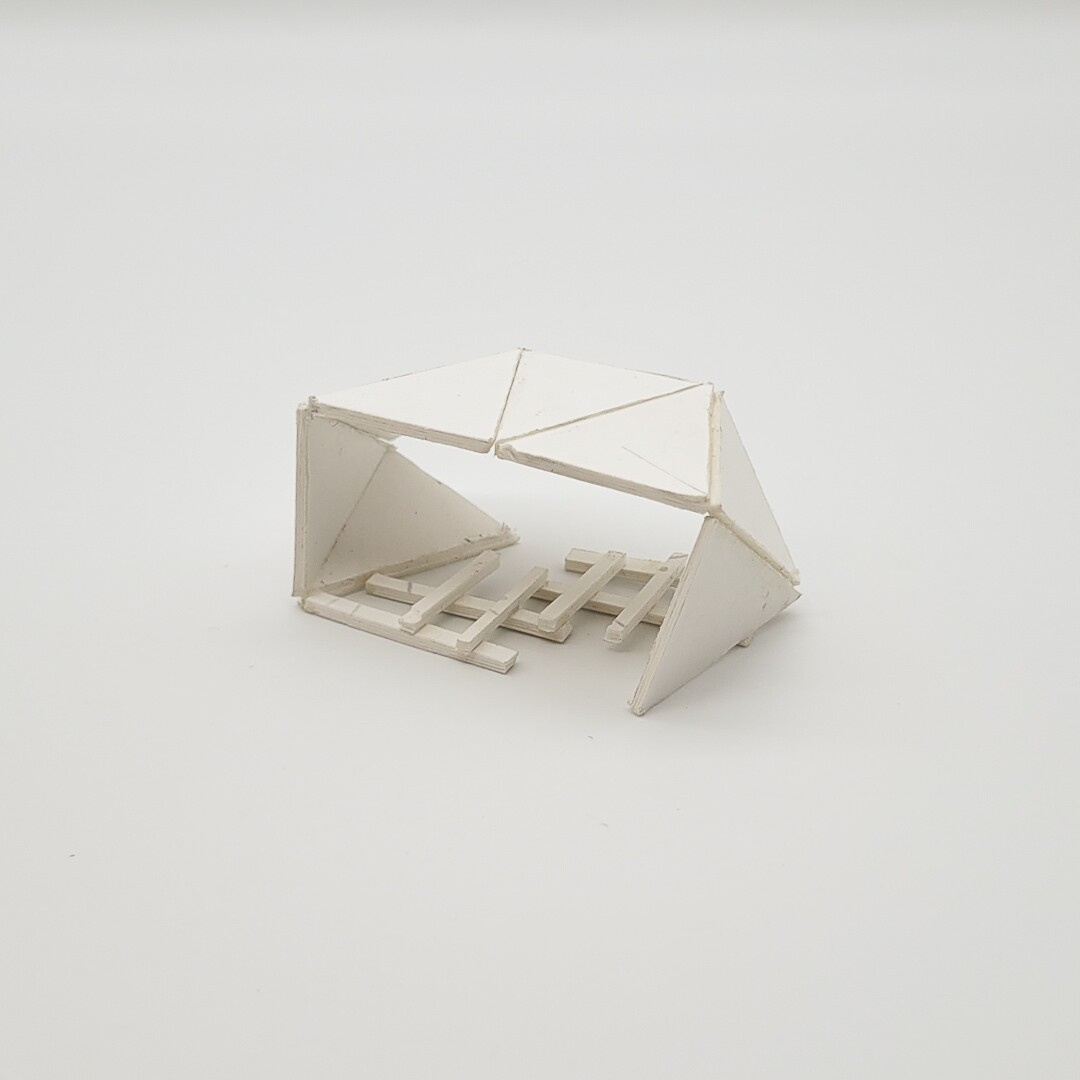
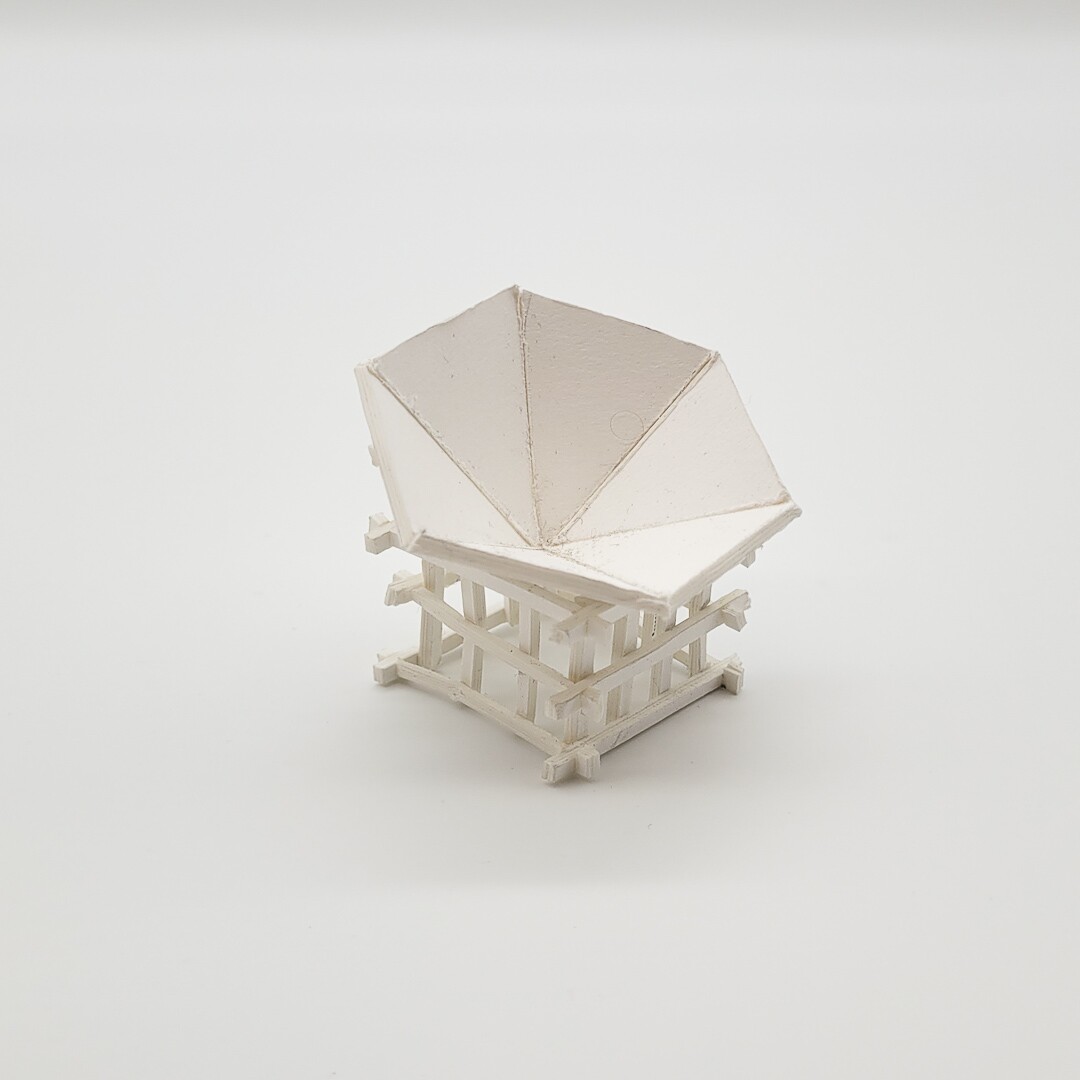
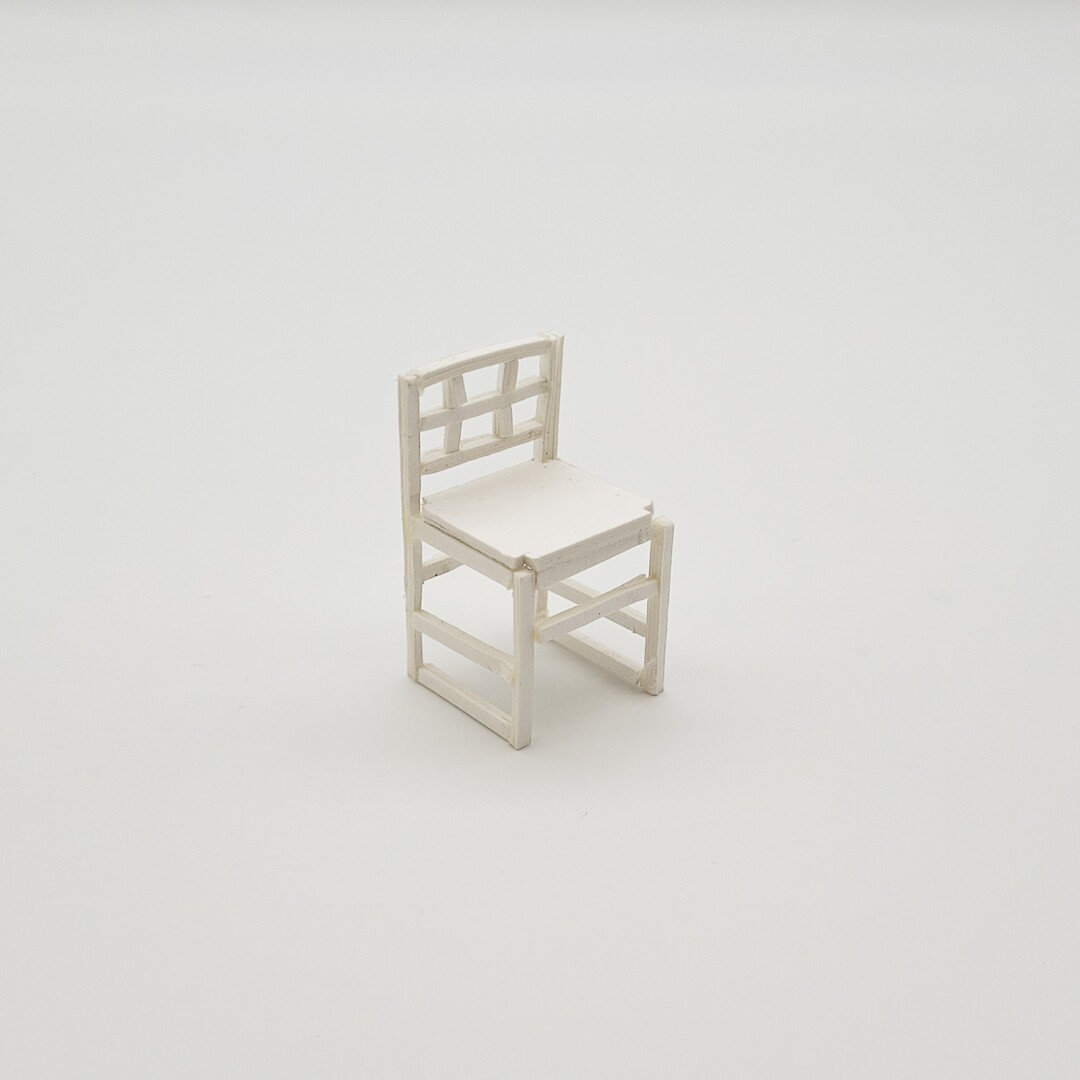
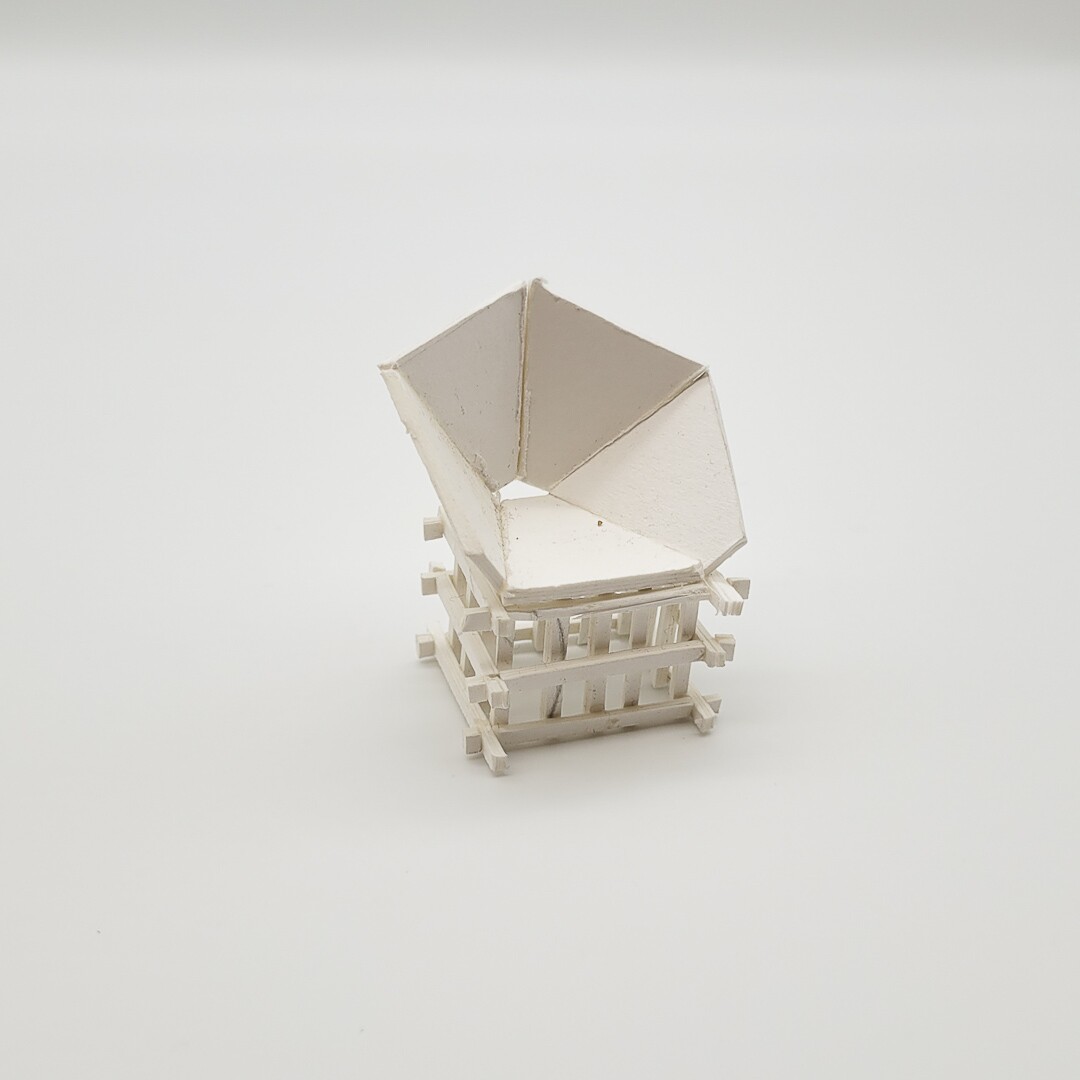
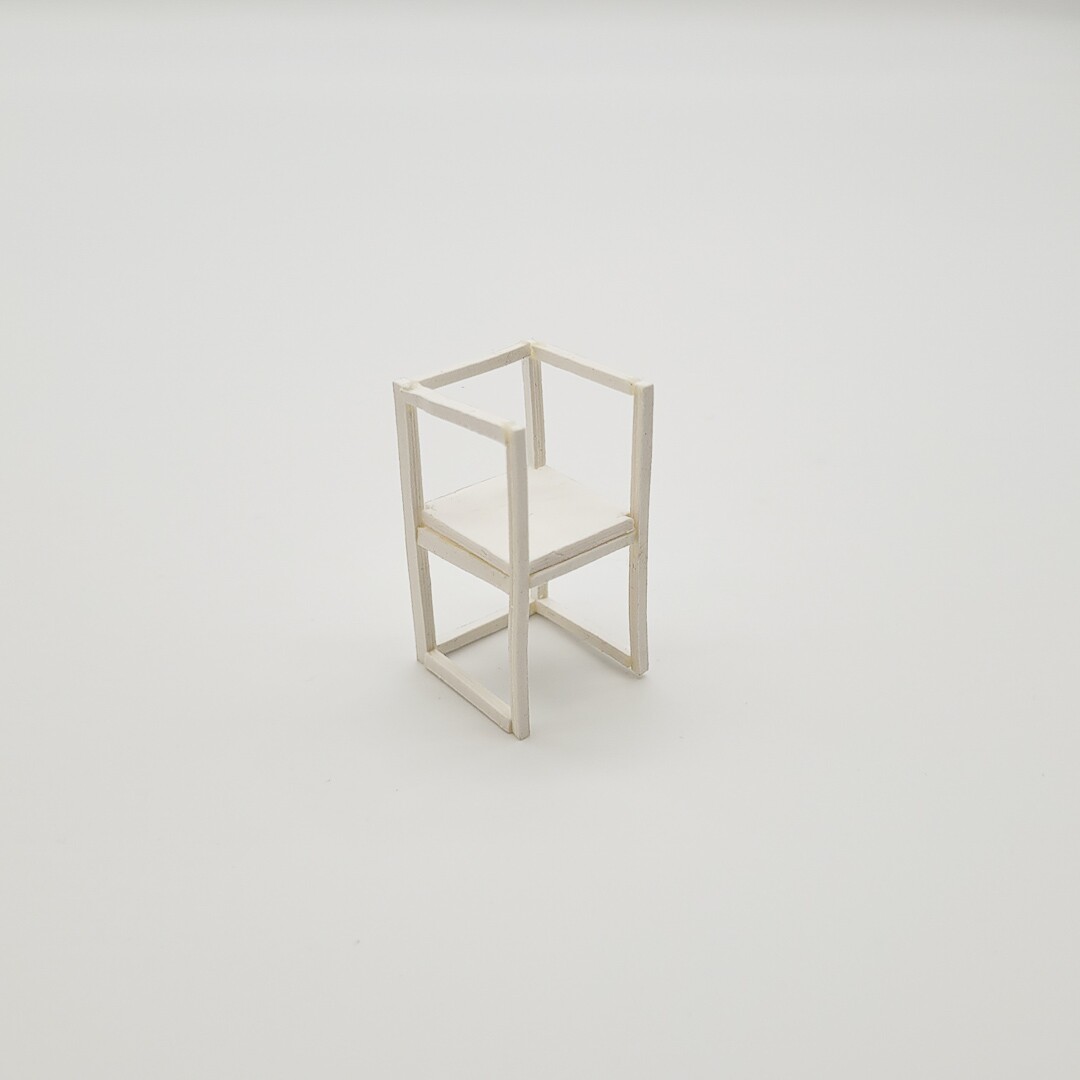
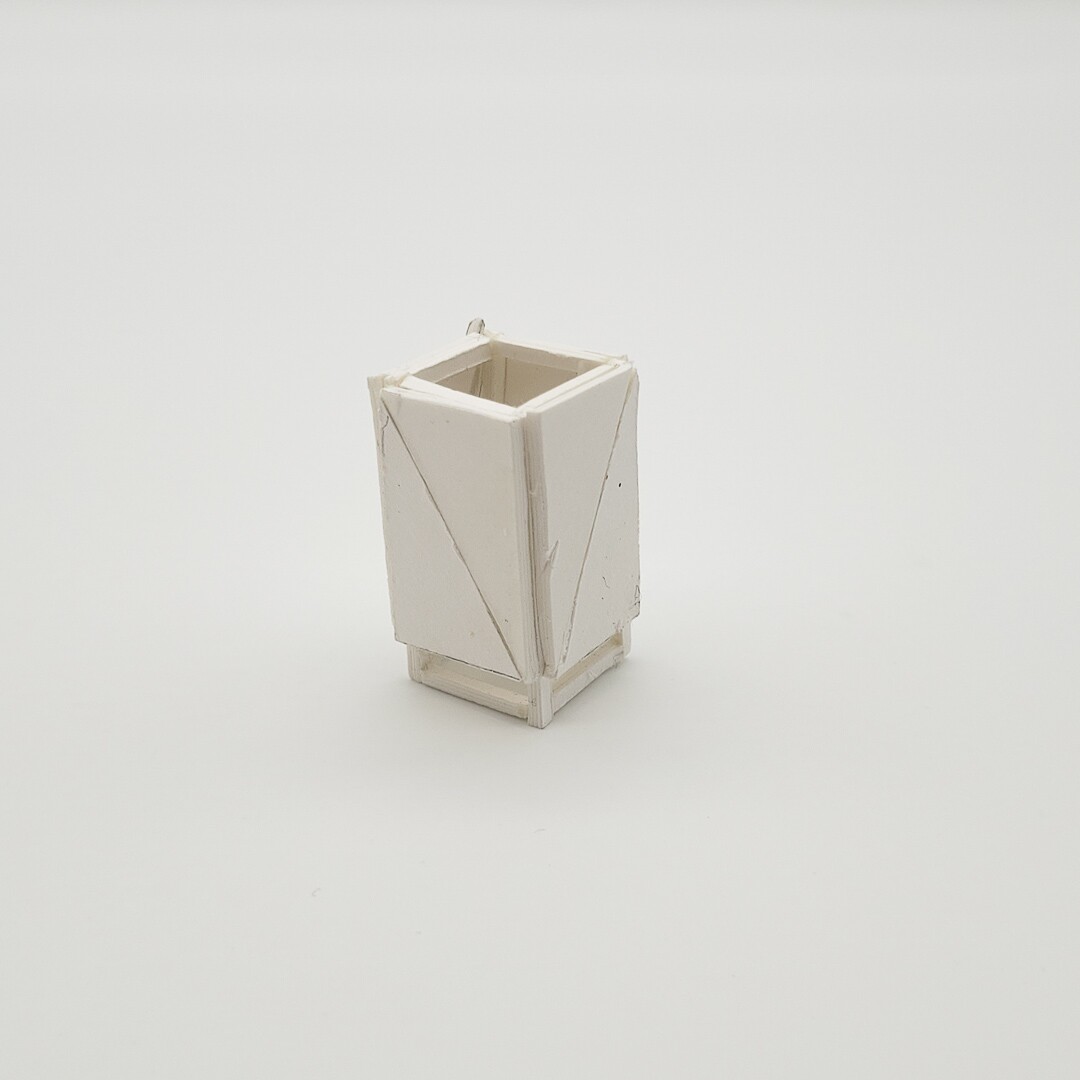
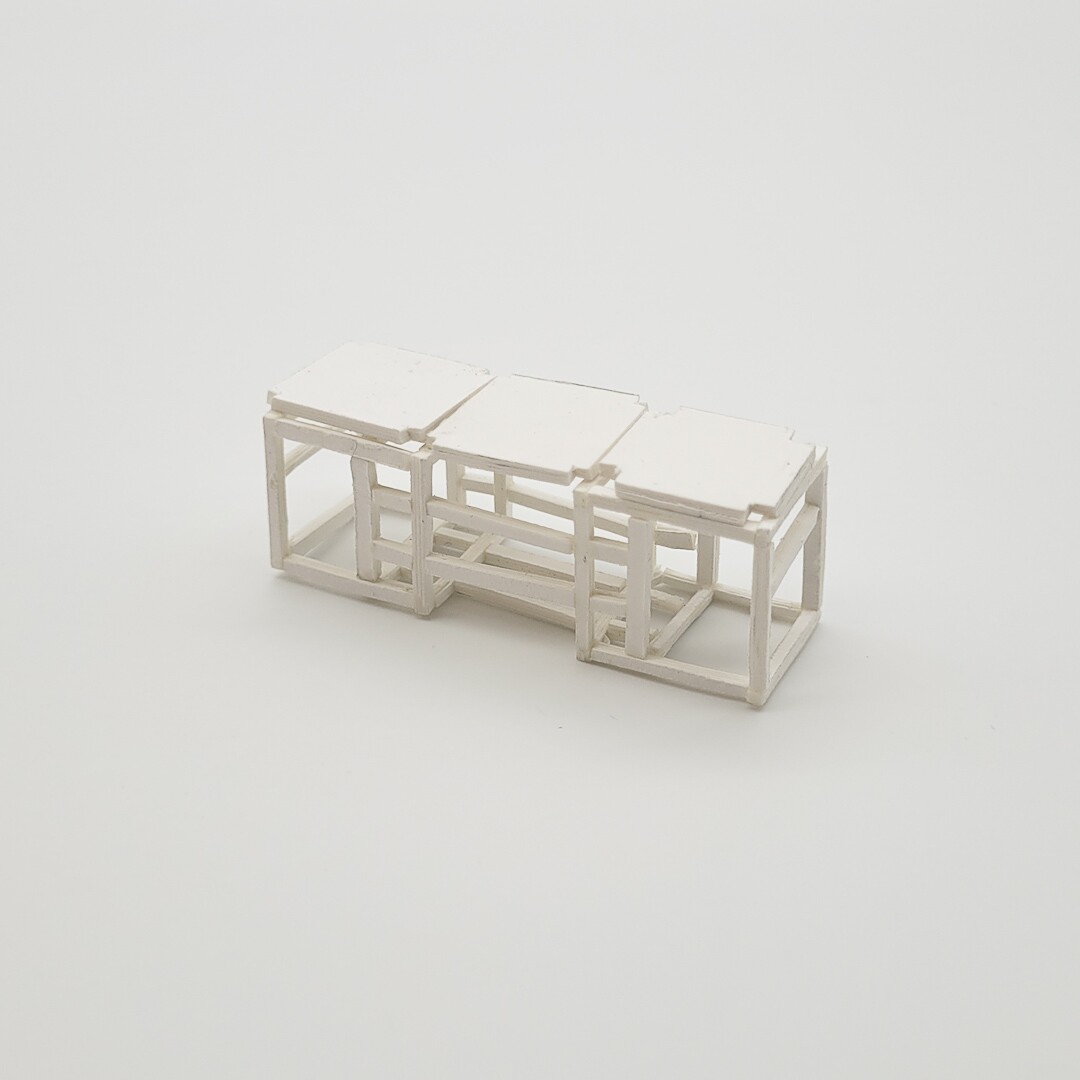
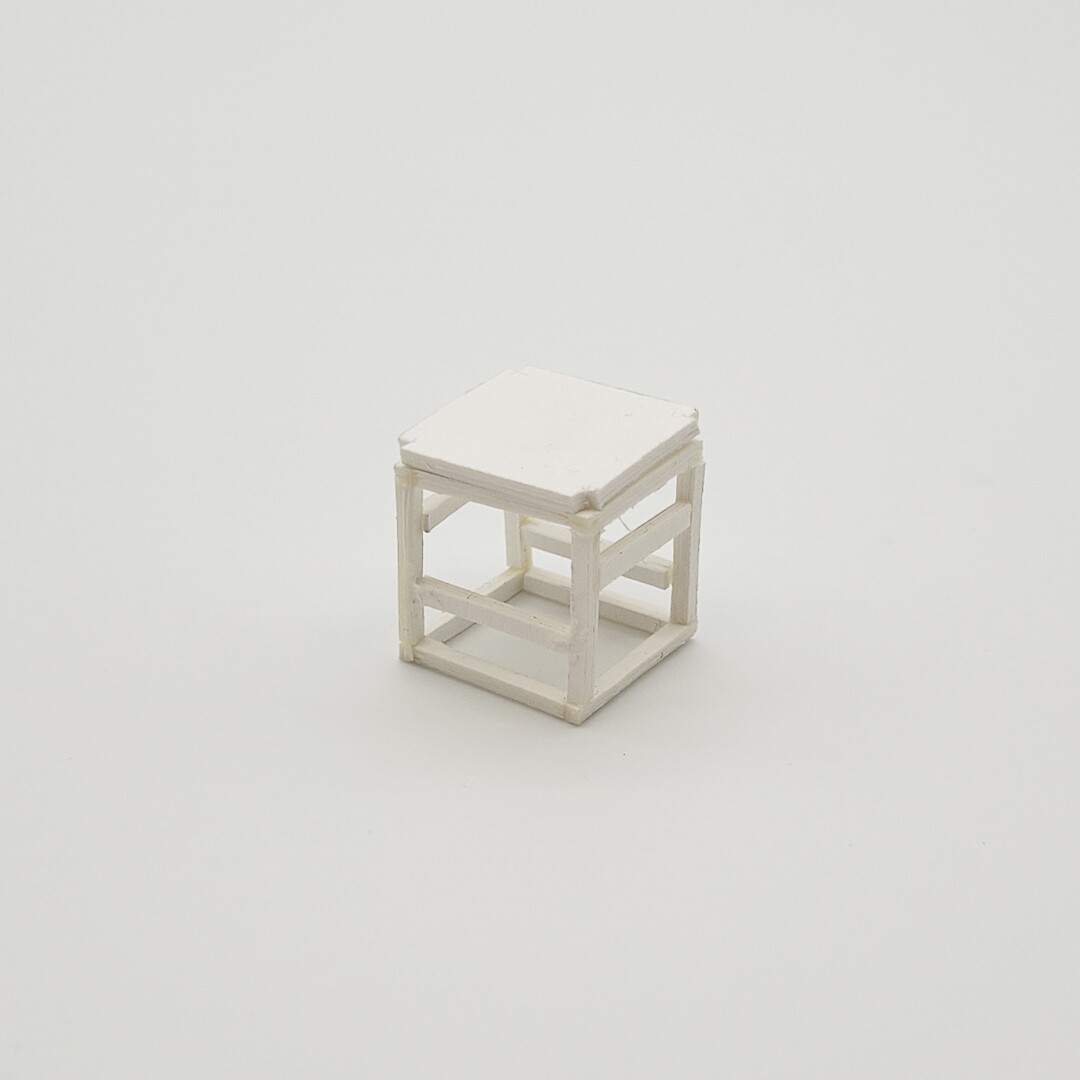
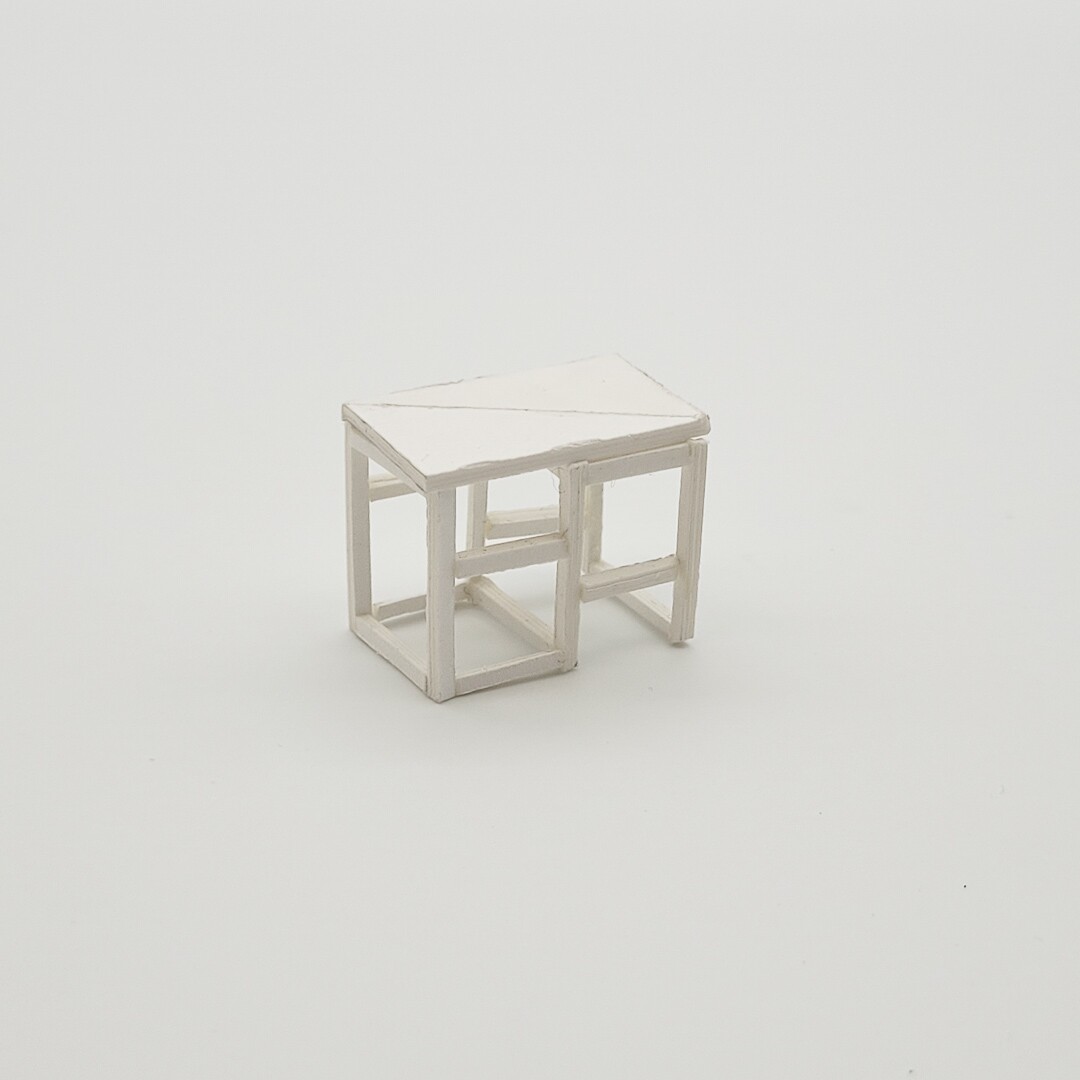
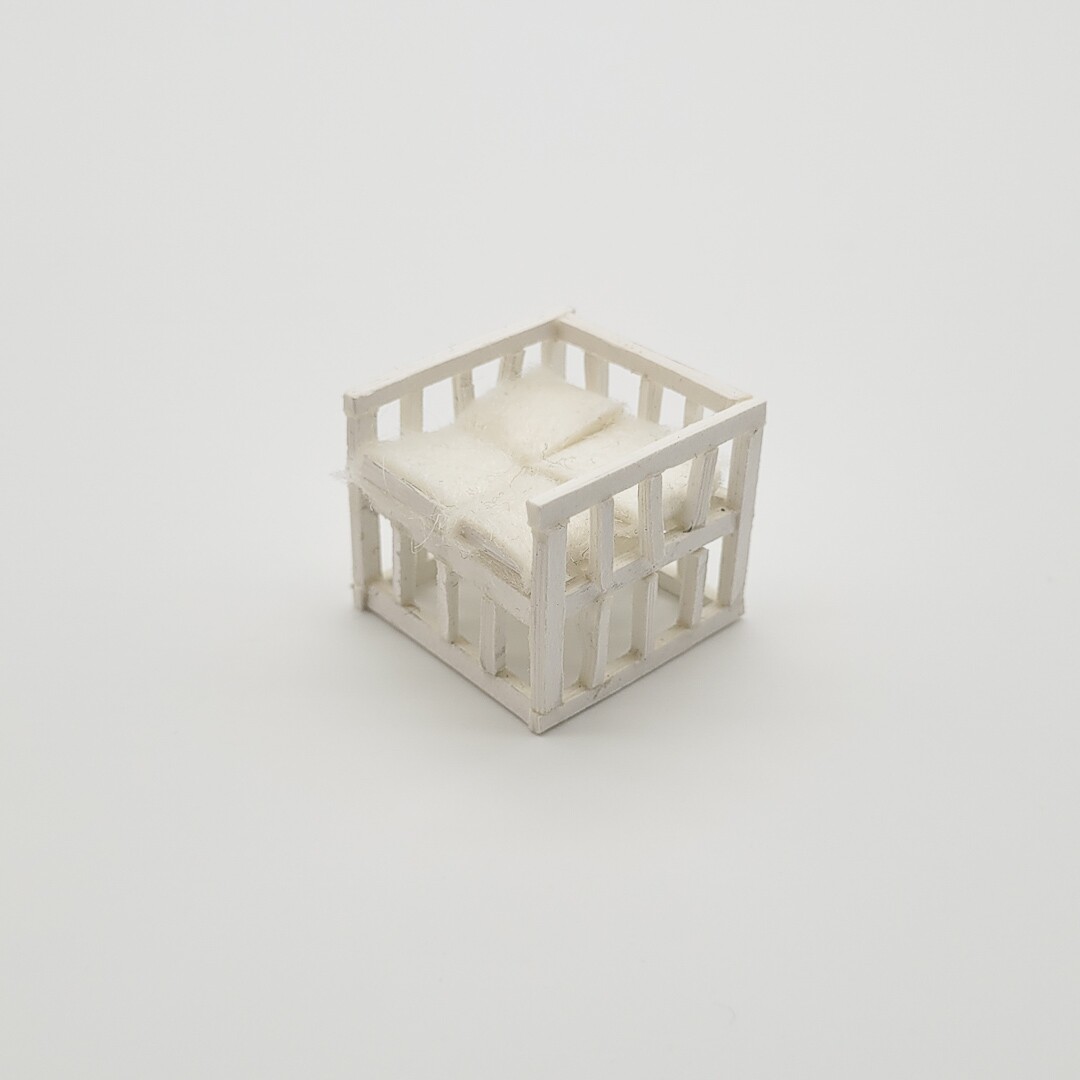
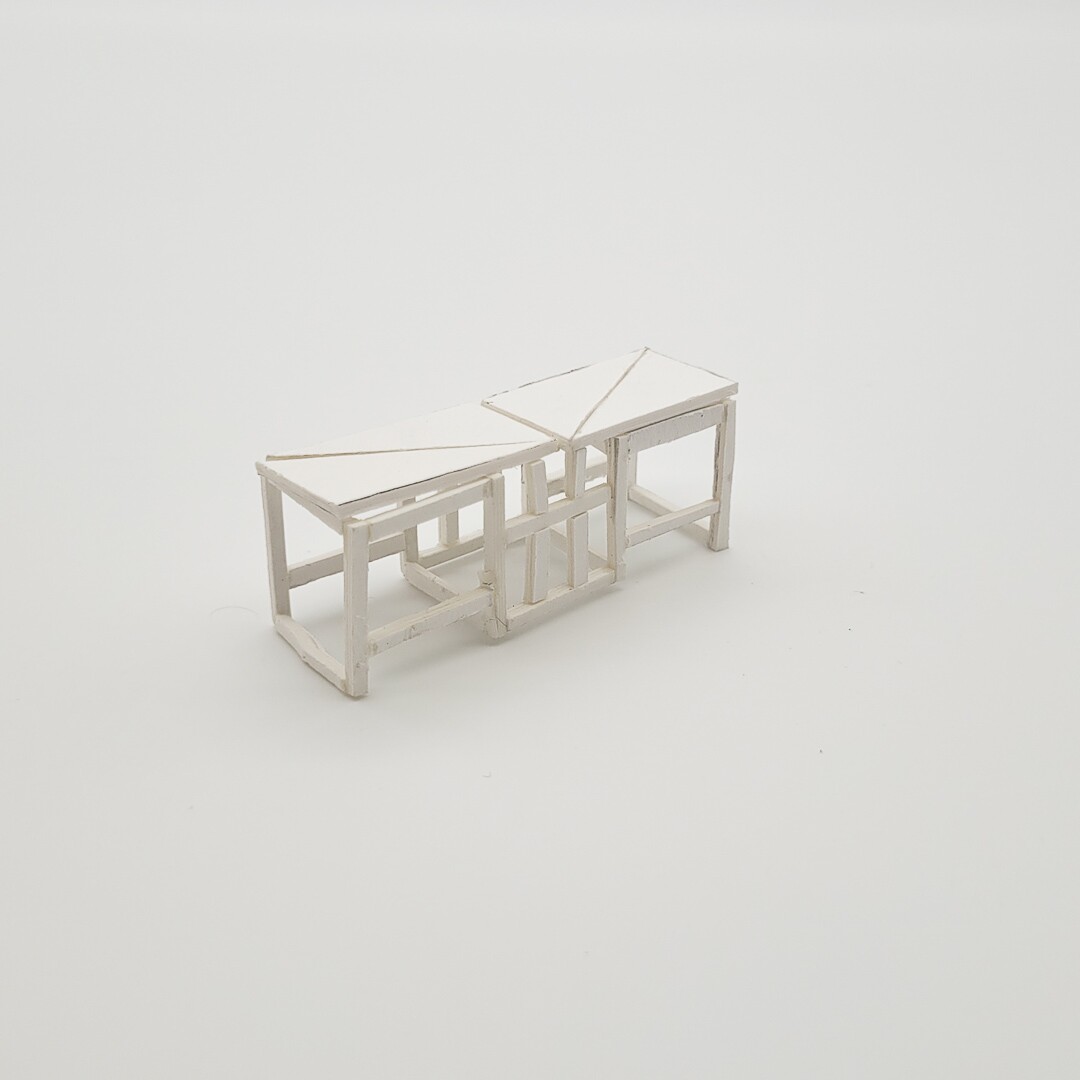
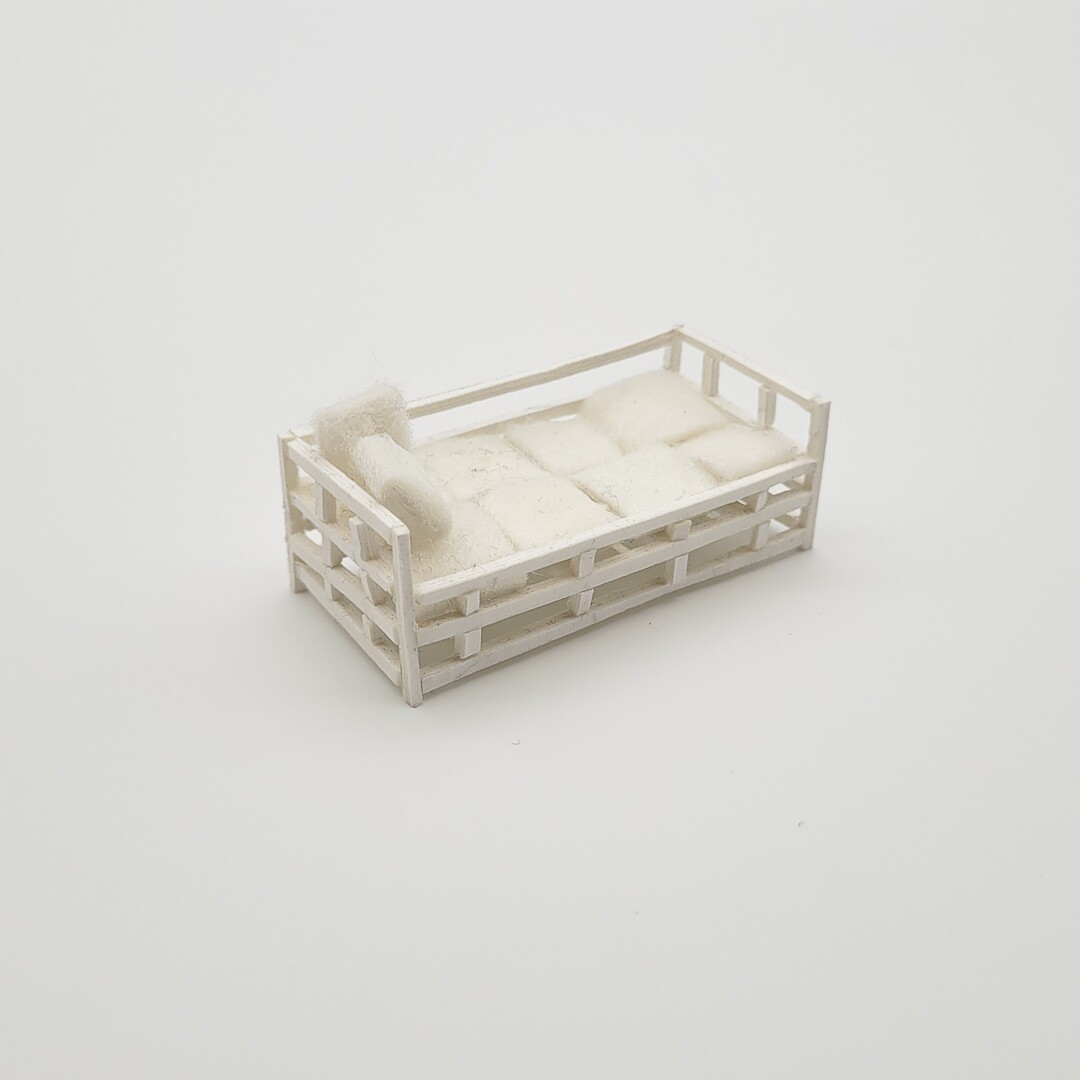
1to1 prototype/ergonomics
For the design of a piece of furniture with a participatory approach to assembly, there are some ergonomic values to consider besides the seat height, e.g., the gripping spaces and the edges of the individual modules during assembly, even if these are no longer considered after the furniture is assembled. The table shows some reference values from the "Kleine ergonomische Datensammlung", which I commonly use as a reference. Important for my product were primarily the dimensions of the seat surface and the seat height. I calculated with the 95th percentile values for the dimensions due to my own height.
.png)
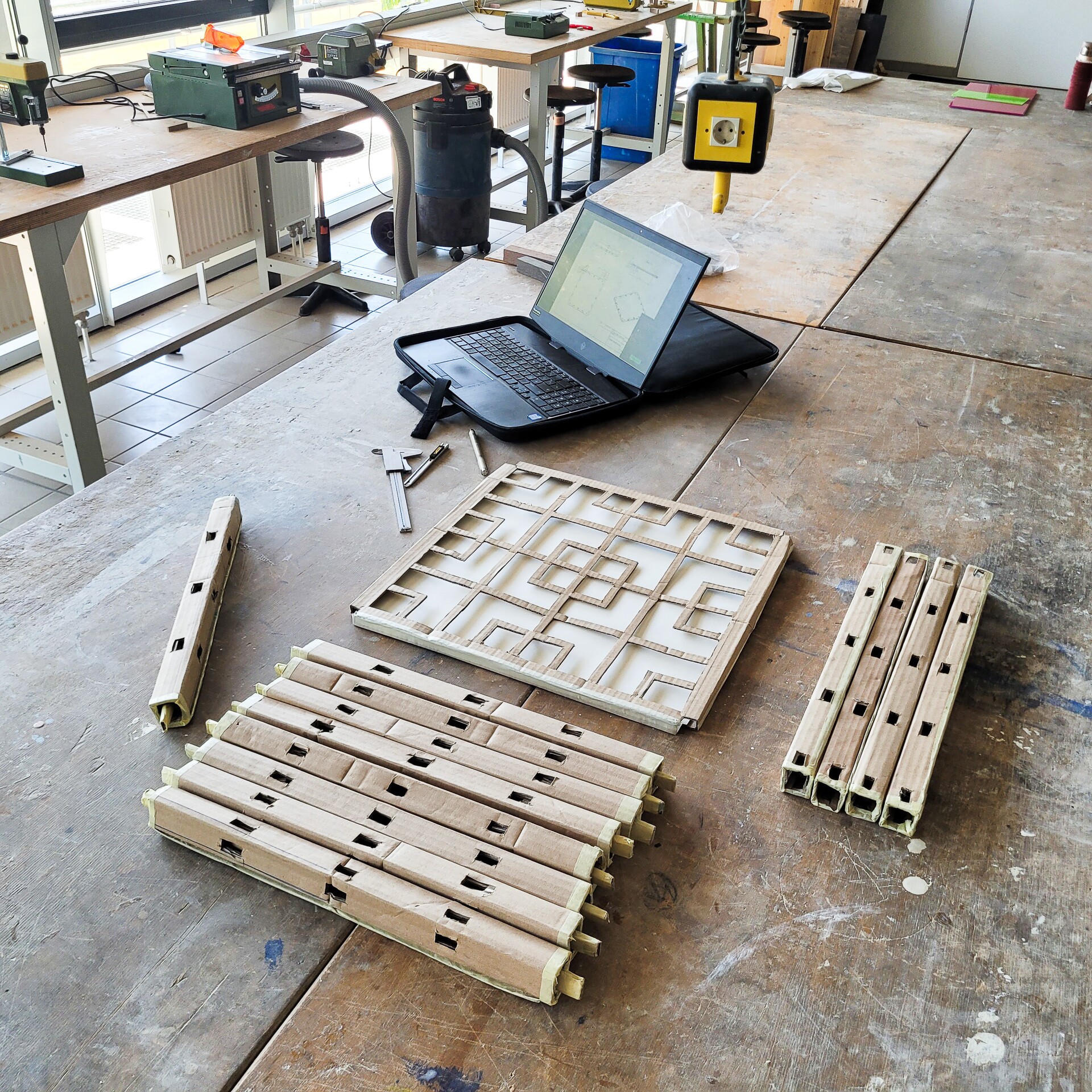

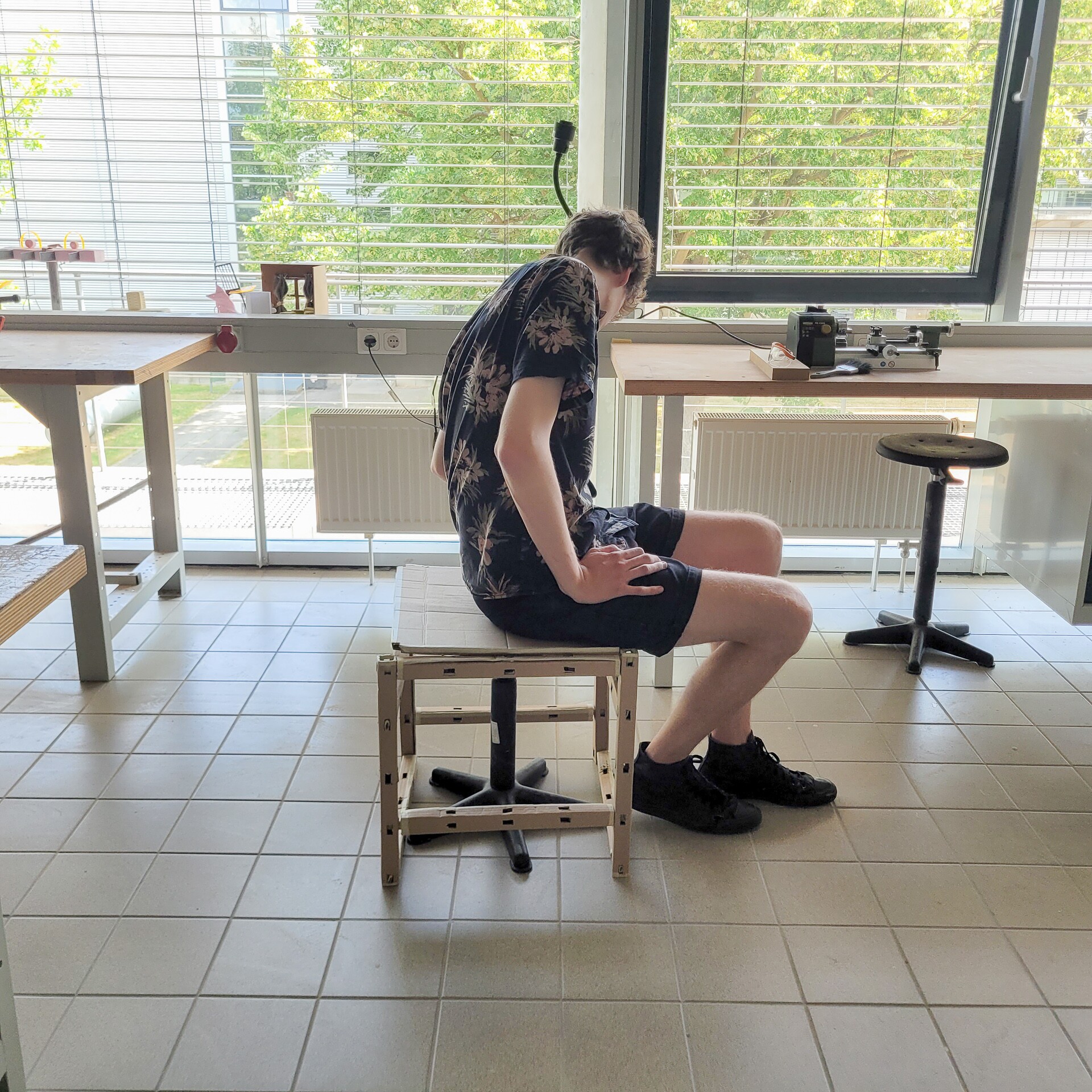
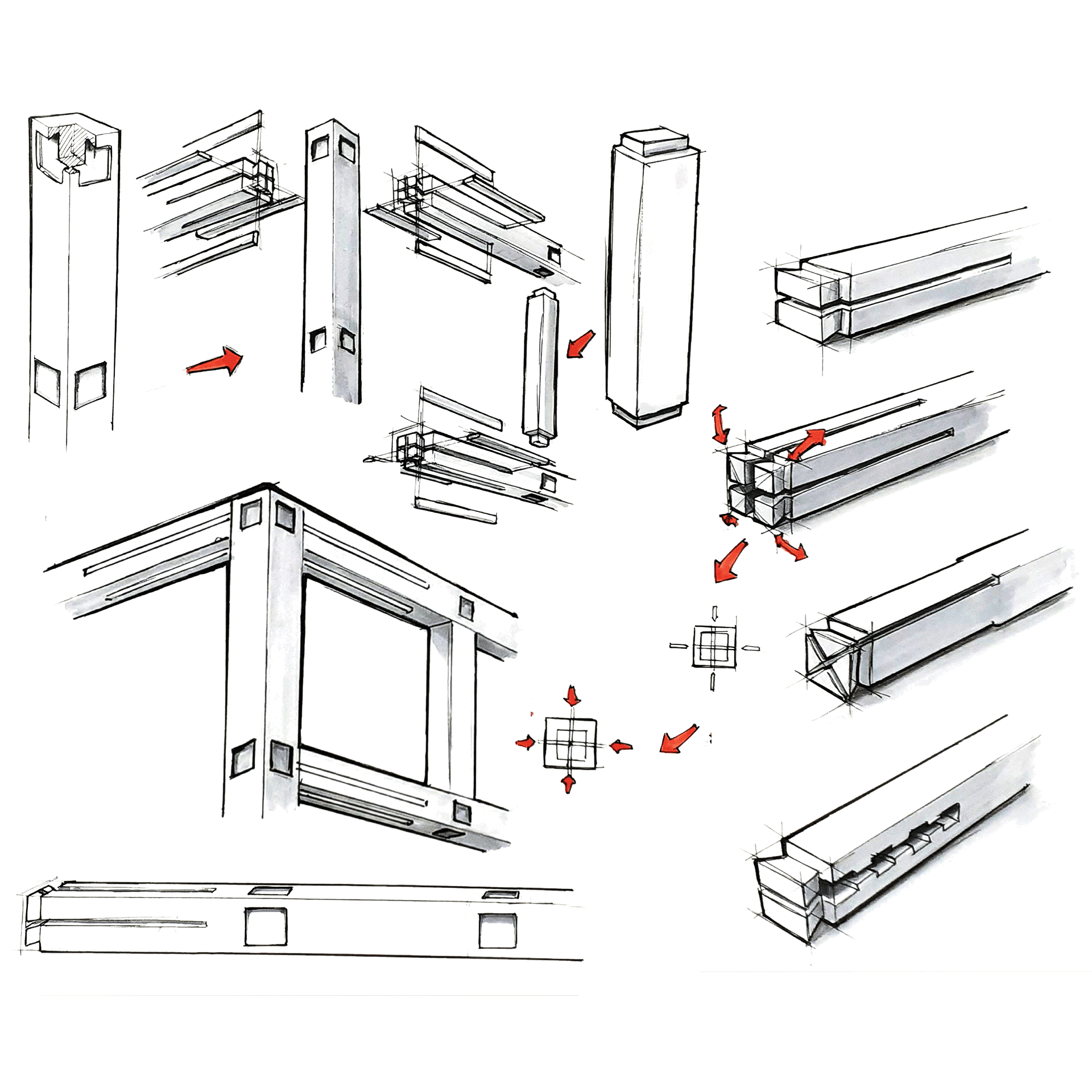
The Frame
The following sketches show the two concepts I considered most appropriate for keeping the frame together. Both are rooted in the "kumiko" concept, so they work just by sticking them together. To me, the connection provided by the flexibility of the wood seemed more interesting, and at the same time, I wouldn't have to use extra materials except for some small wooden plates to stabilize the connection.
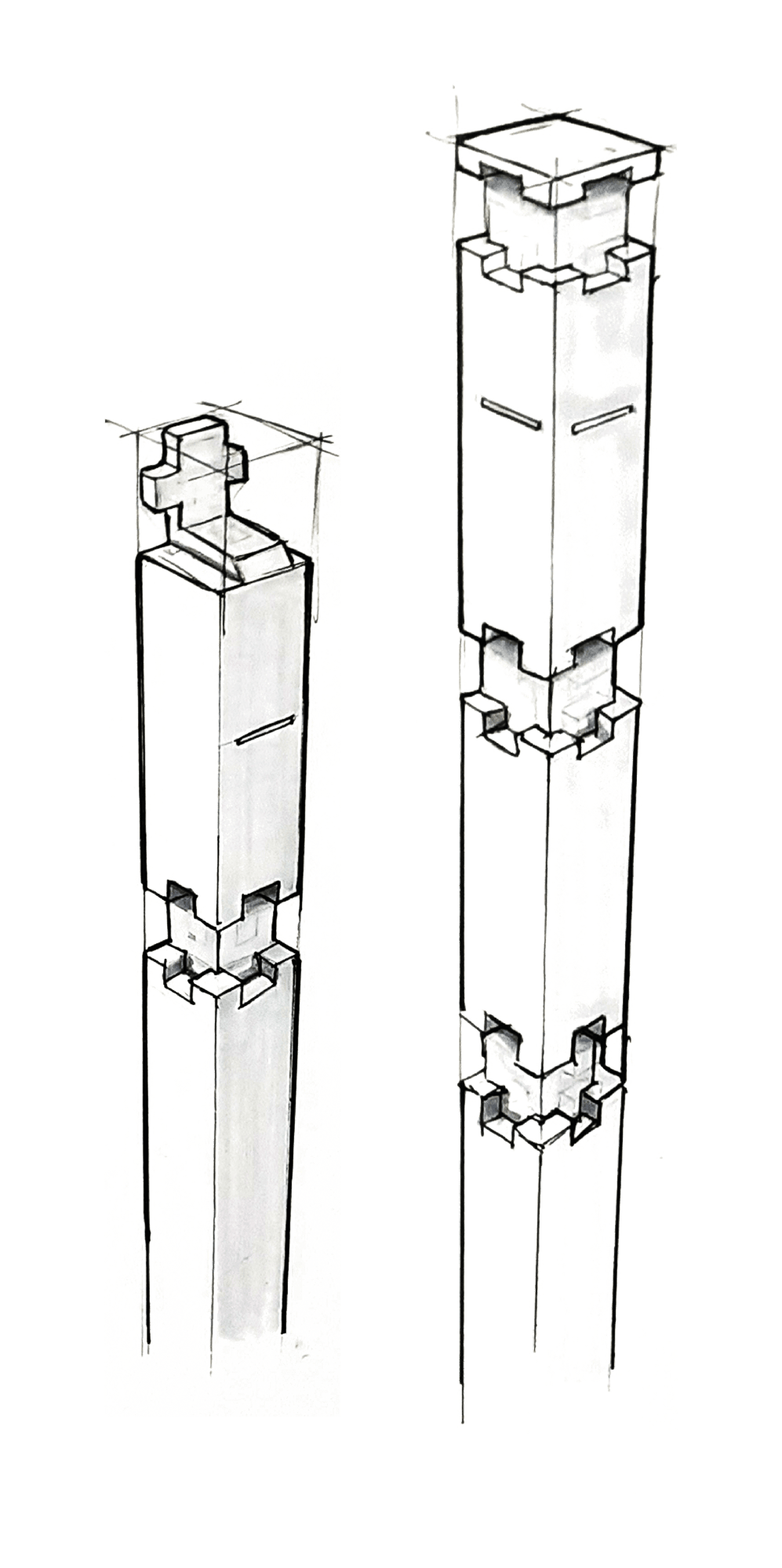
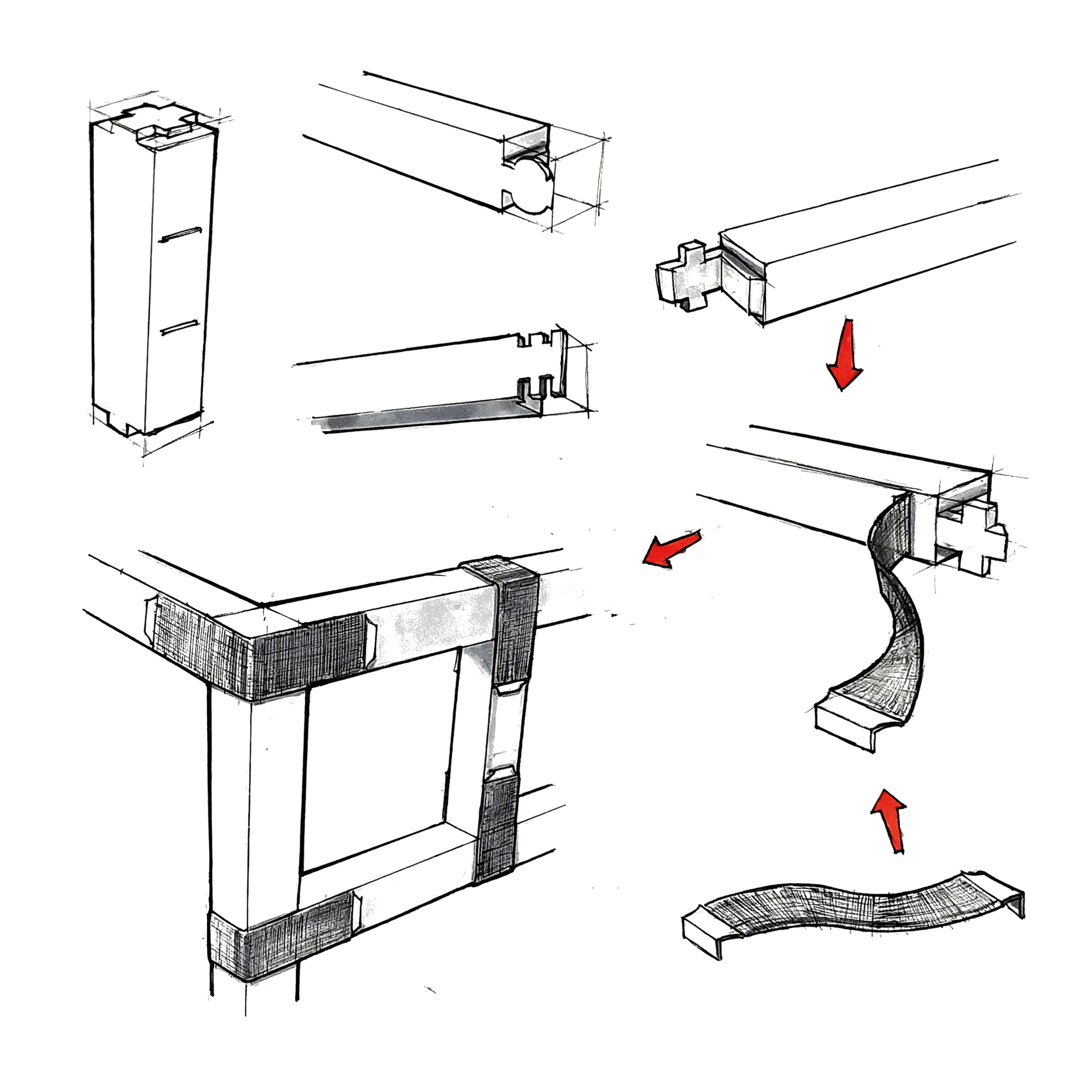
Choosing the wood
To choose the best of the joints I designed, I made my prototypes from different woods. I tested the woods that are listed in the following picture on the properties documented in the chart with the wood types.
.png)
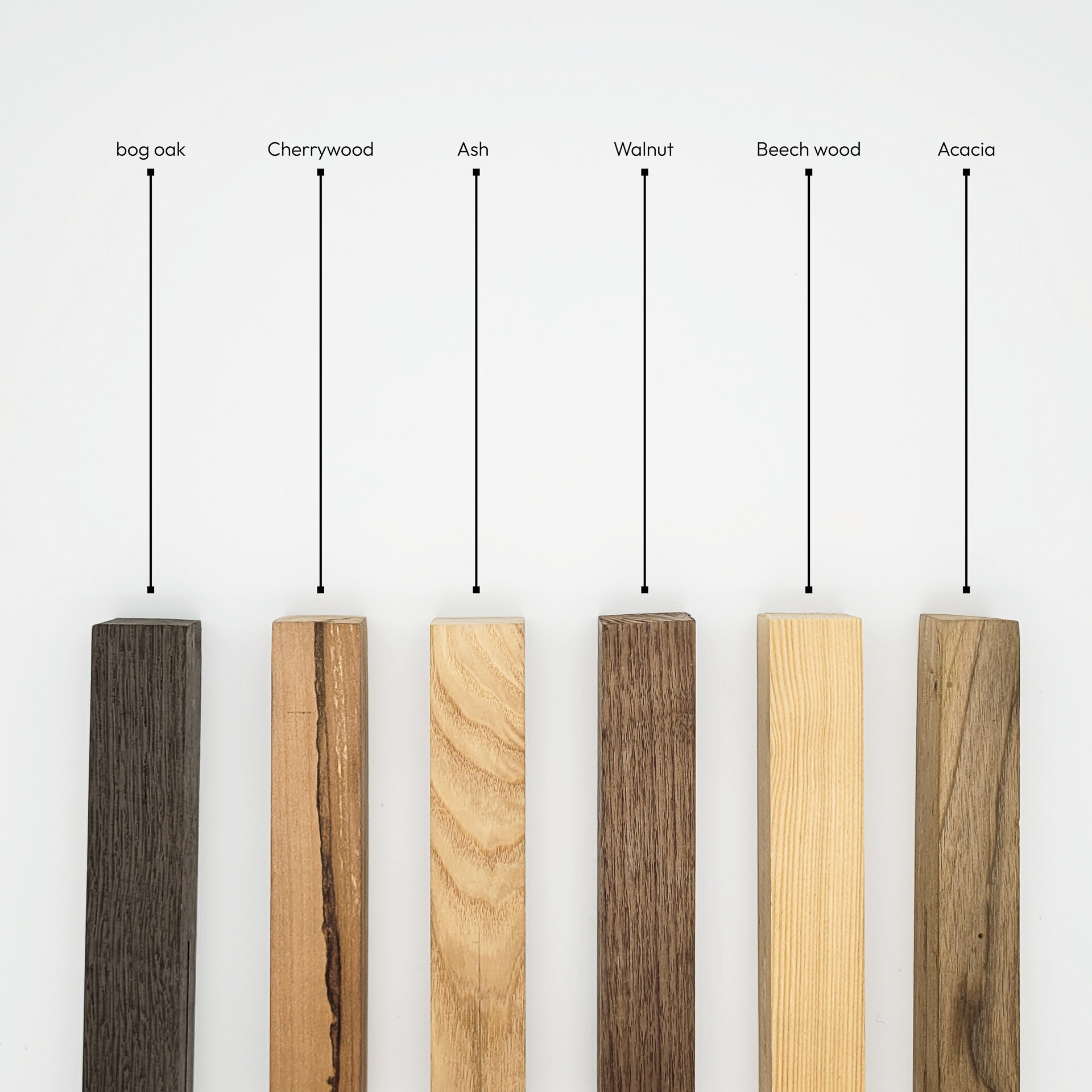
The connector shape
The project was executed during the Corona lockdowns. For this reason, I created the prototypes at home and 3D-printed the square-drilled and mortised joints for myself. Even though this makes the results less reliable, it was my only way to build a halfway-suitable prototype at the time. After testing, walnut and cherry woods turned out to be the most suitable. I chose to use walnut wood because it is available from many online retailers. For the connection, I chose the third one documented below (marked in red) for the 3D model and later switched to the last one of the prototypes (marked in yellow) for the model I built.
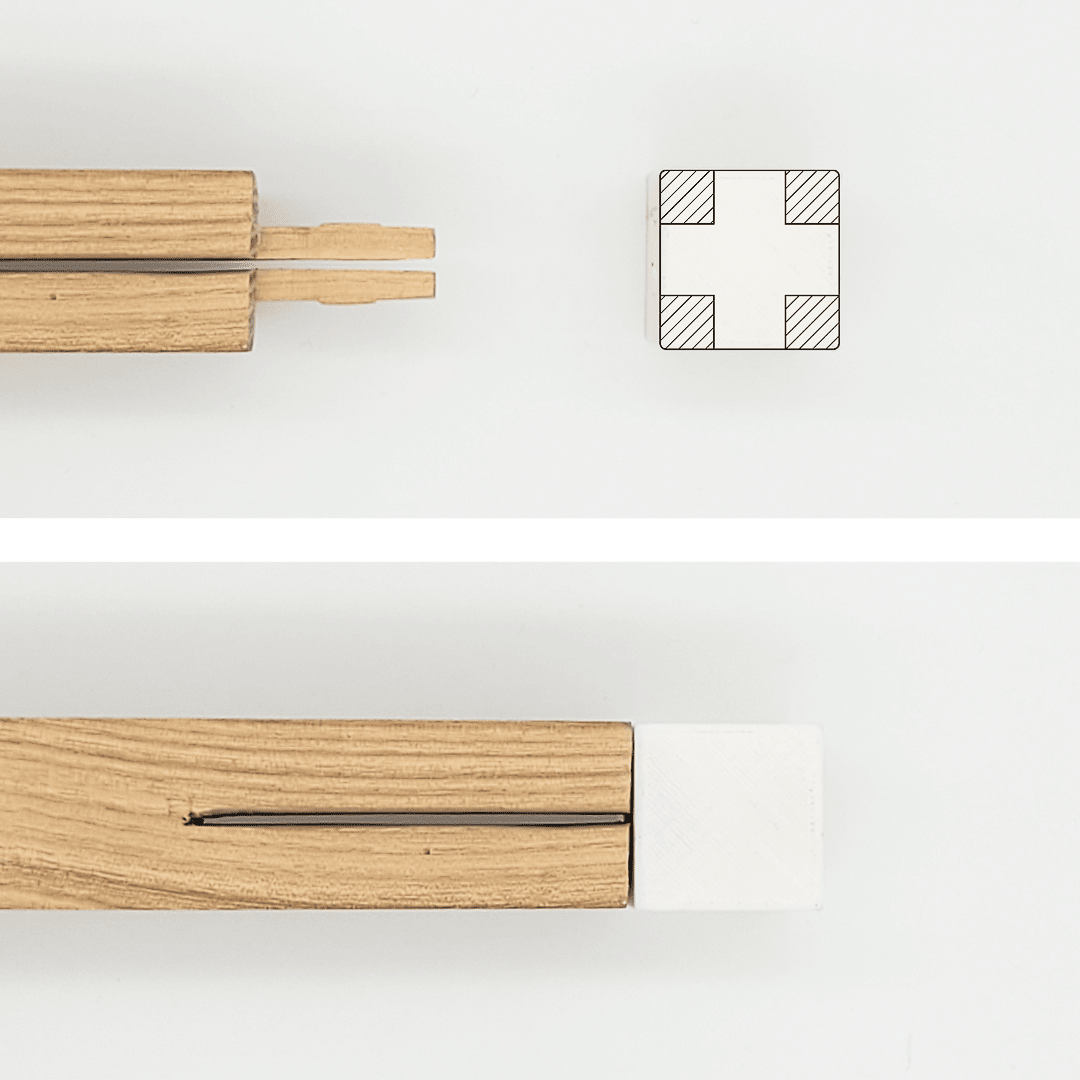
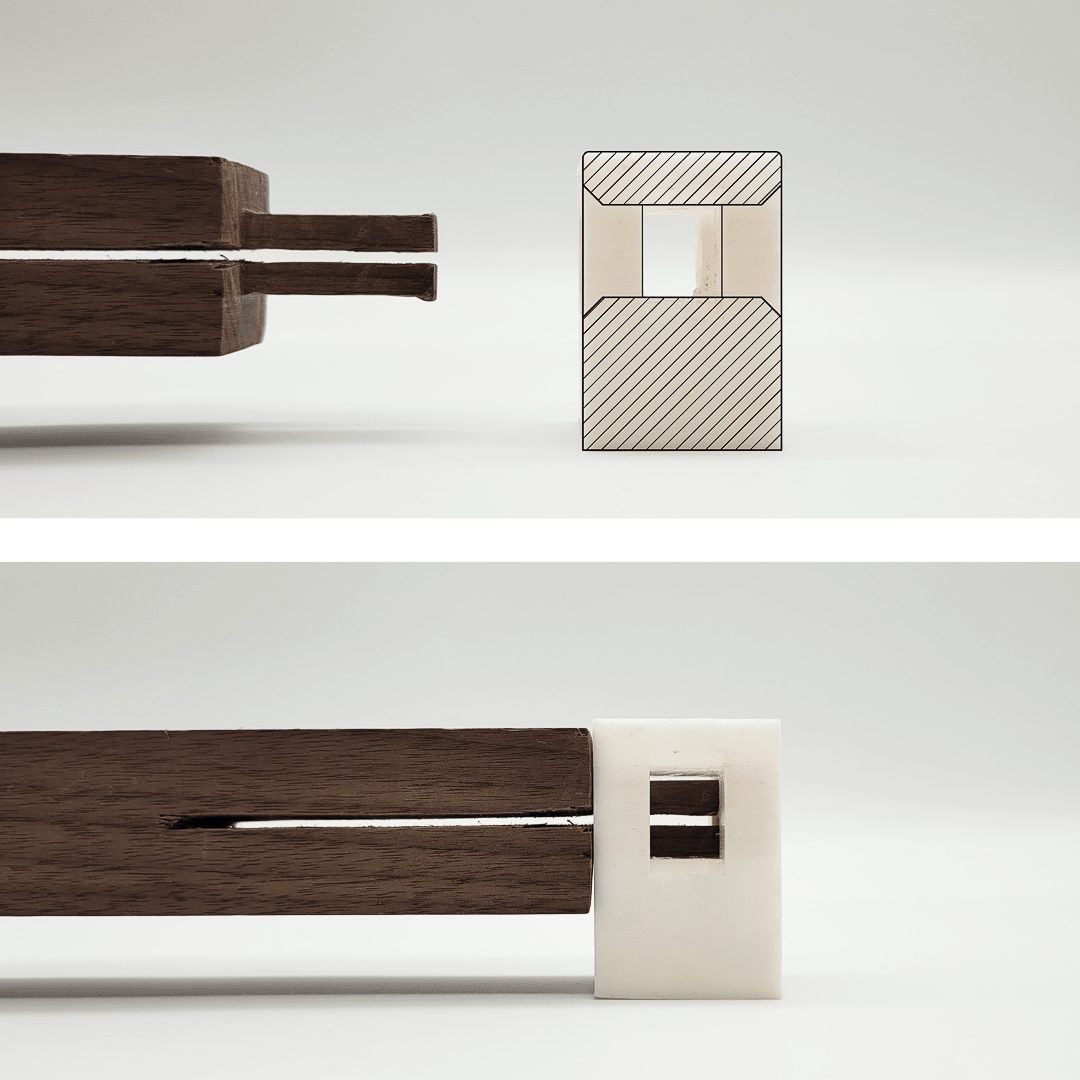
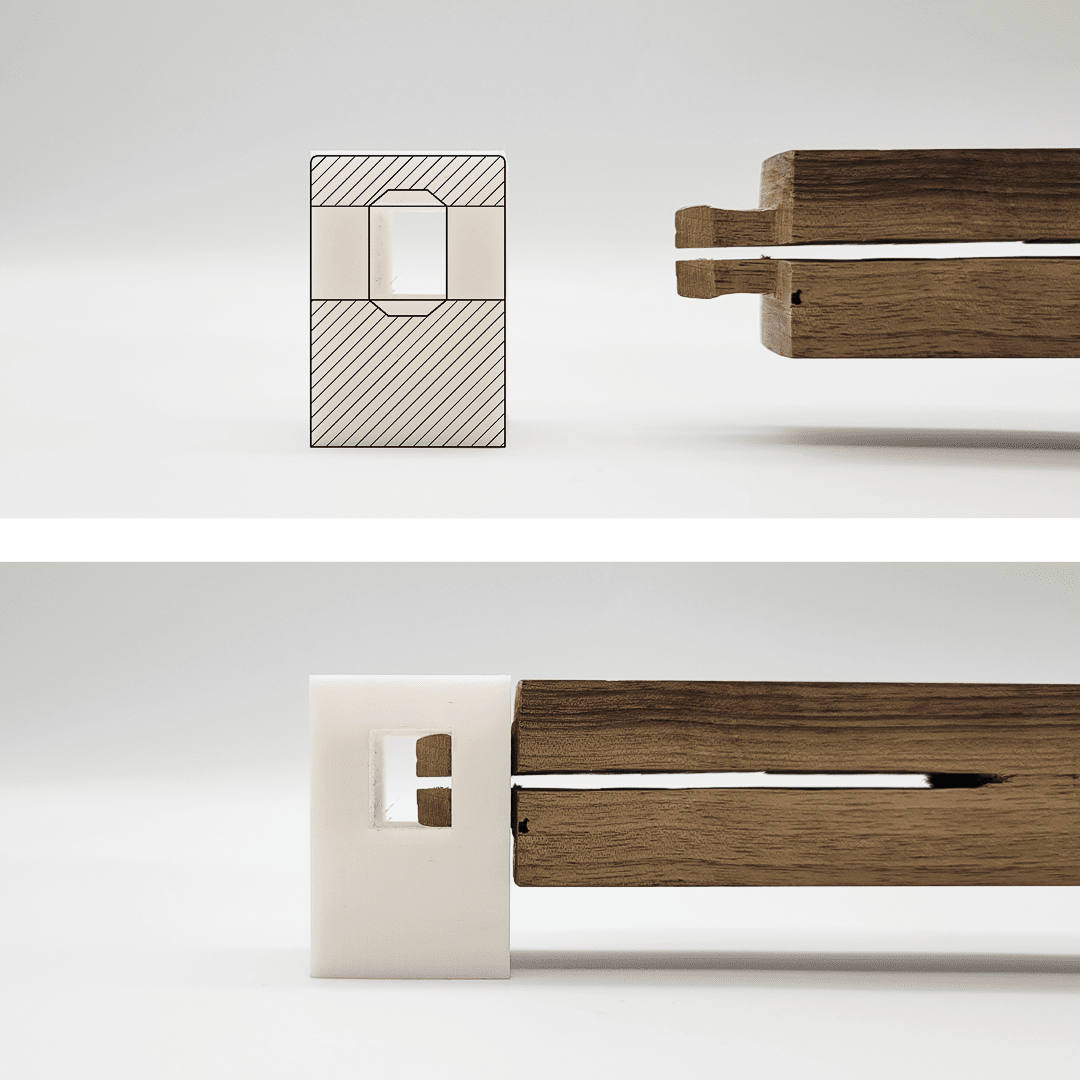
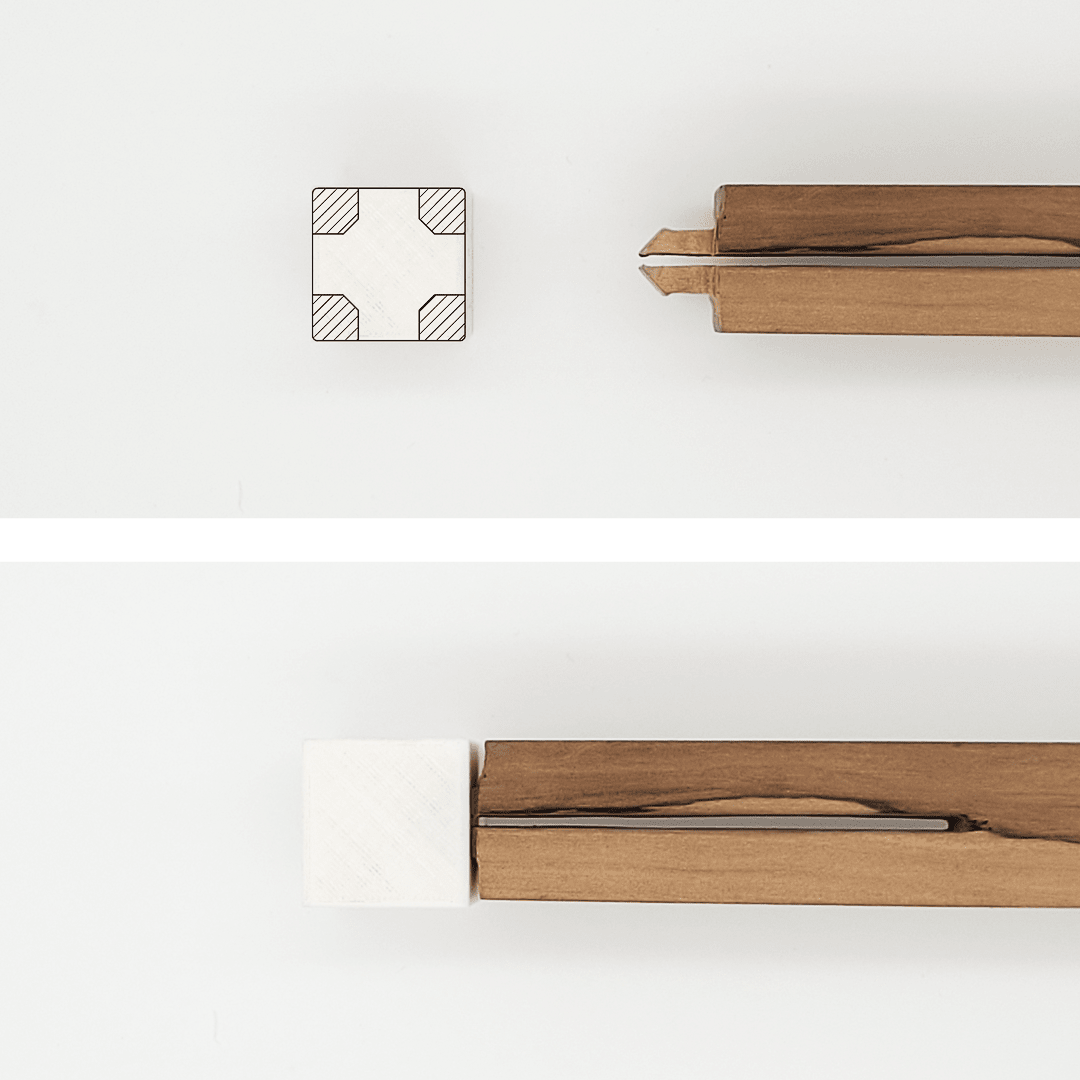
The seating panel
The sketches show the complete assembly of the plate and the plug-in connection for the plate and the frame, as I imagined them. As for the frame, most of the materials used for the seating panel are planned to be from wood as well.
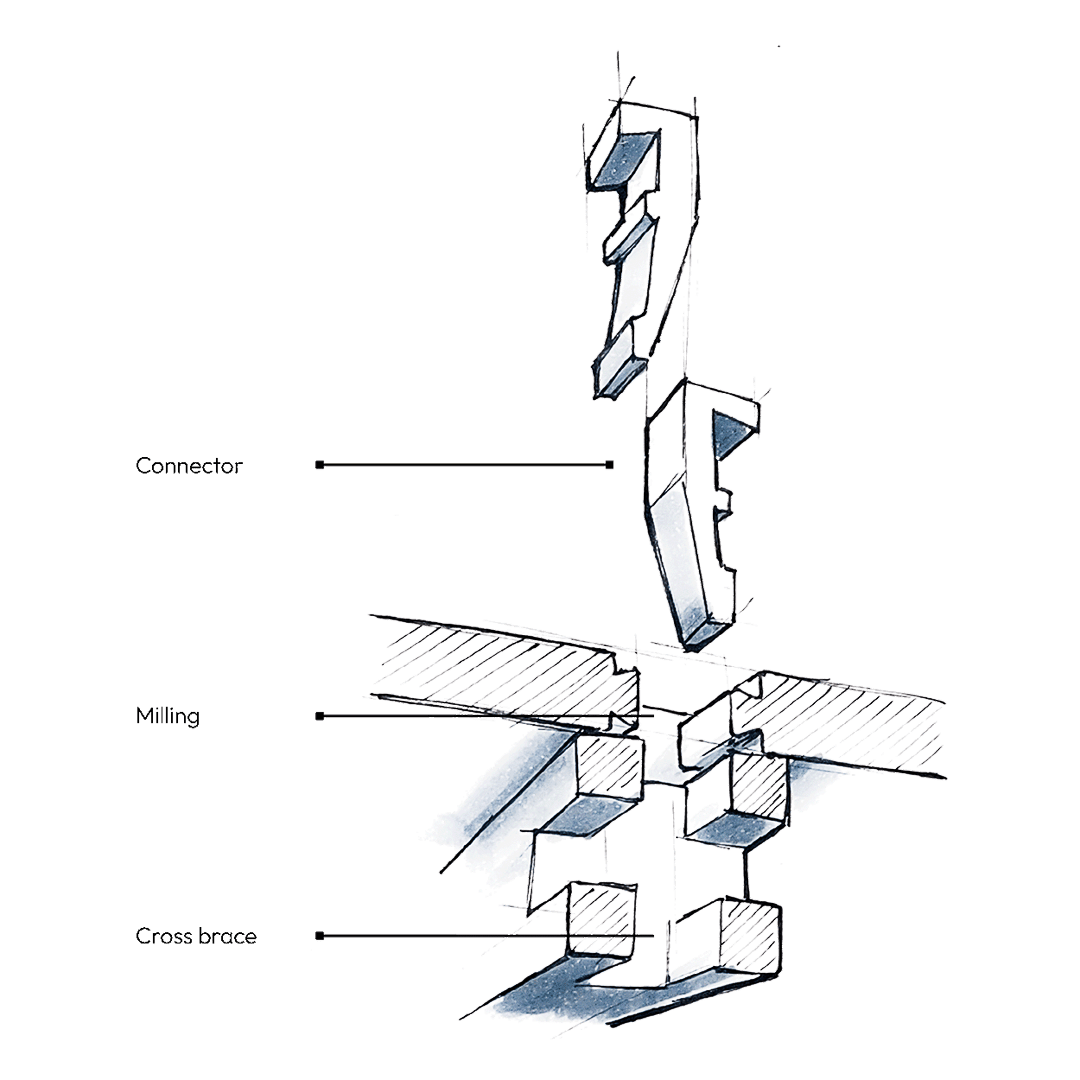
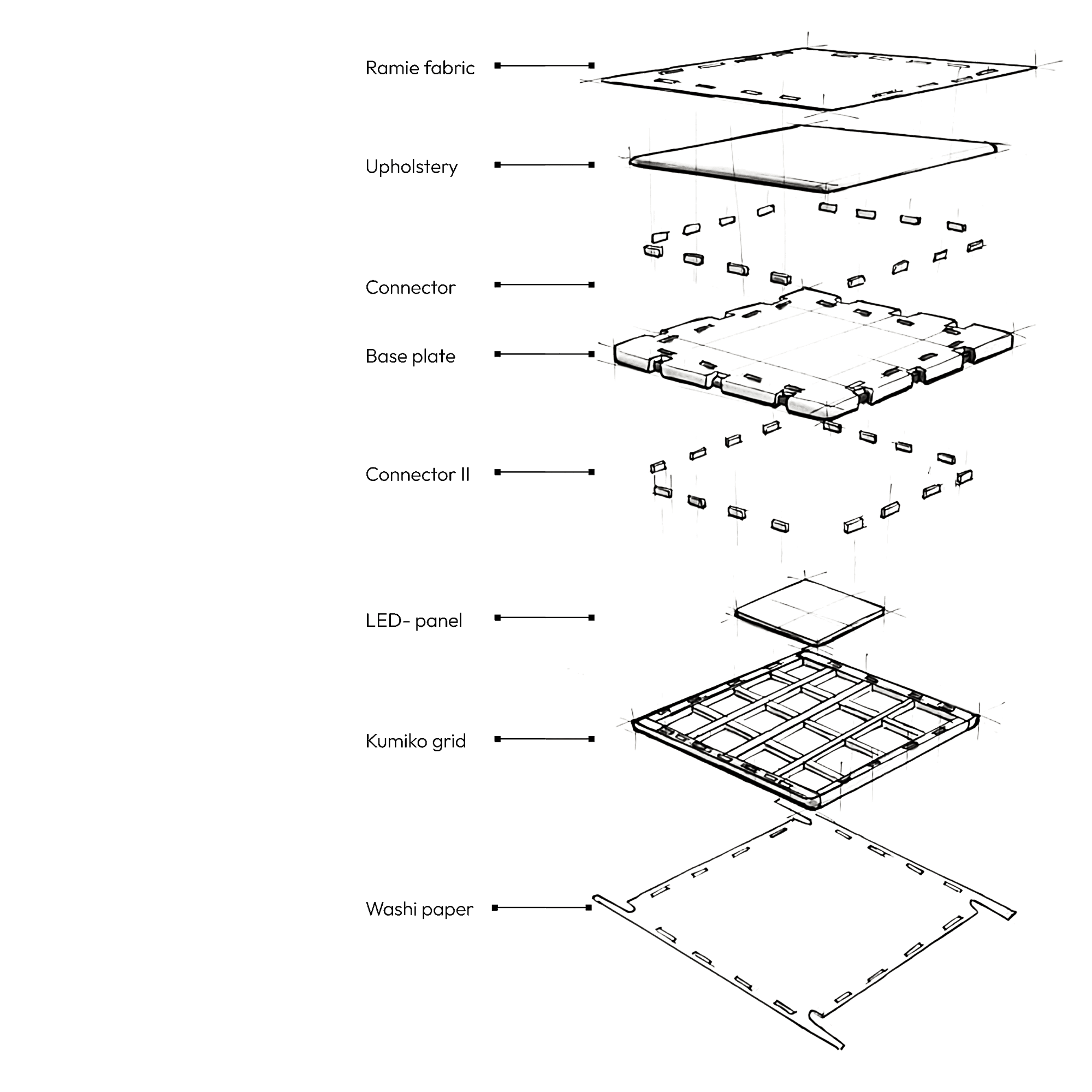
Connector prototypes
The prototypes for the connectors were 3D printed, for the same reason I printed the prototypes for the square milled holes of the frame. These connections are also to be considered more conventional, which made 3D printing seem like a good choice.
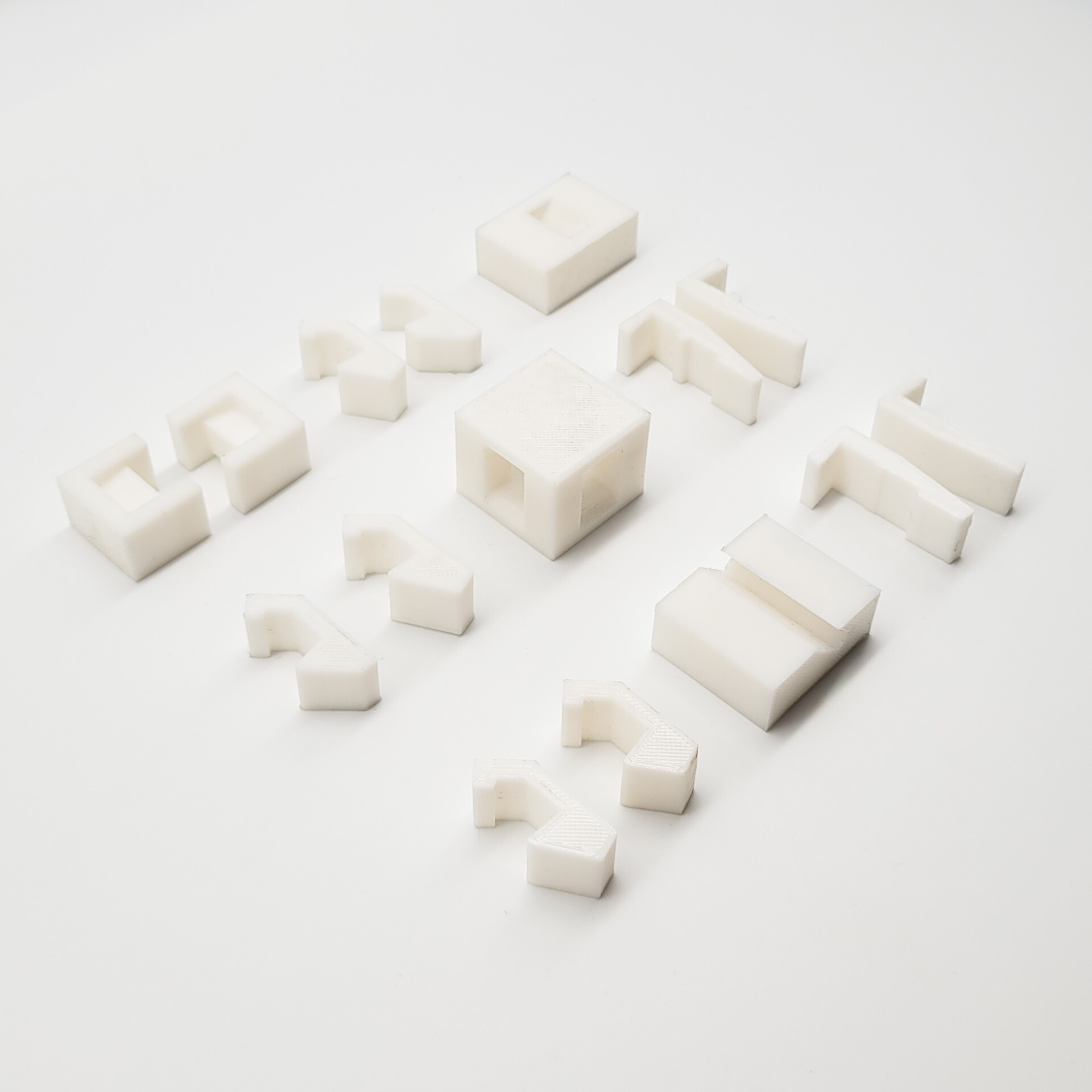
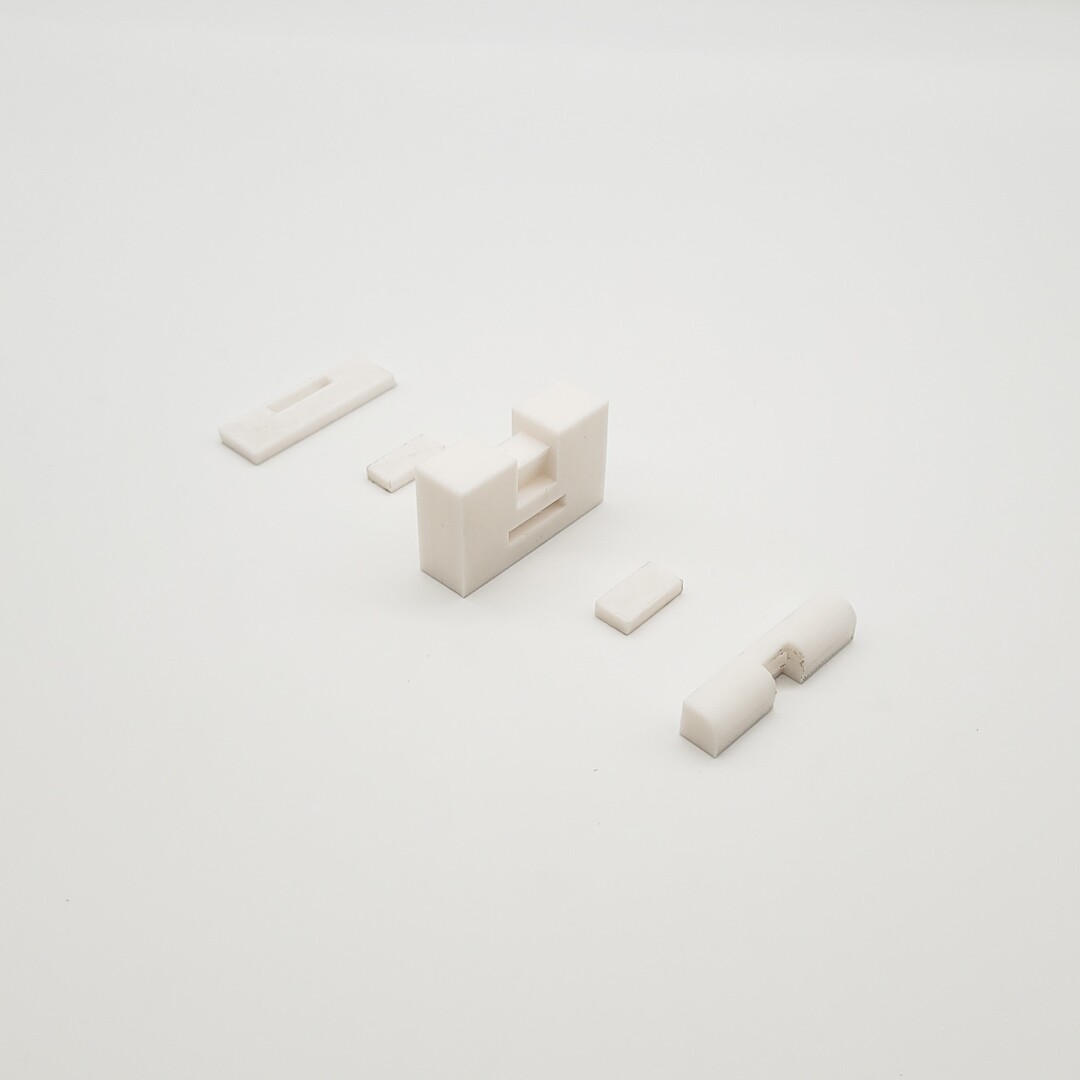
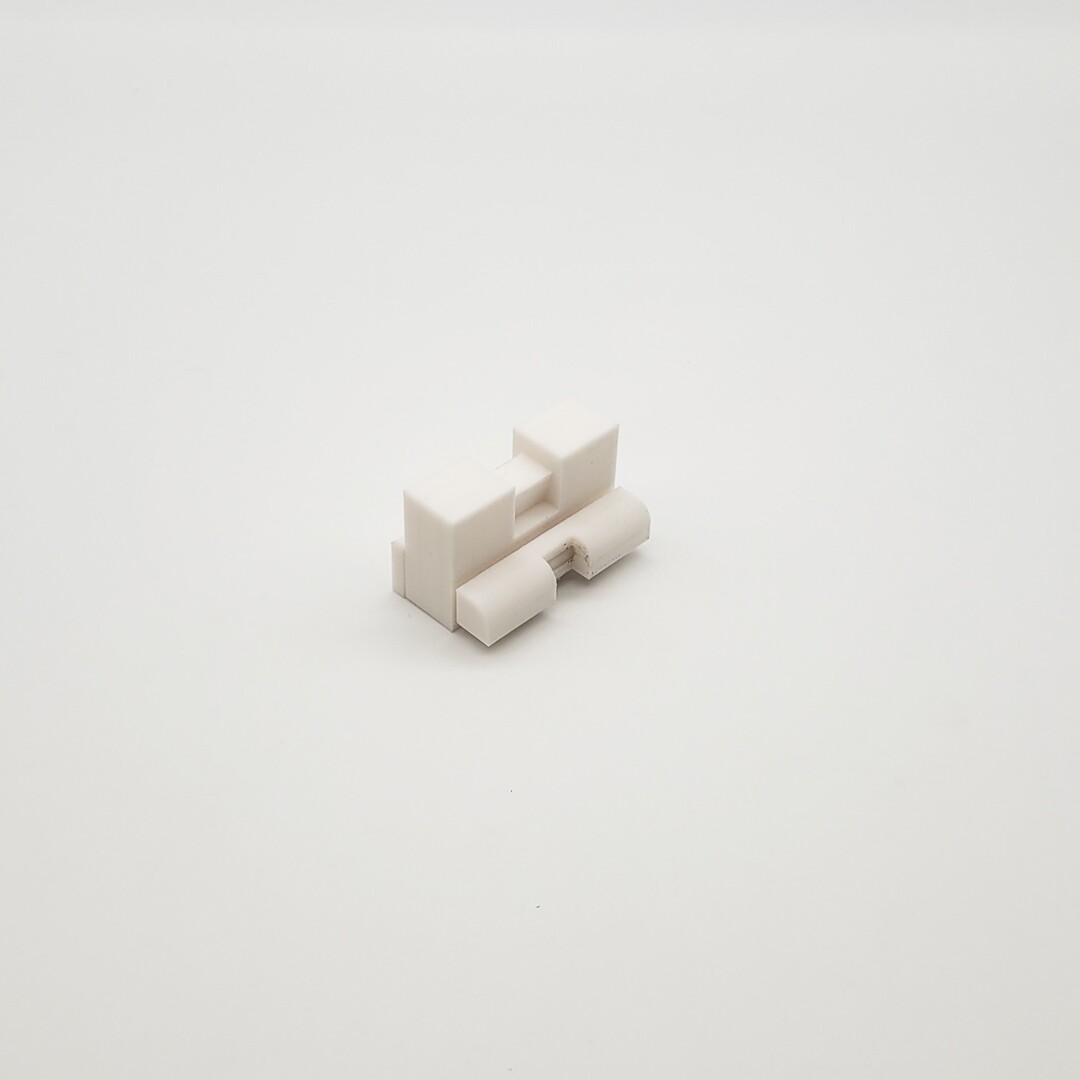
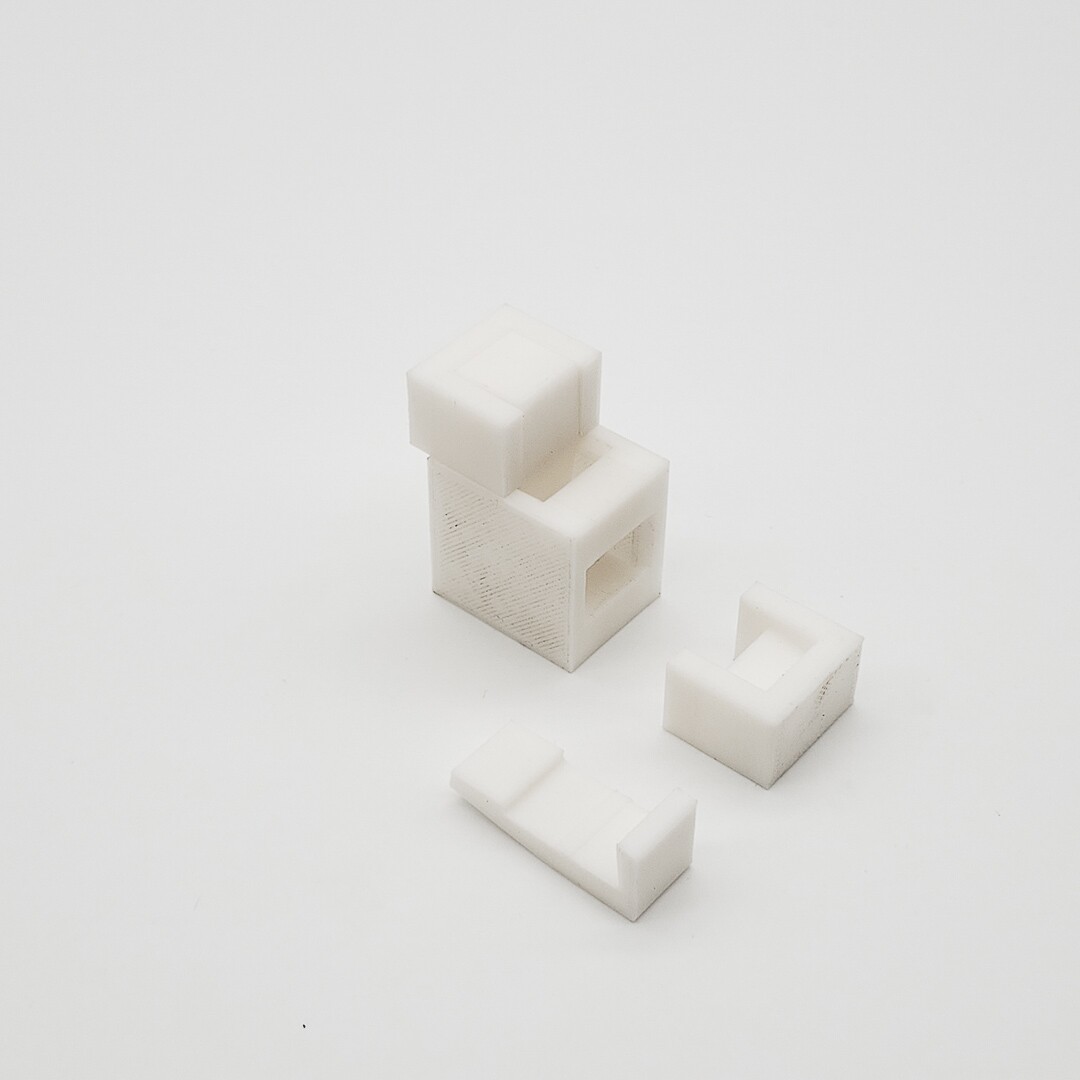
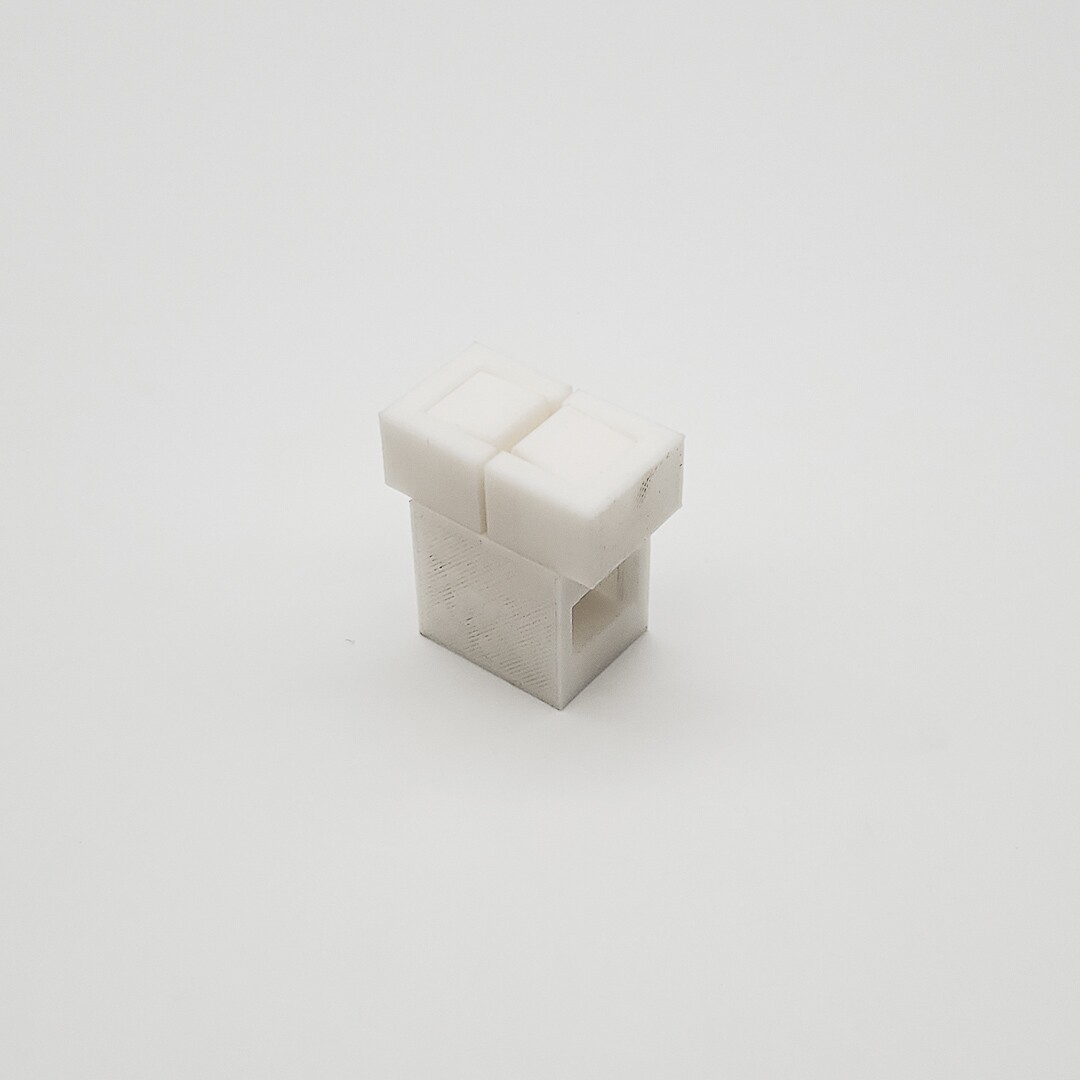
The final design
The sketches show the final shape of the most basic piece of furniture that I wanted to build with the modular system.
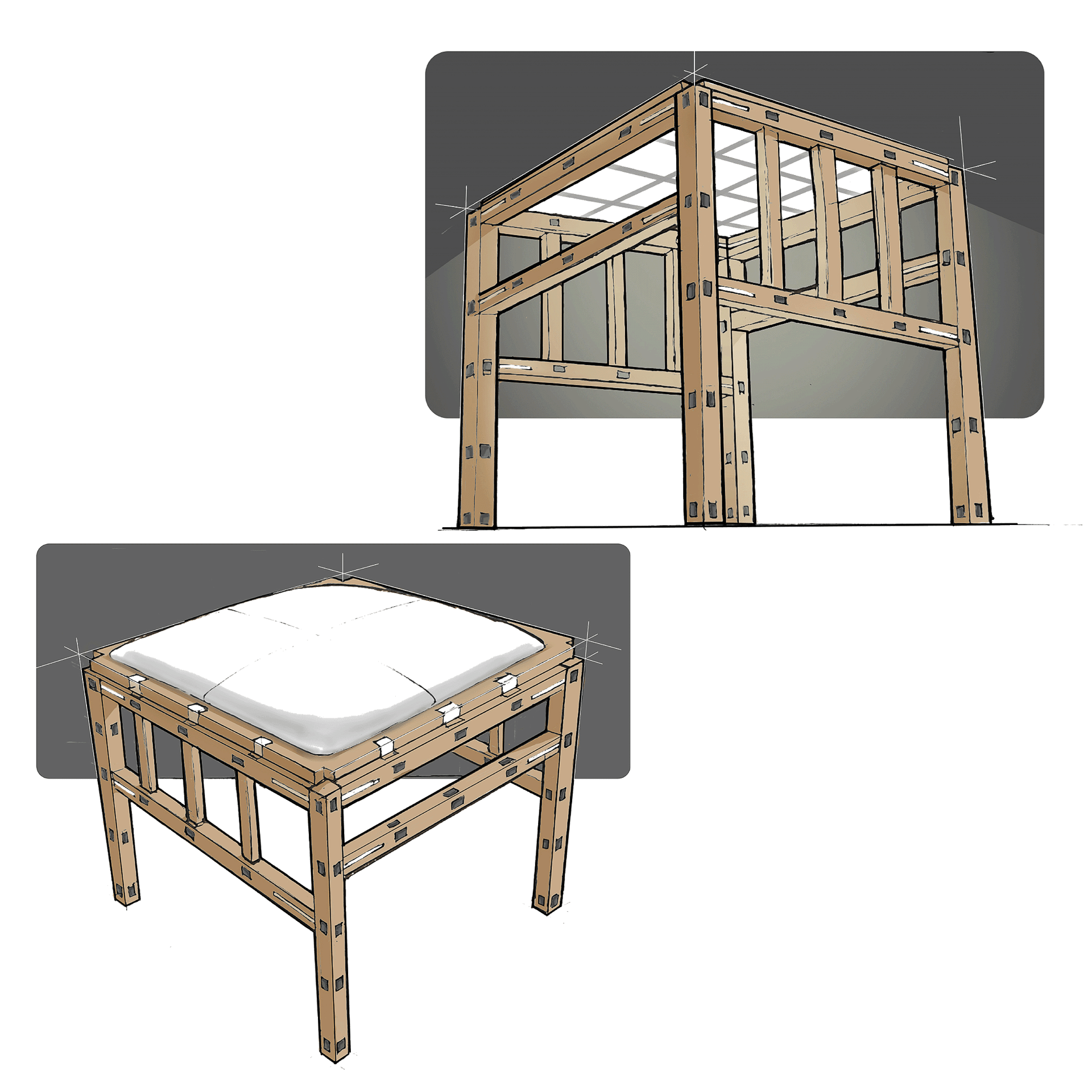
3D model
I used Fusion 360 for modeling the parts and Keyshot for rendering some of the pictures. The pictures below show all the necessary parts for the piece of furniture, including a USB cable for the light underneath the seating panel and some tools for the easy assembly of the design. The animation of the product also shows the packaging I designed for all these pieces.
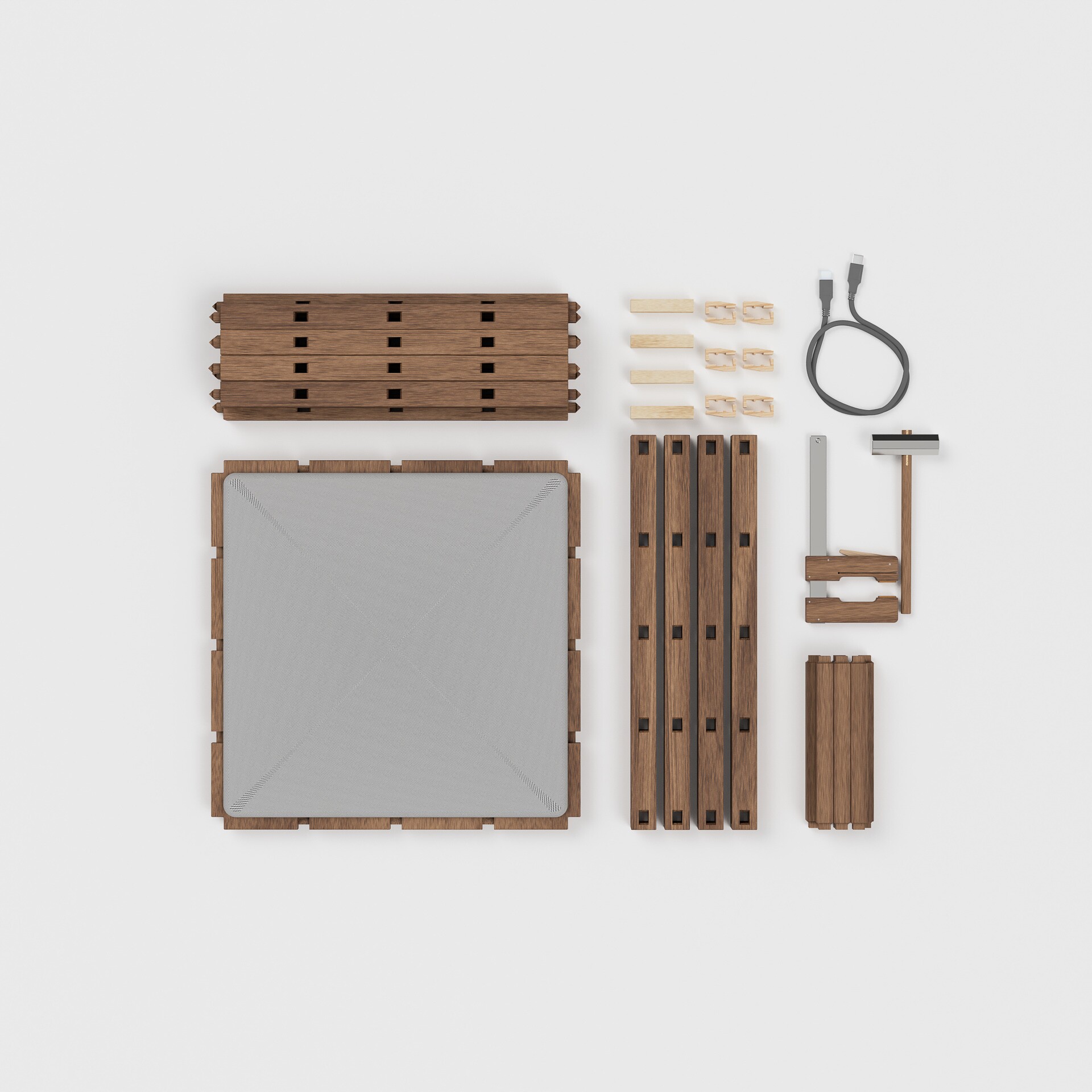
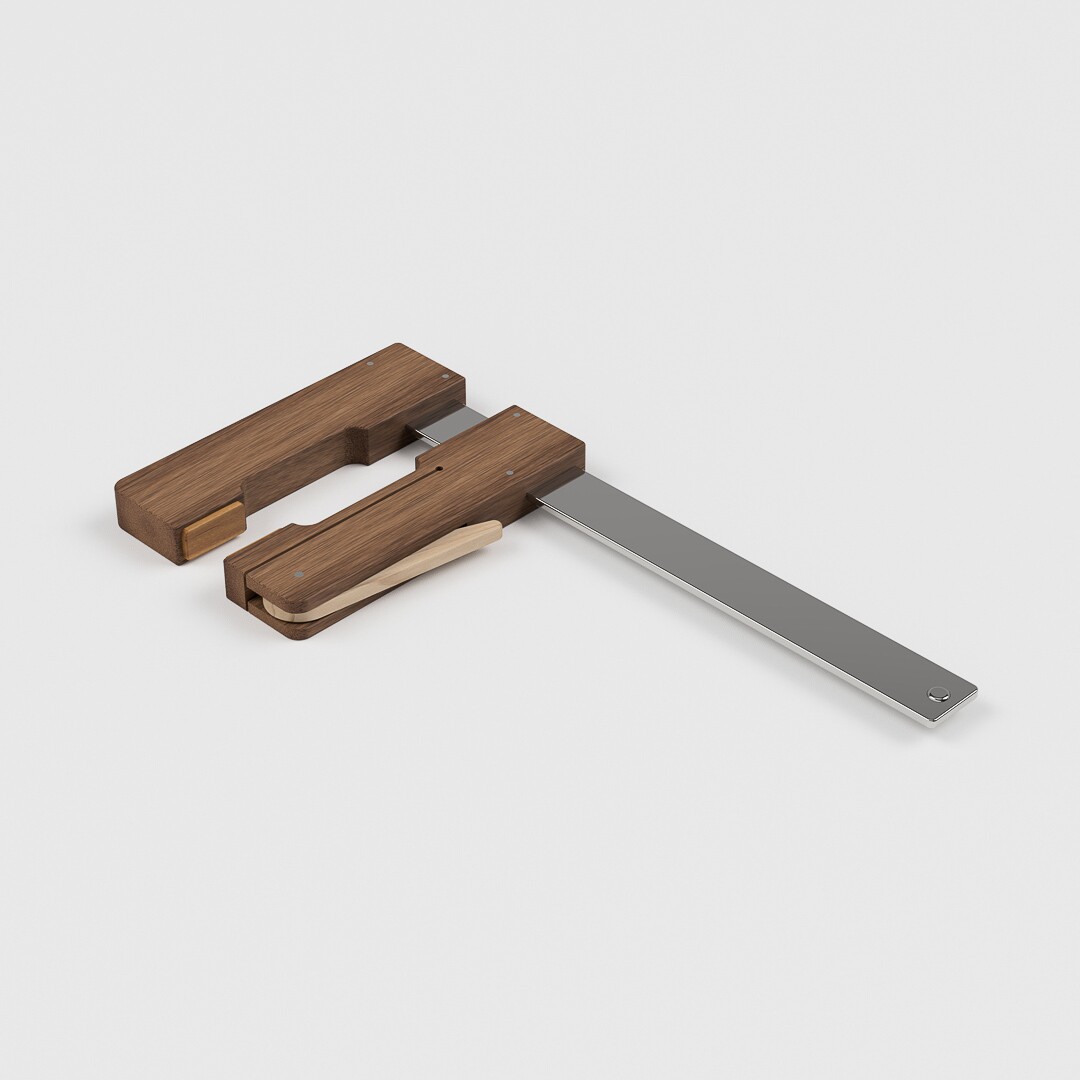
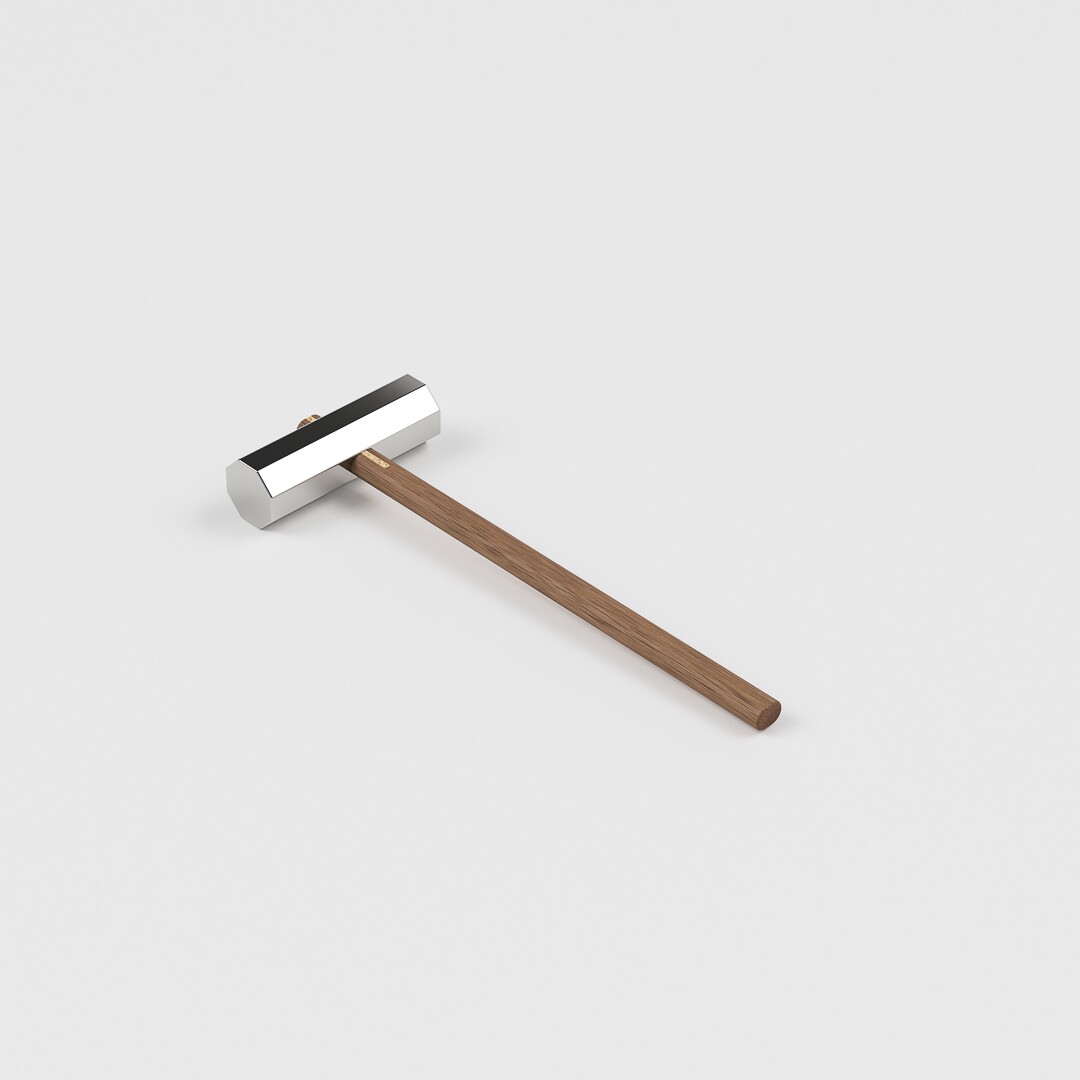
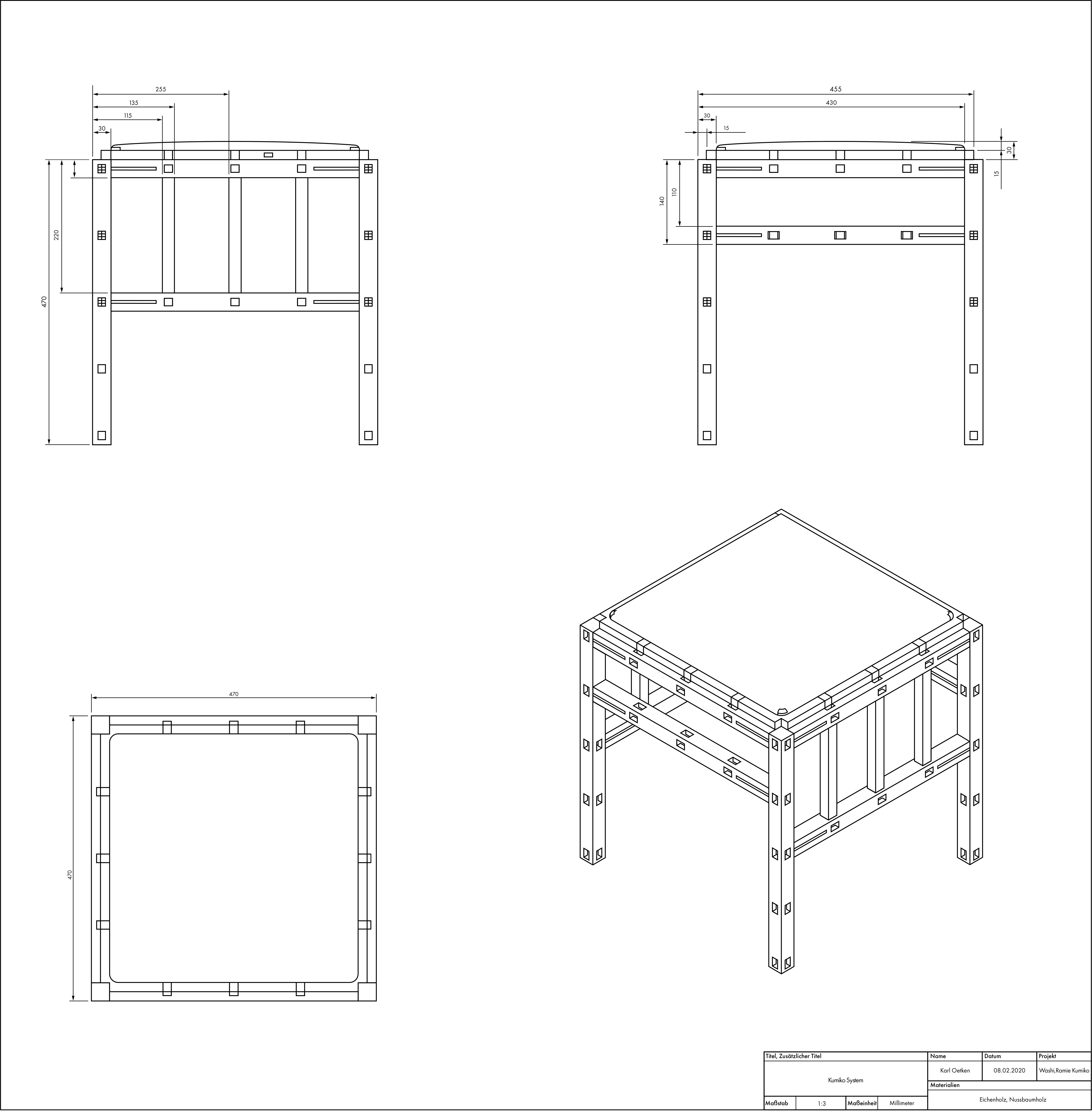
Assembly of the frame
The first pictures show the assembly of the frame with the tools provided in the "set" I designed. The second row shows the assembly of the frame and the seating panel.
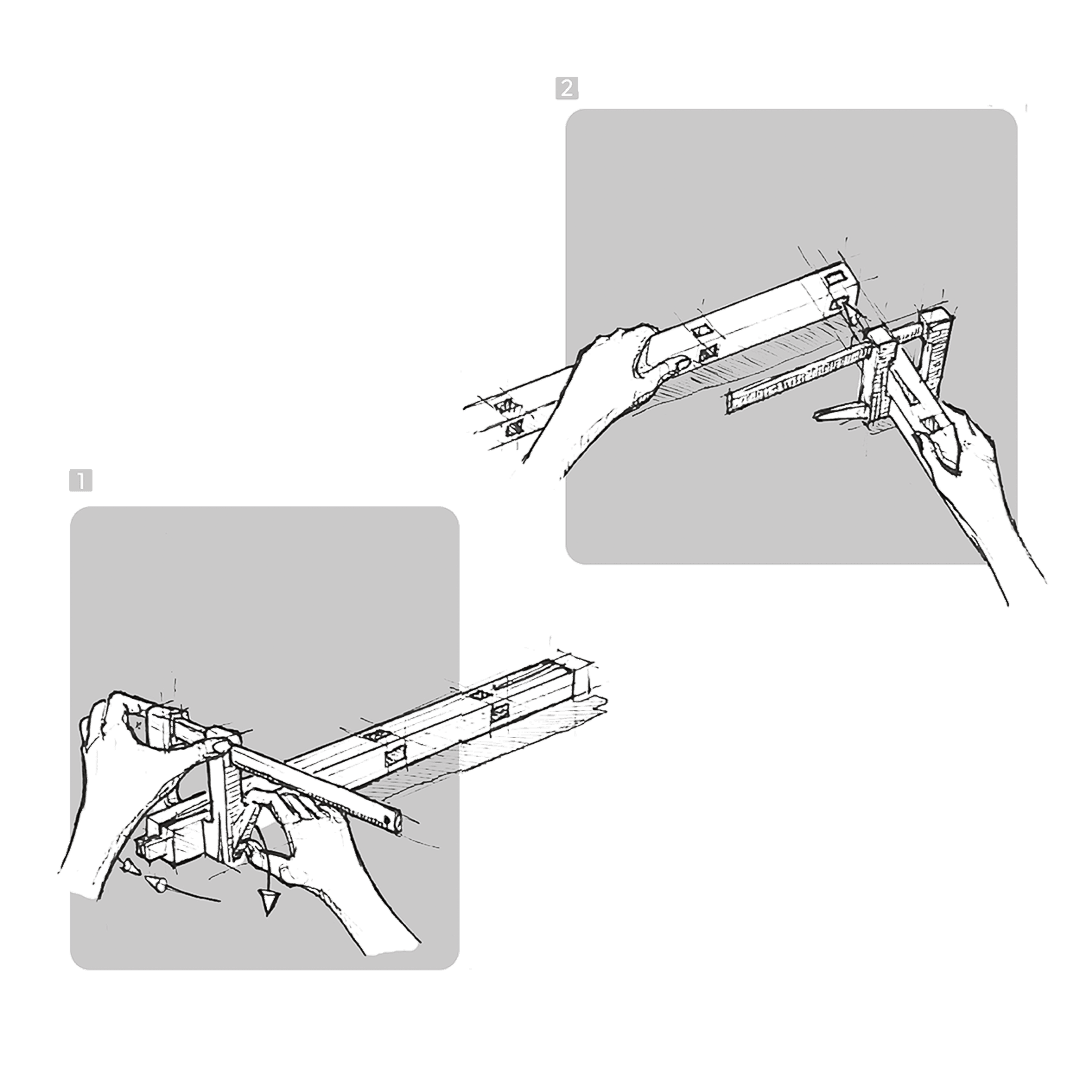
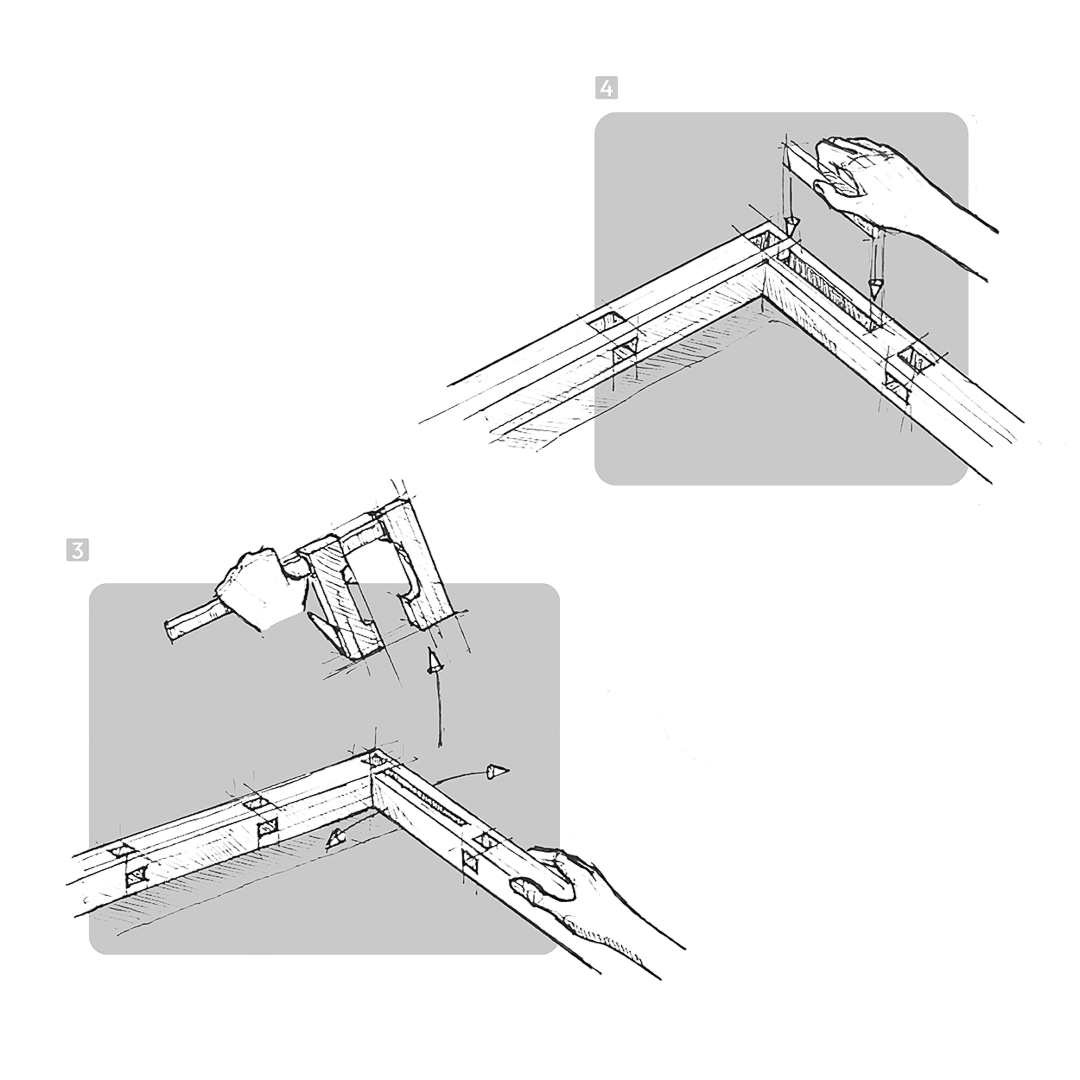
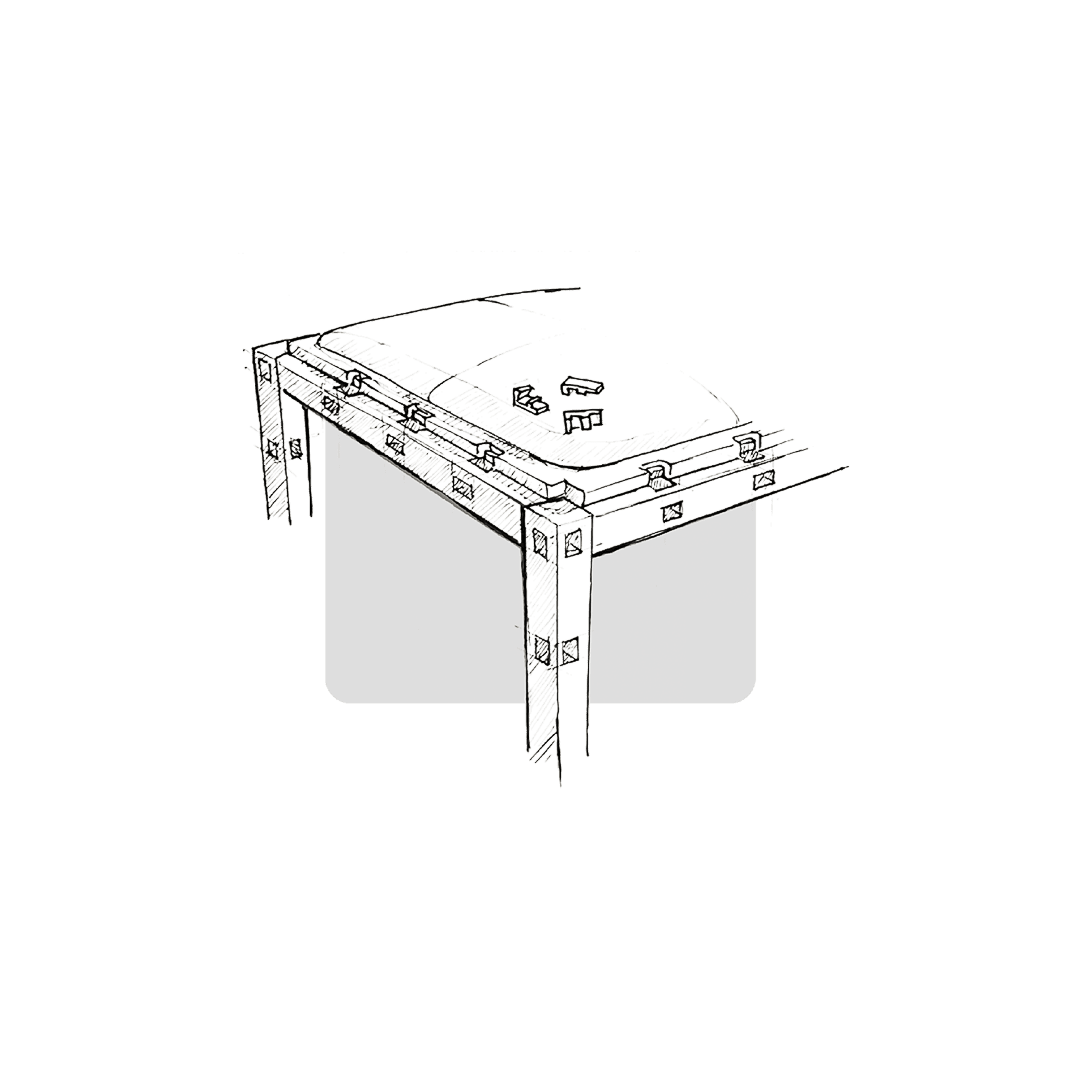
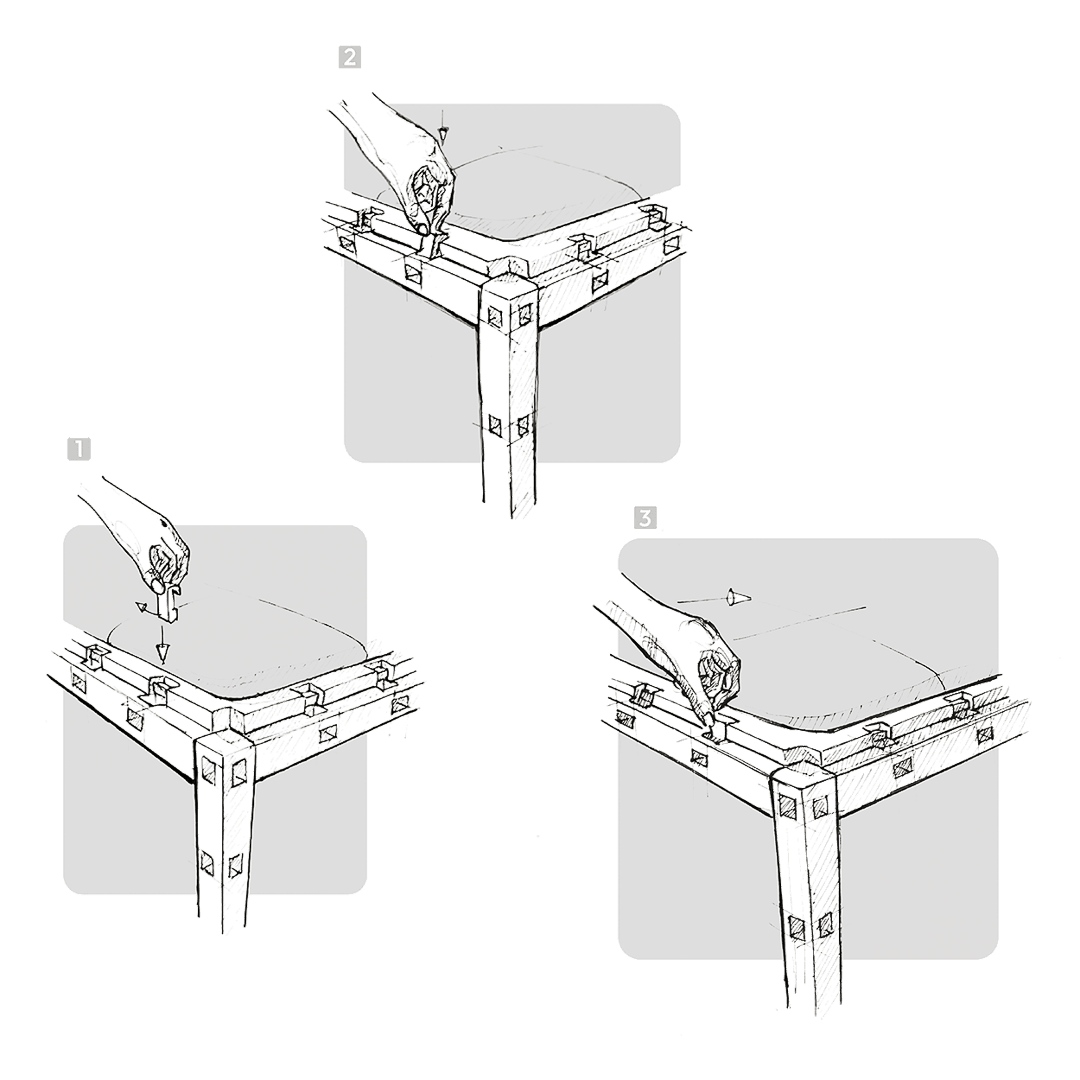
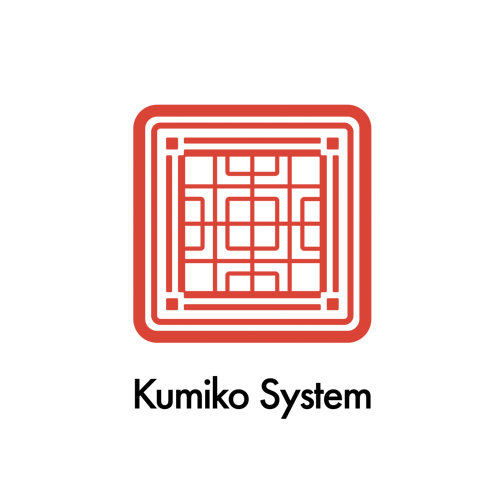
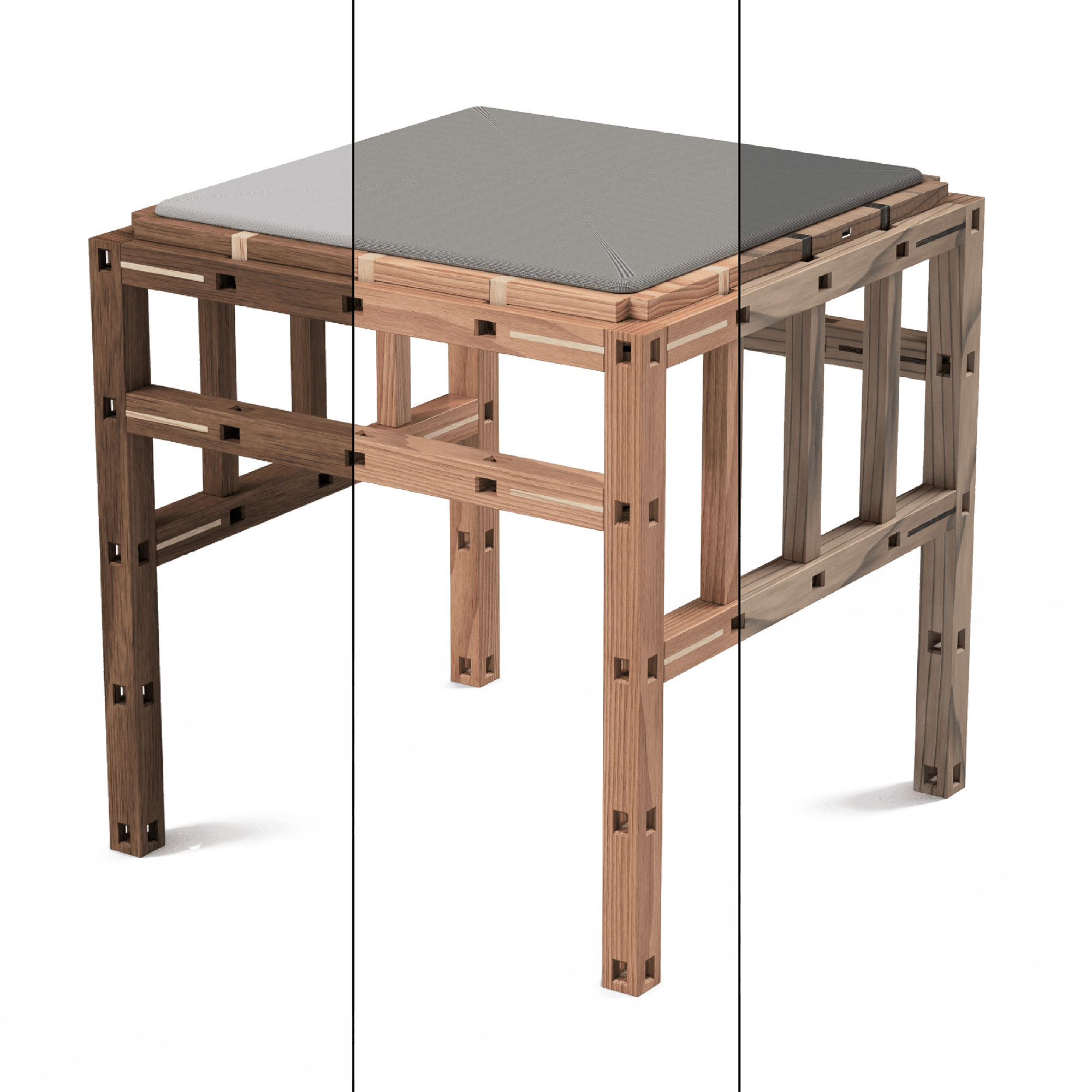
About washi ramie kumiko
The starting point for the project "Washi Rami kumiko" were the two materials washi and ramie and a Japanese woodworking technique called kumiko. The materials and woodworking techniques are deeply rooted in Japanese and Asian culture.
The starting point was the task of transferring the materials and craft techniques to the European cultural space.
I had the intent to design a modular furniture concept focused on the kumiko aspect of the project and on bringing the woodworking technique and effort connected to it closer to people that consume products originating from this craft. The project documented here focuses on only one possible design that originated from the modules, as an example.
Washi is a paper that is produced from mulberry fibers and has been used in Japanese craftsmanship for centuries. It's mostly known for its use in shoji doors (traditional Japanese sliding doors) or lanterns.
Ramie fiber, also called china linen or grass linen, is a fabric that strongly resembles linen in terms of materiality and is obtained from ramie plants, a plant belonging to the nettle family.
Kumiko or "kumiko zaiku" is a traditional woodworking technique from Asia that is based on the principle of sticking together wooden patterns without using any glue.
Prototyping
In the beginning, I decided to use a simple geometric form language, as it has been common in Japan for centuries. The prototypes are made on a small scale (4 cm to 10 cm), which made it possible for me to test numerous variations in three-dimensional space.
I used mat board for the models. Additionally, I used a small roll of fiber fleece tape to better represent the shape of the cushions.
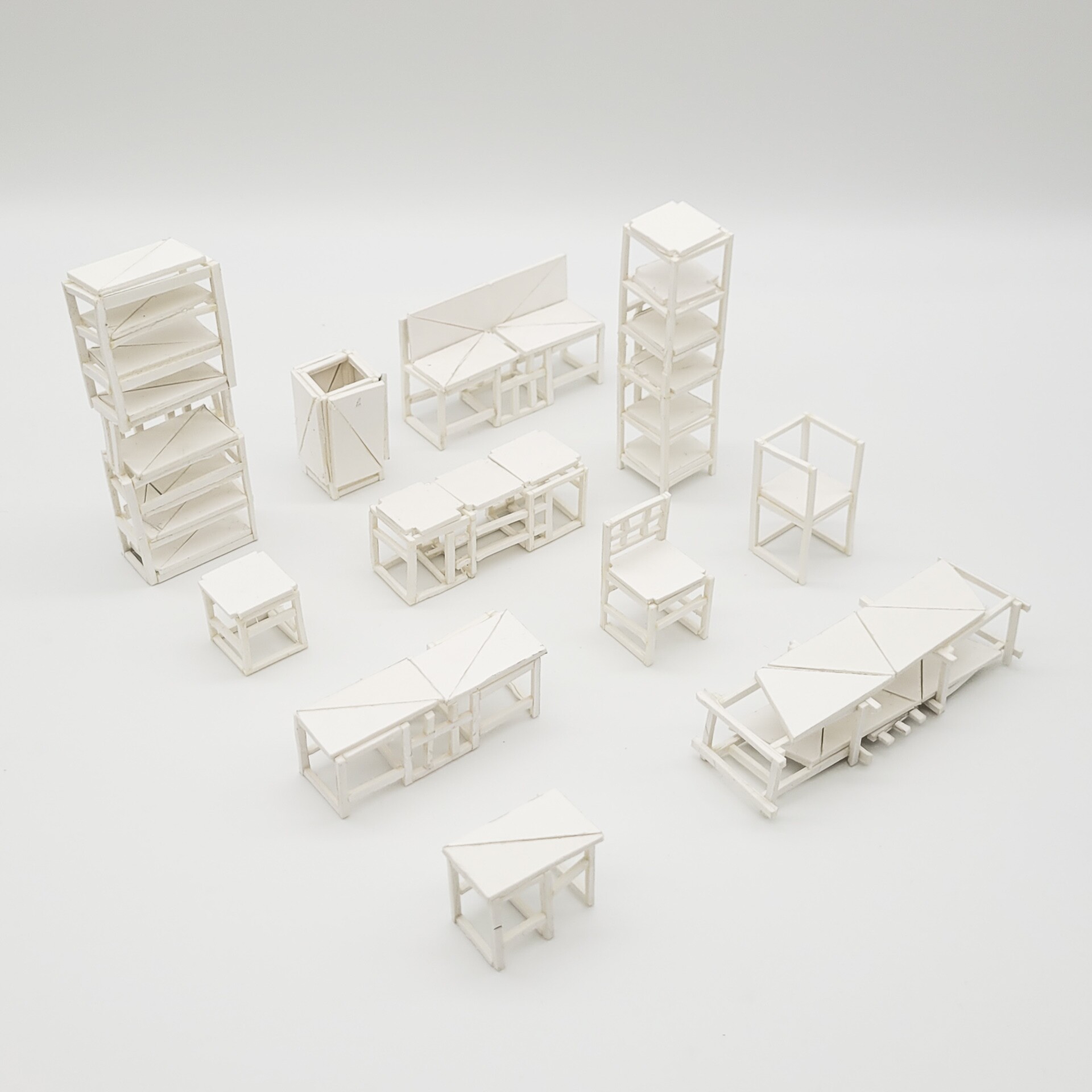
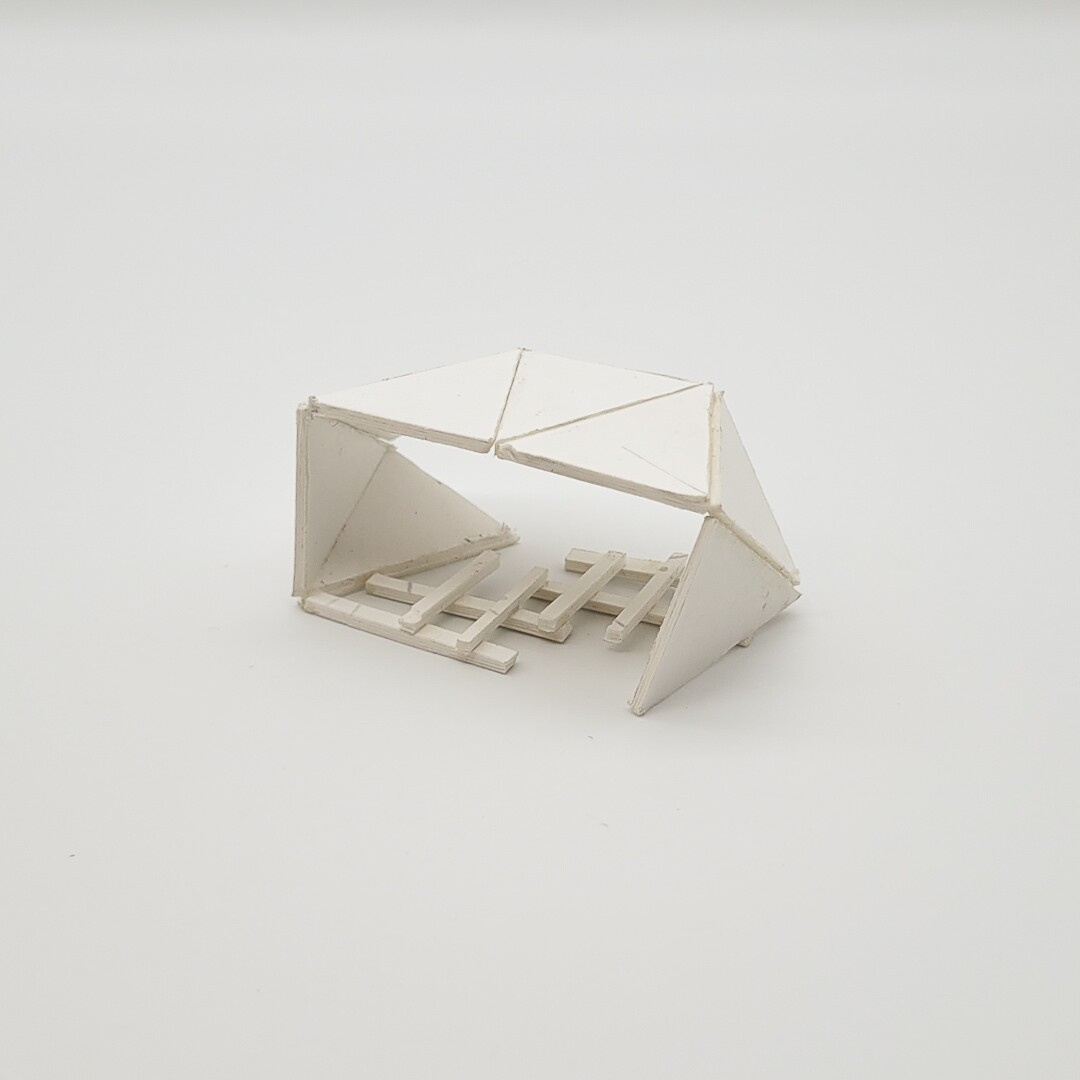
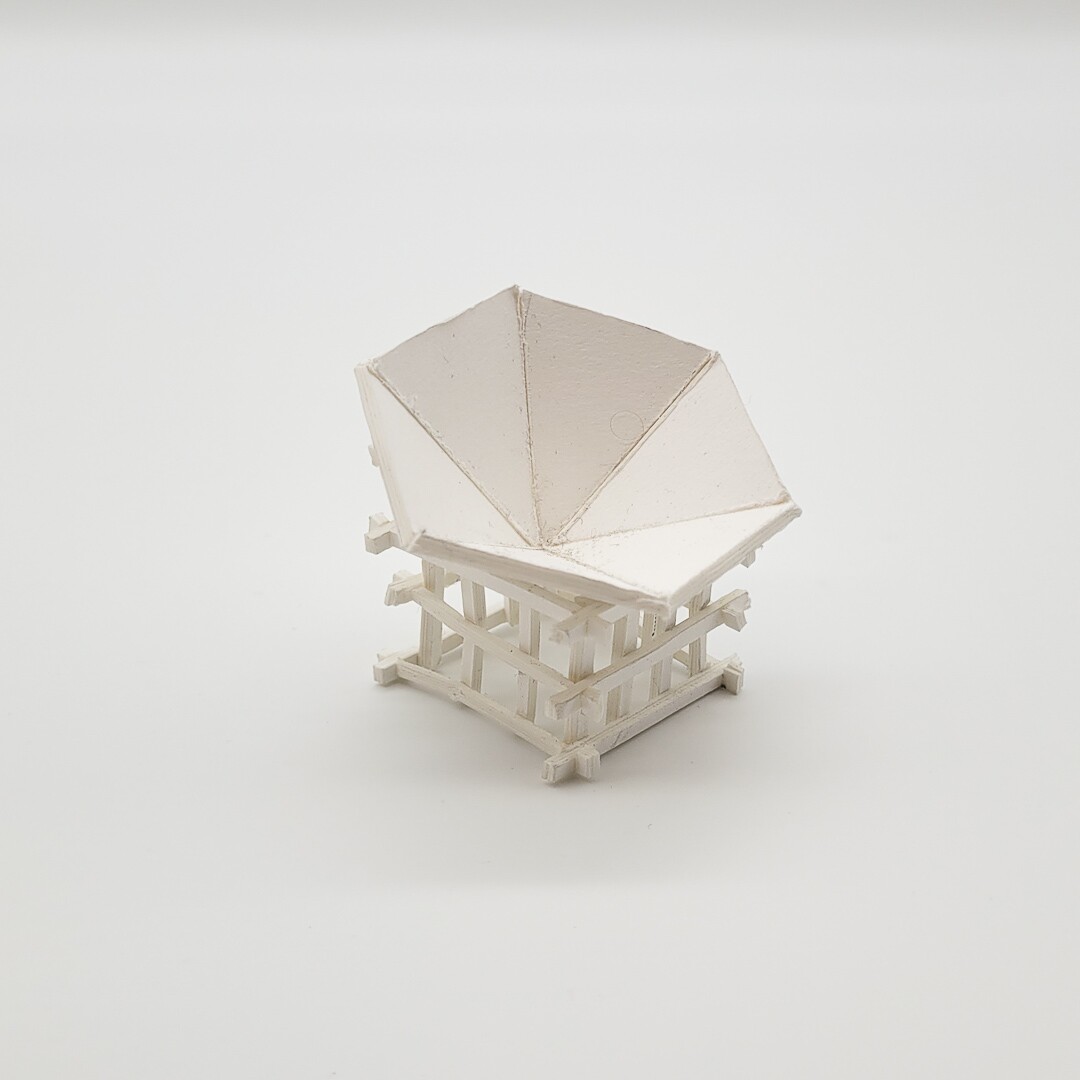
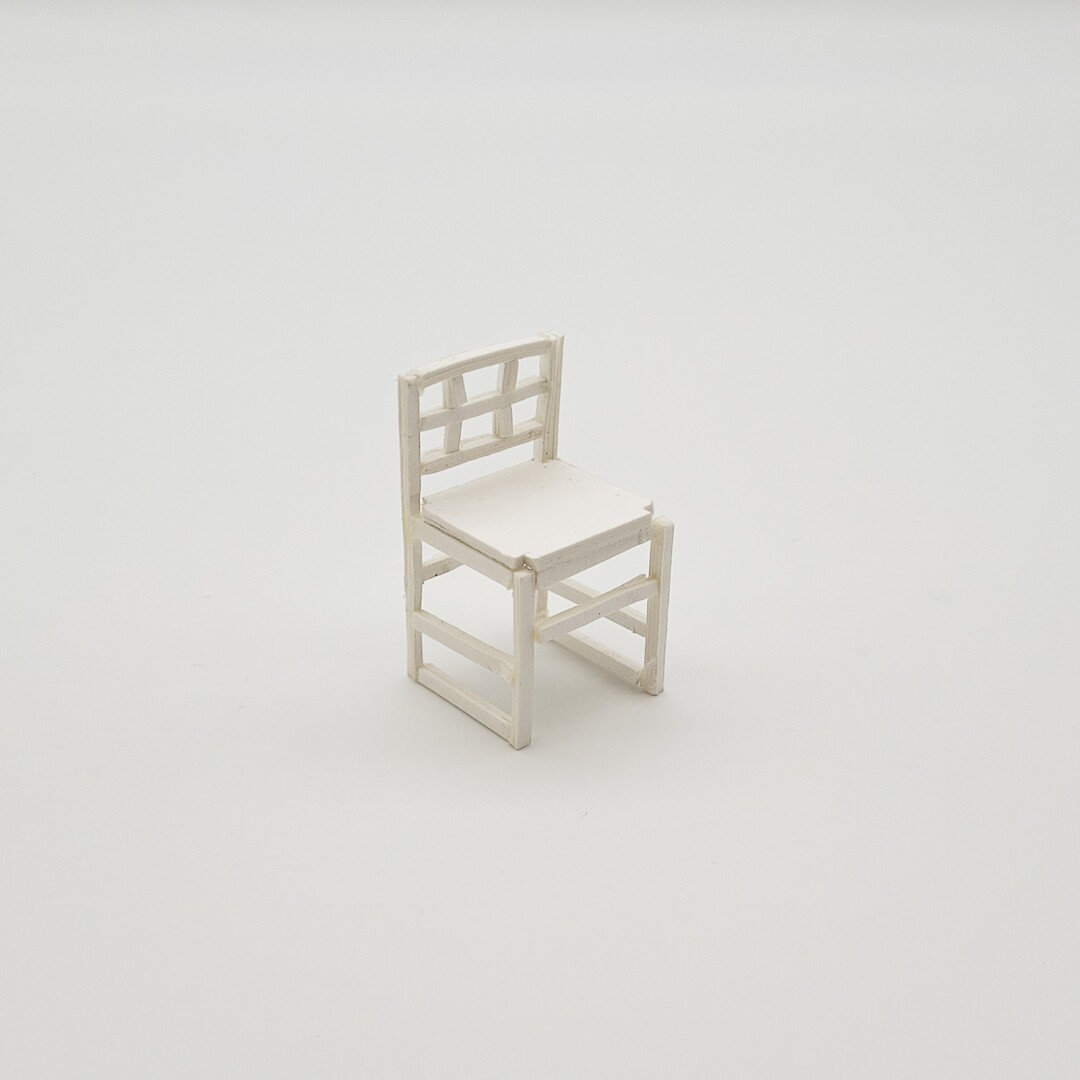
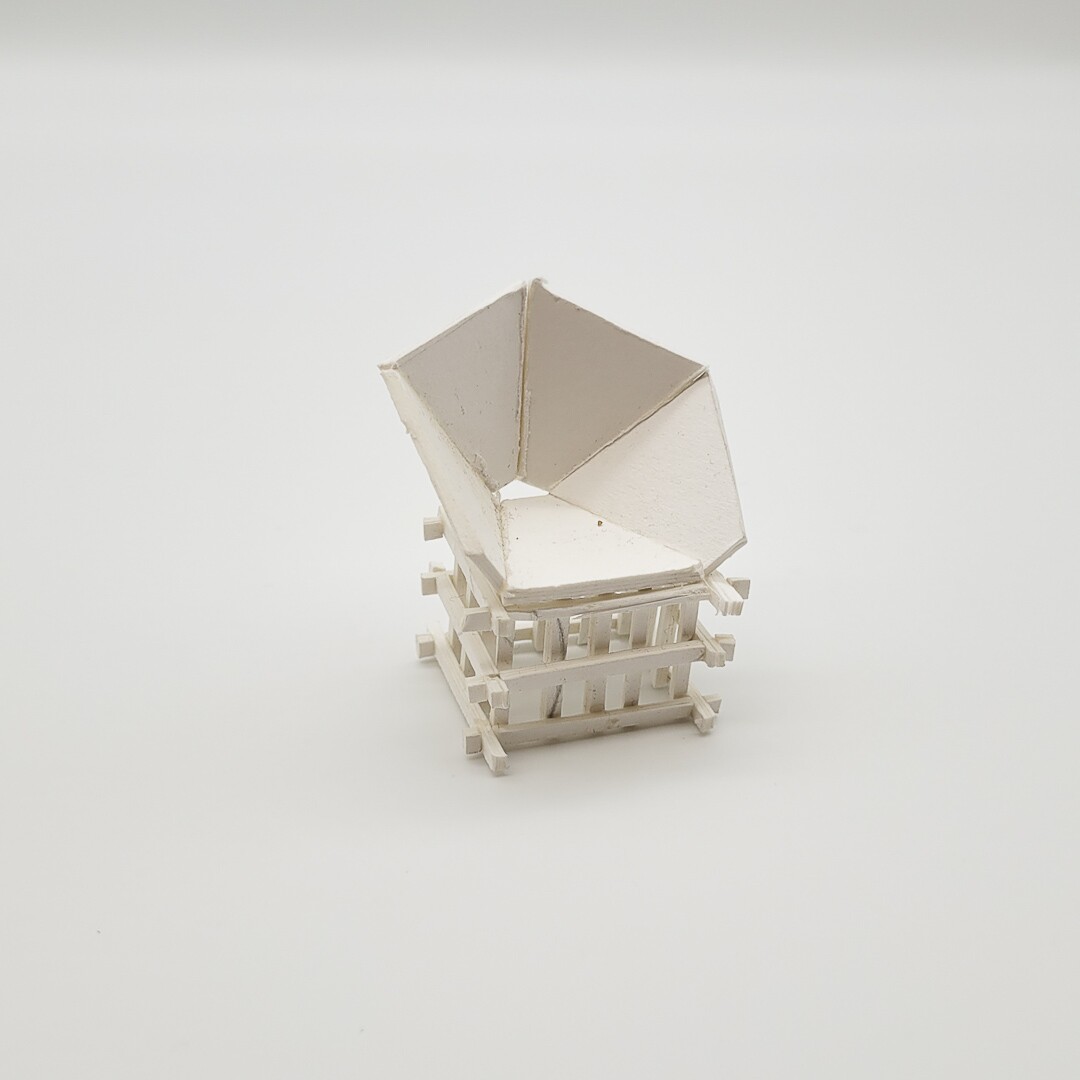
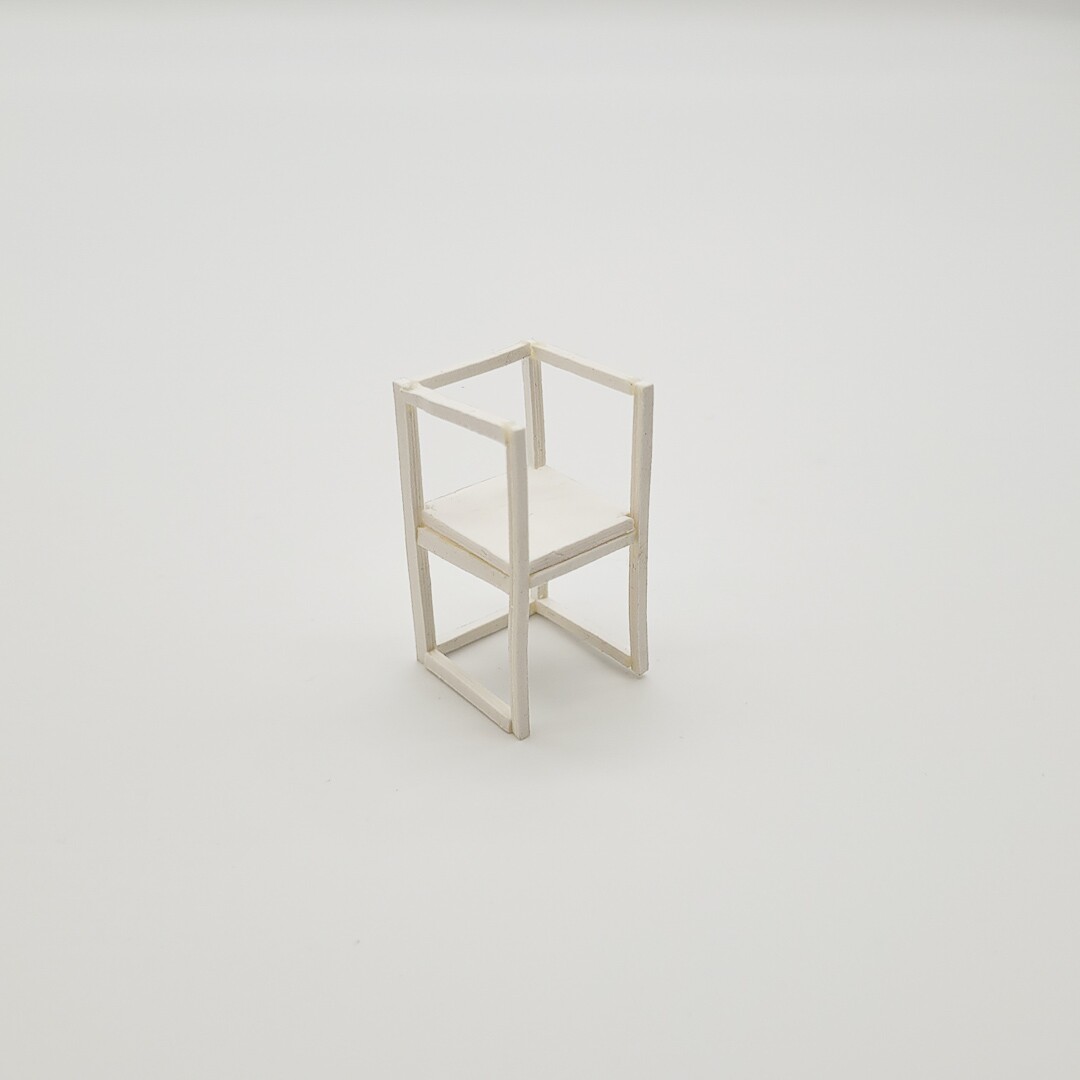
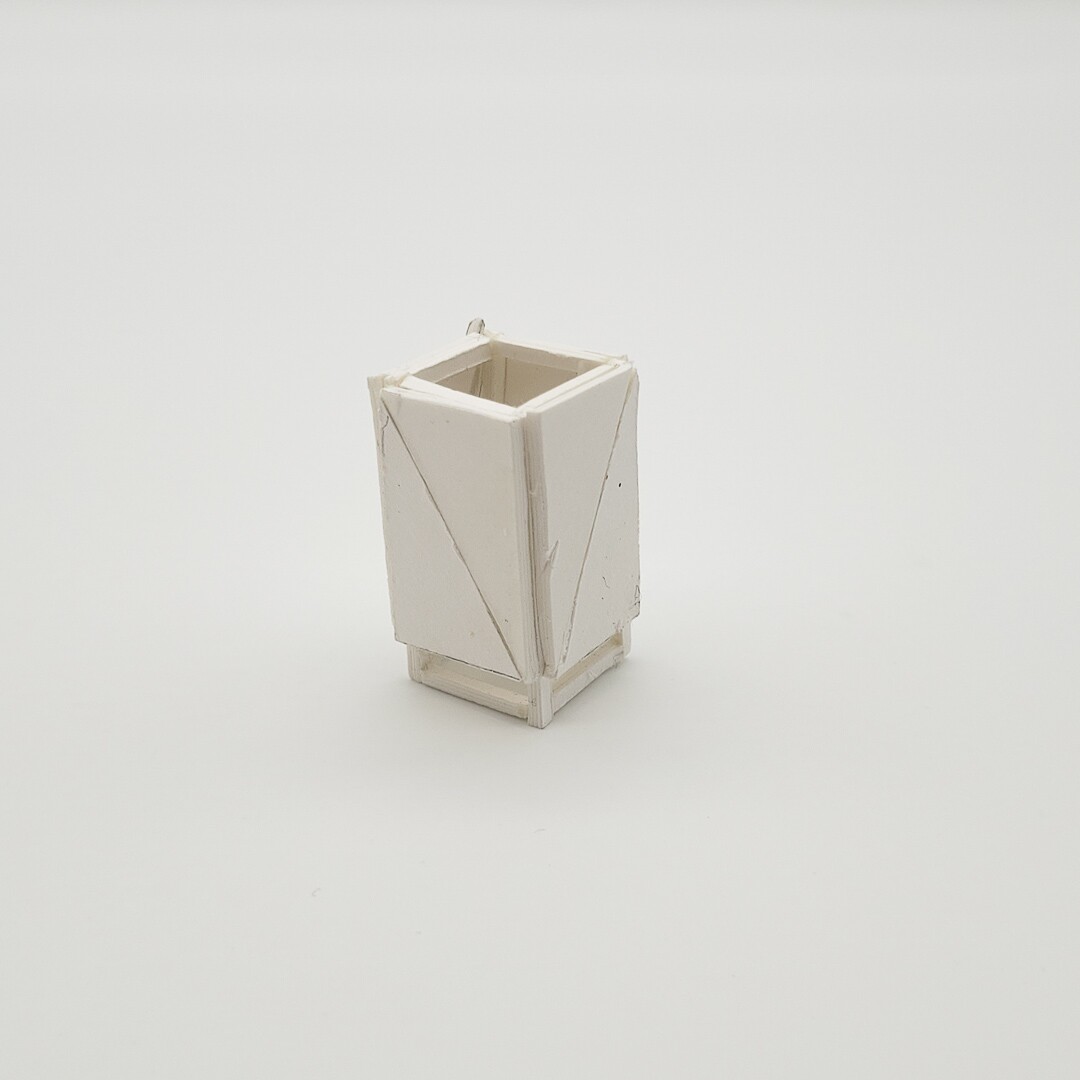
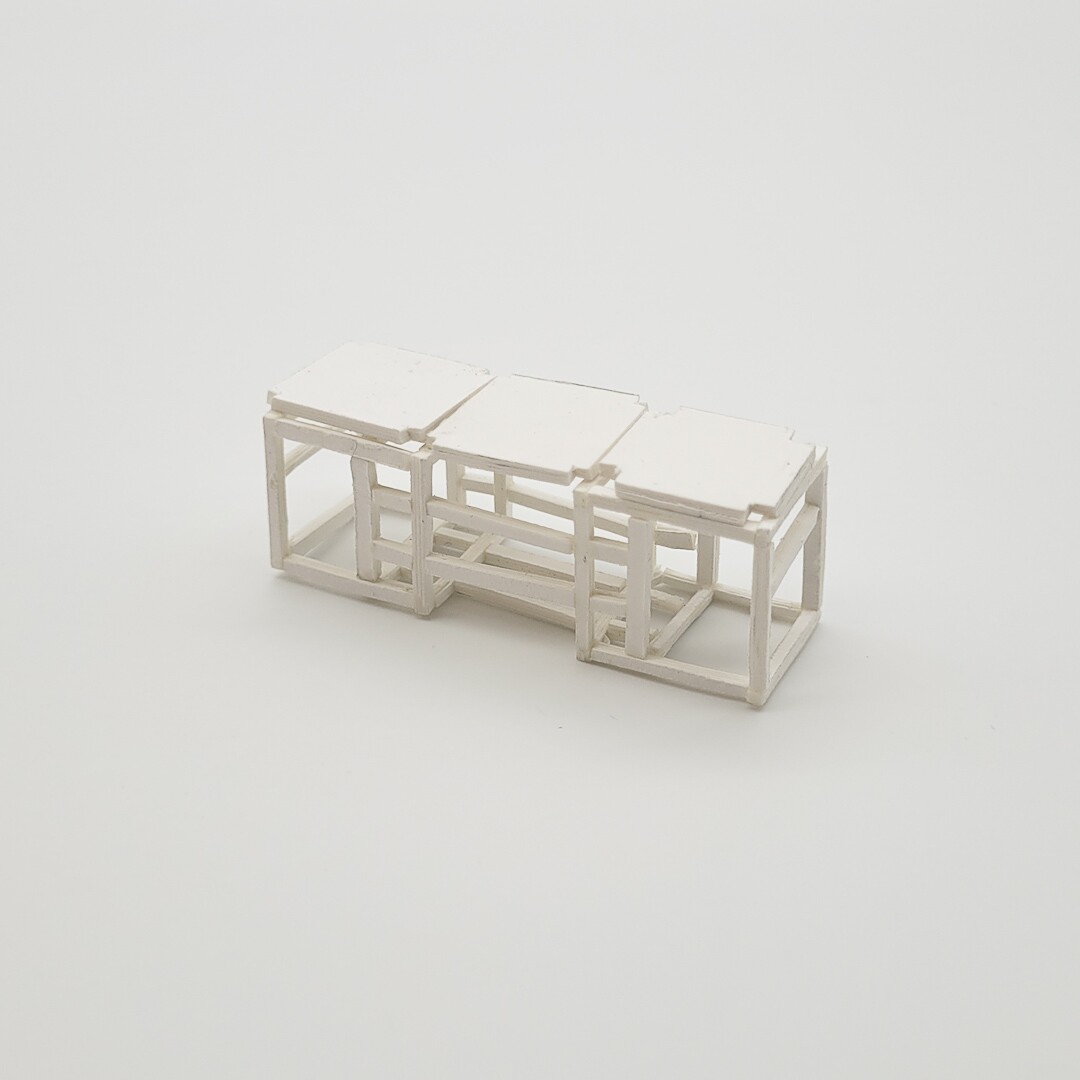
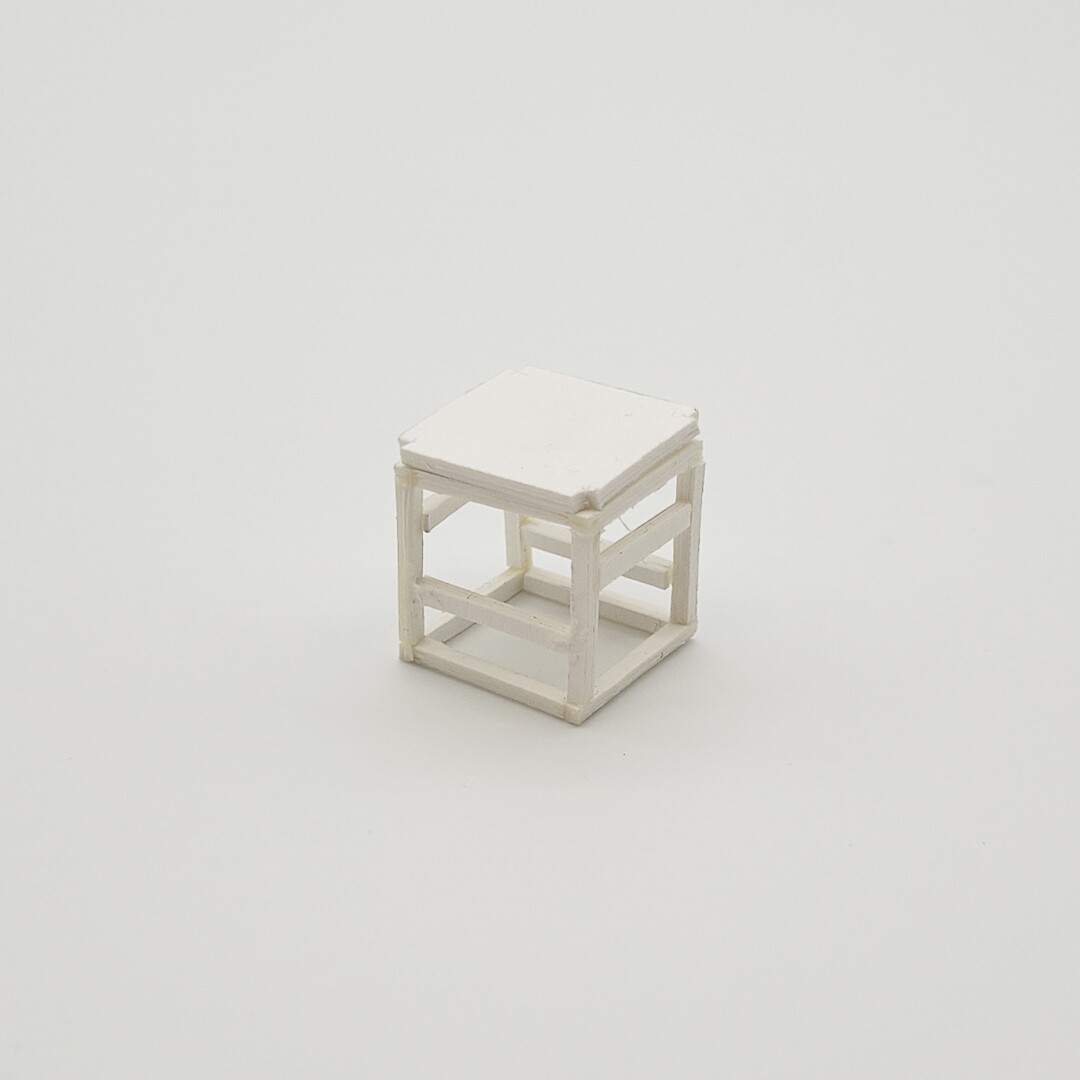
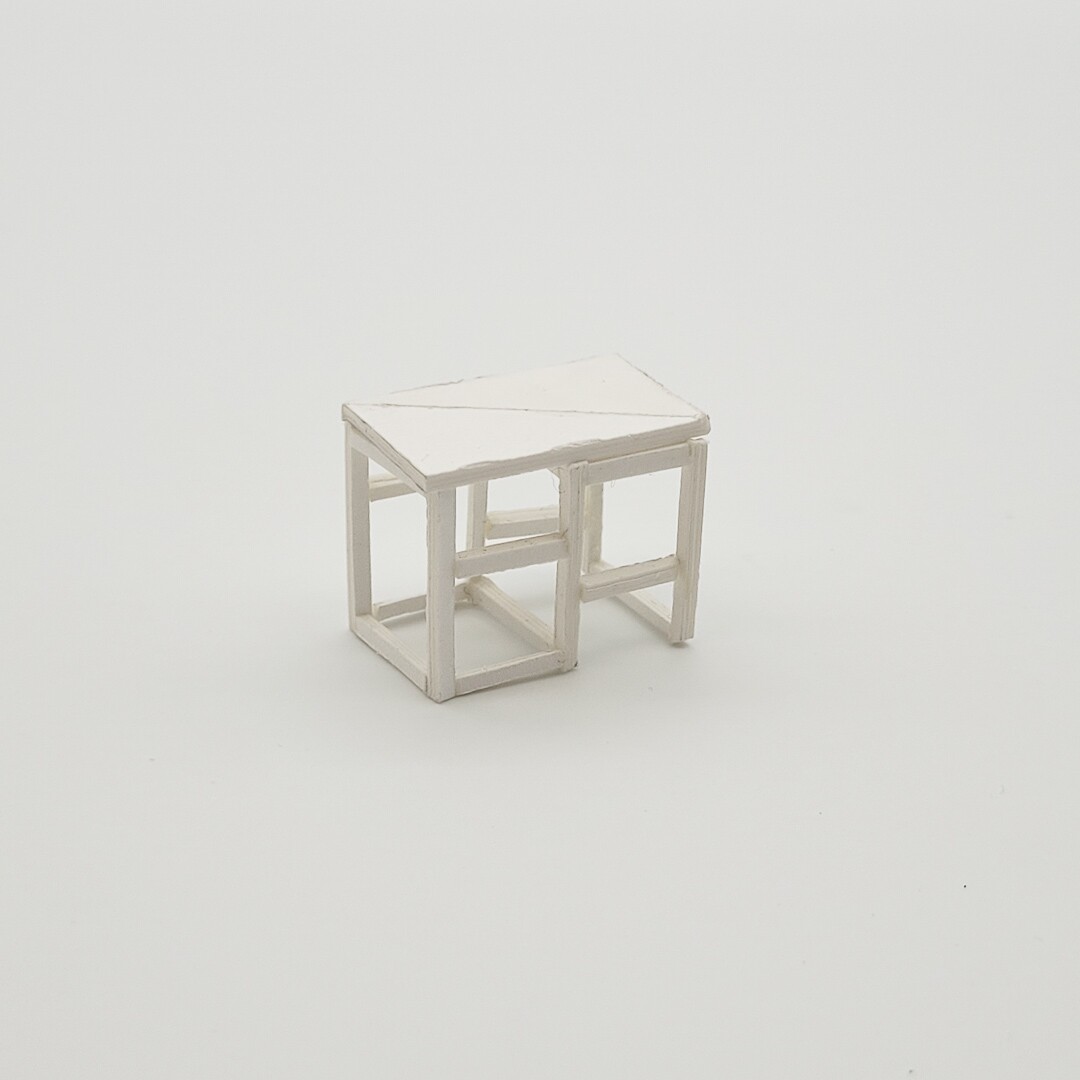
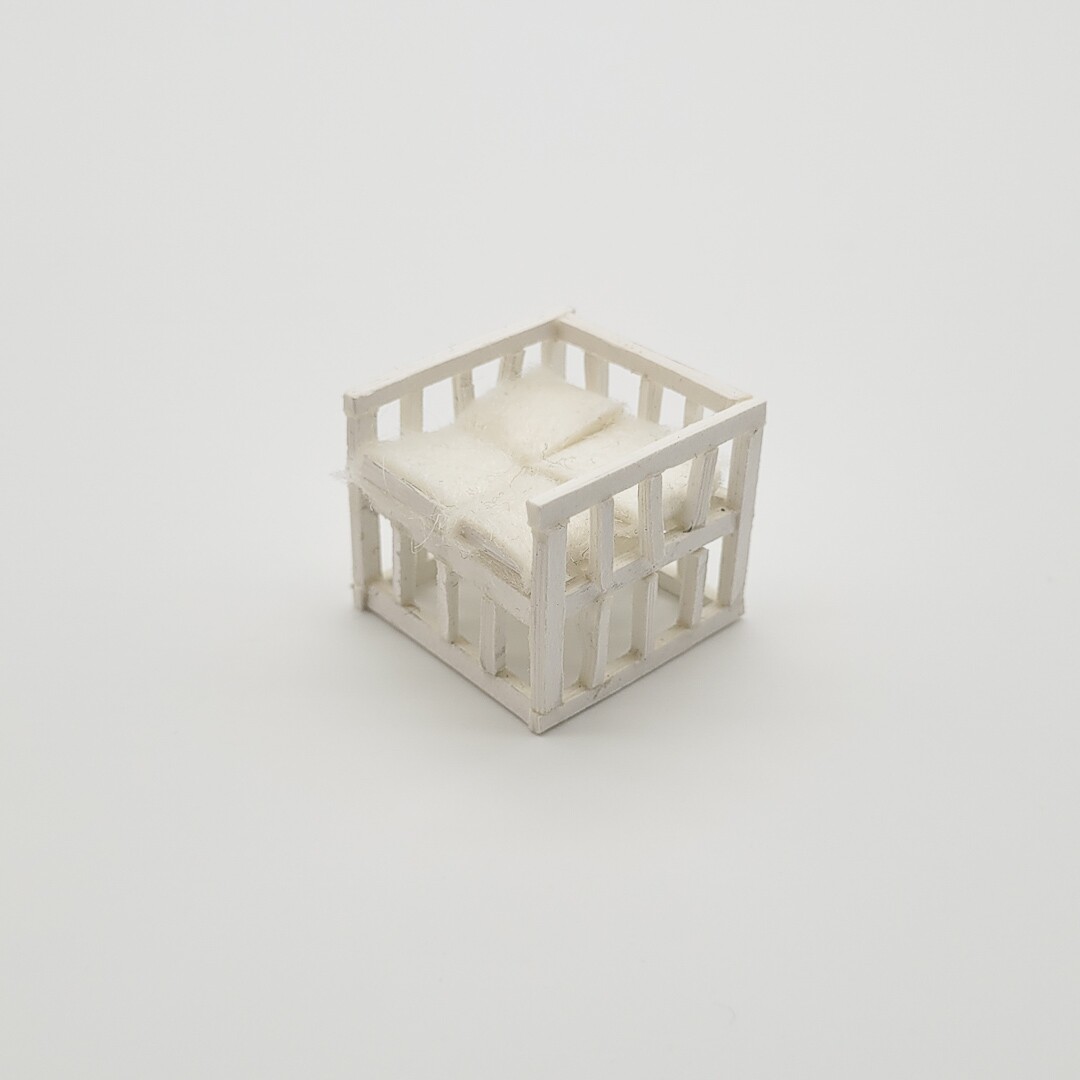
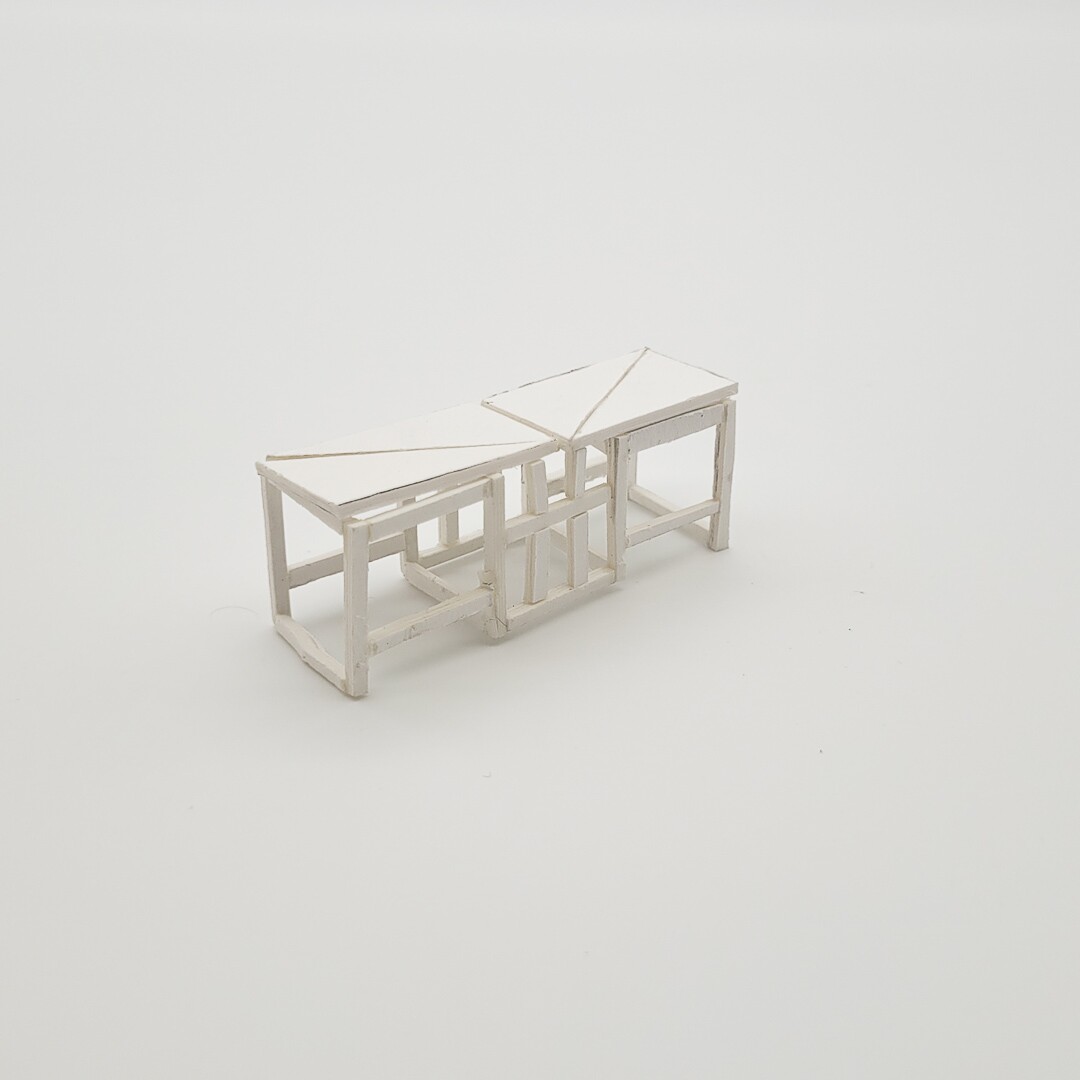
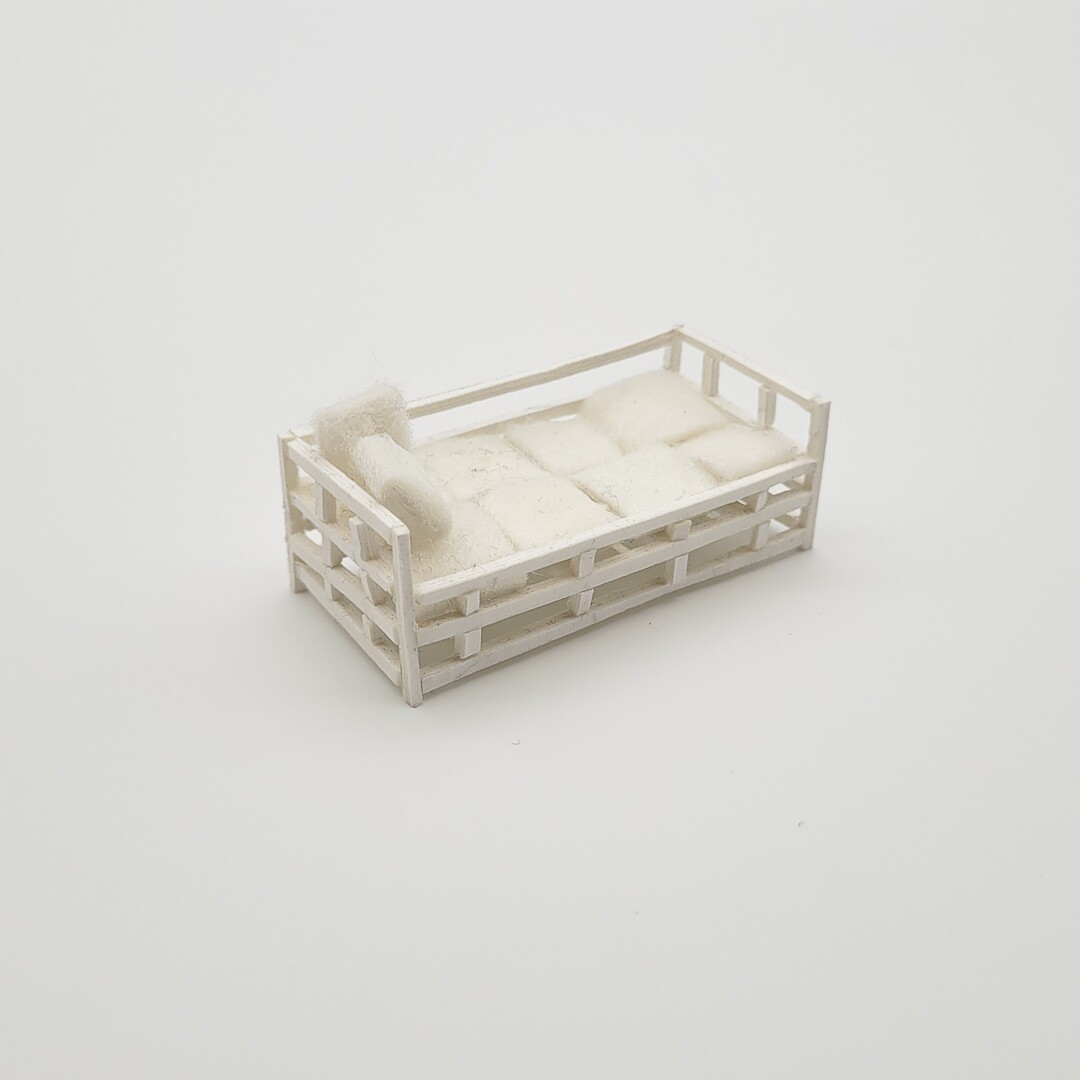
1to1 prototype/ergonomics
For the design of a piece of furniture with a participatory approach to assembly, there are some ergonomic values to consider besides the seat height, e.g., the gripping spaces and the edges of the individual modules during assembly, even if these are no longer considered after the furniture is assembled. The table shows some reference values from the "Kleine ergonomische Datensammlung", which I commonly use as a reference. Important for my product were primarily the dimensions of the seat surface and the seat height. I calculated with the 95th percentile values for the dimensions due to my own height.
.png)
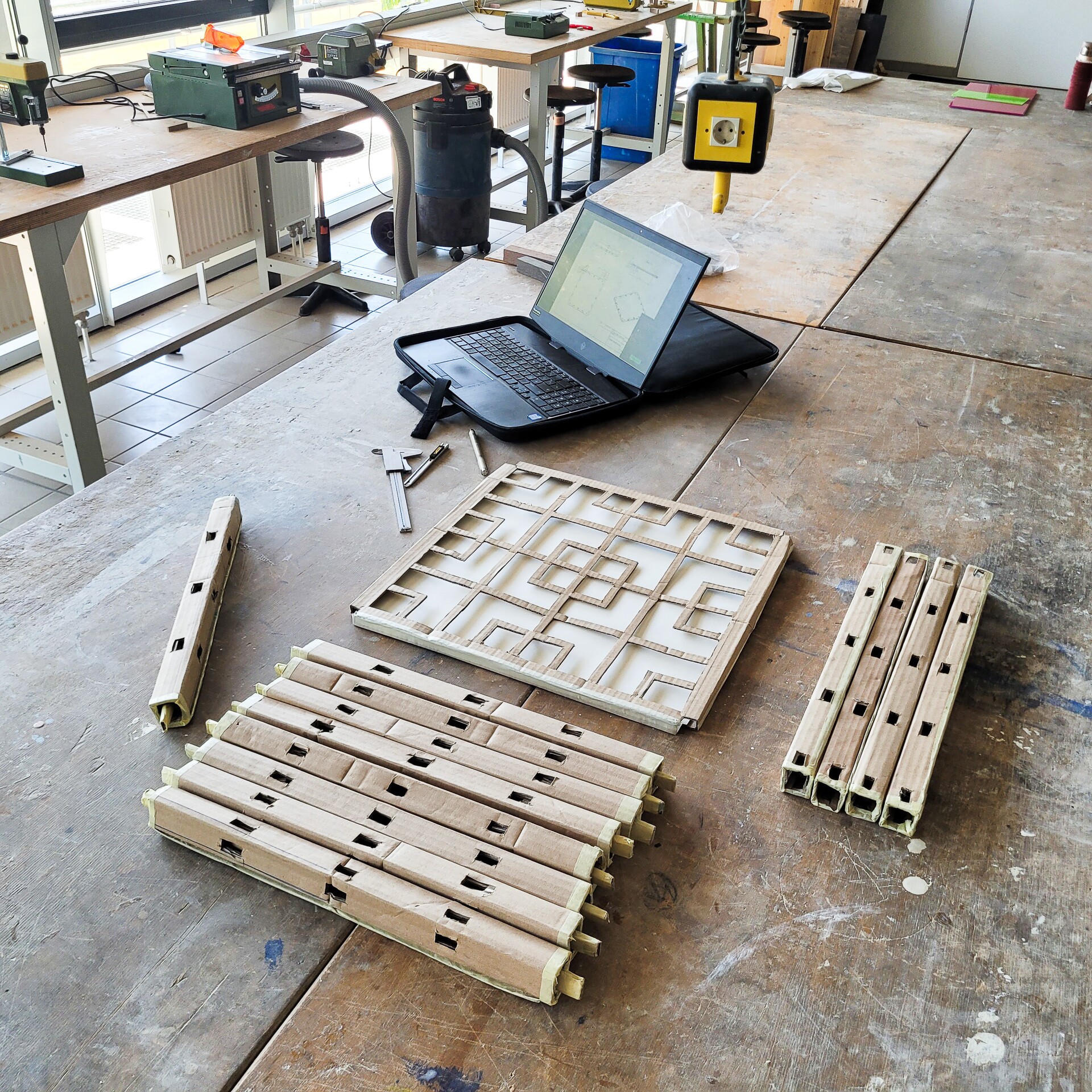

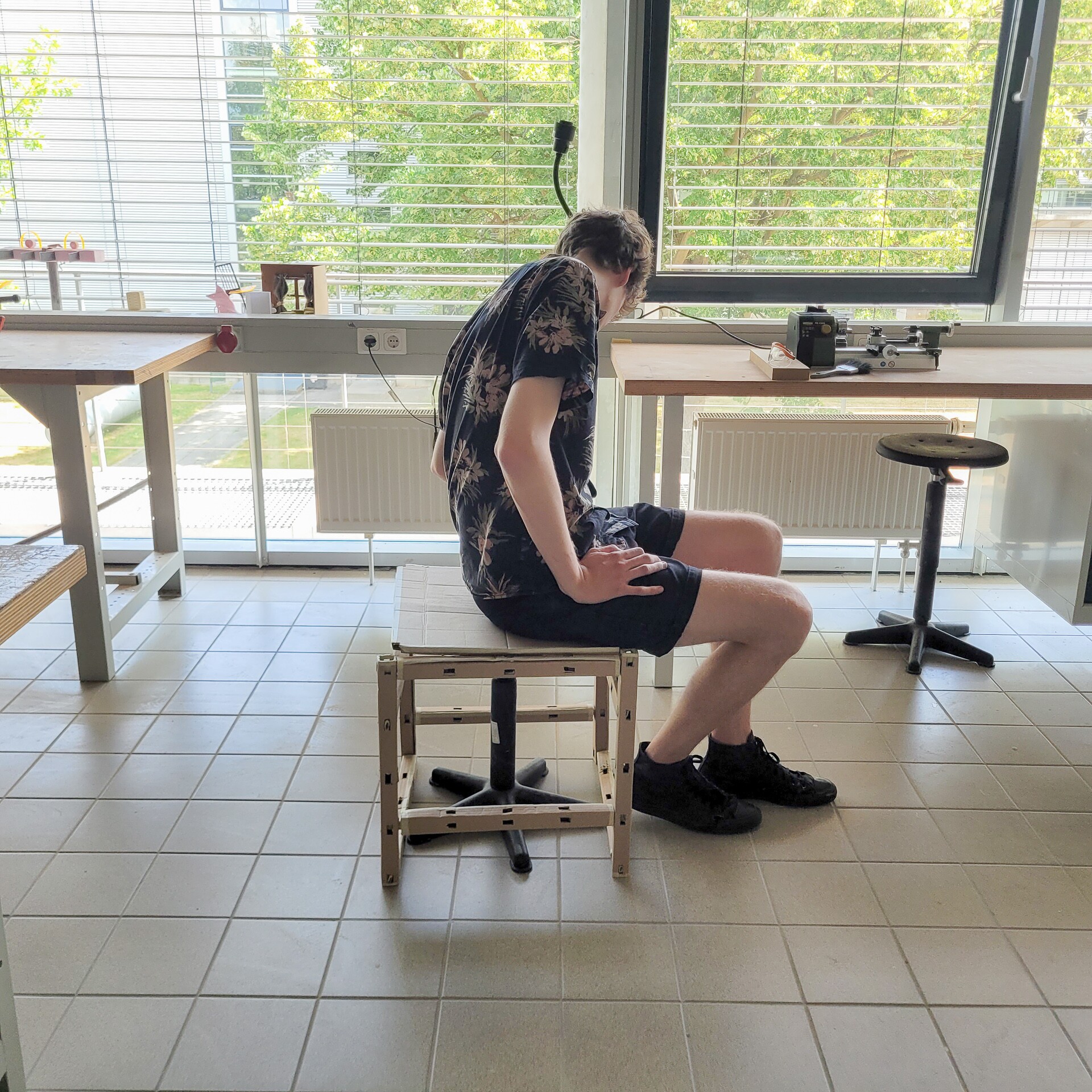
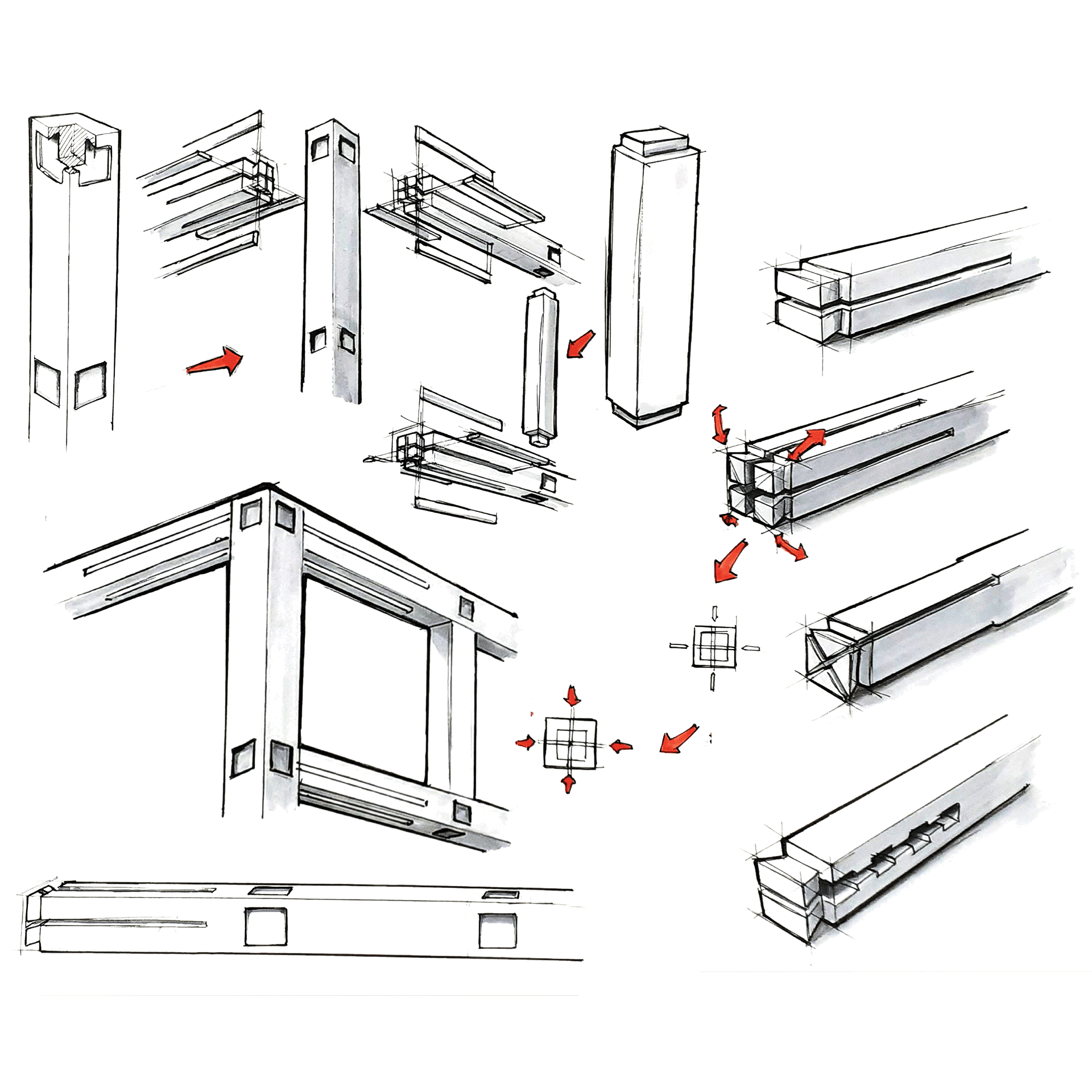
The Frame
The following sketches show the two concepts I considered most appropriate for keeping the frame together. Both are rooted in the "kumiko" concept, so they work just by sticking them together. To me, the connection provided by the flexibility of the wood seemed more interesting, and at the same time, I wouldn't have to use extra materials except for some small wooden plates to stabilize the connection.
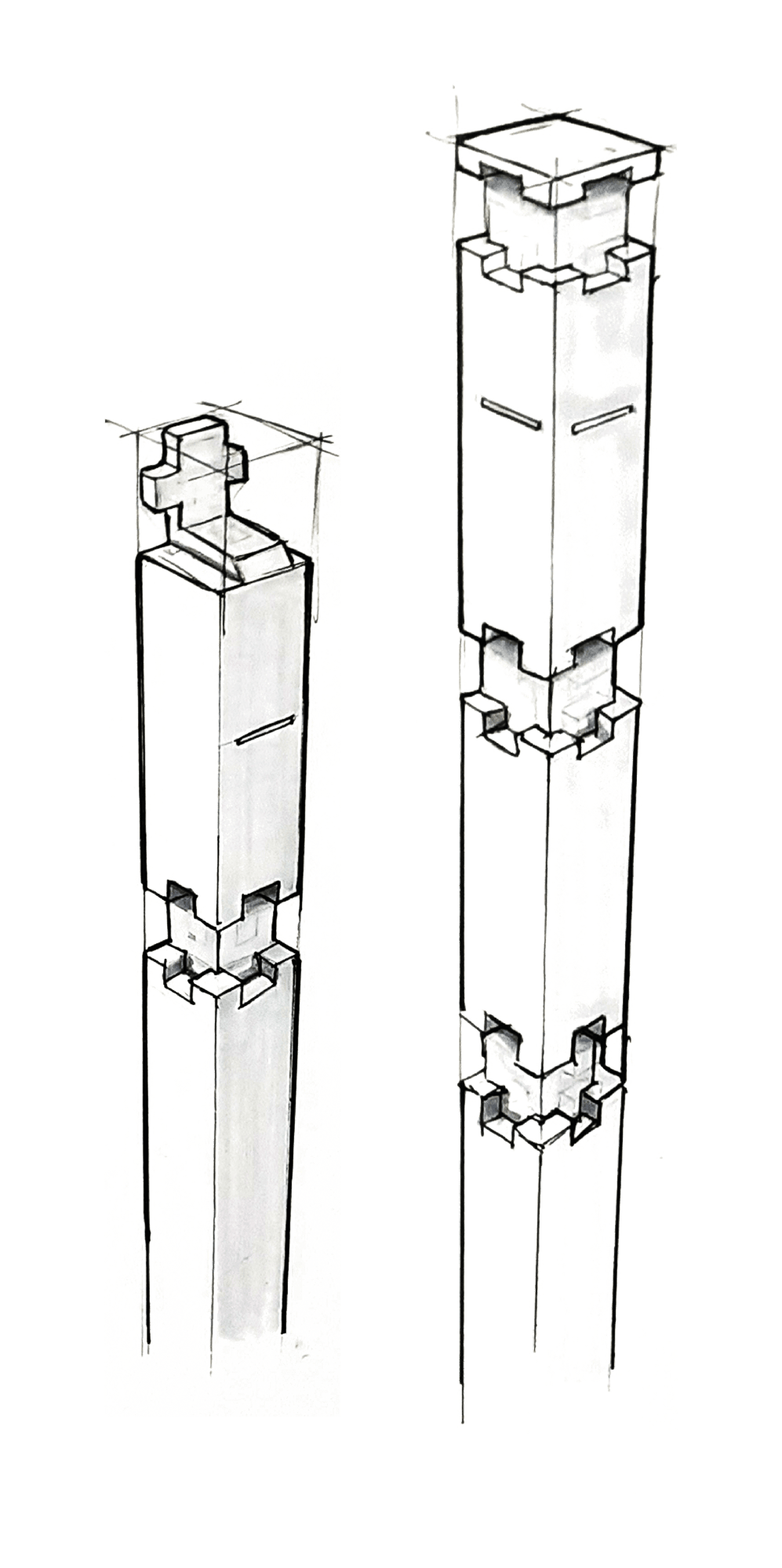
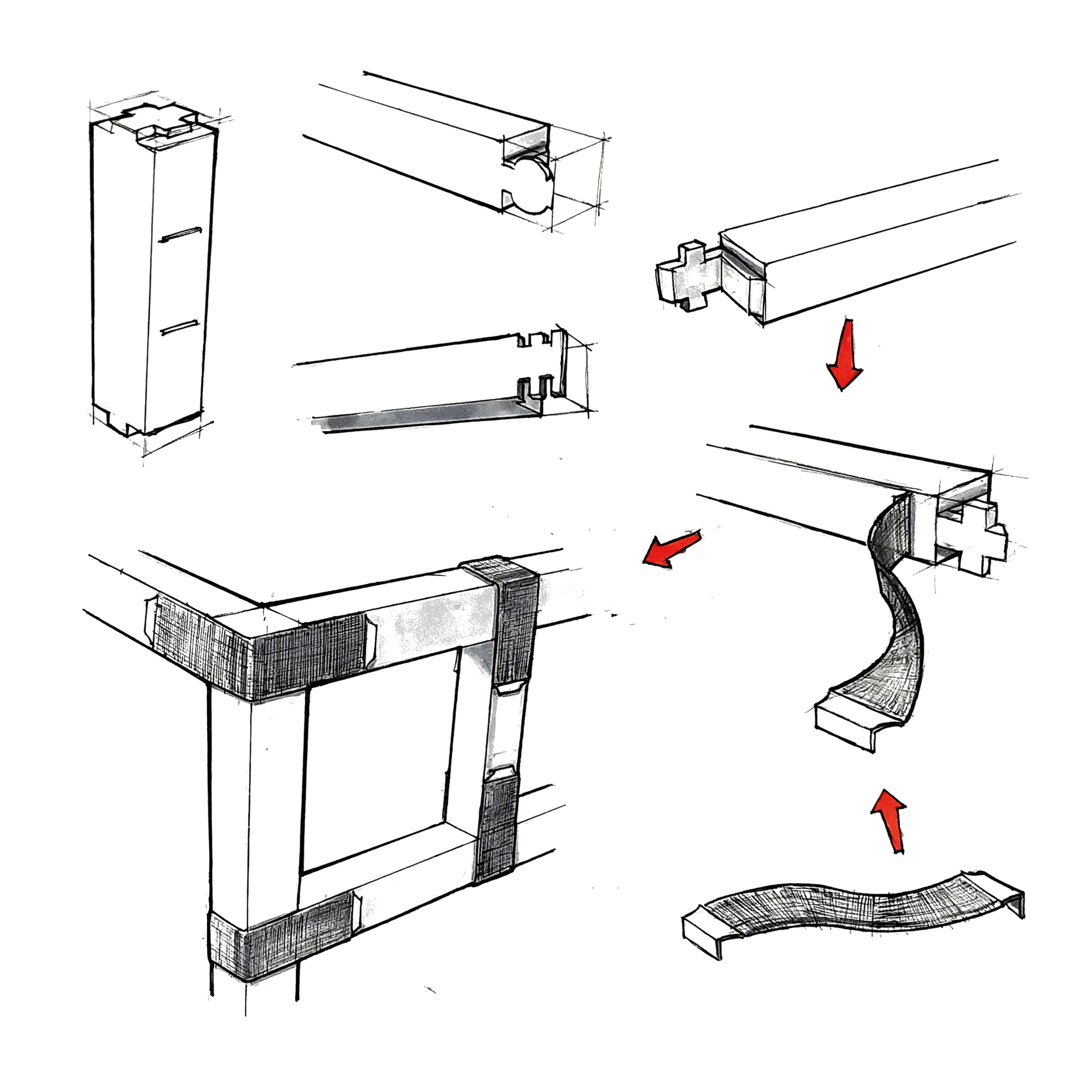
Choosing the wood
To choose the best of the joints I designed, I made my prototypes from different woods. I tested the woods that are listed in the following picture on the properties documented in the chart with the wood types.
.png)
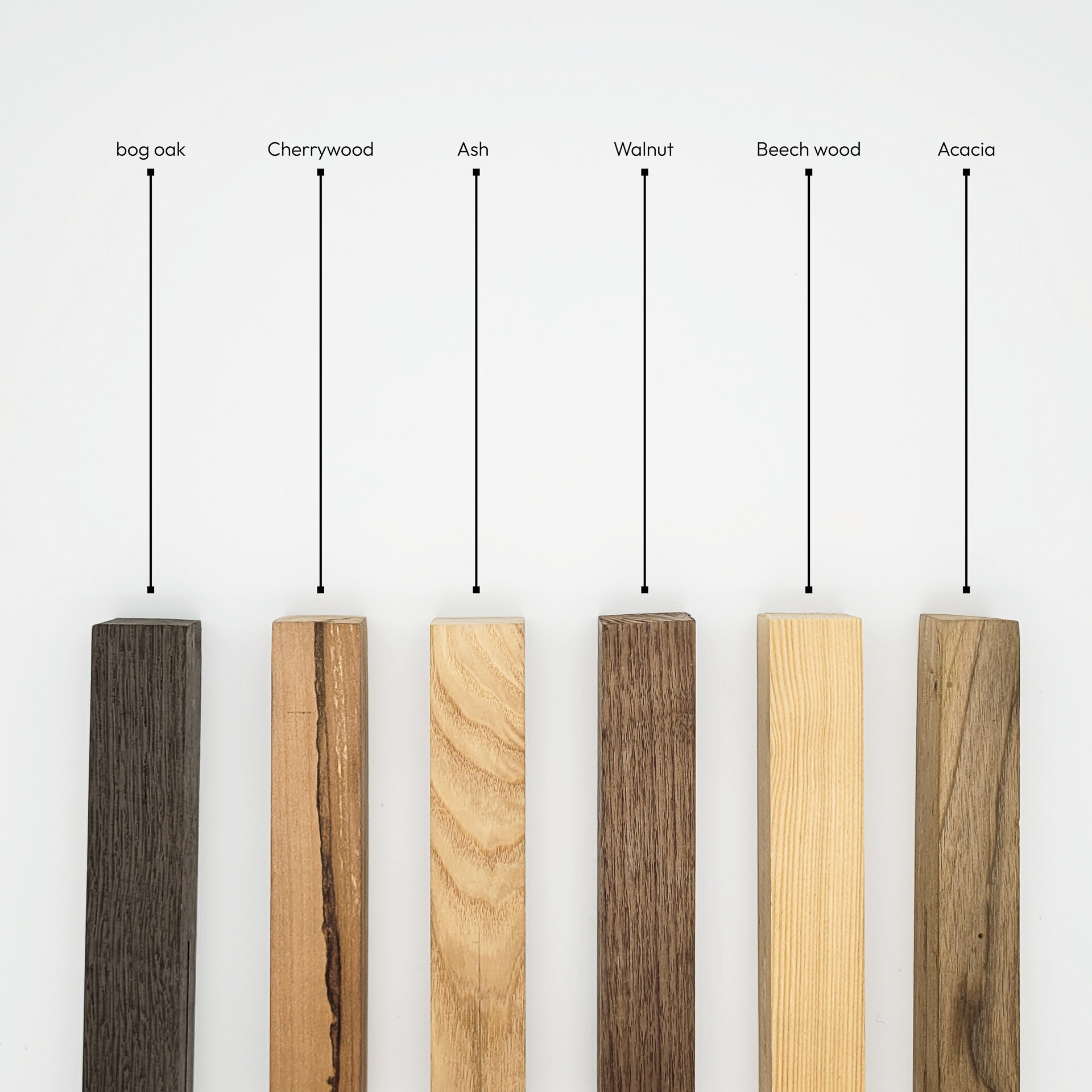
The connector shape
The project was executed during the Corona lockdowns. For this reason, I created the prototypes at home and 3D-printed the square-drilled and mortised joints for myself. Even though this makes the results less reliable, it was my only way to build a halfway-suitable prototype at the time. After testing, walnut and cherry woods turned out to be the most suitable. I chose to use walnut wood because it is available from many online retailers. For the connection, I chose the third one documented below (marked in red) for the 3D model and later switched to the last one of the prototypes (marked in yellow) for the model I built.
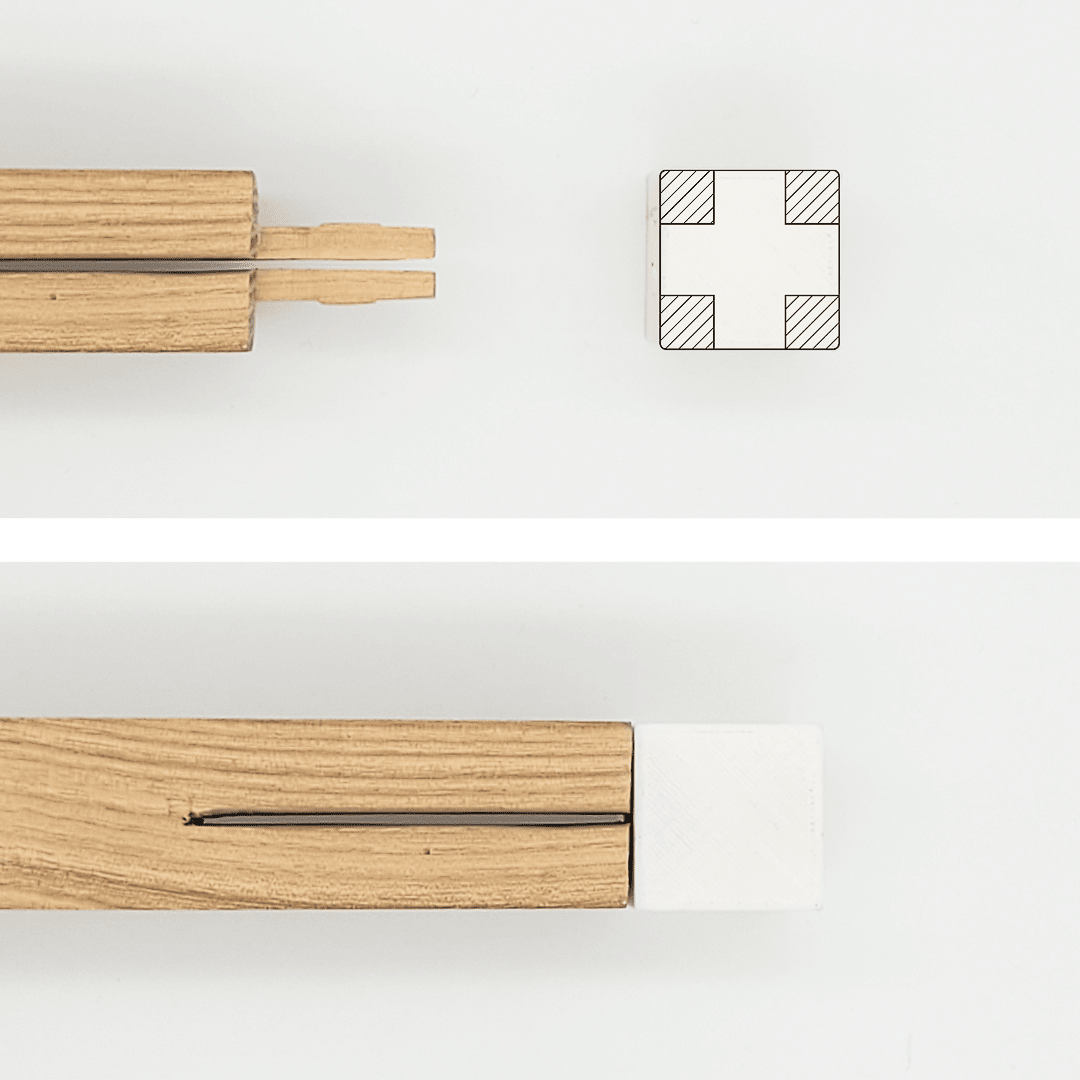
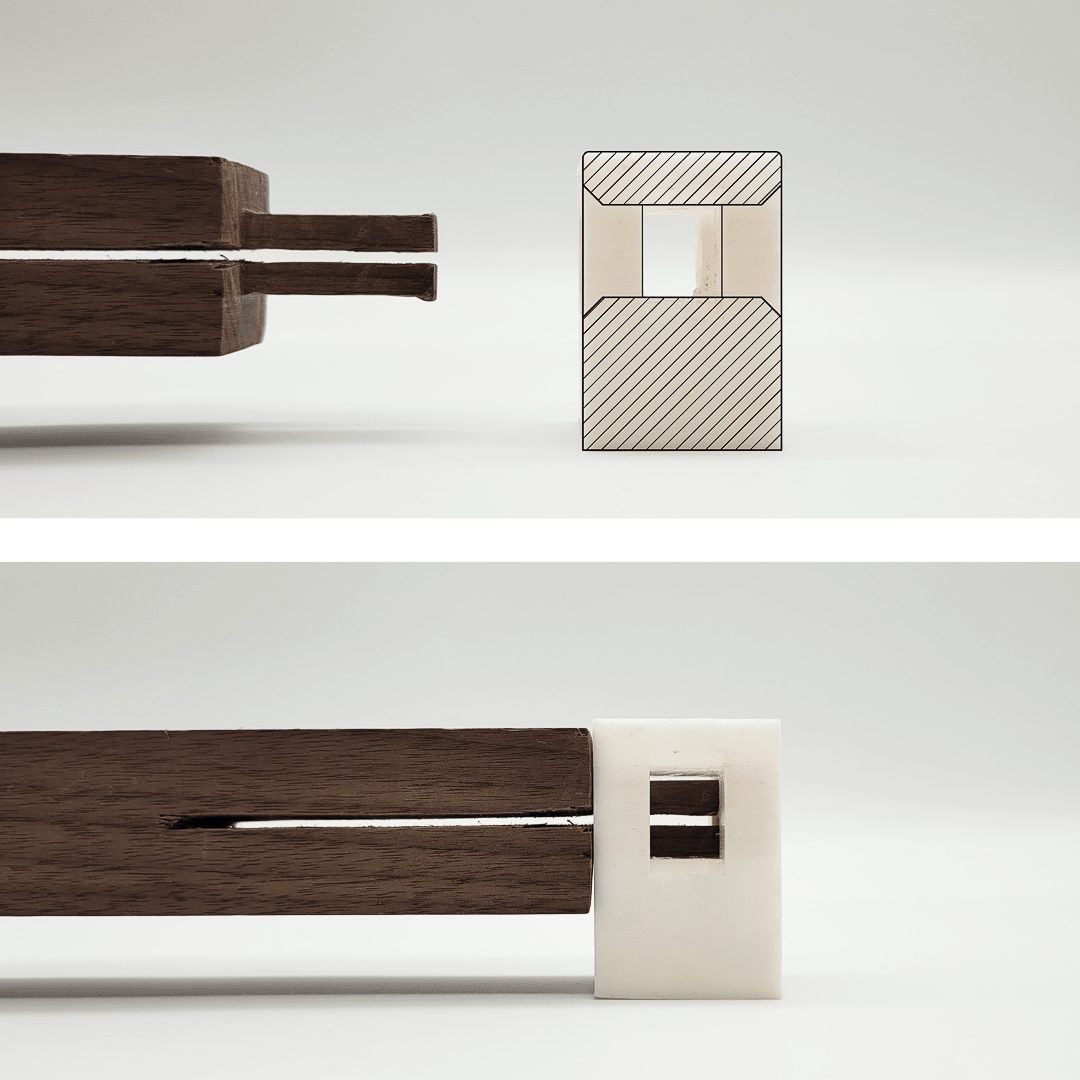
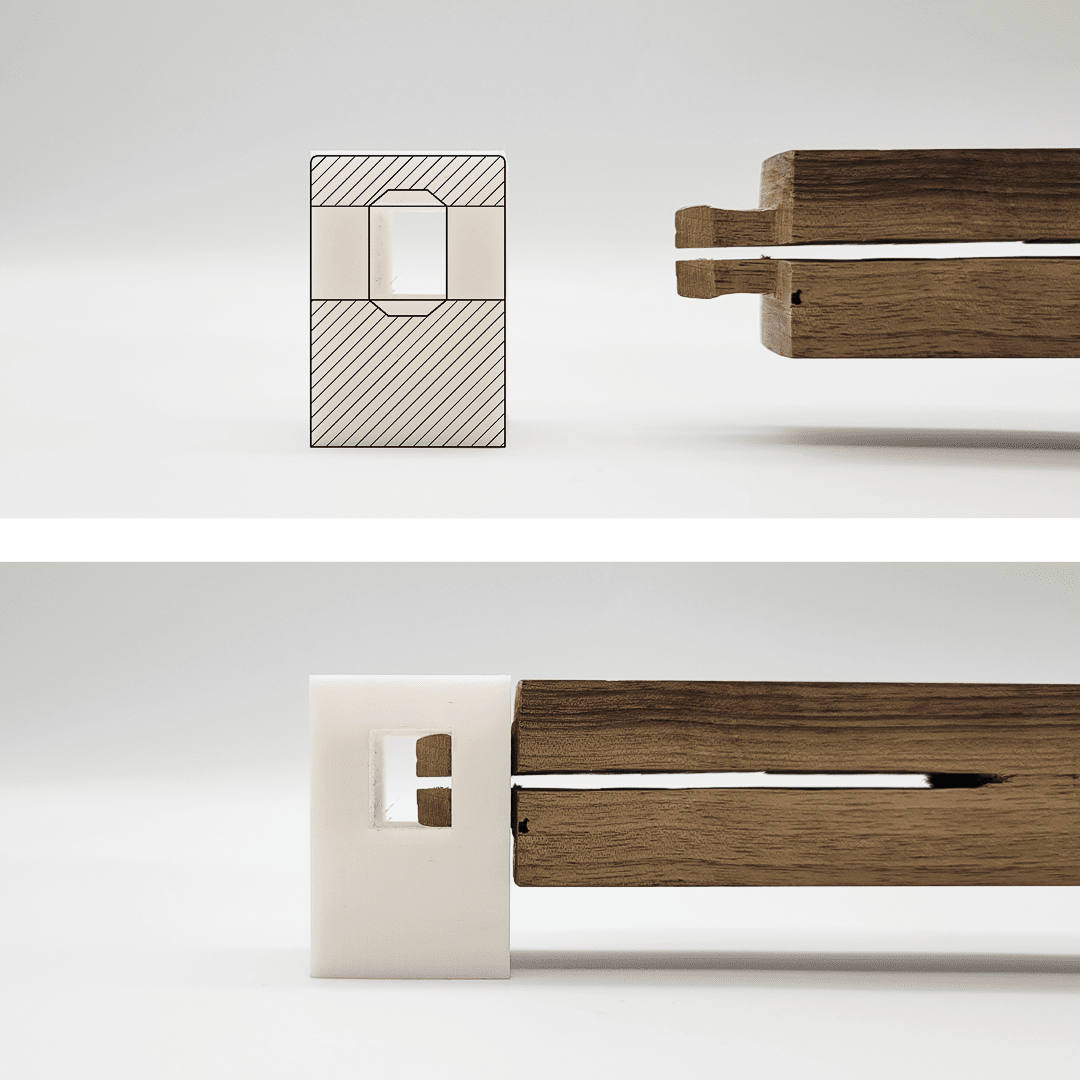
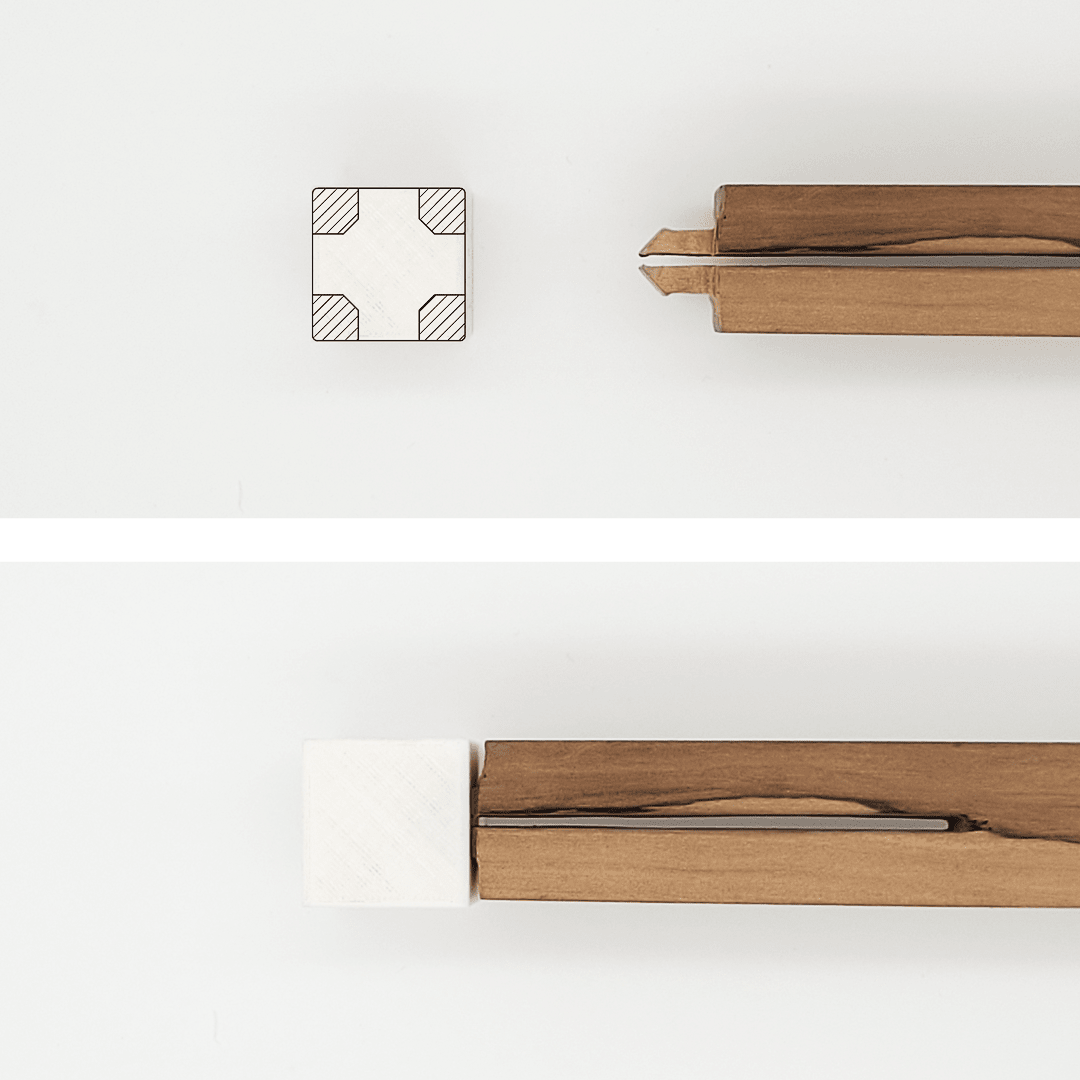
The seating panel
The sketches show the complete assembly of the plate and the plug-in connection for the plate and the frame, as I imagined them. As for the frame, most of the materials used for the seating panel are planned to be from wood as well.
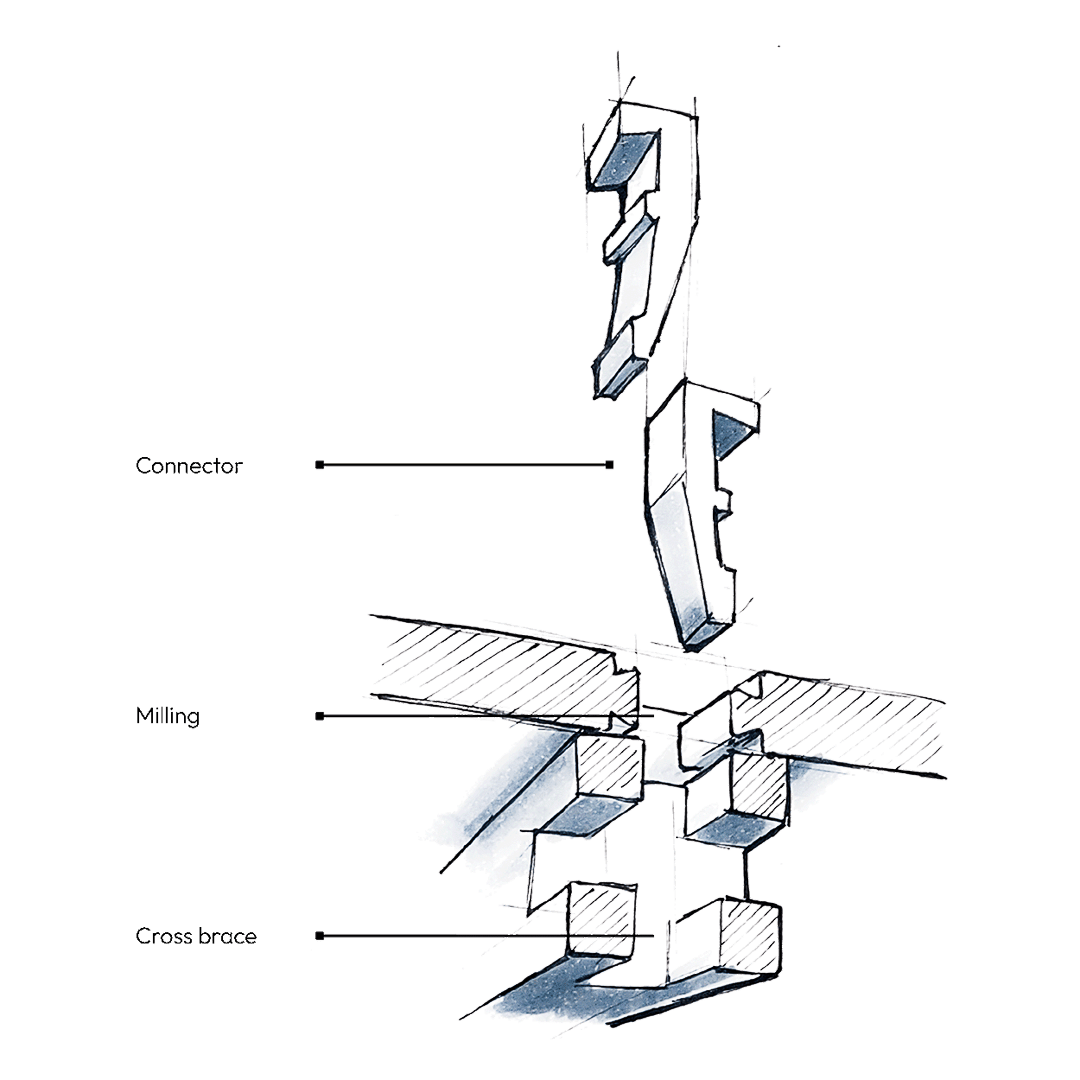
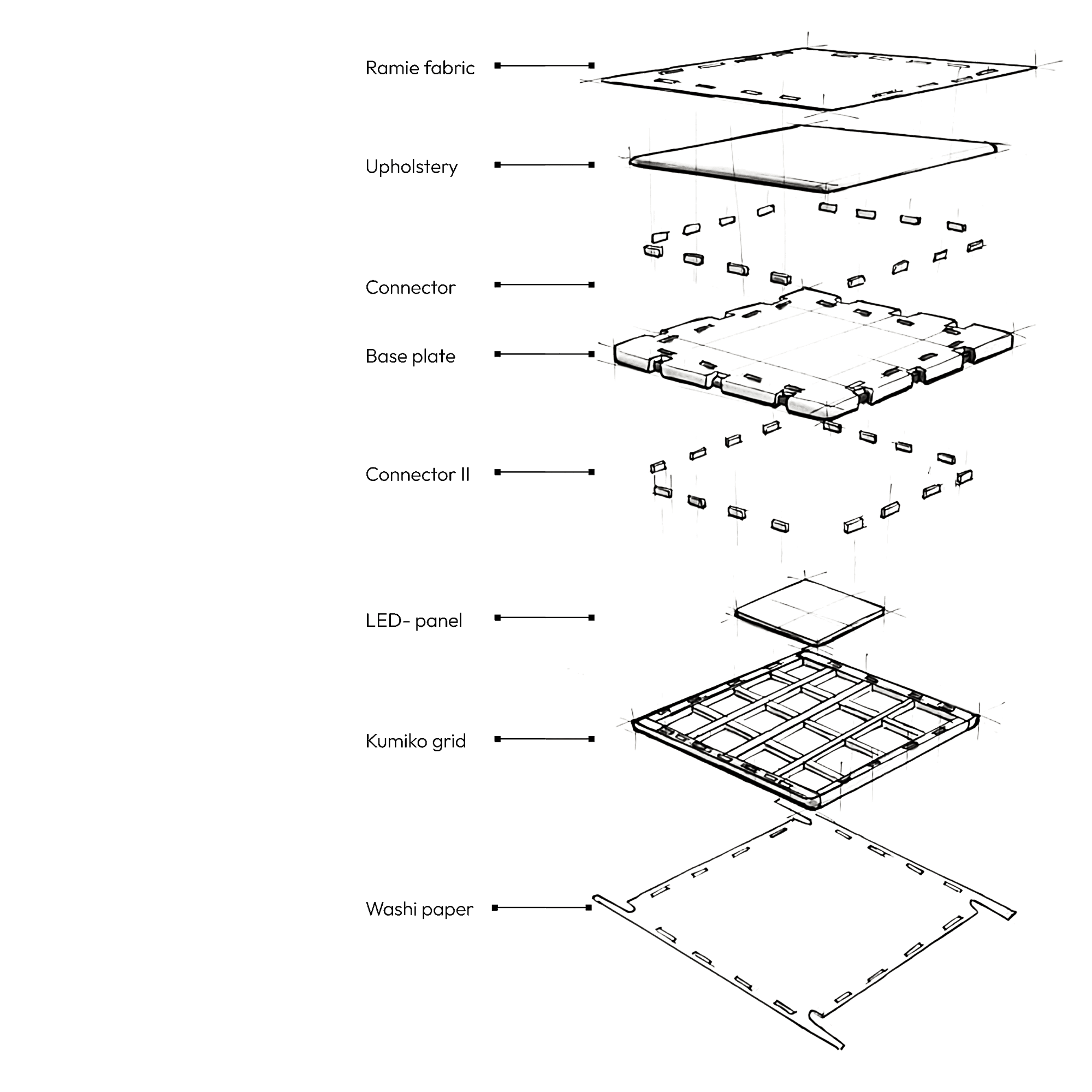
Connector prototypes
The prototypes for the connectors were 3D printed, for the same reason I printed the prototypes for the square milled holes of the frame. These connections are also to be considered more conventional, which made 3D printing seem like a good choice.
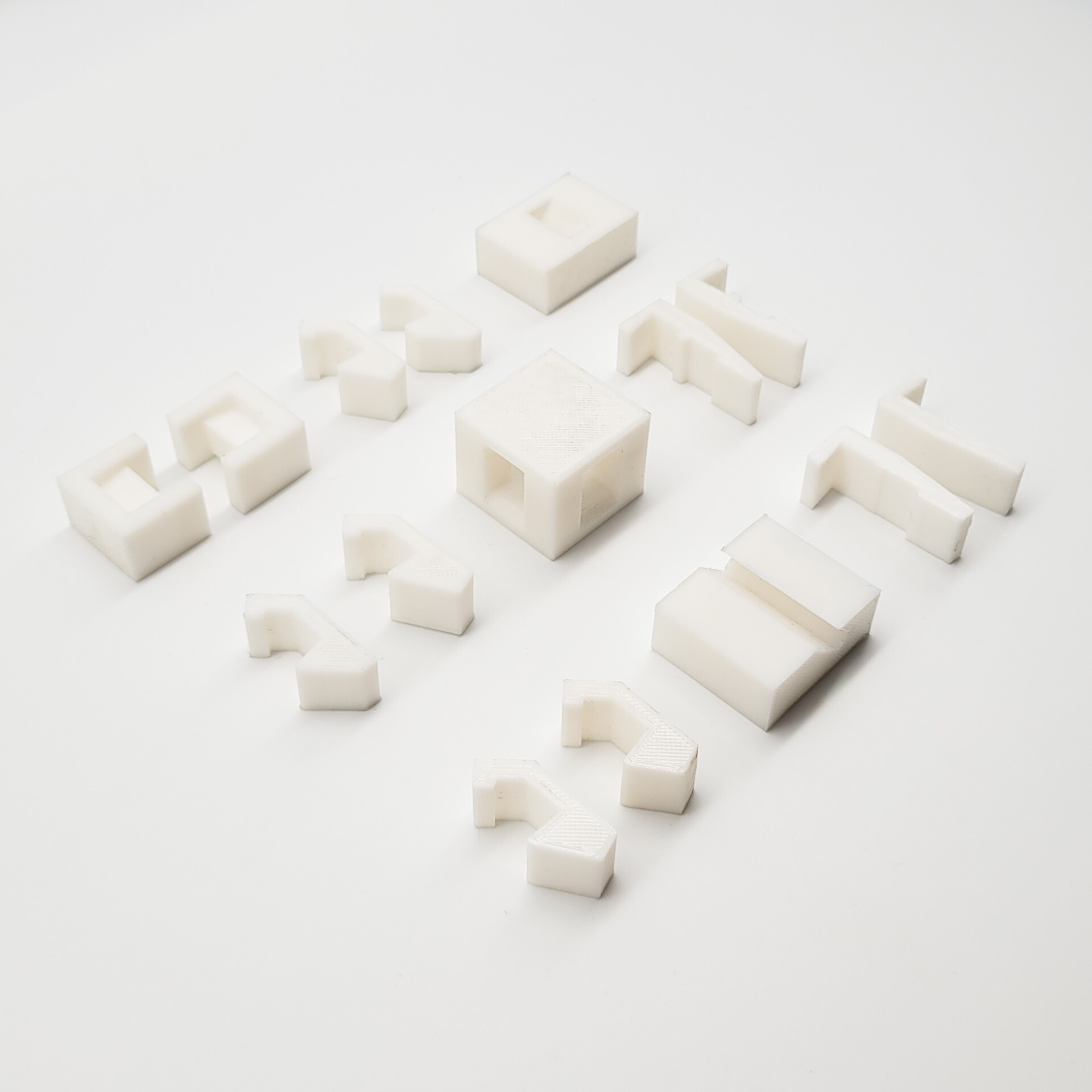
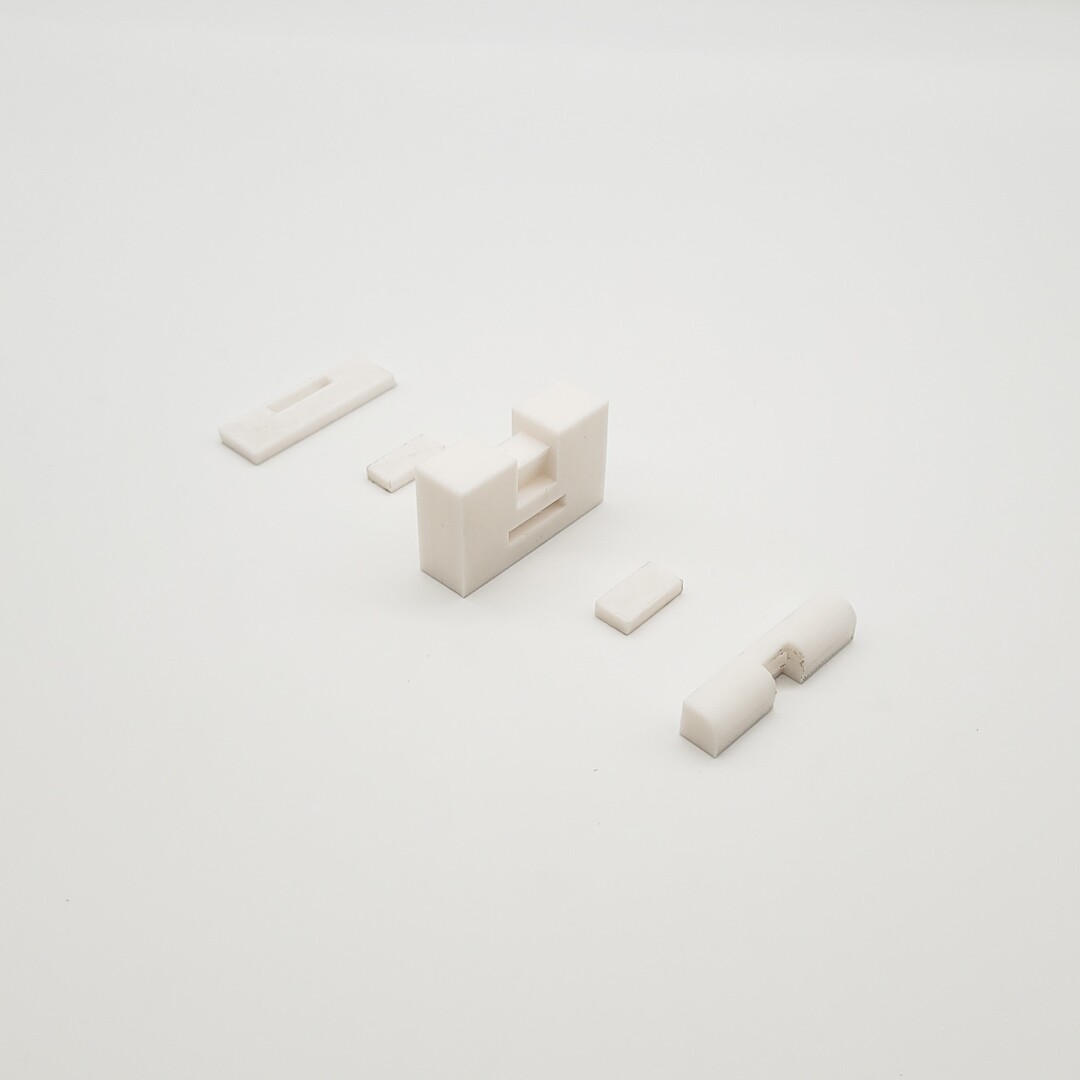
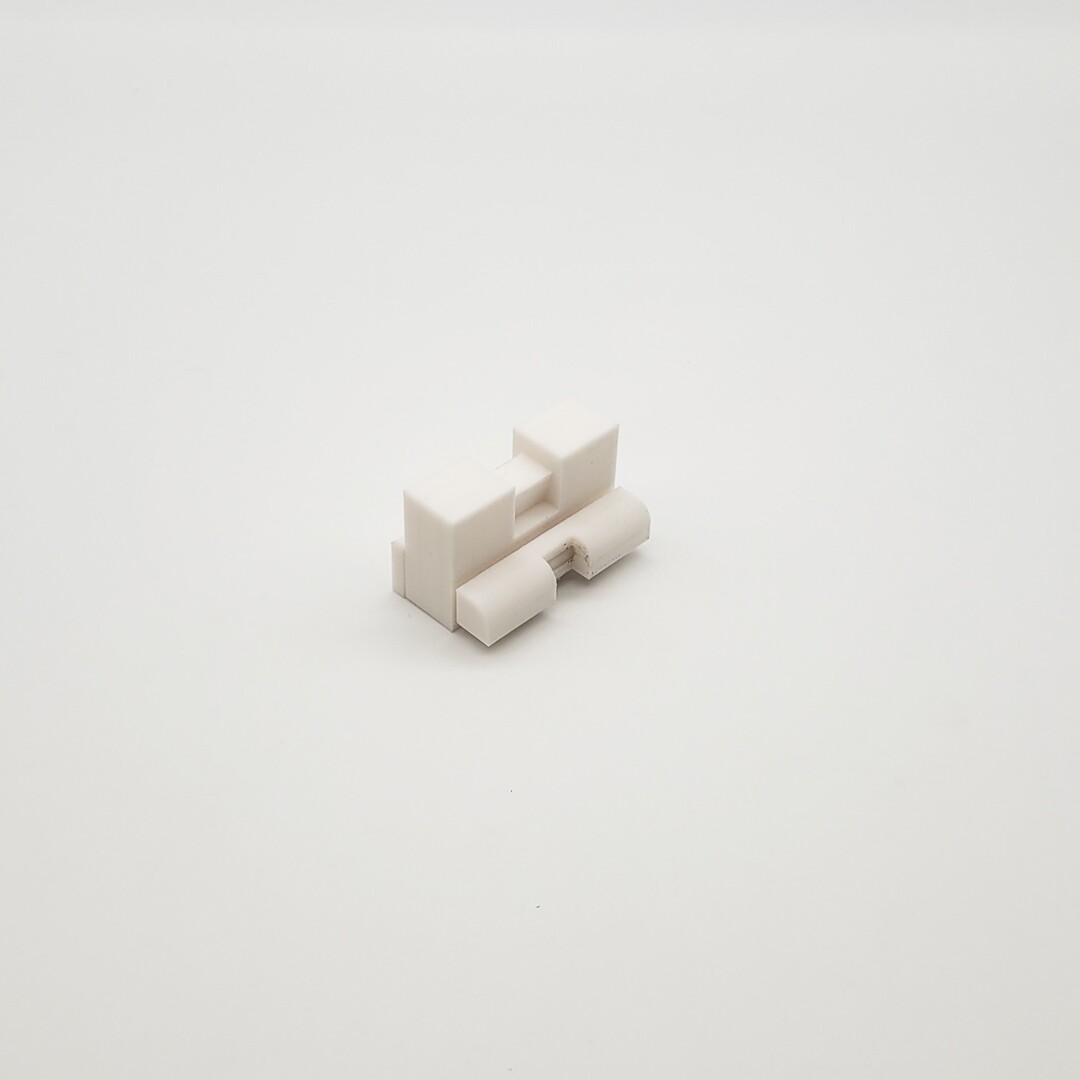
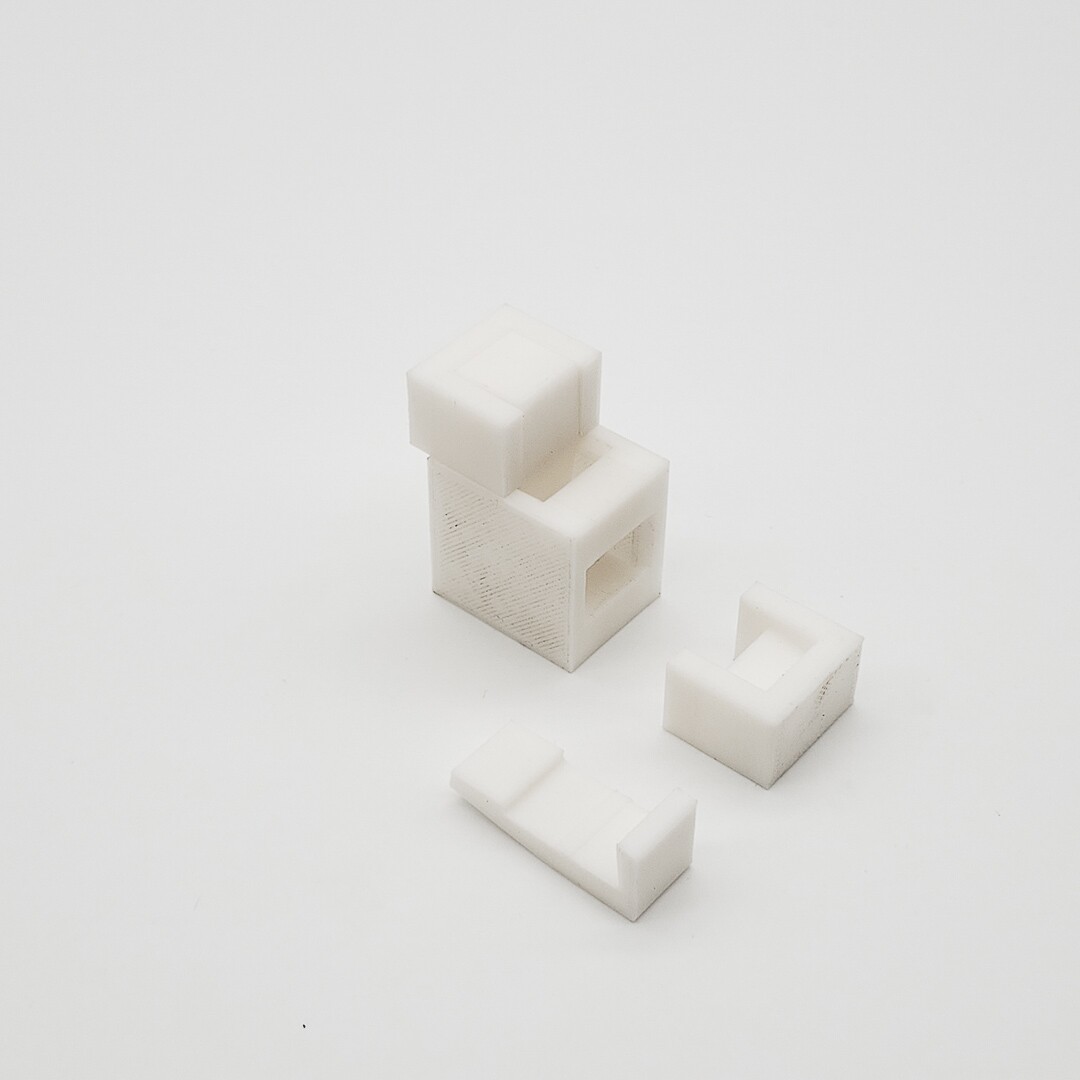
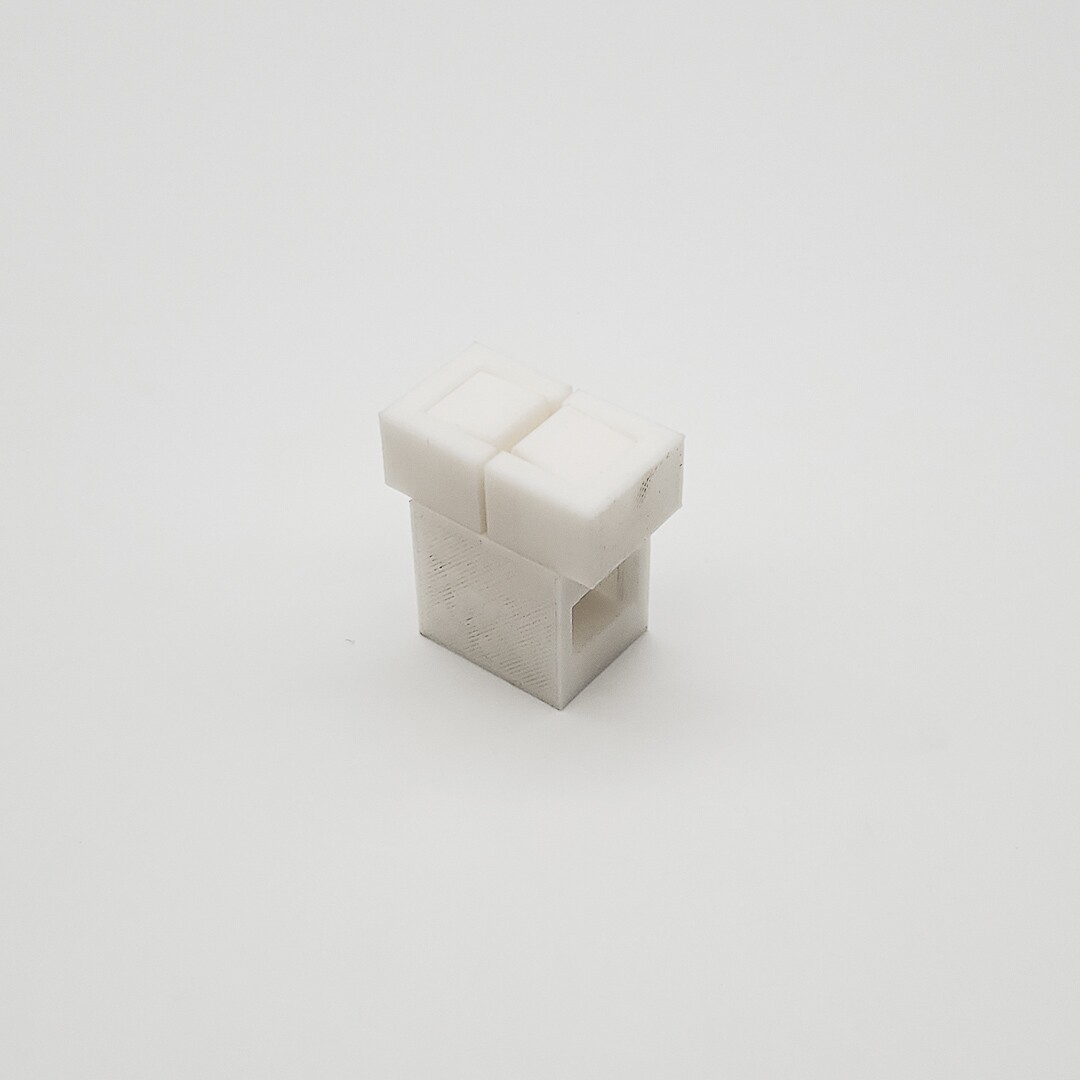
The final design
The sketches show the final shape of the most basic piece of furniture that I wanted to build with the modular system.
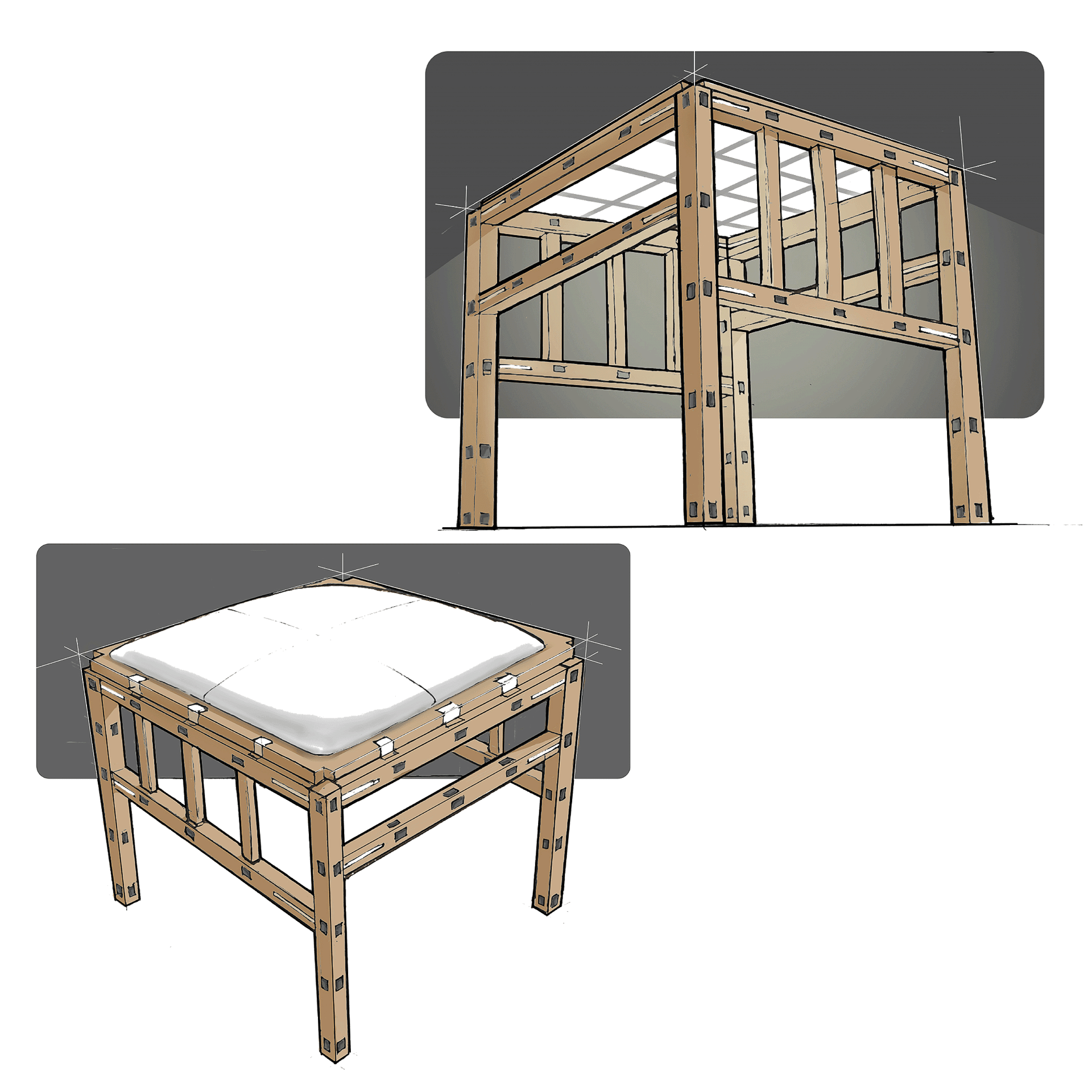
3D model
I used Fusion 360 for modeling the parts and Keyshot for rendering some of the pictures. The pictures below show all the necessary parts for the piece of furniture, including a USB cable for the light underneath the seating panel and some tools for the easy assembly of the design. The animation of the product also shows the packaging I designed for all these pieces.
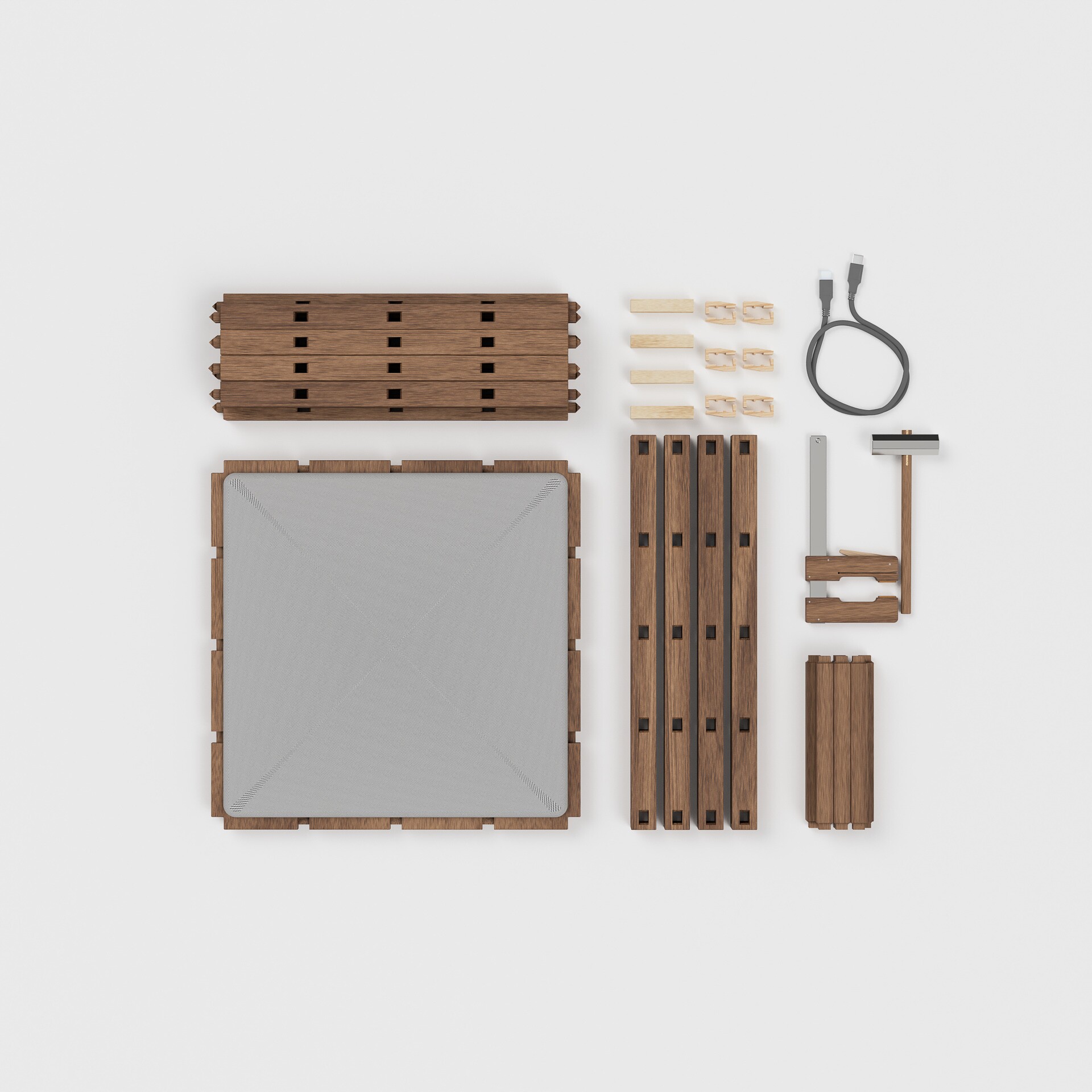
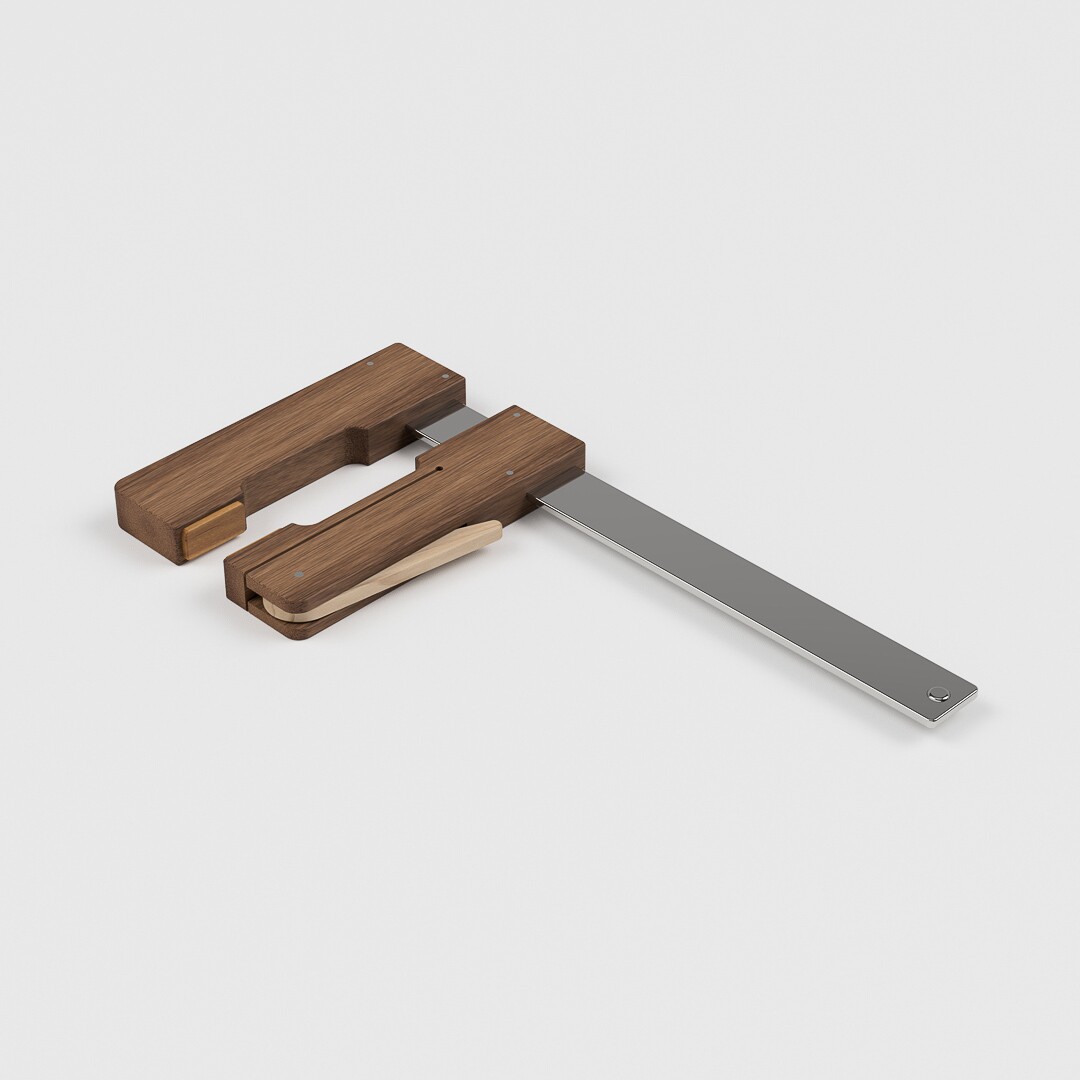
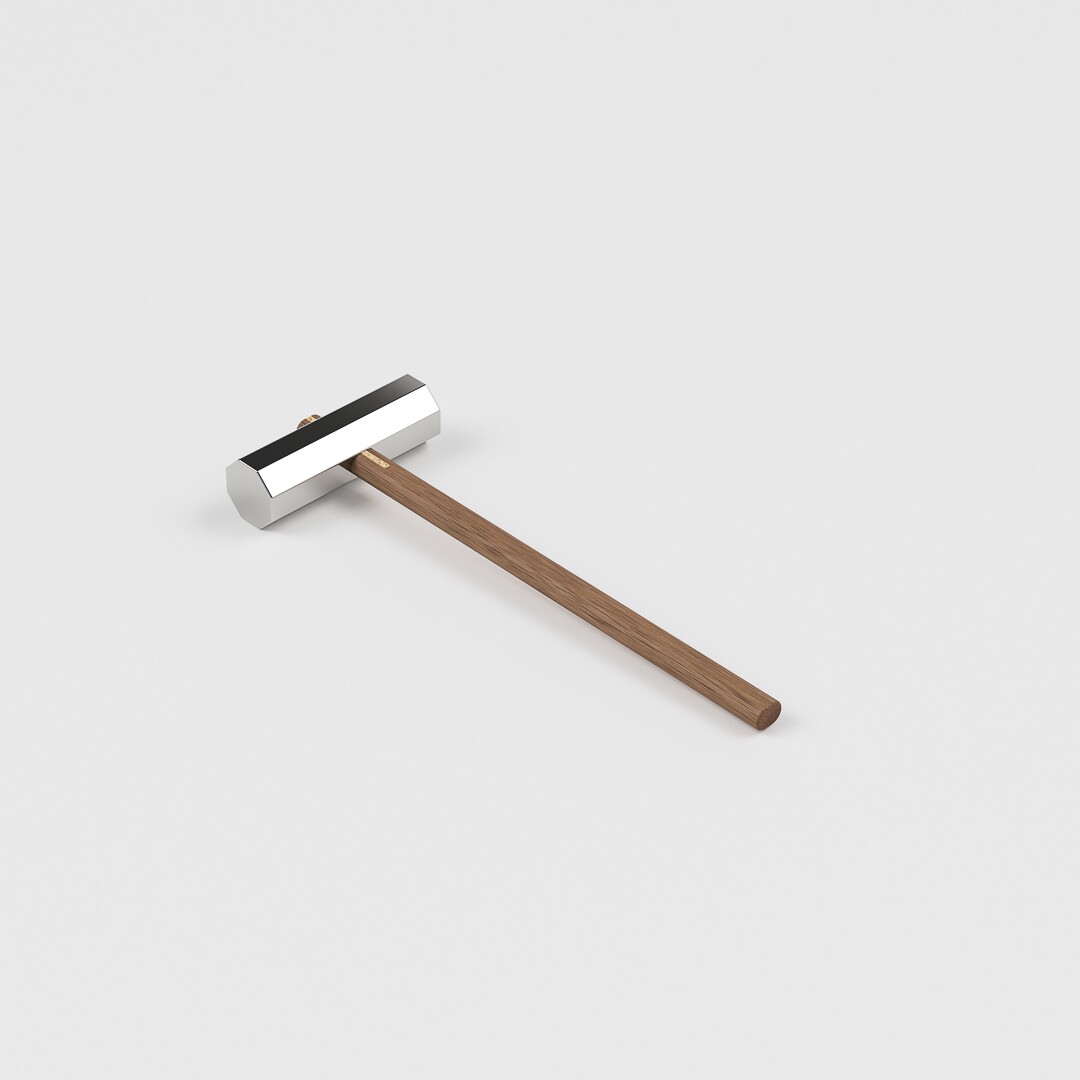
Assembly of the frame
The first pictures show the assembly of the frame with the tools provided in the "set" I designed. The second row shows the assembly of the frame and the seating panel.
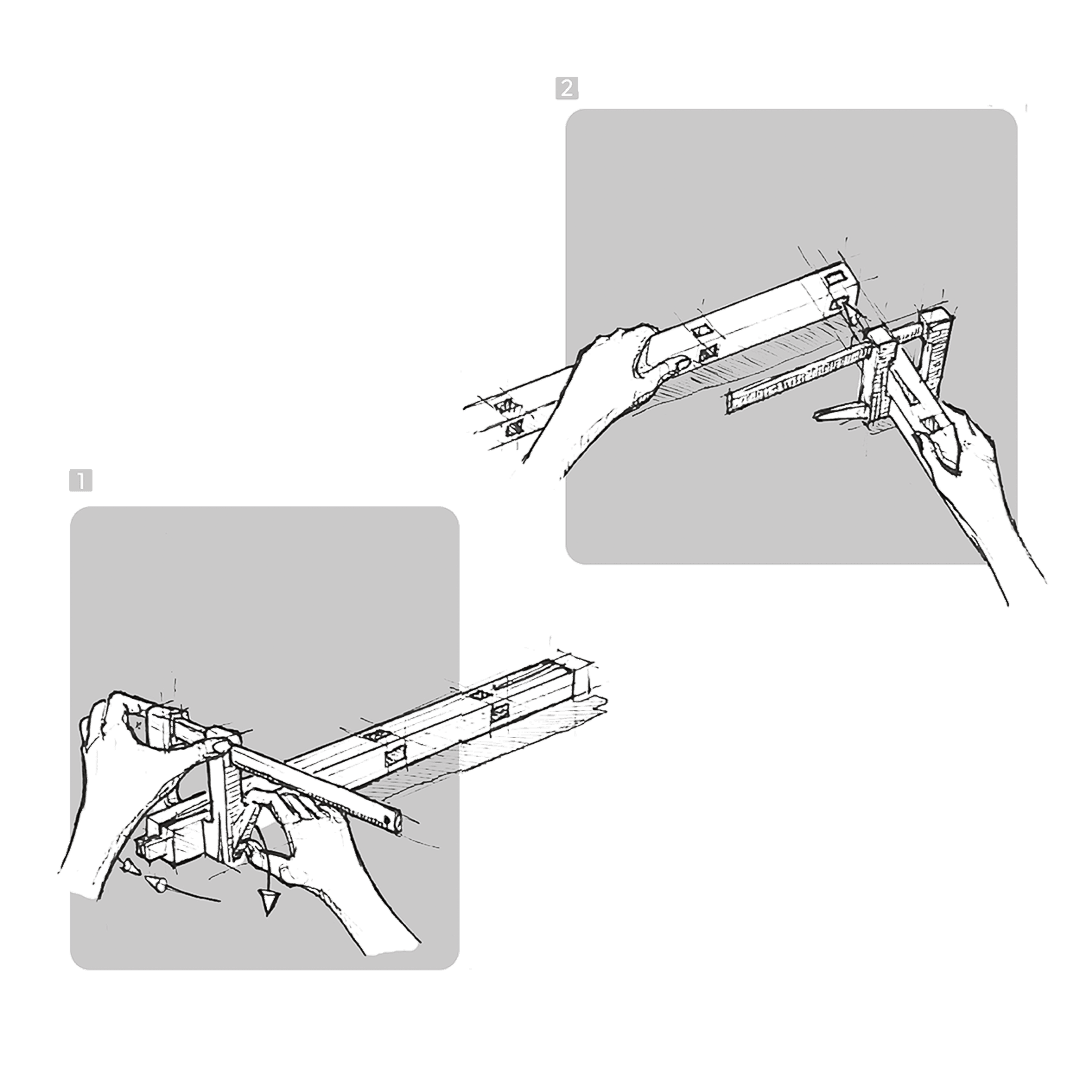
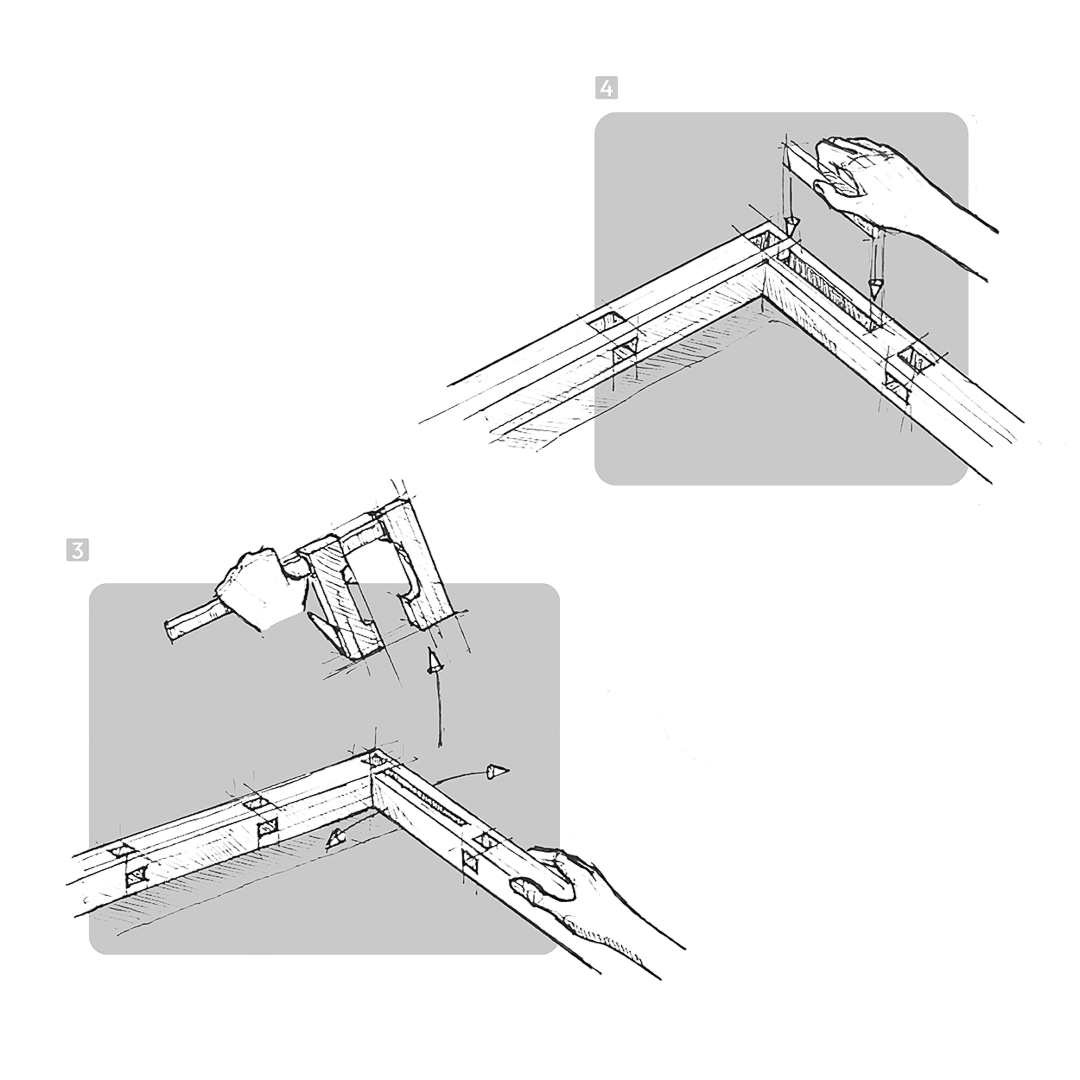
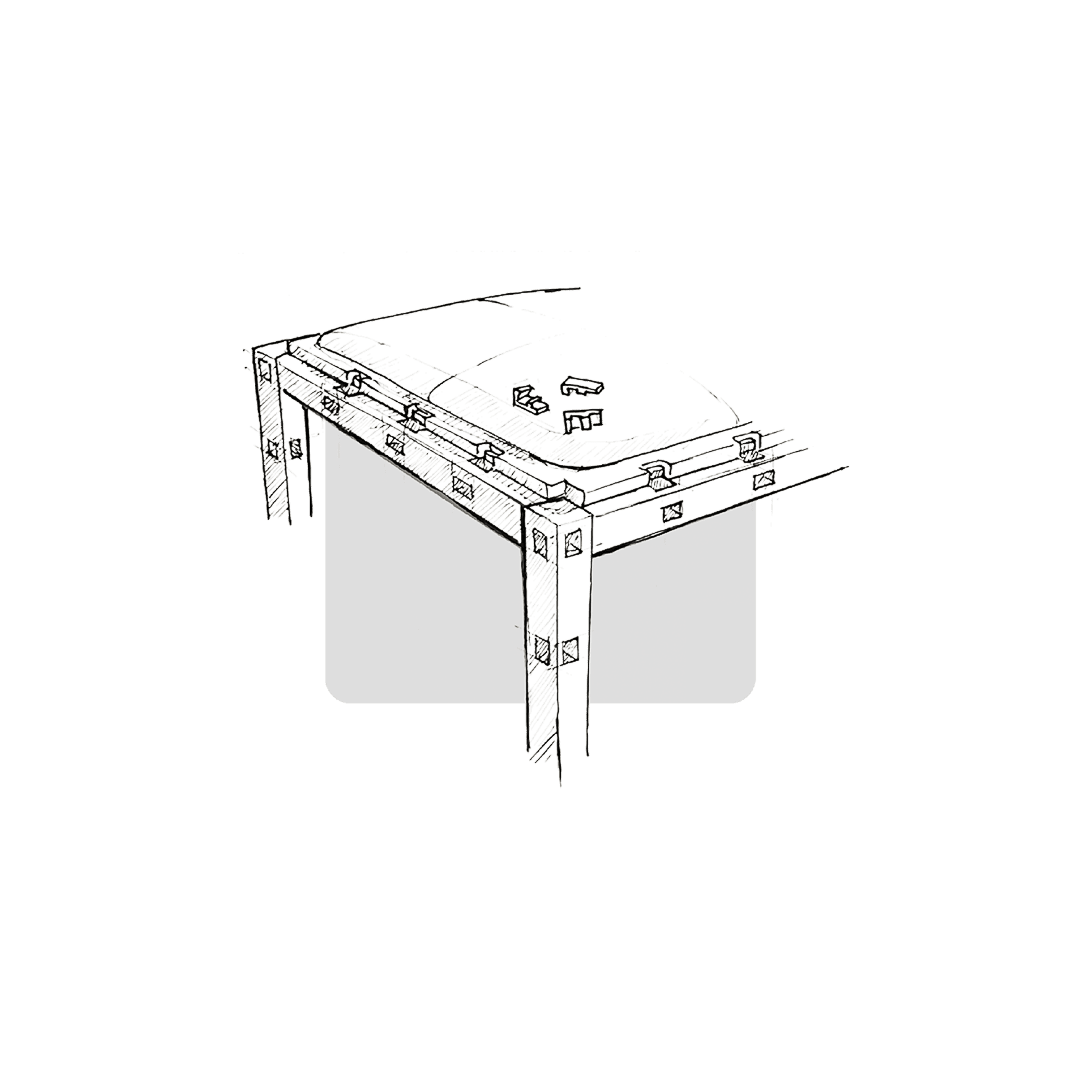
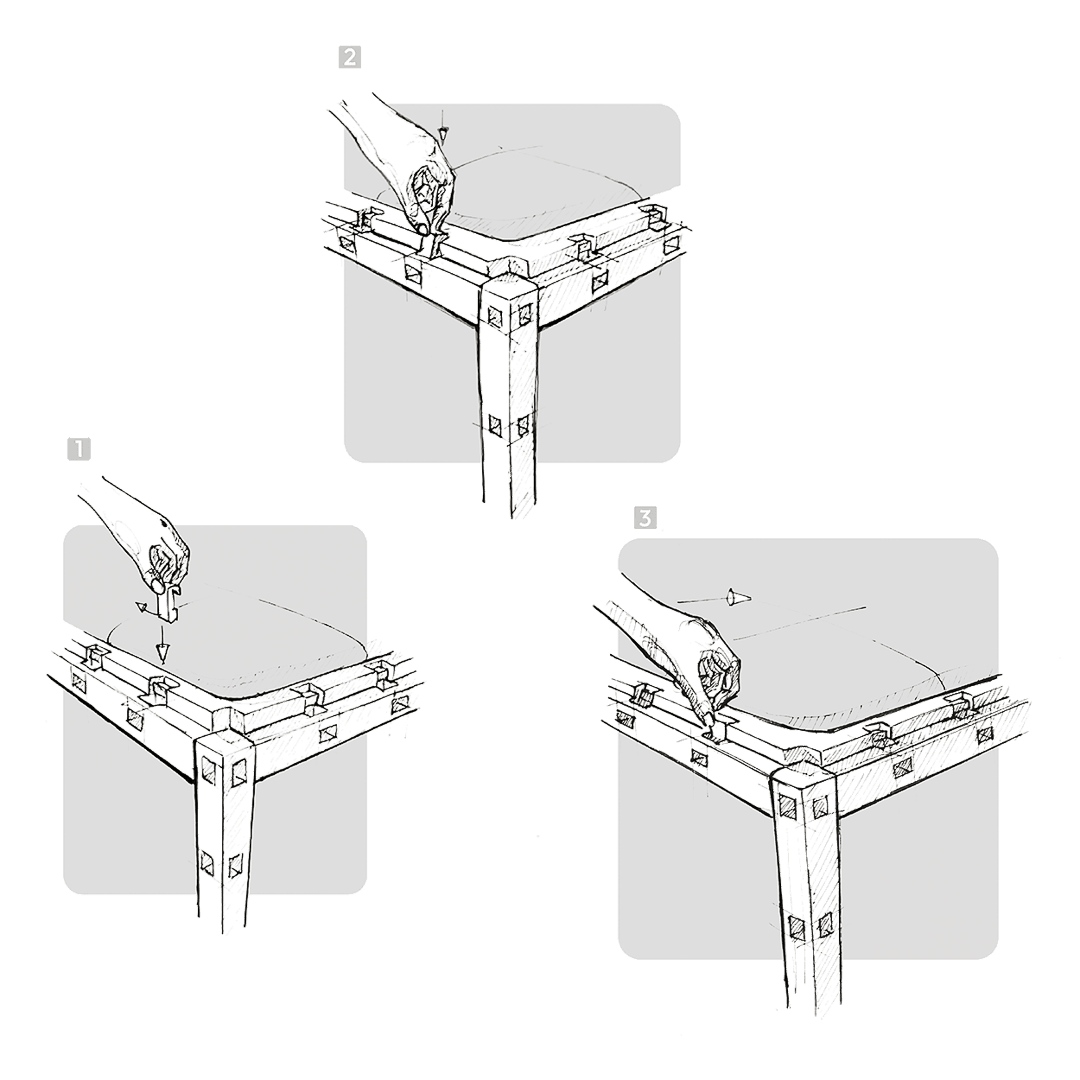
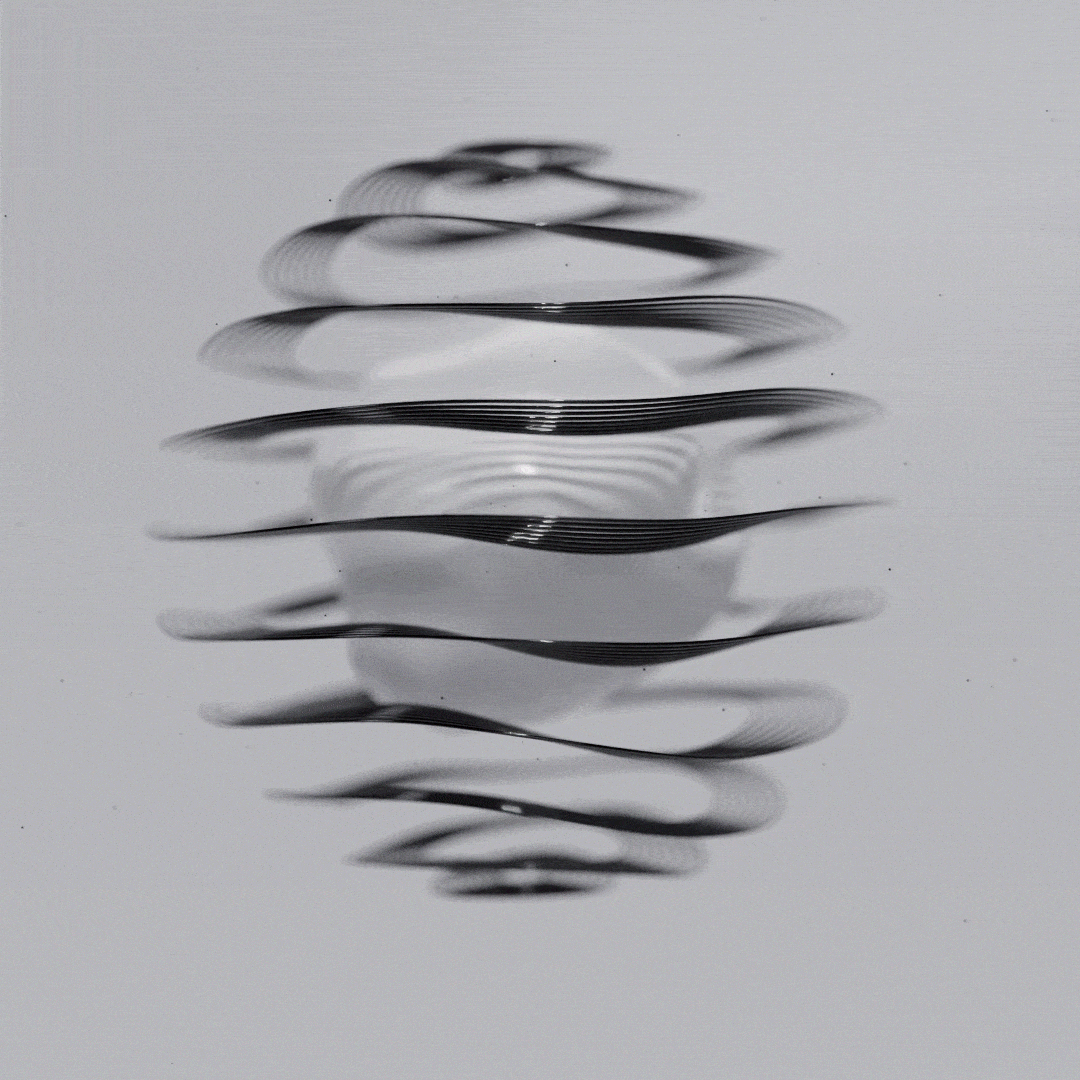
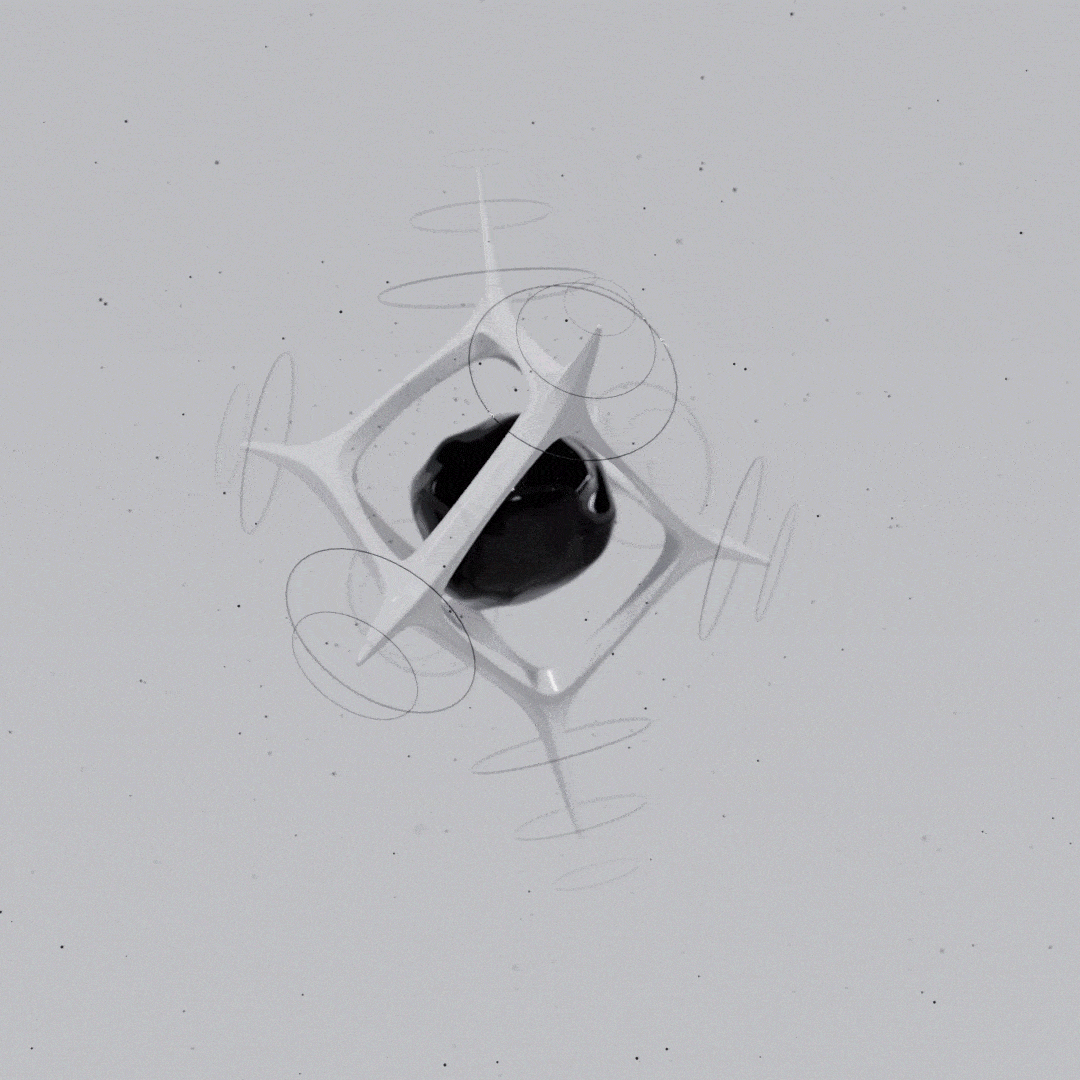
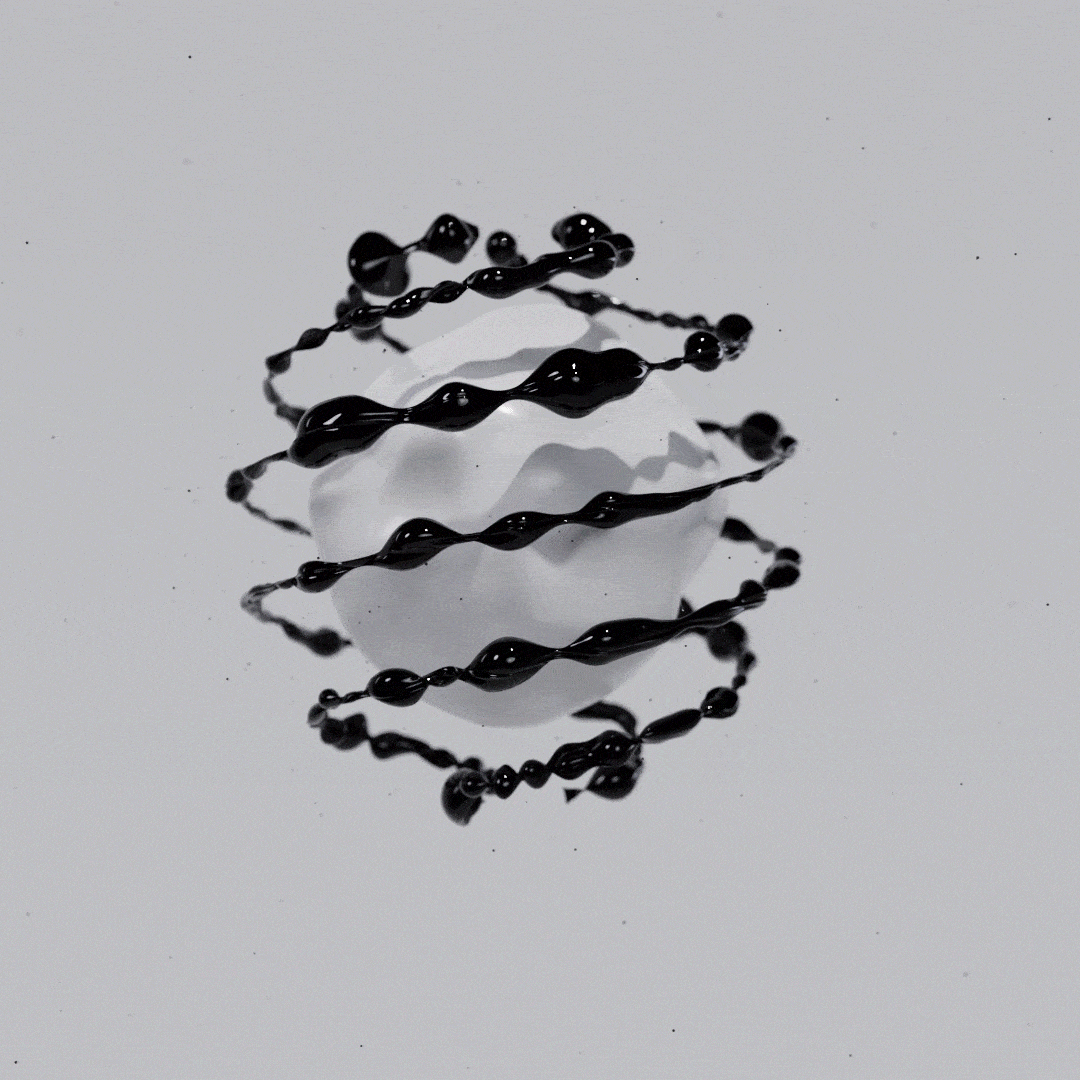
INK
INK is a private project I started a while ago, to get my hands on Blender's geometry node system. Other aspects are composition and working with only black and white. Furthermore, I use them to get more familiar with effectors and physics- simulations, just as i used them for the particles. The number of animations will be continuously updated as I create them in my free time, between other, bigger projects.
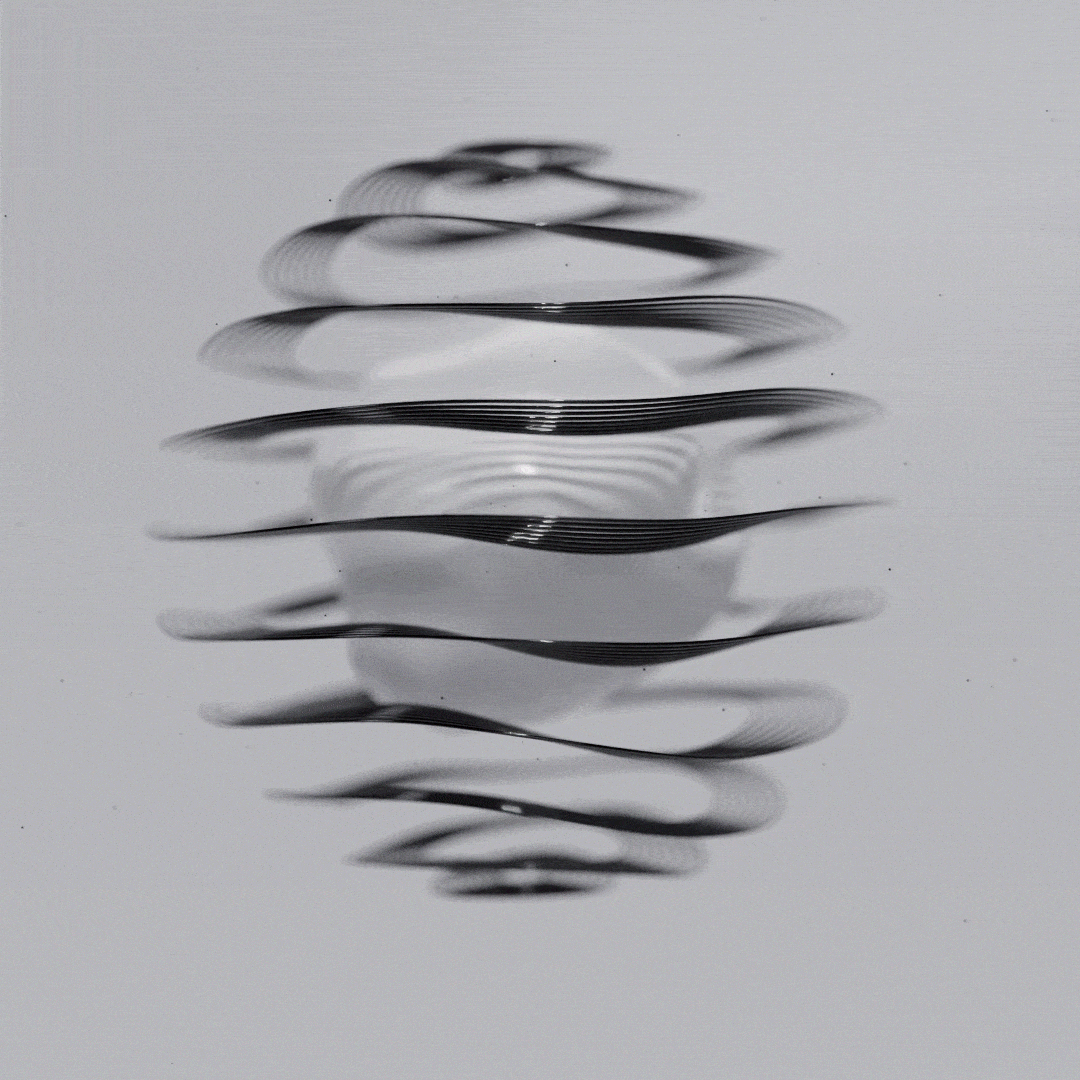
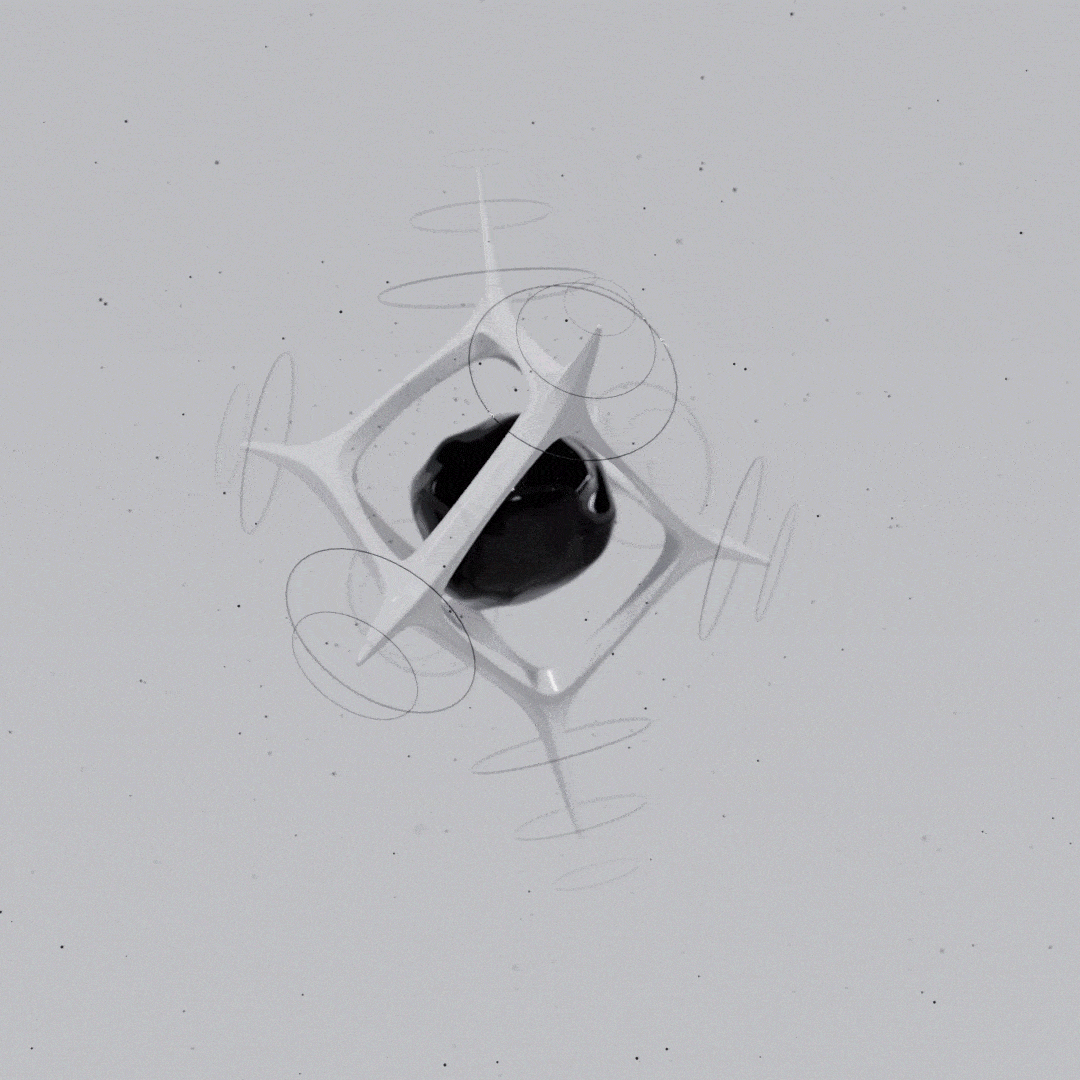
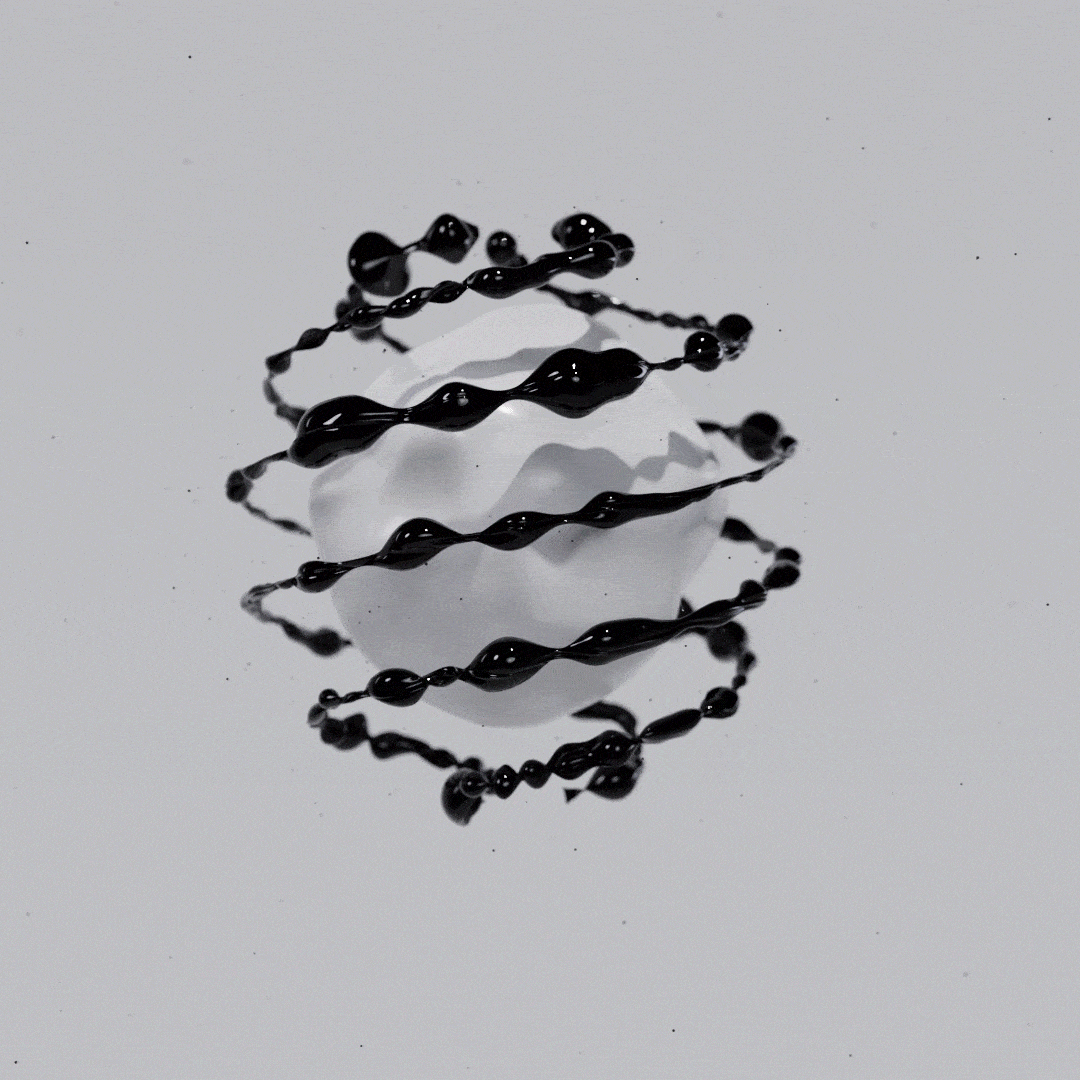
INK
INK is a private project I started a while ago, to get my hands on Blender's geometry node system. Other aspects are composition and working with only black and white. Furthermore, I use them to get more familiar with effectors and physics- simulations, just as i used them for the particles. The number of animations will be continuously updated as I create them in my free time, between other, bigger projects.
.jpg)
 (7).jpg)
Sketches
One of my private projects is an ongoing collection of designs for unconventional instruments, vehicles, and other objects. At the moment, it consists of around 26 sketches with a size between A3 and A0.
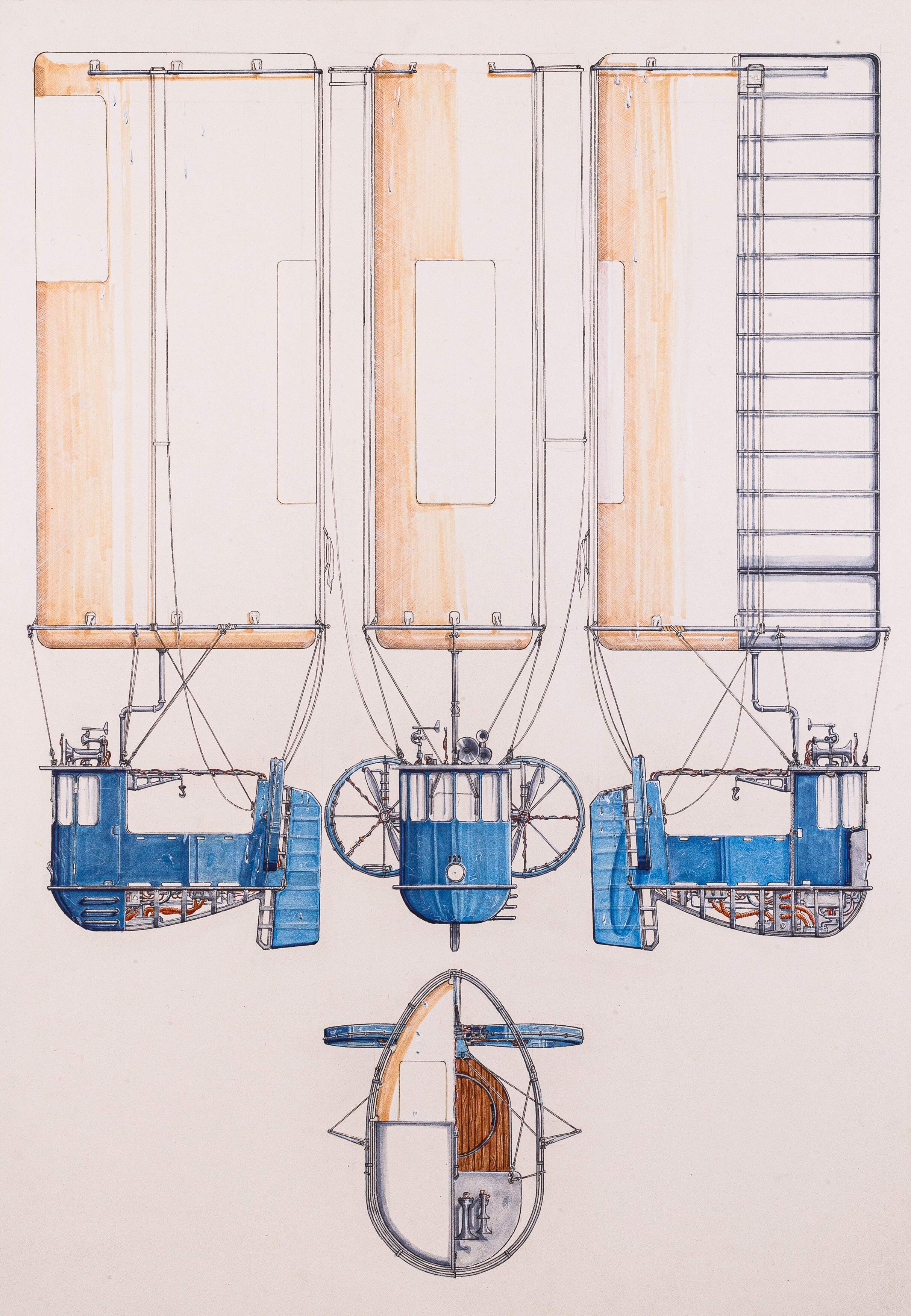
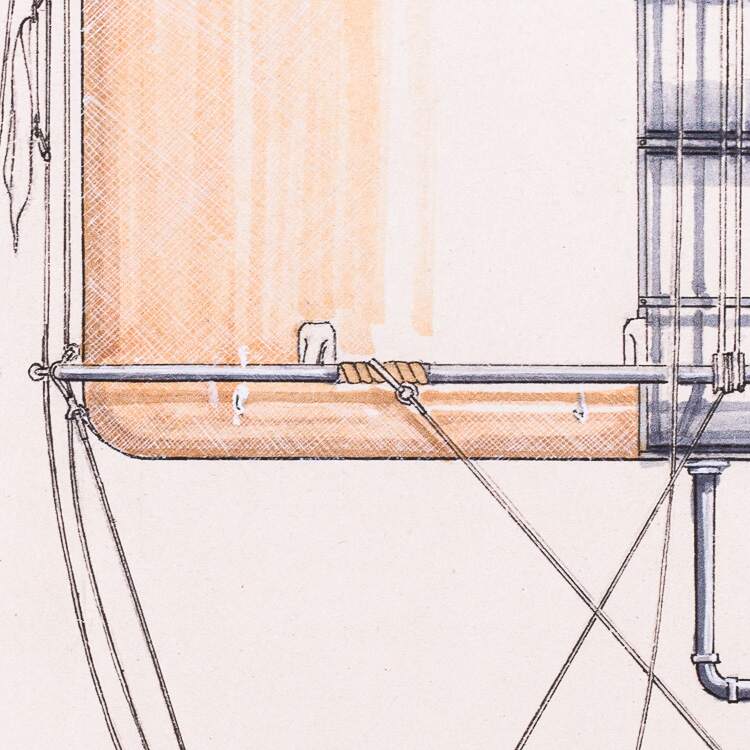
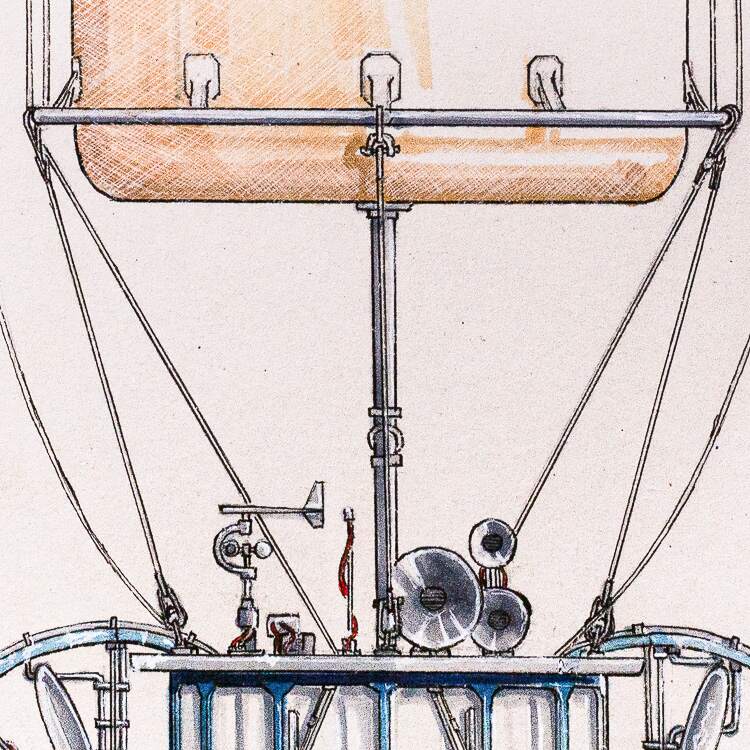
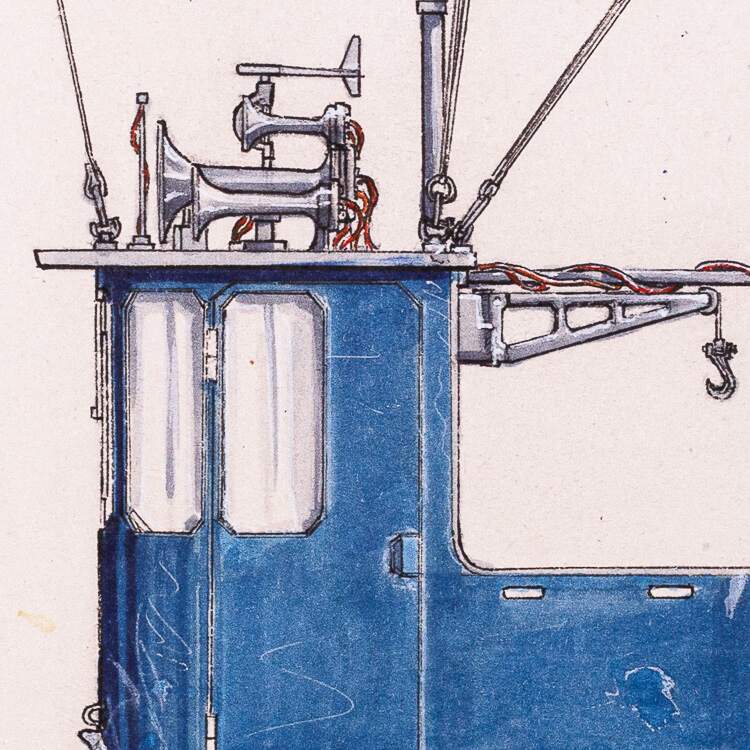
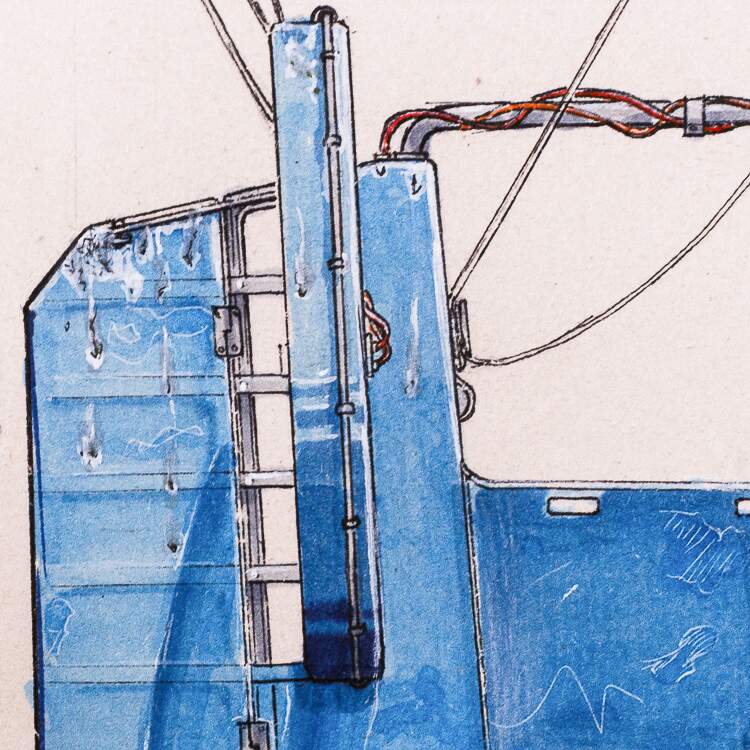
.jpg)
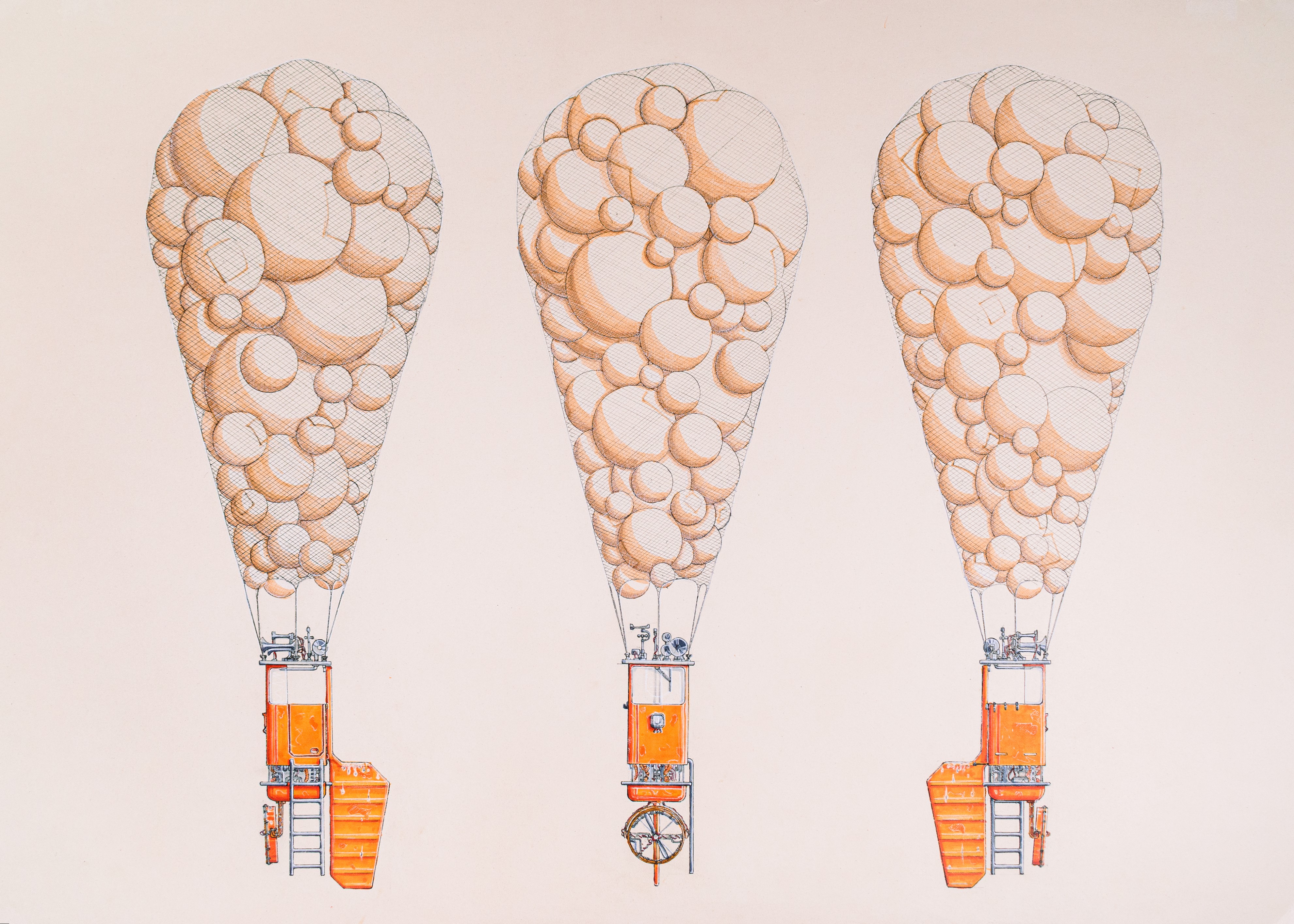
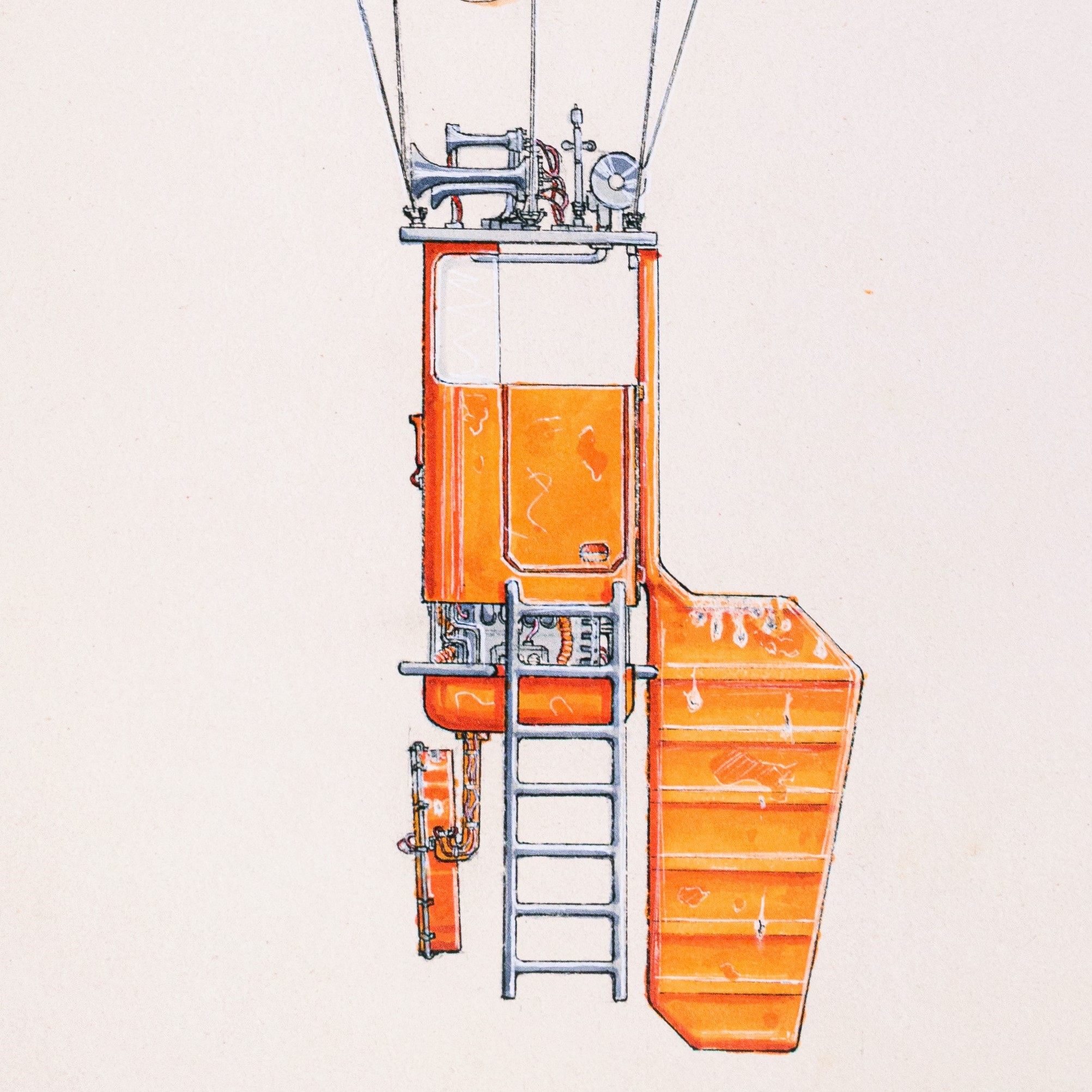
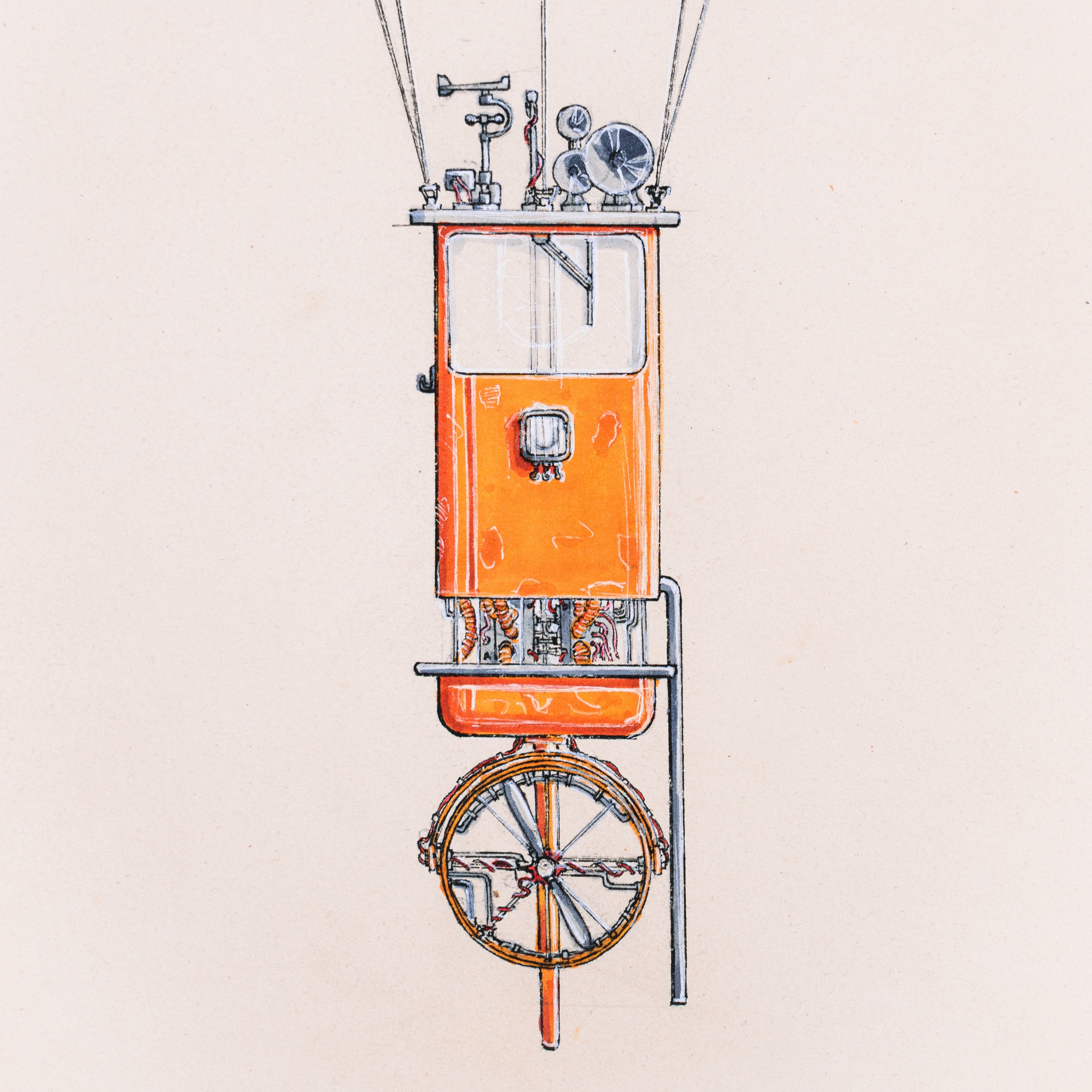
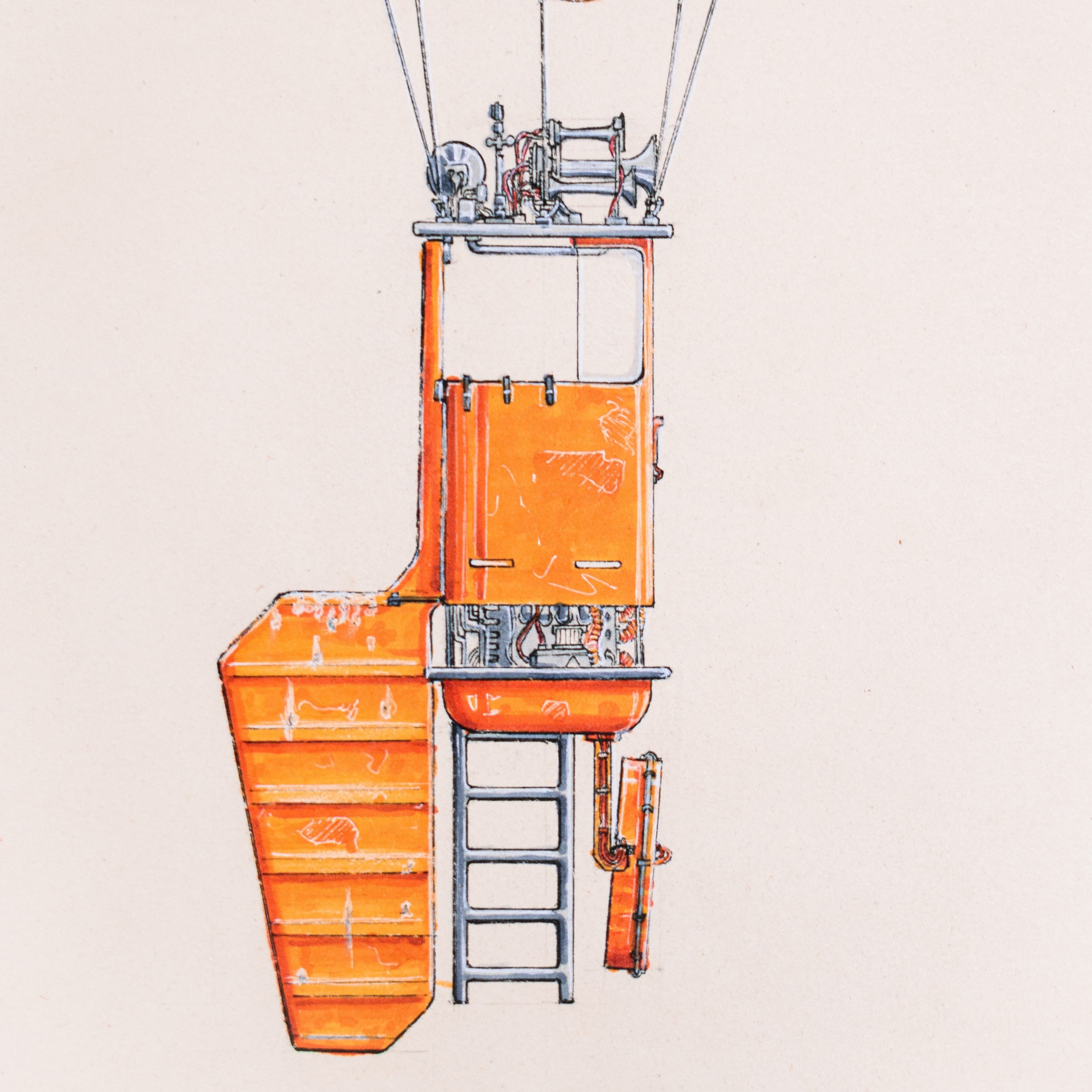
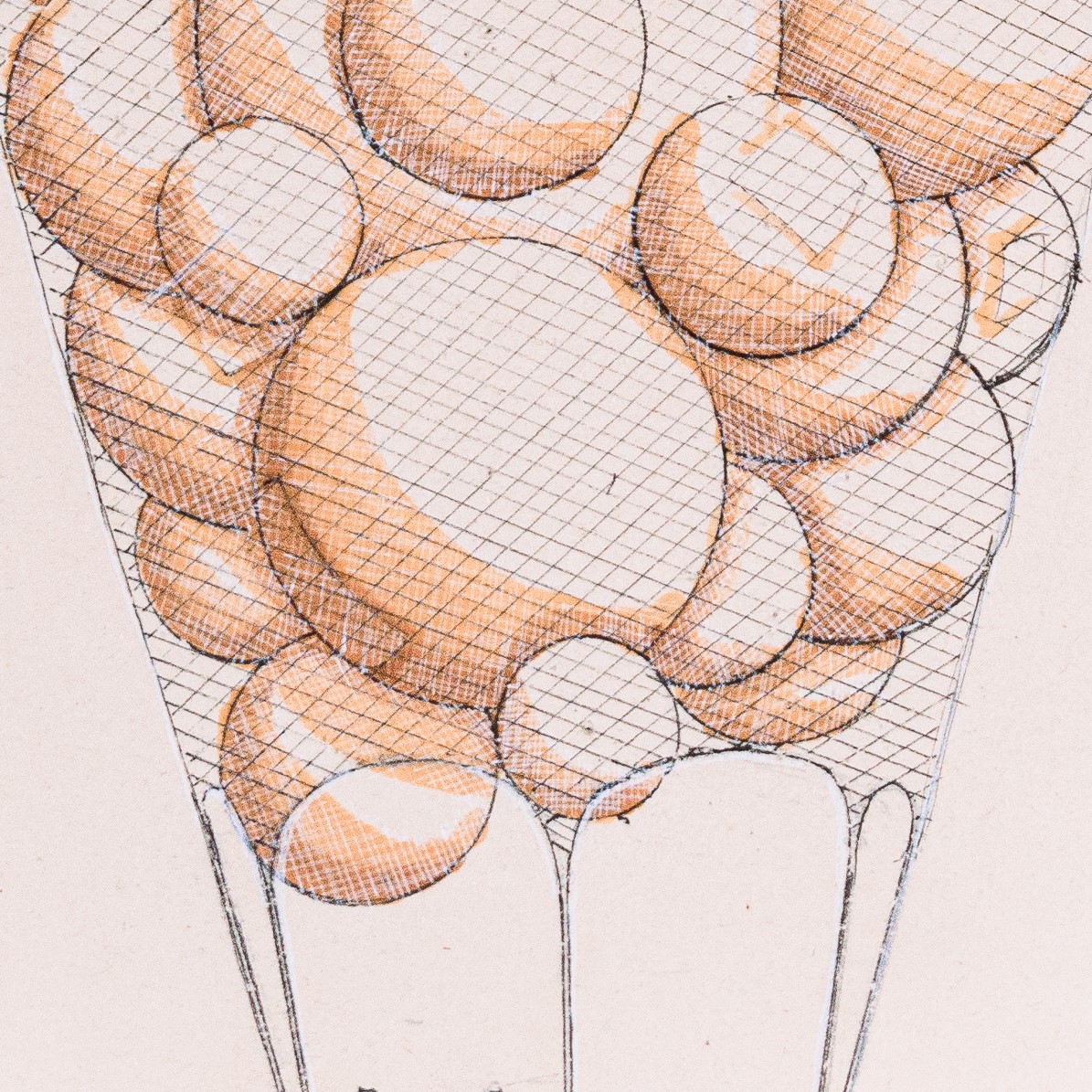
.jpg)
.jpg)
cropped.jpg)
.jpg)
.jpg)
.jpg)
.jpg)
2.jpg)
 (14).jpg)
 (6).jpg)
 (8).jpg)
 (2).jpg)
 (3).jpg)
 (2).jpg)
.jpg)
.jpg)
.jpg)
.jpg)
.jpg)
.jpg)
.jpg)
.jpg)
.jpg)
.jpg)
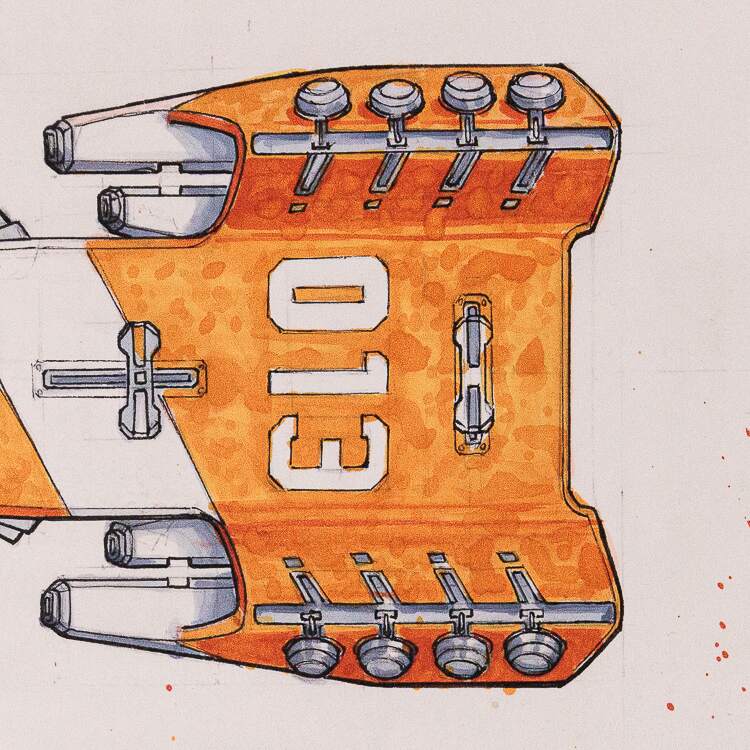
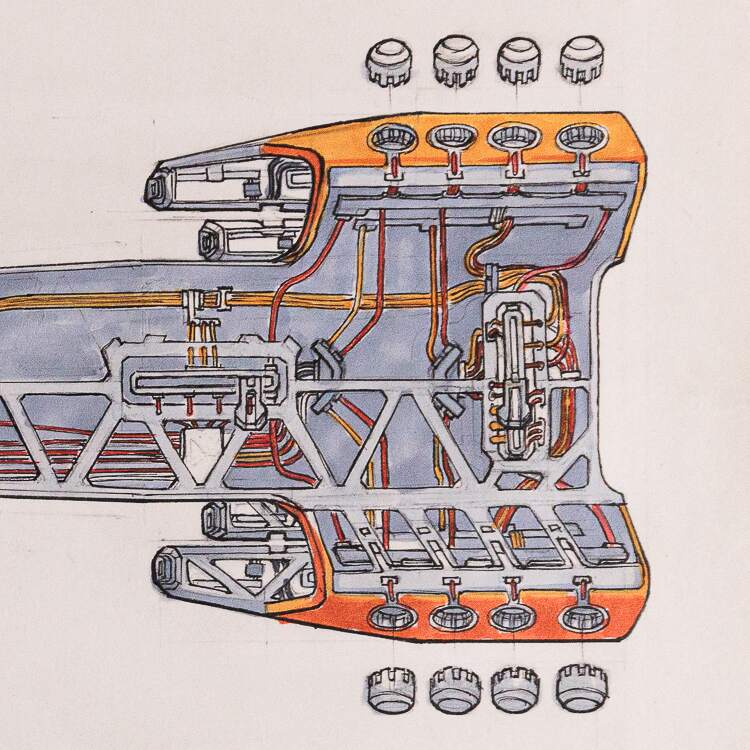
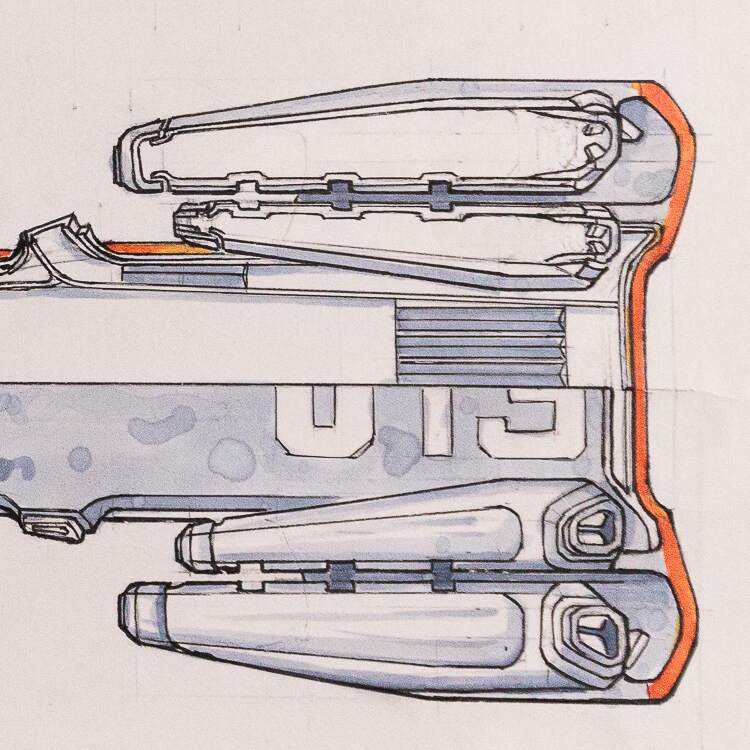
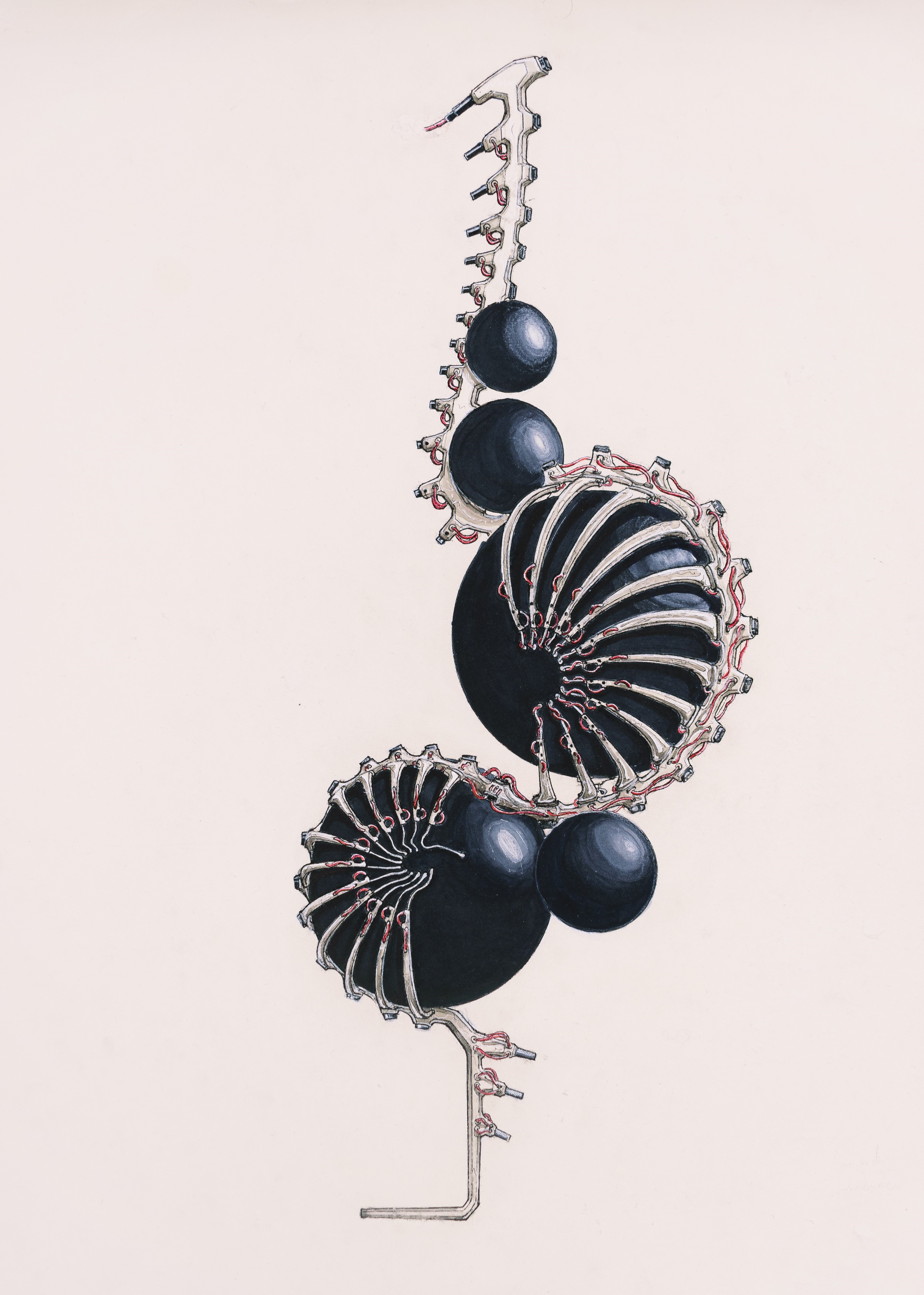
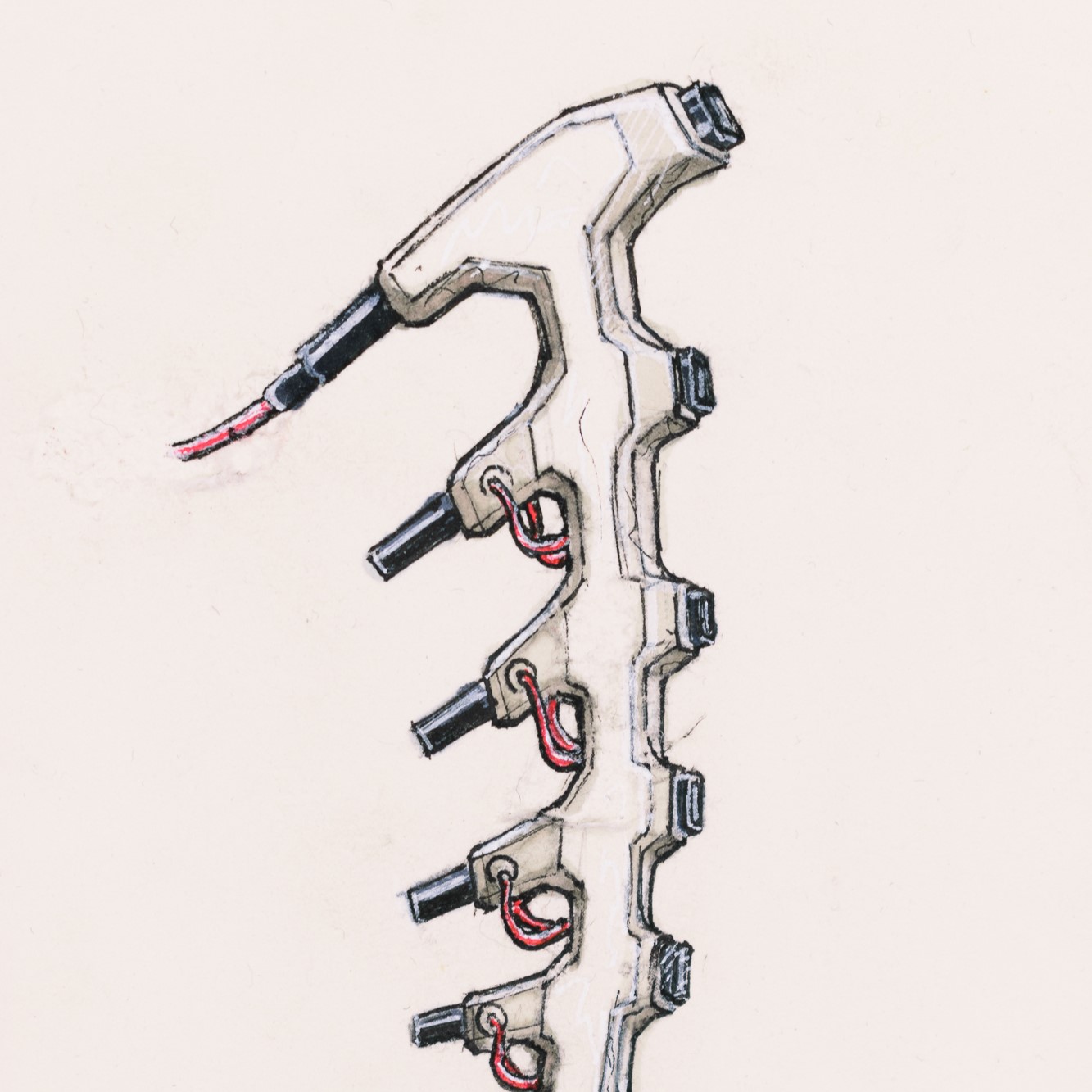
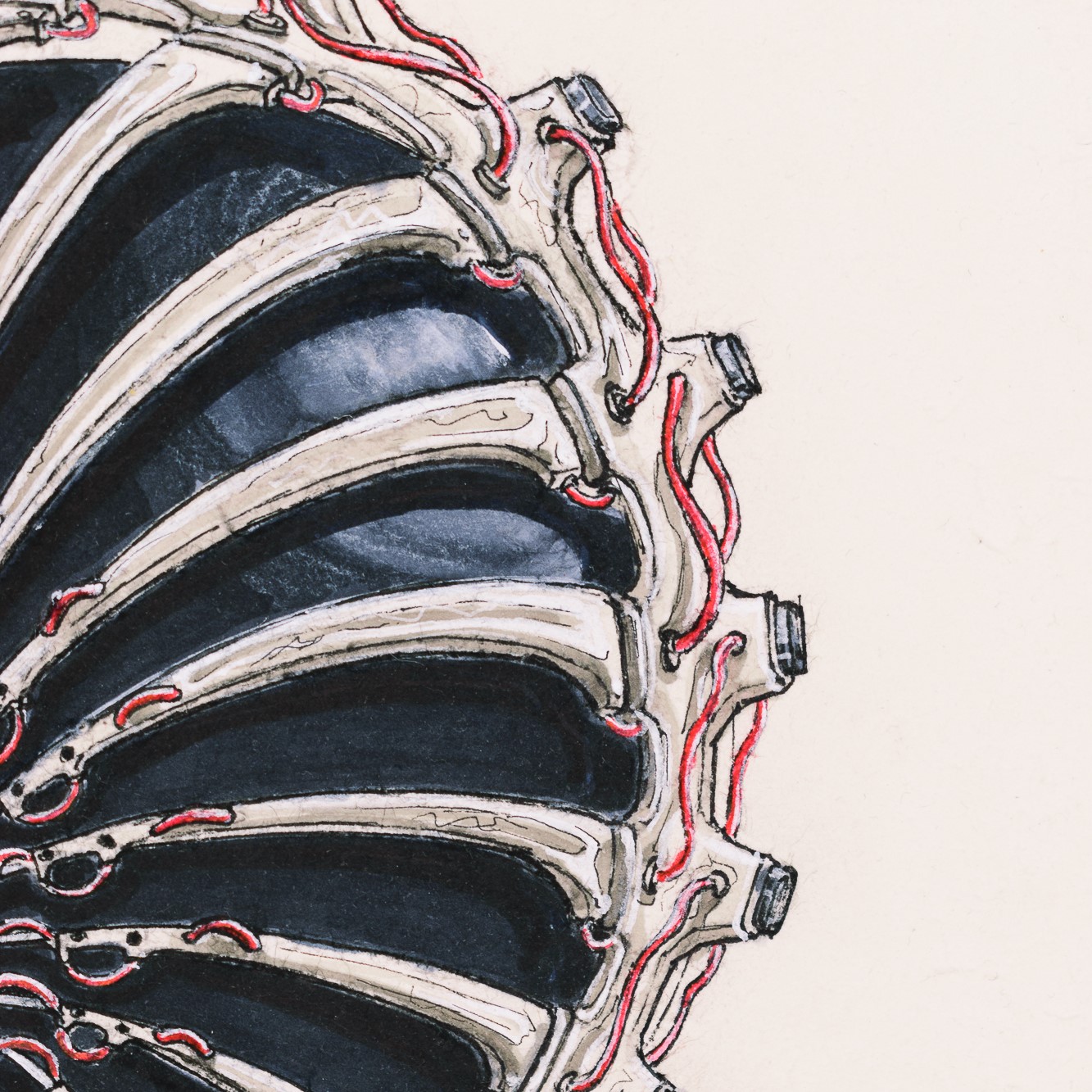
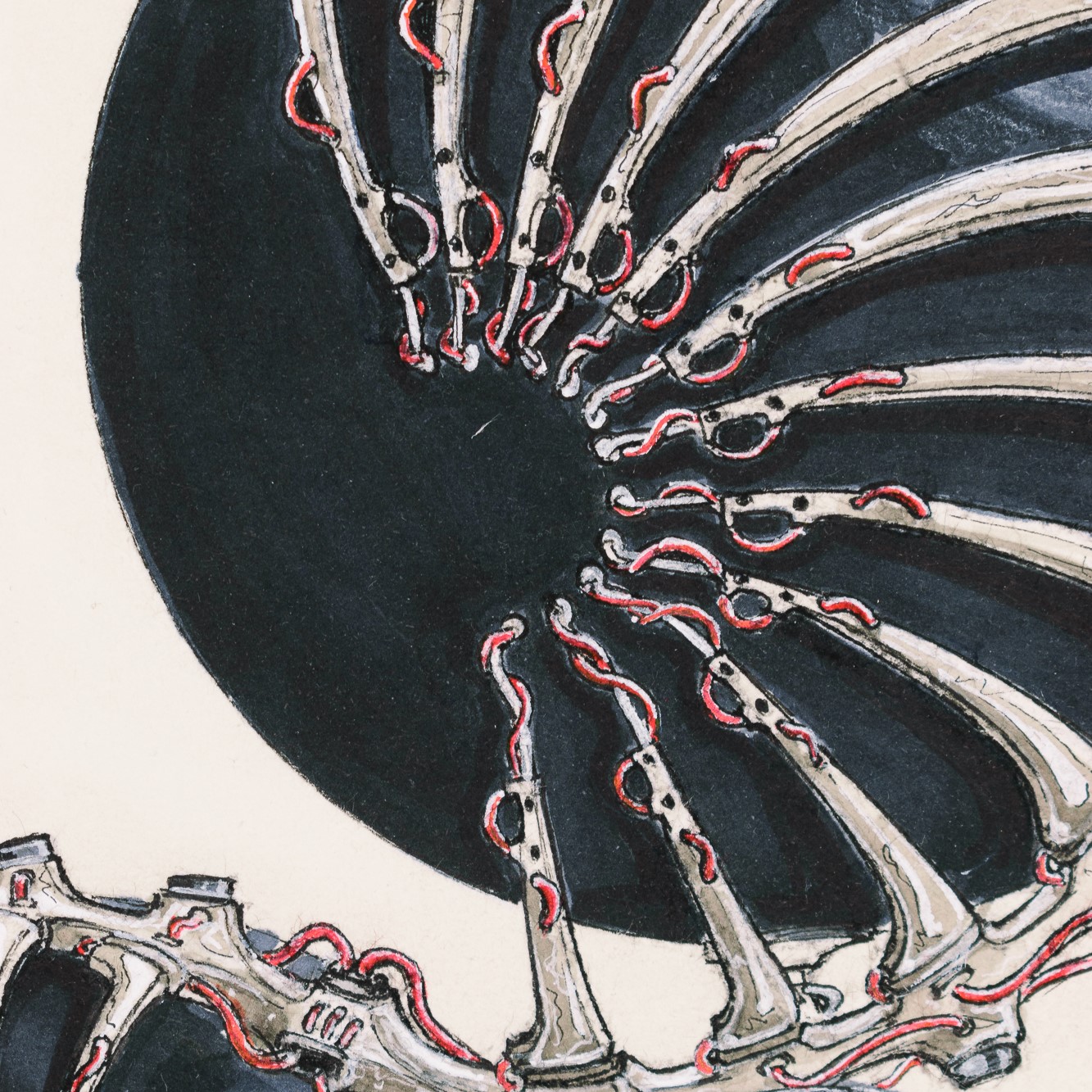
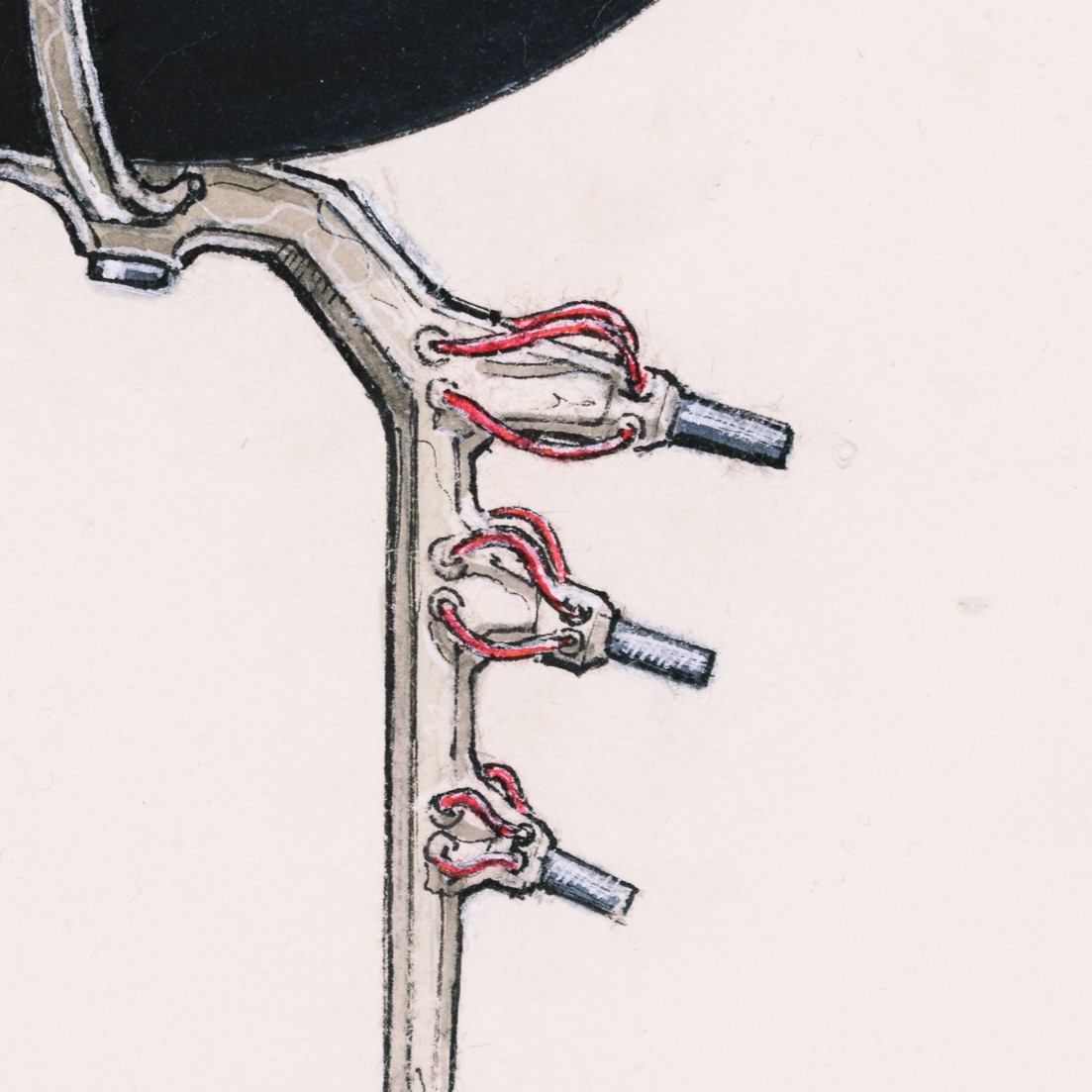
 (8).jpg)
 (9).jpg)
 (10).jpg)
 (13).jpg)
.jpg)
.jpg)
.jpg)
.jpg)
 (10).jpg)
 (8).jpg)
.jpg)
.jpg)
 (8).jpg)
 (4).jpg)
.jpg)
 (2).jpg)
 (4).jpg)
 (6).jpg)
 (9).jpg)
 (2).jpg)
.jpg)
.jpg)
 (7).jpg)
Sketches
One of my private projects is an ongoing collection of designs for unconventional instruments, vehicles, and other objects. At the moment, it consists of around 26 sketches with a size between A3 and A0.
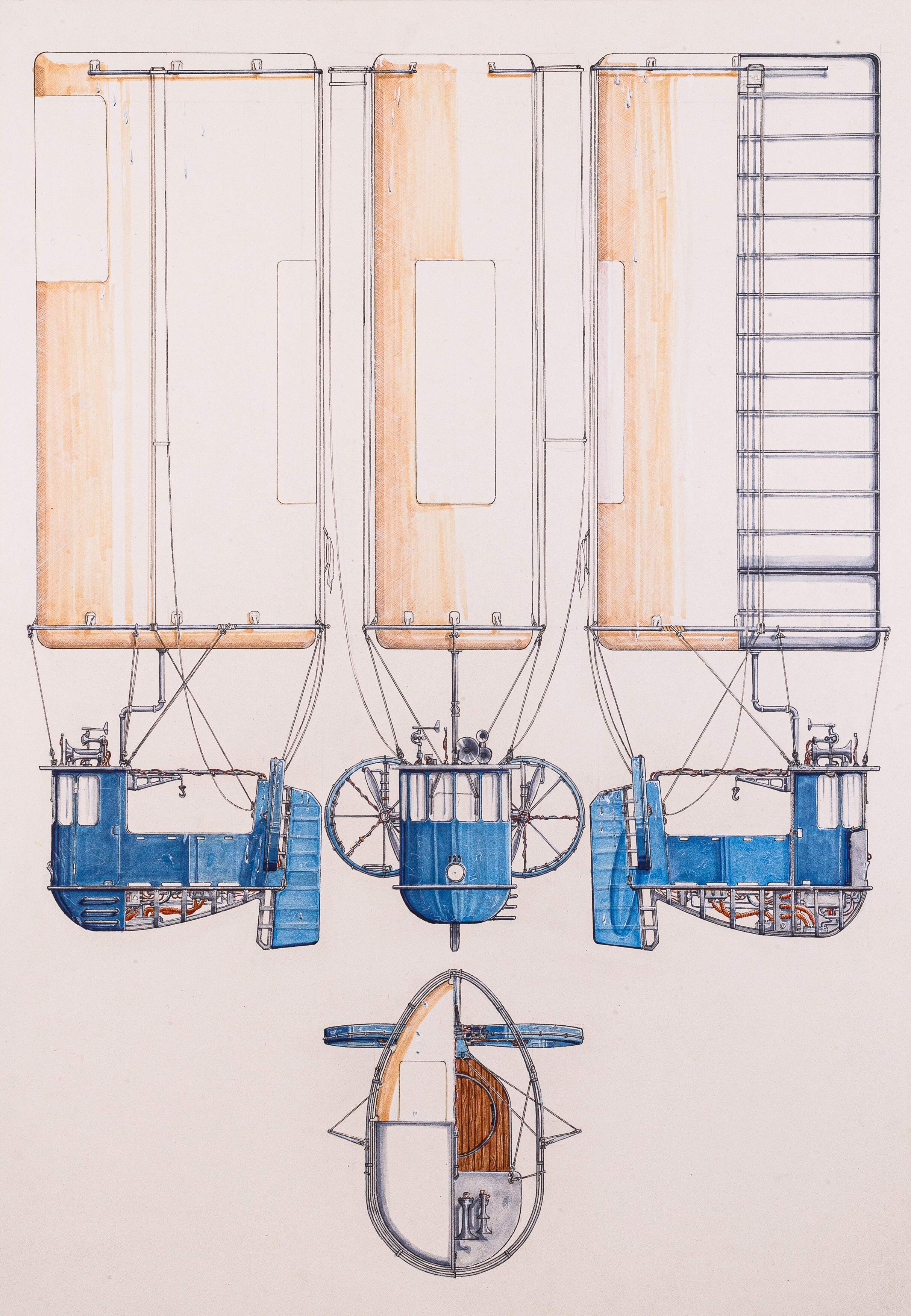
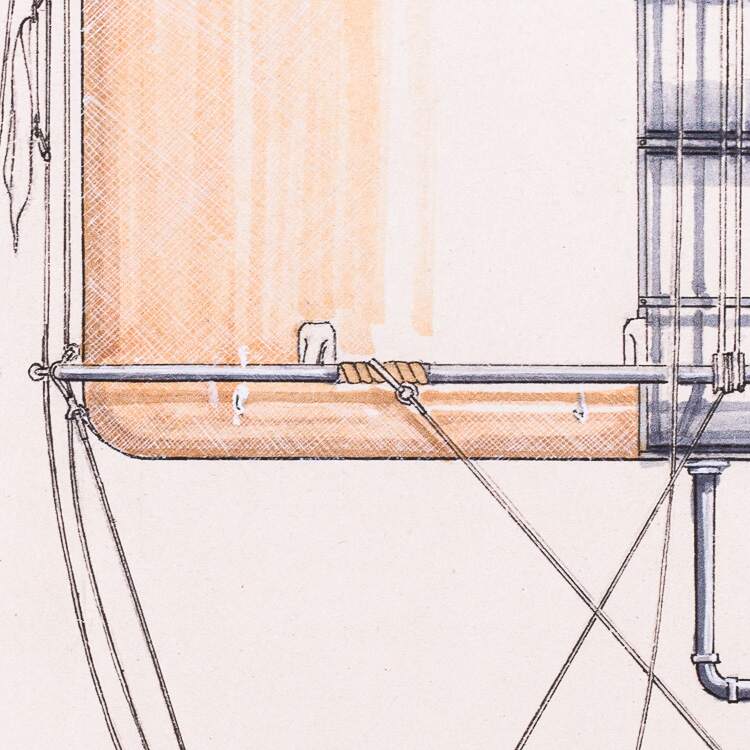
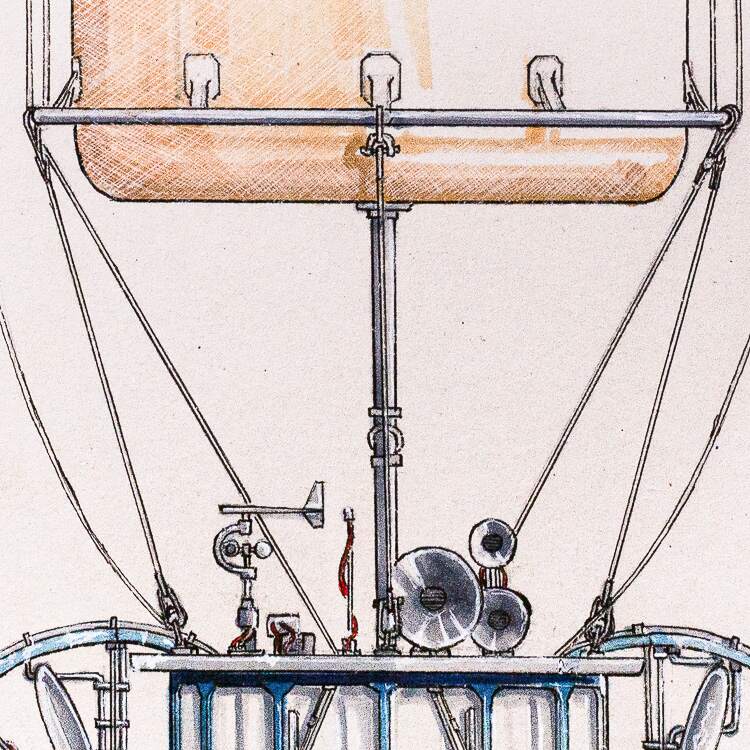
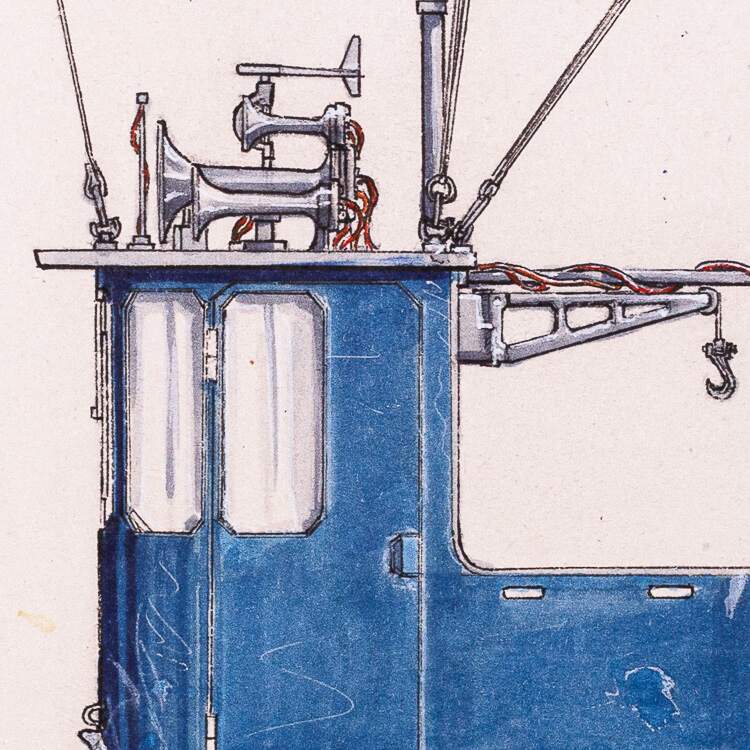
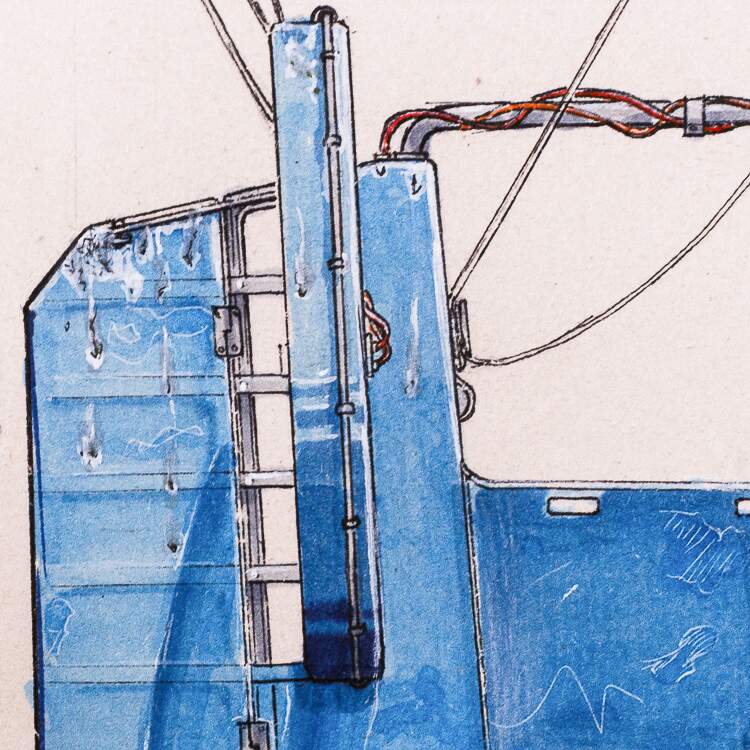
.jpg)
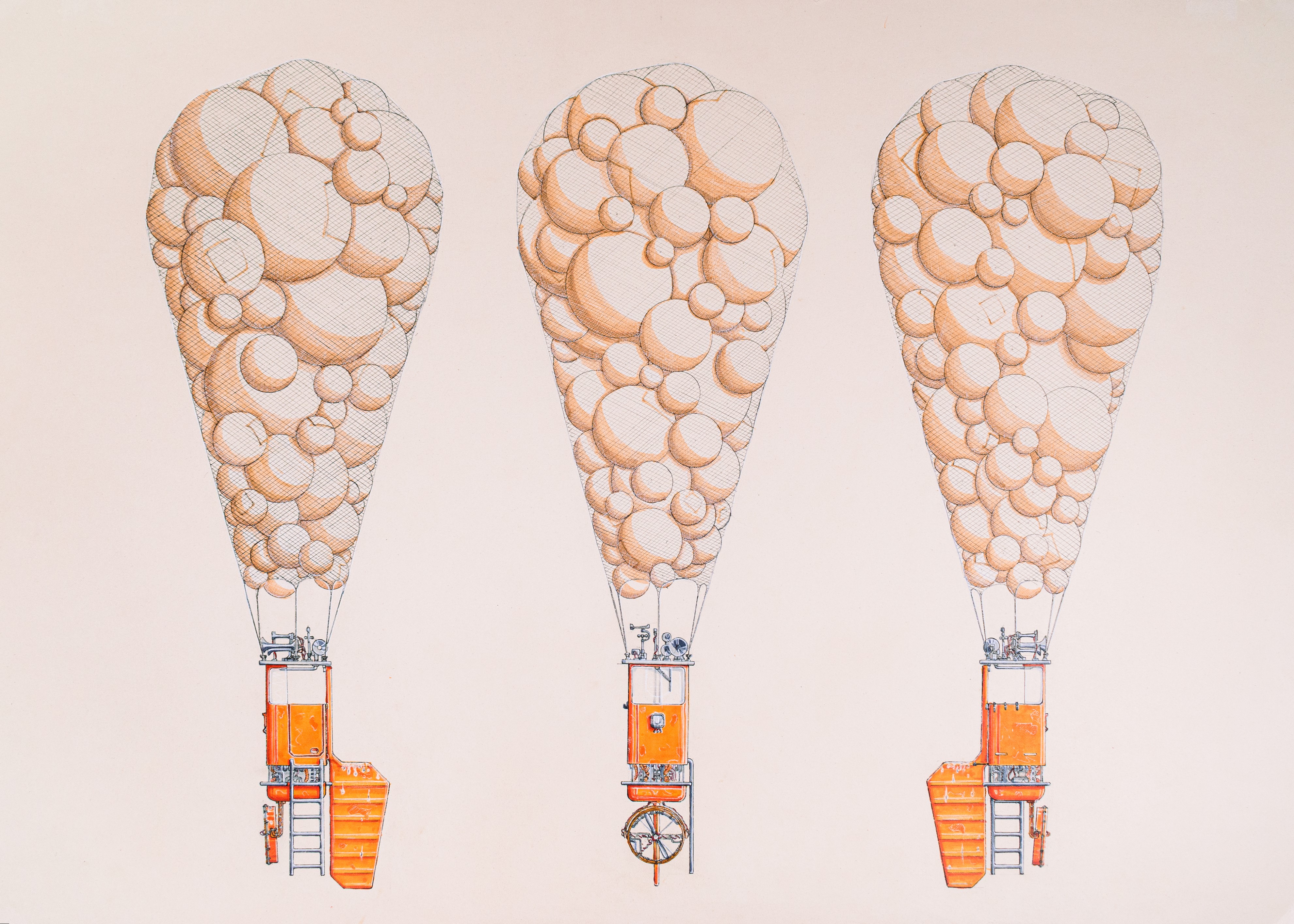
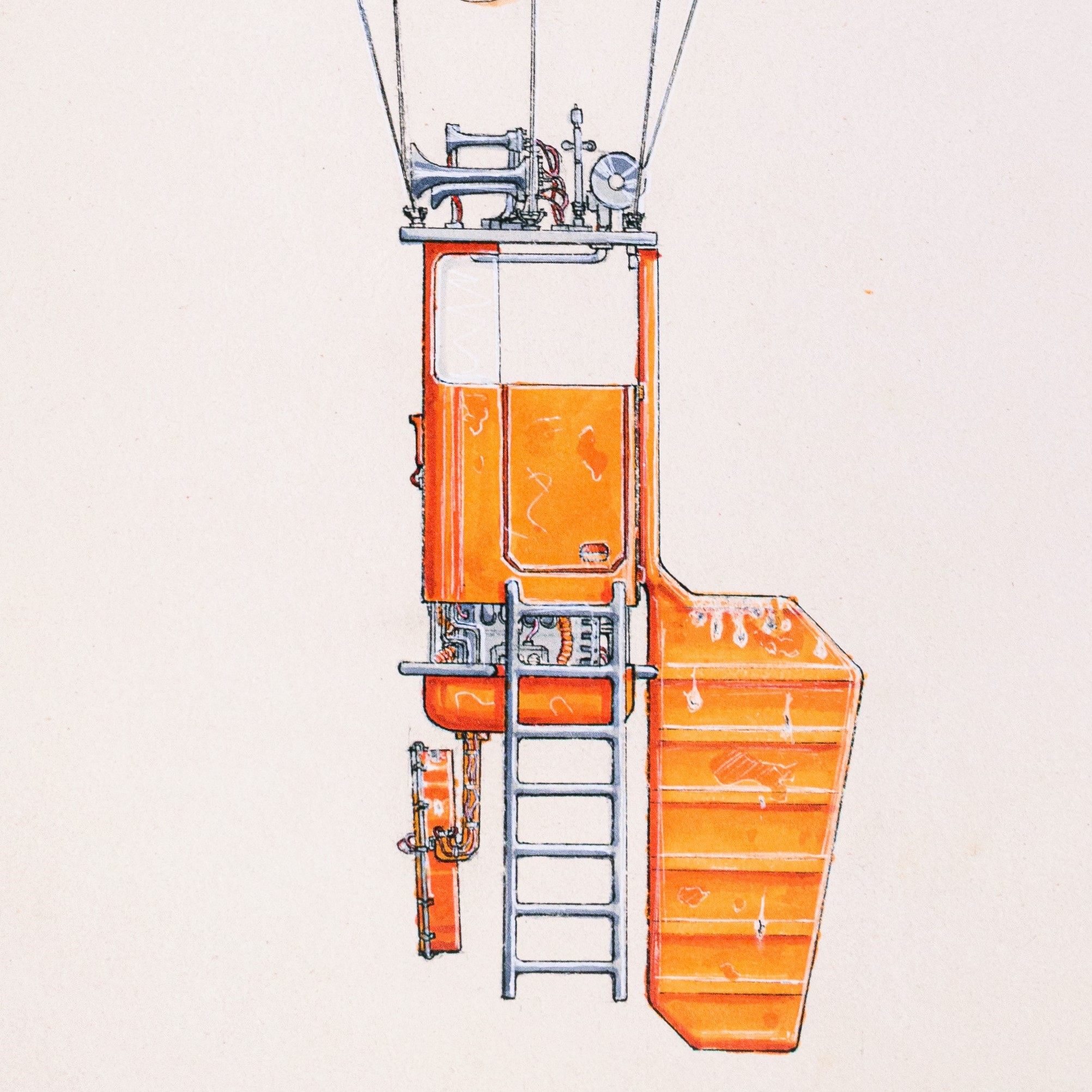
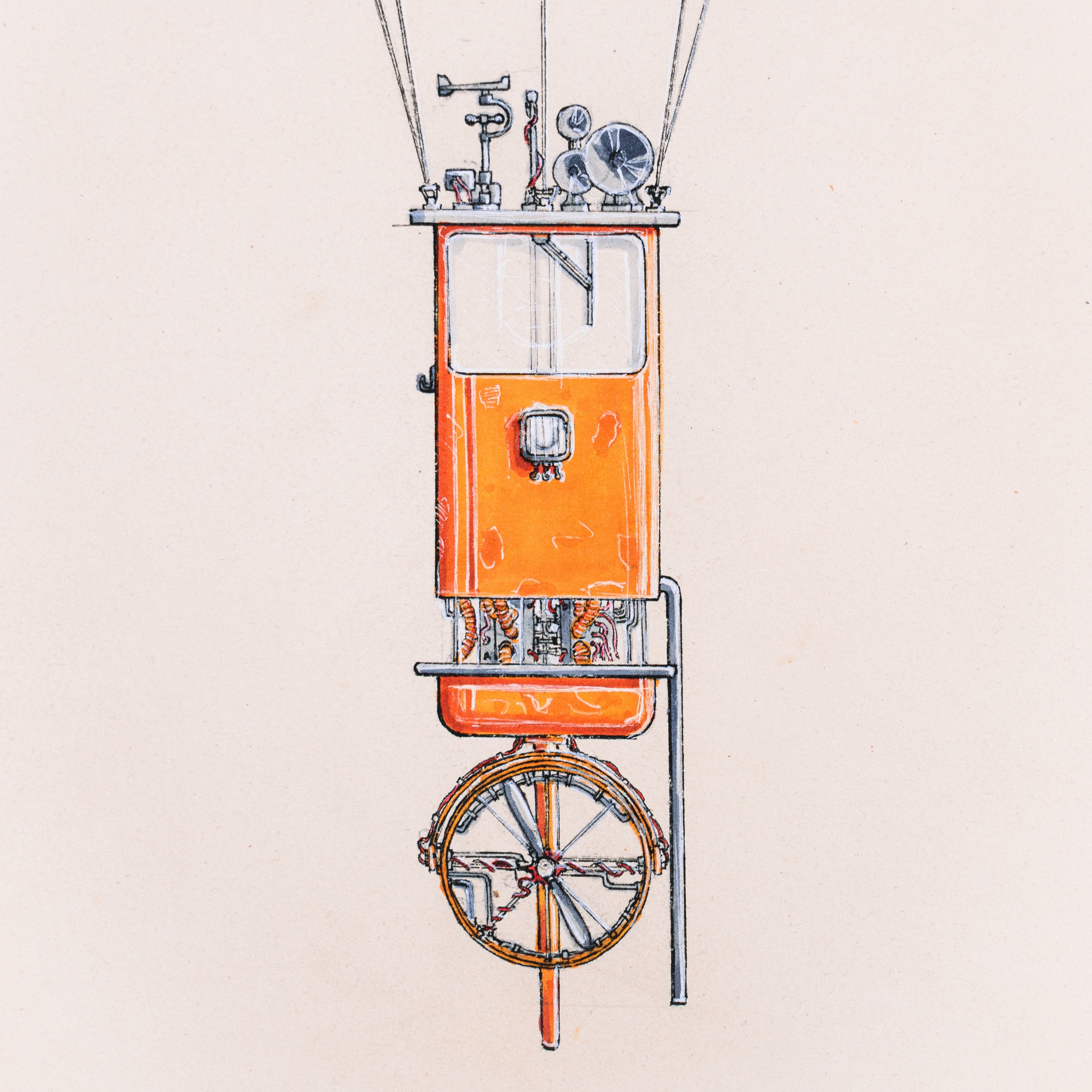
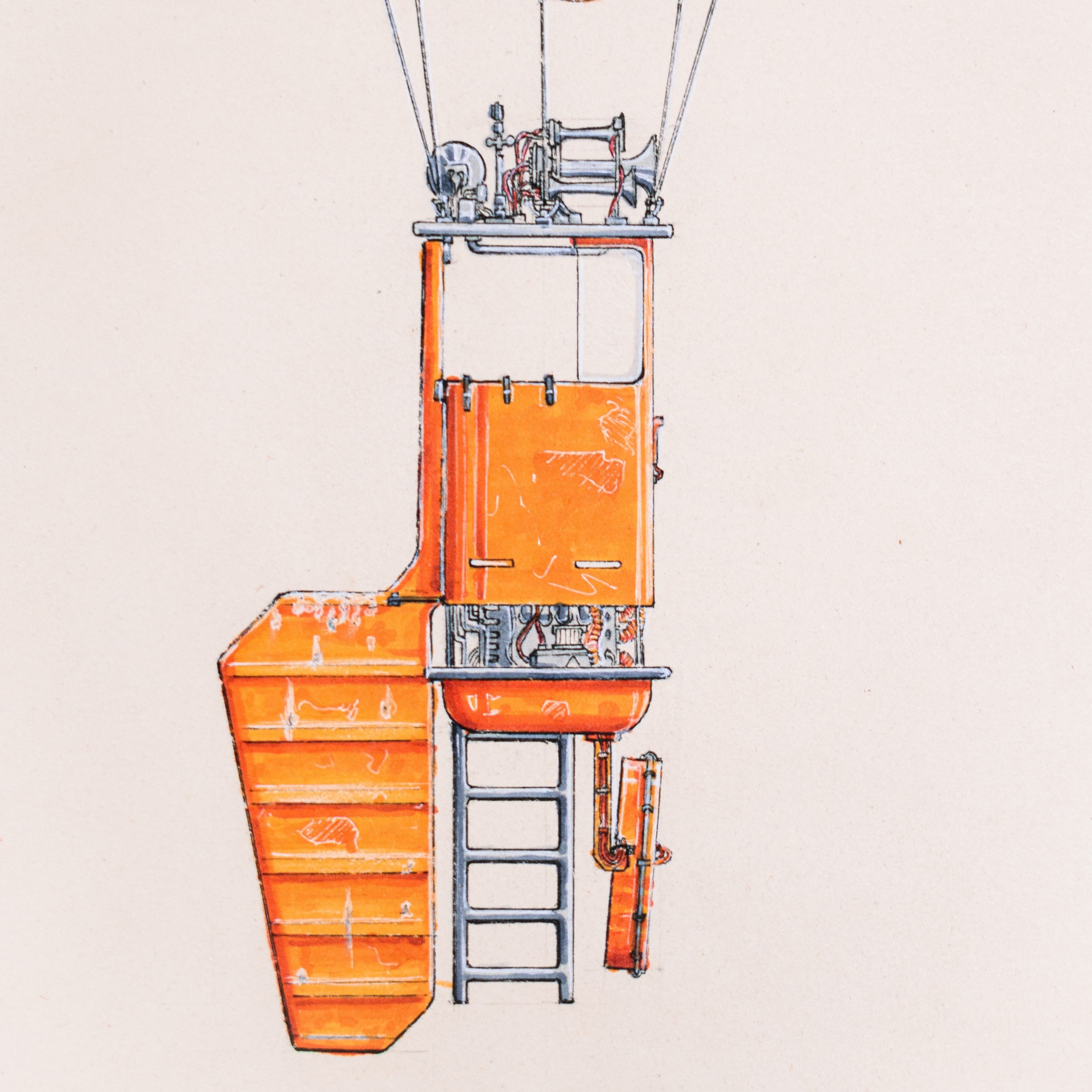
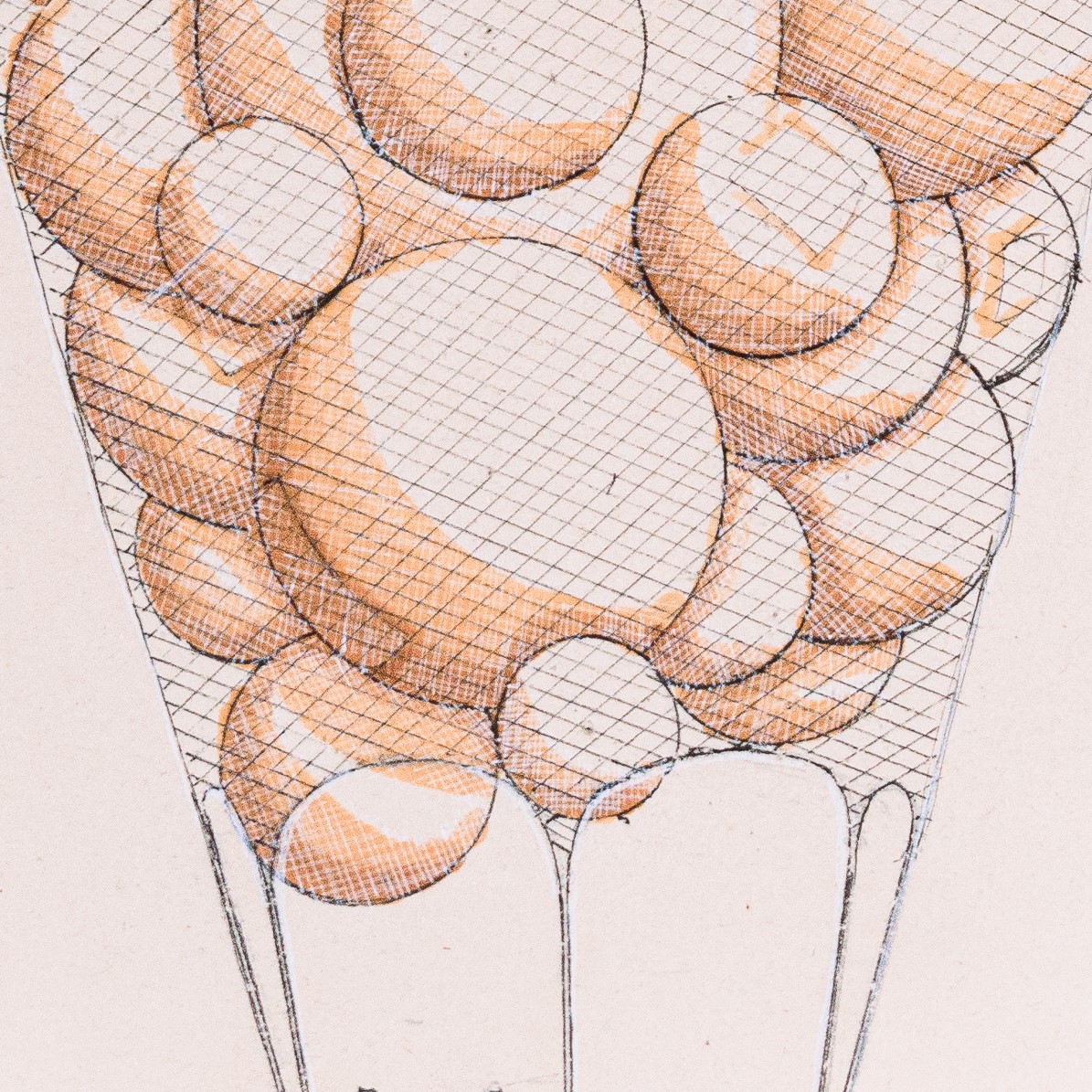
.jpg)
.jpg)
cropped.jpg)
.jpg)
.jpg)
.jpg)
.jpg)
2.jpg)
 (14).jpg)
 (6).jpg)
 (8).jpg)
 (2).jpg)
 (3).jpg)
 (2).jpg)
.jpg)
.jpg)
.jpg)
.jpg)
.jpg)
.jpg)
.jpg)
.jpg)
.jpg)
.jpg)
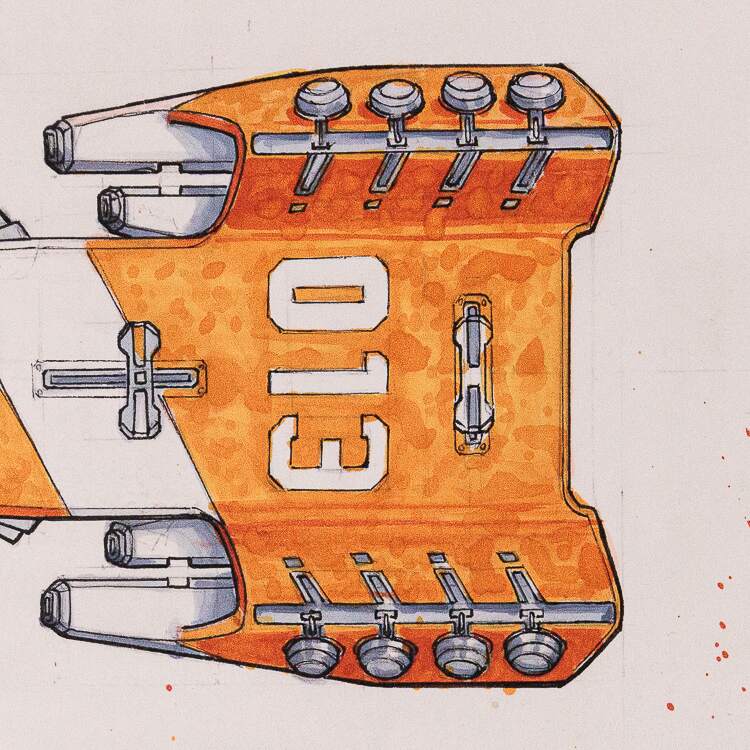
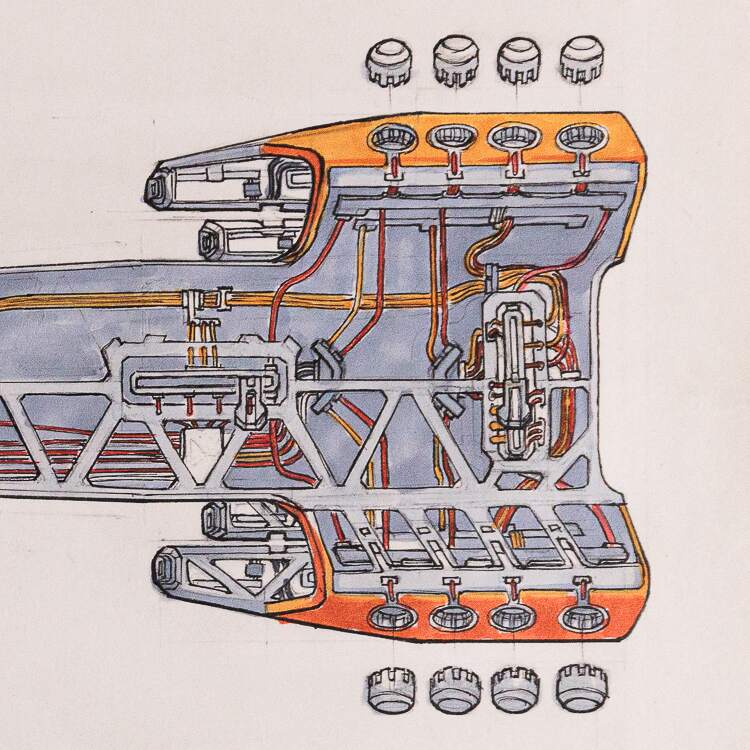
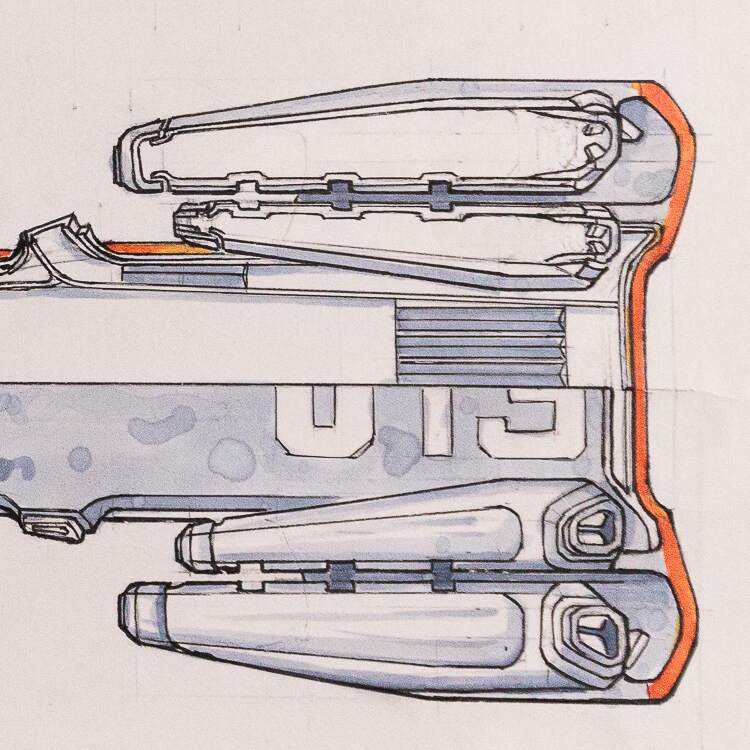
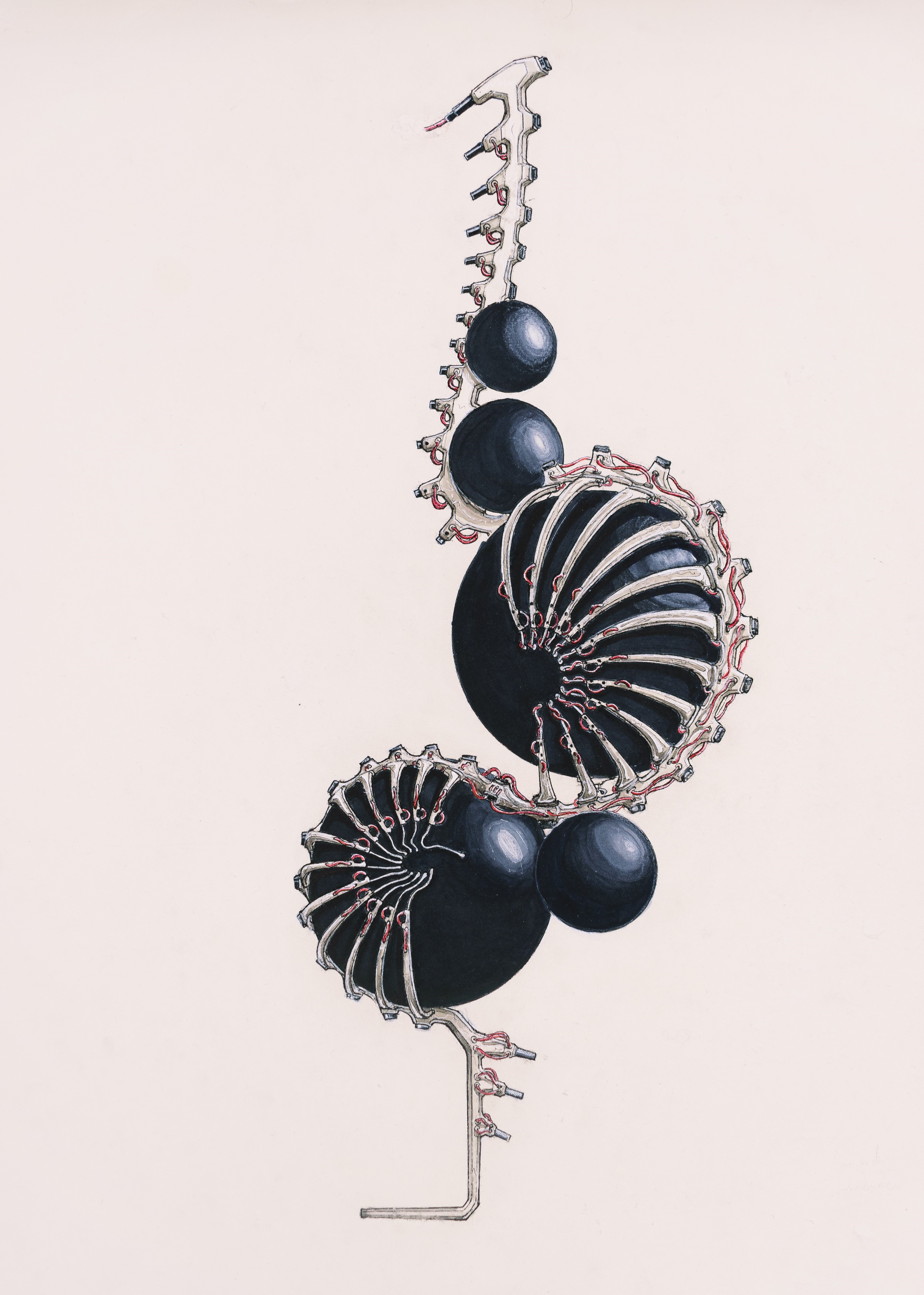
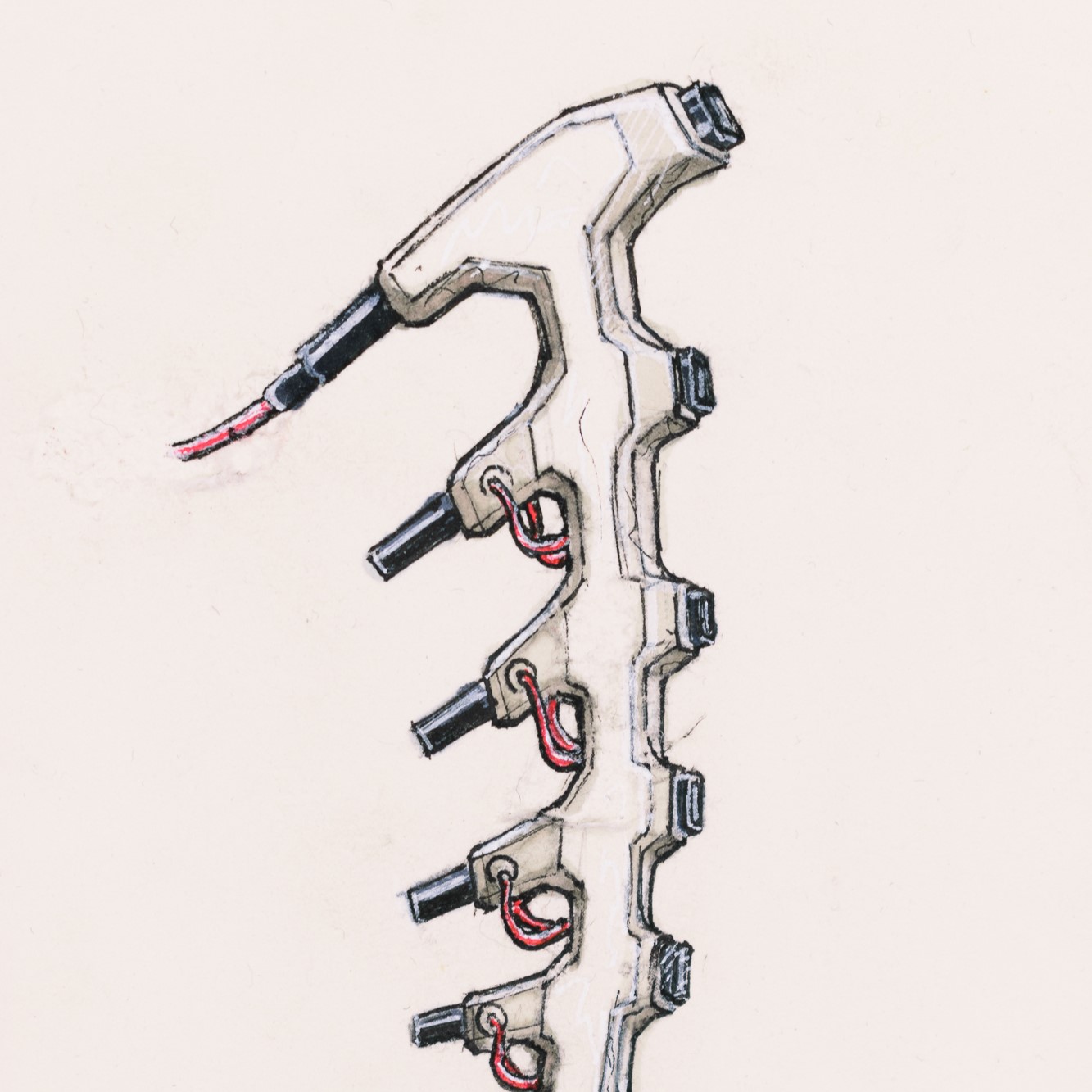
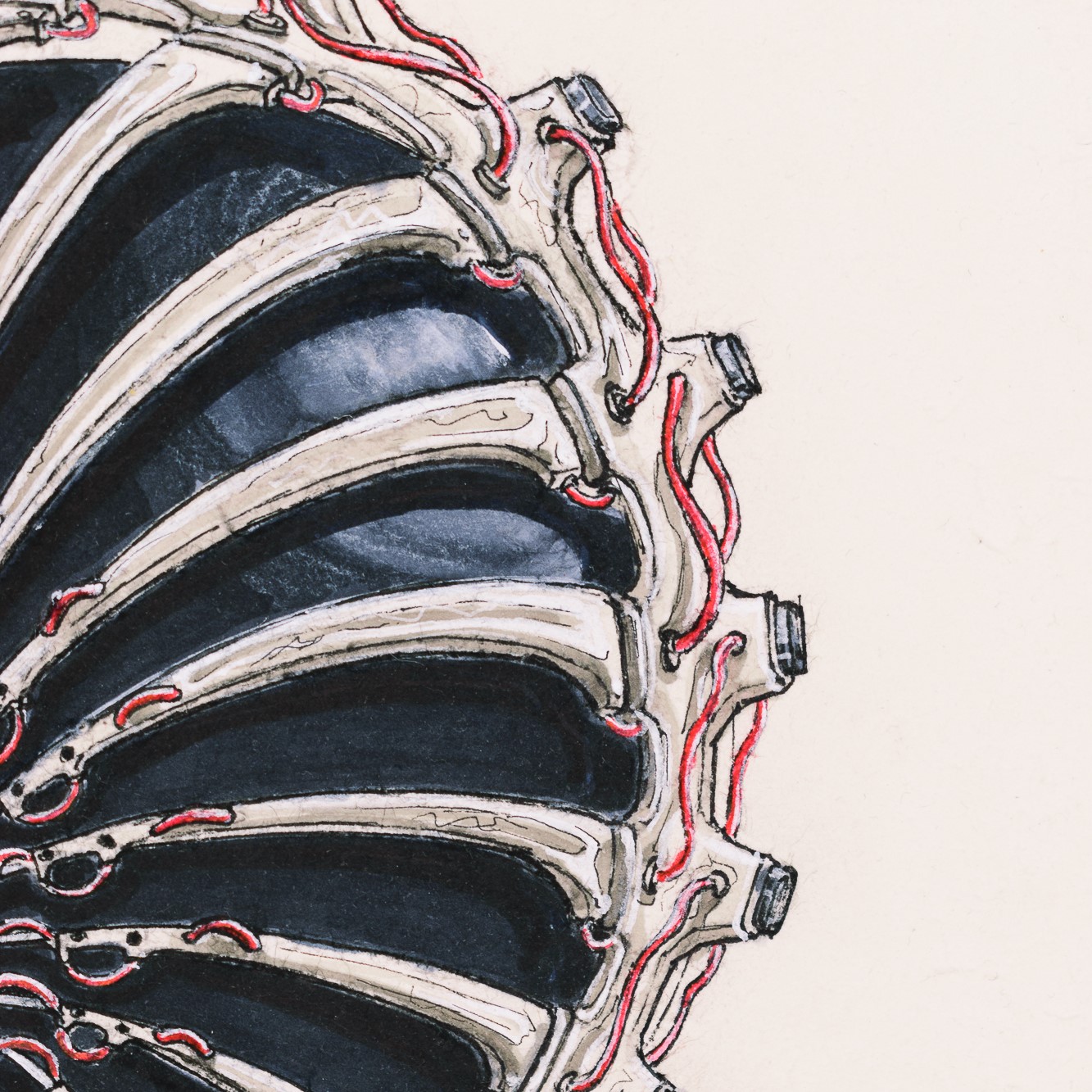
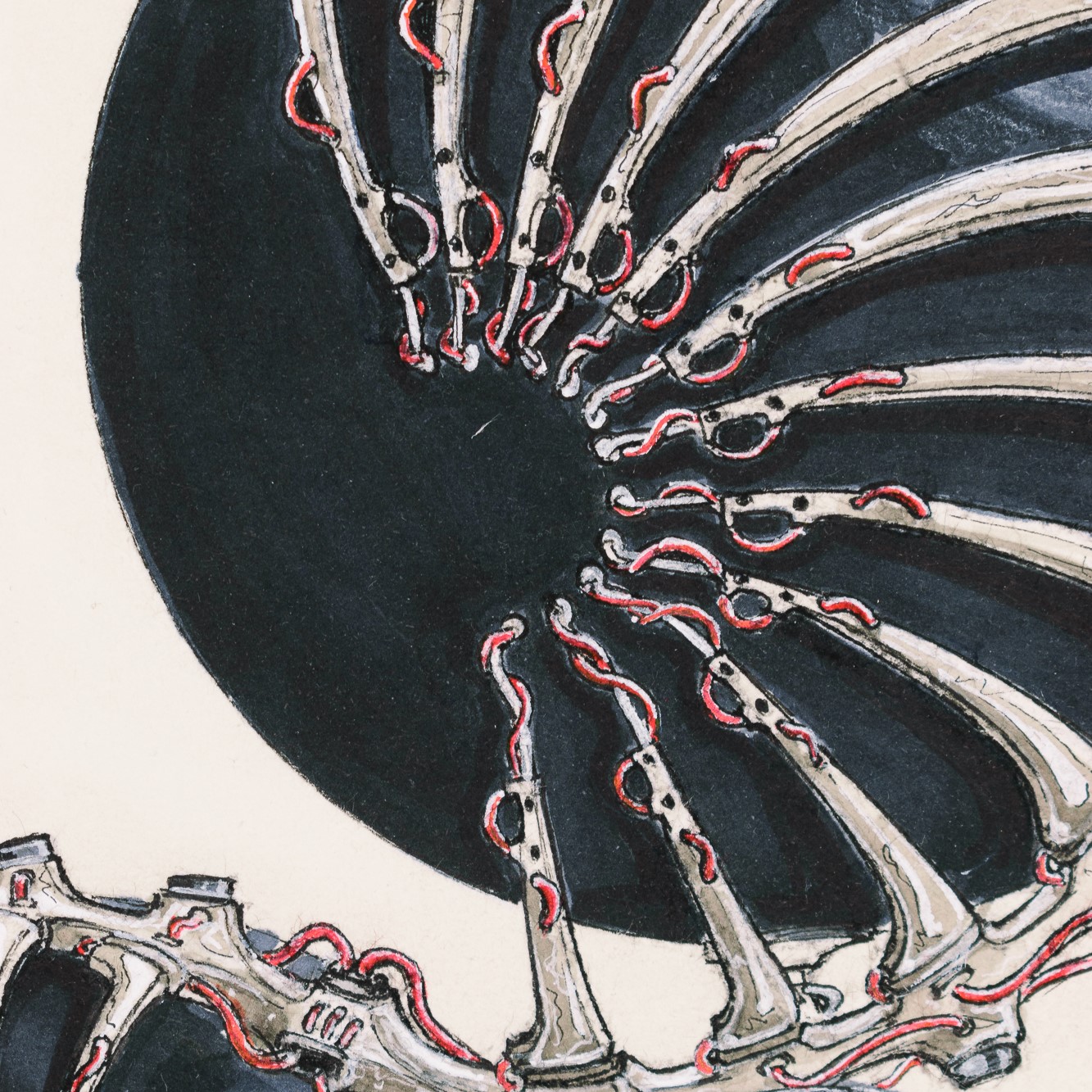
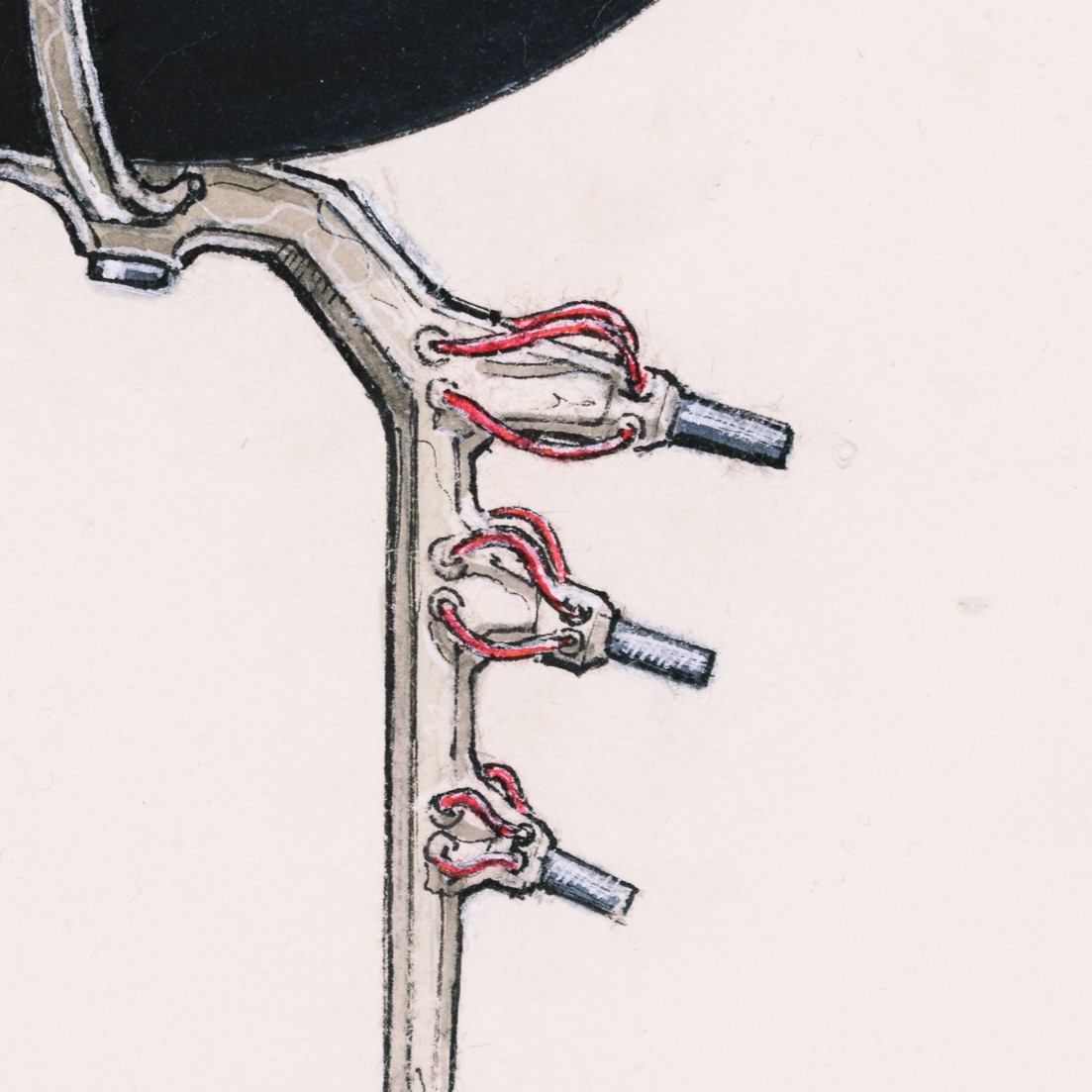
 (8).jpg)
 (9).jpg)
 (10).jpg)
 (13).jpg)
.jpg)
.jpg)
.jpg)
.jpg)
 (10).jpg)
 (8).jpg)
.jpg)
.jpg)
 (8).jpg)
 (4).jpg)
.jpg)
 (2).jpg)
 (4).jpg)
 (6).jpg)
 (9).jpg)
 (2).jpg)
.jpg)
Framed Fluids
"Framed Fluids" was my first attempt to get my hands on the Blender geometry node workflow. In my opinion, this kind of workflow seems more suitable for creating abstract shapes than precise models, at least for a beginner. Furthermore, I wanted to know how much effort I had to put into creating just slightly different iterations in a pretty short amount of time. I intend to implement geometry-node-based models into my workflow to make quick iterations of products and artistic animations in the future.
Framed Fluids
"Framed Fluids" was my first attempt to get my hands on the Blender geometry node workflow. In my opinion, this kind of workflow seems more suitable for creating abstract shapes than precise models, at least for a beginner. Furthermore, I wanted to know how much effort I had to put into creating just slightly different iterations in a pretty short amount of time. I intend to implement geometry-node-based models into my workflow to make quick iterations of products and artistic animations in the future.
Rocking Horse
Rocking Horse
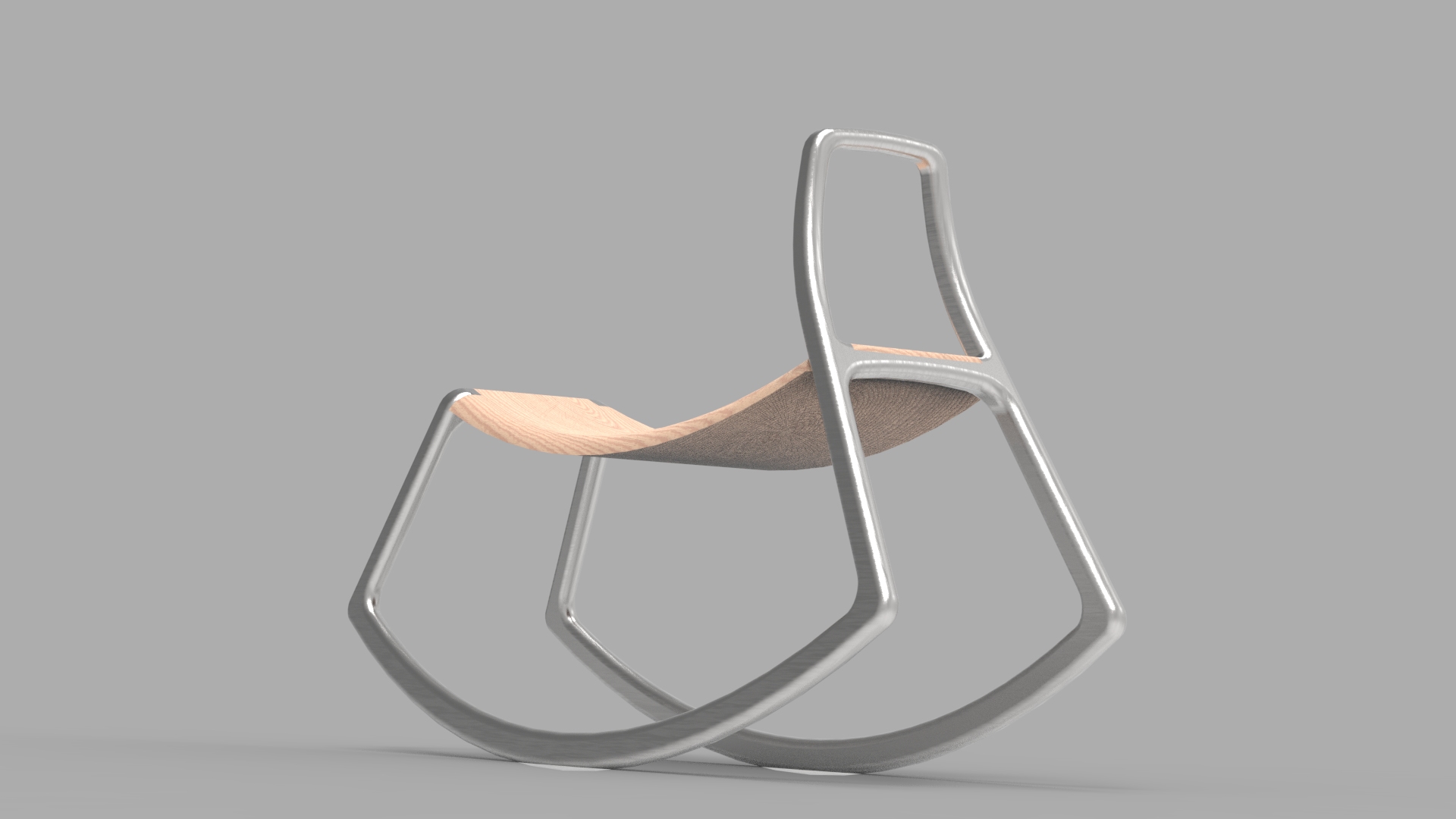
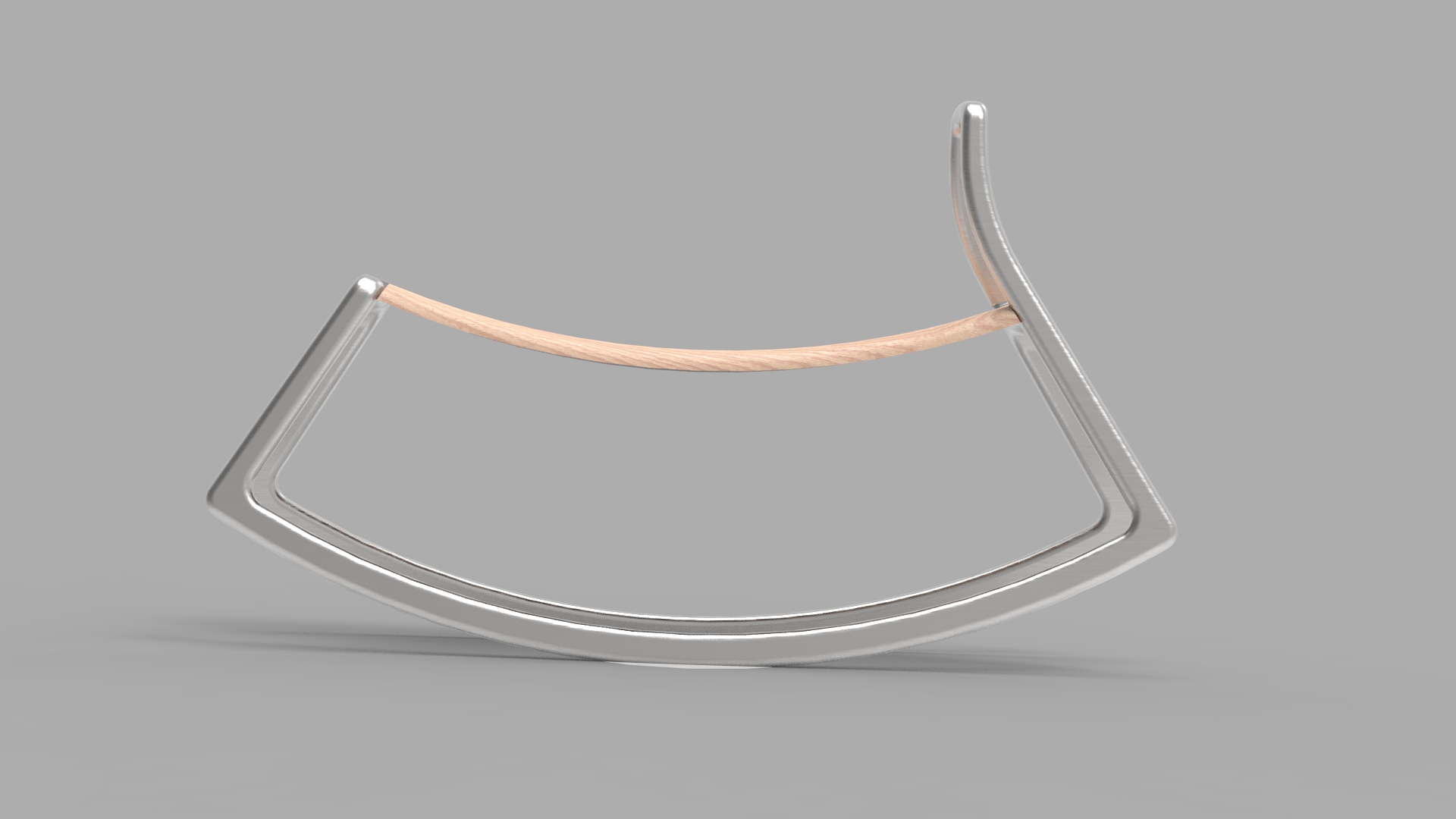
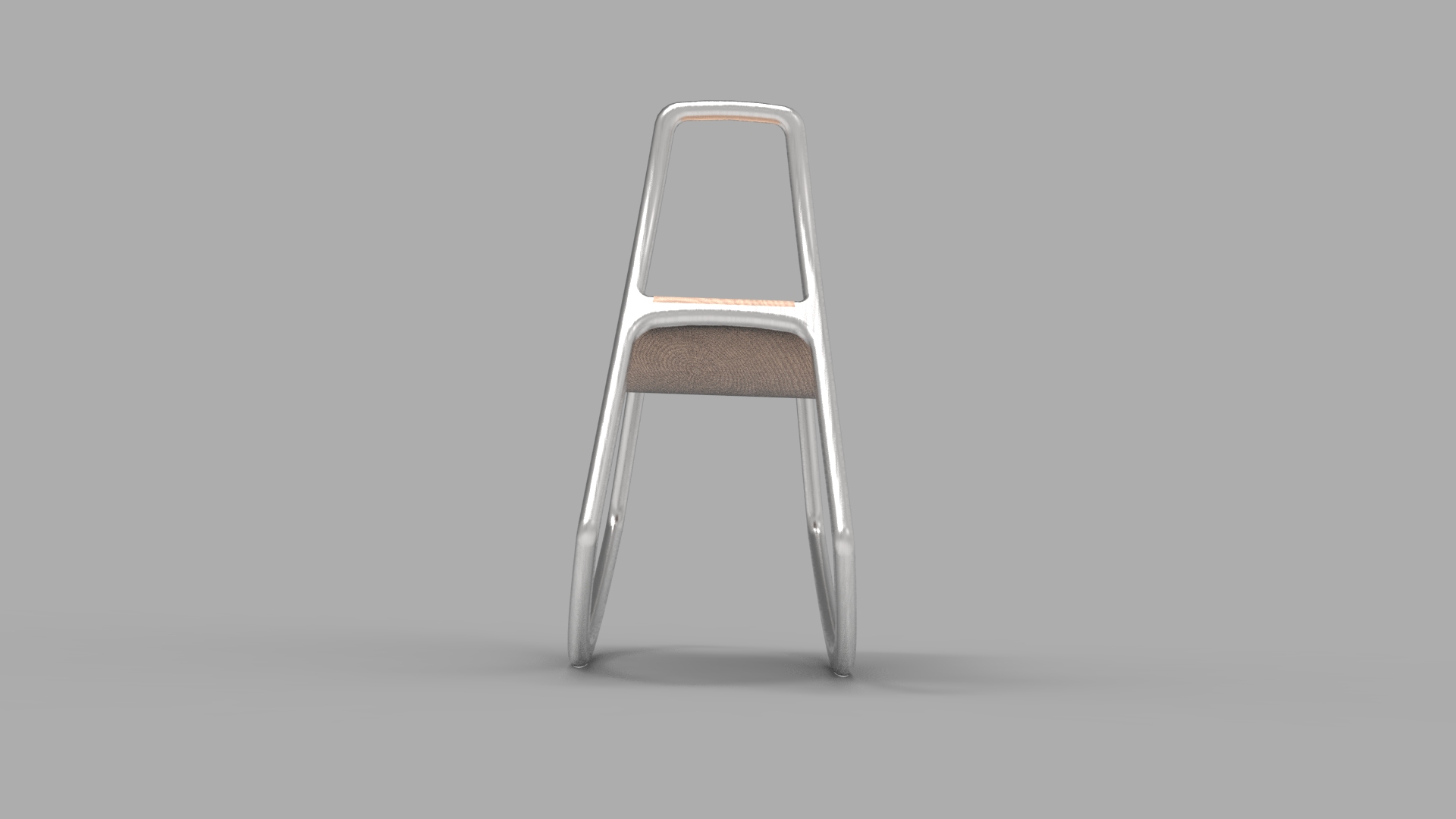
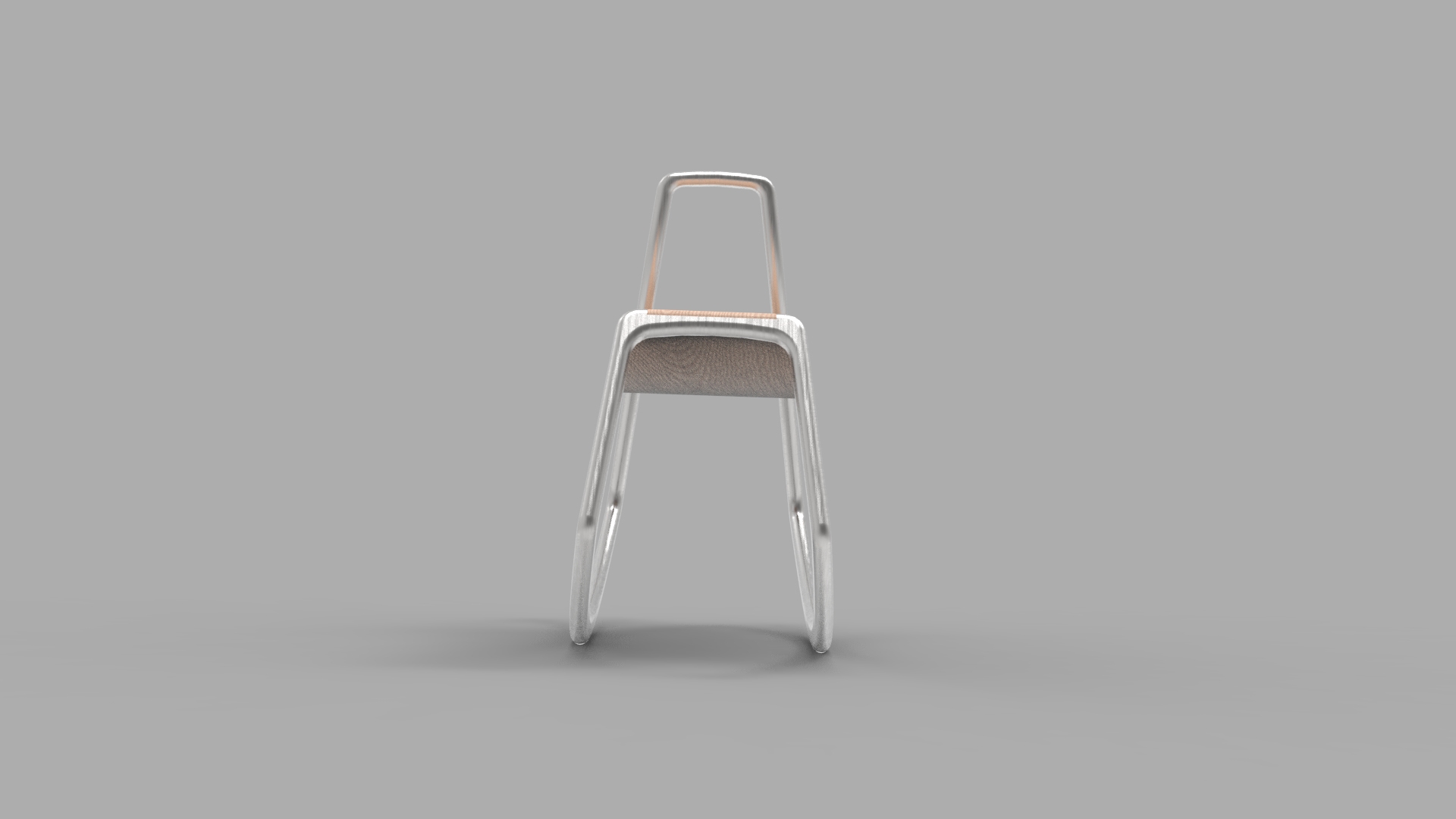
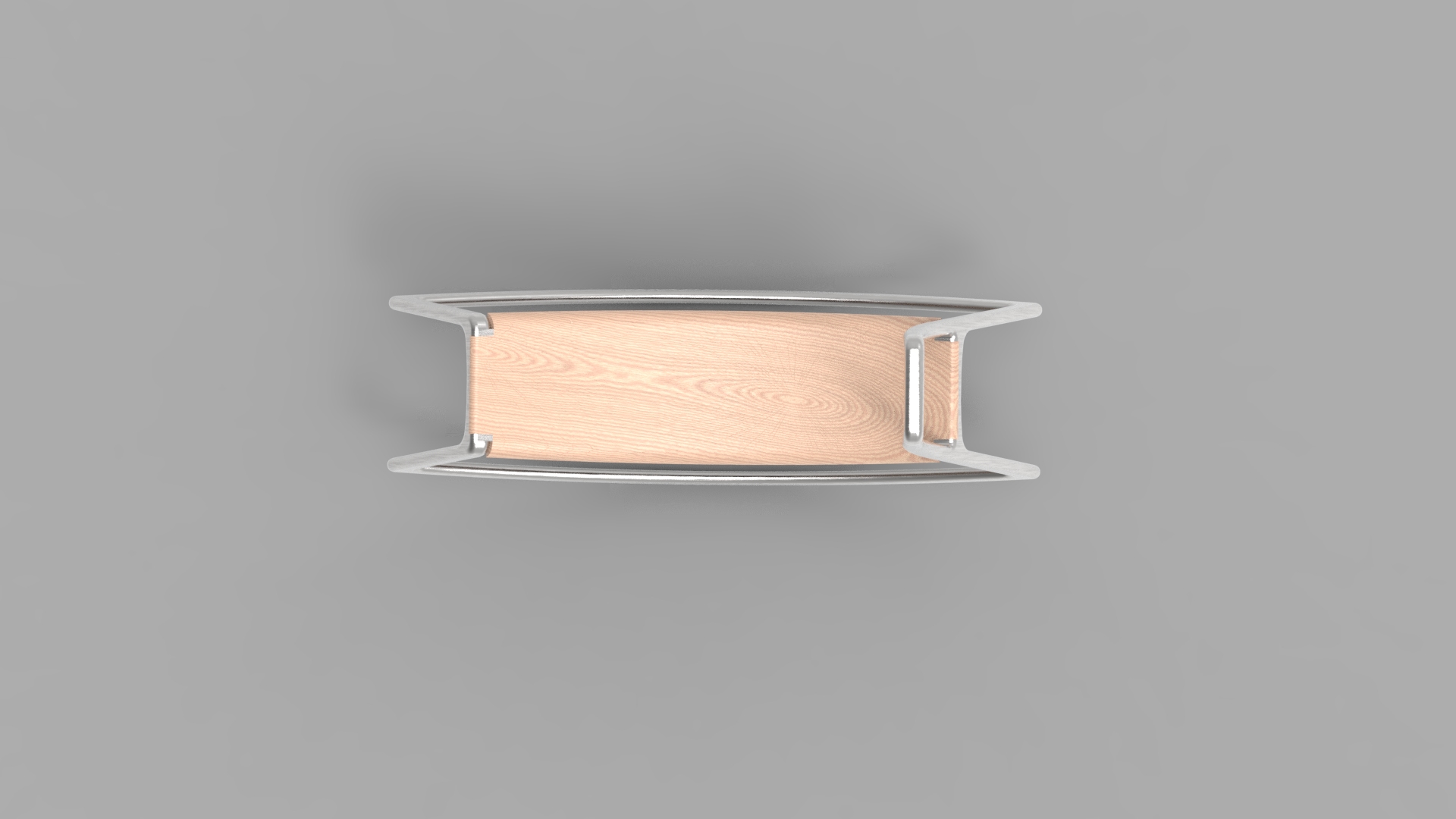
An ergonomics study
The rocking horse for grownups was a project we did in our first ergonomics course in the third semester. I had the intent to create something comfortable that still has an uncommon
design compared to regular rocking horses. The used data is documented in the charts further down in this widget. I took the needed data from my "Ergonomische Datensammlung". I calculated the size of the rocking horse depending on my own height of around 197 cm.
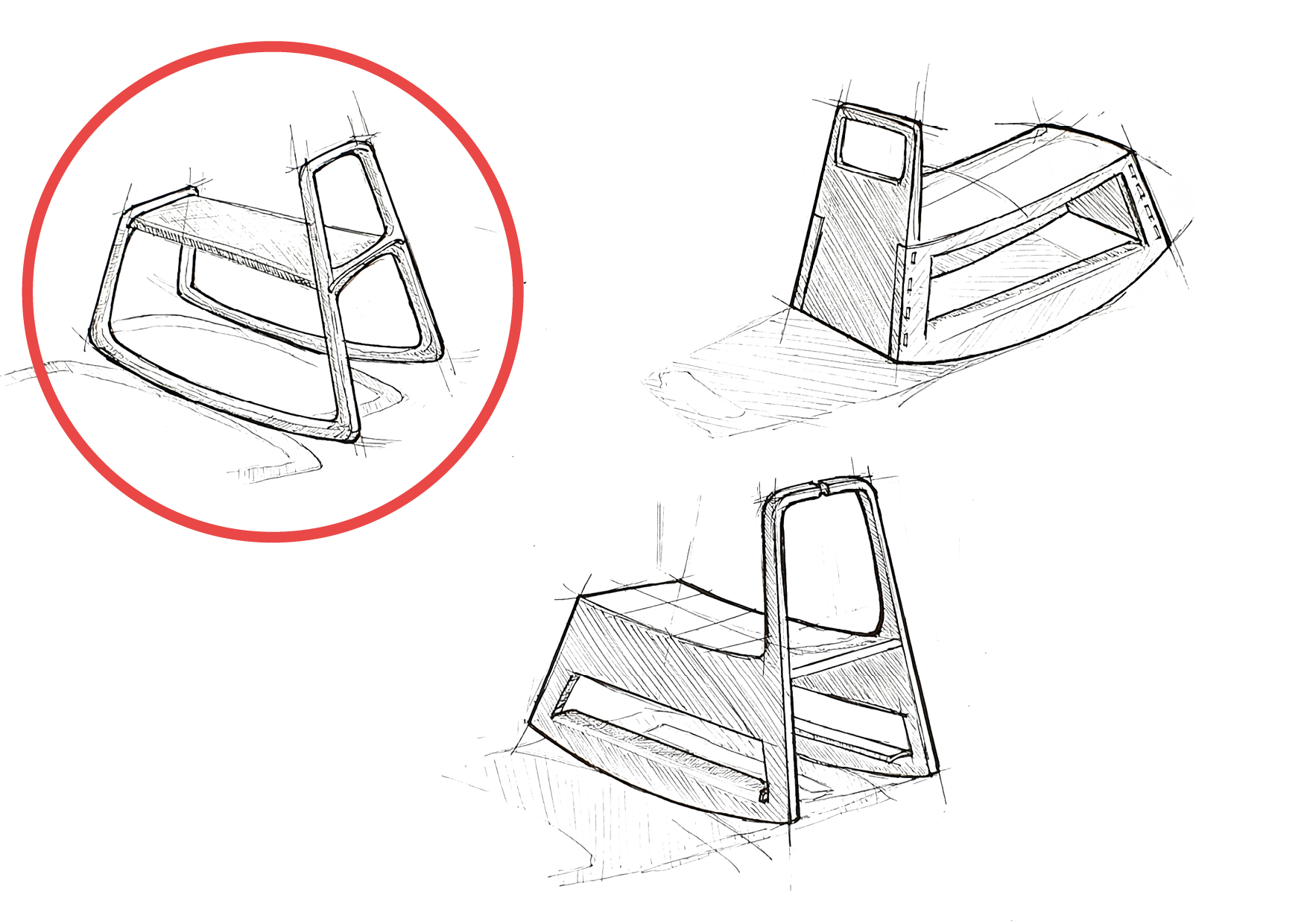
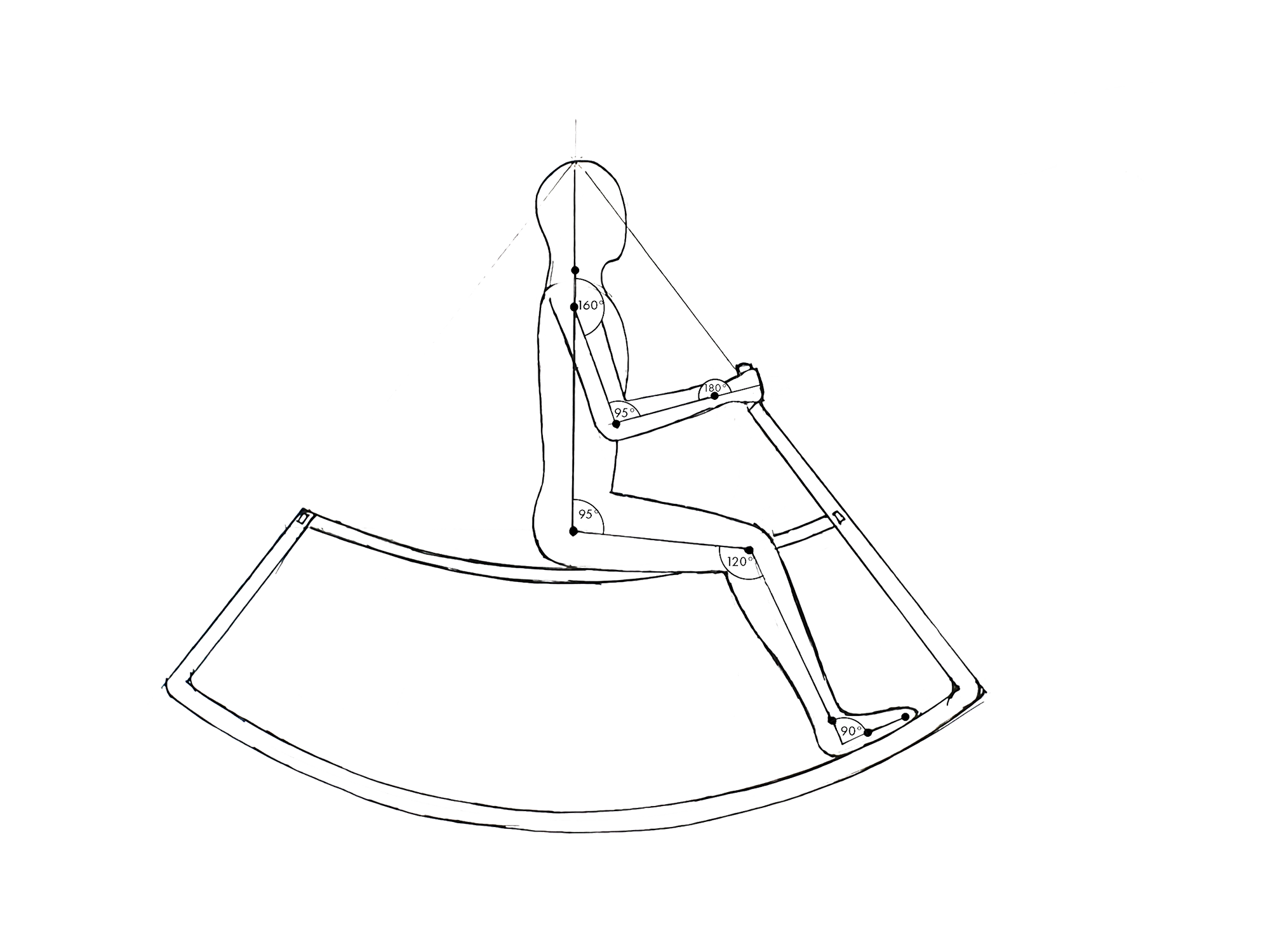
The relevant data
The data inside the chats shows the values that I considered to be the most relevant for the design. I applied the comfortable angles to the sketch above so that I could see if the shape I created was suitable for the given ergonomic data.
.png)
.png)
.png)
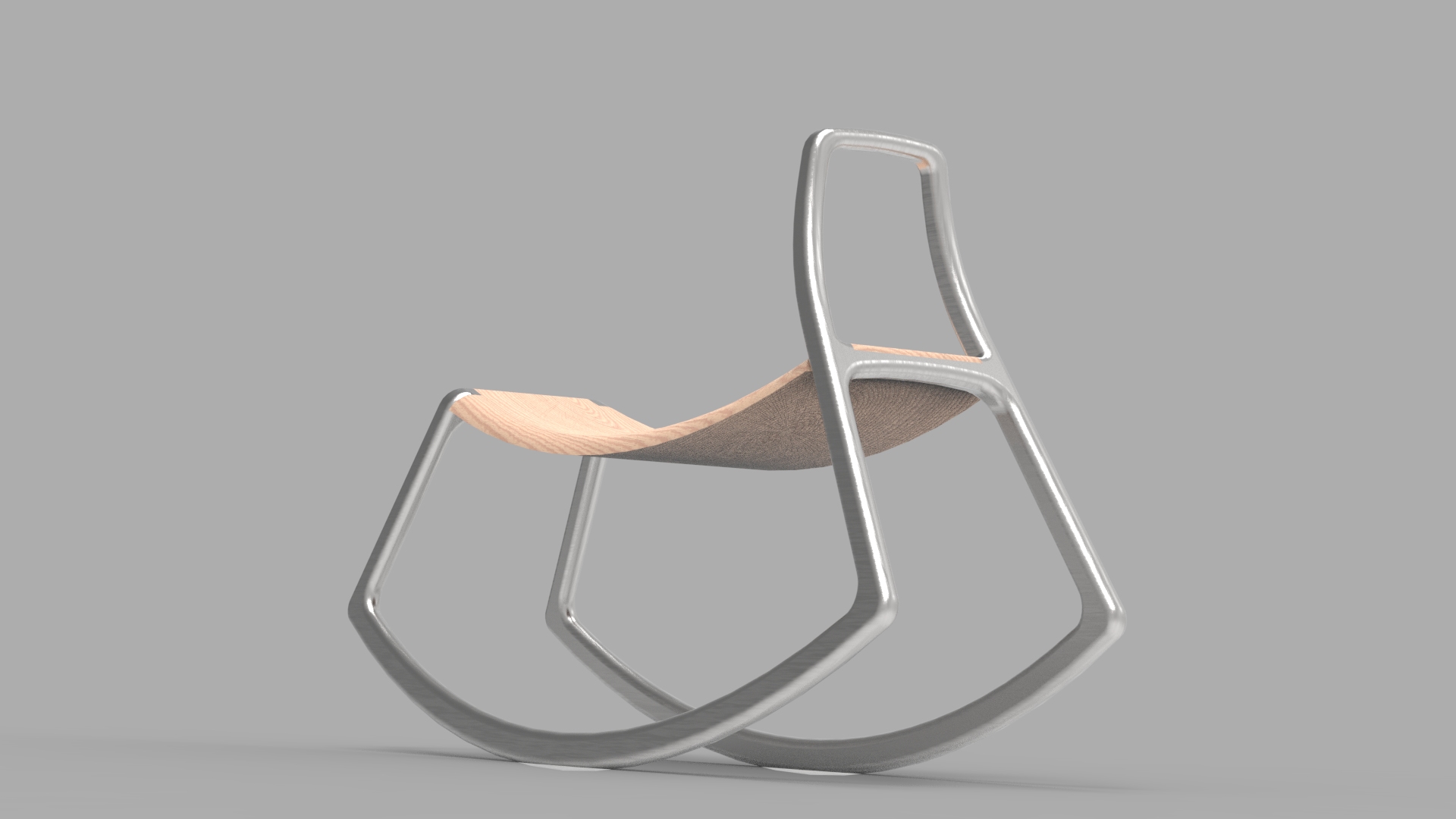
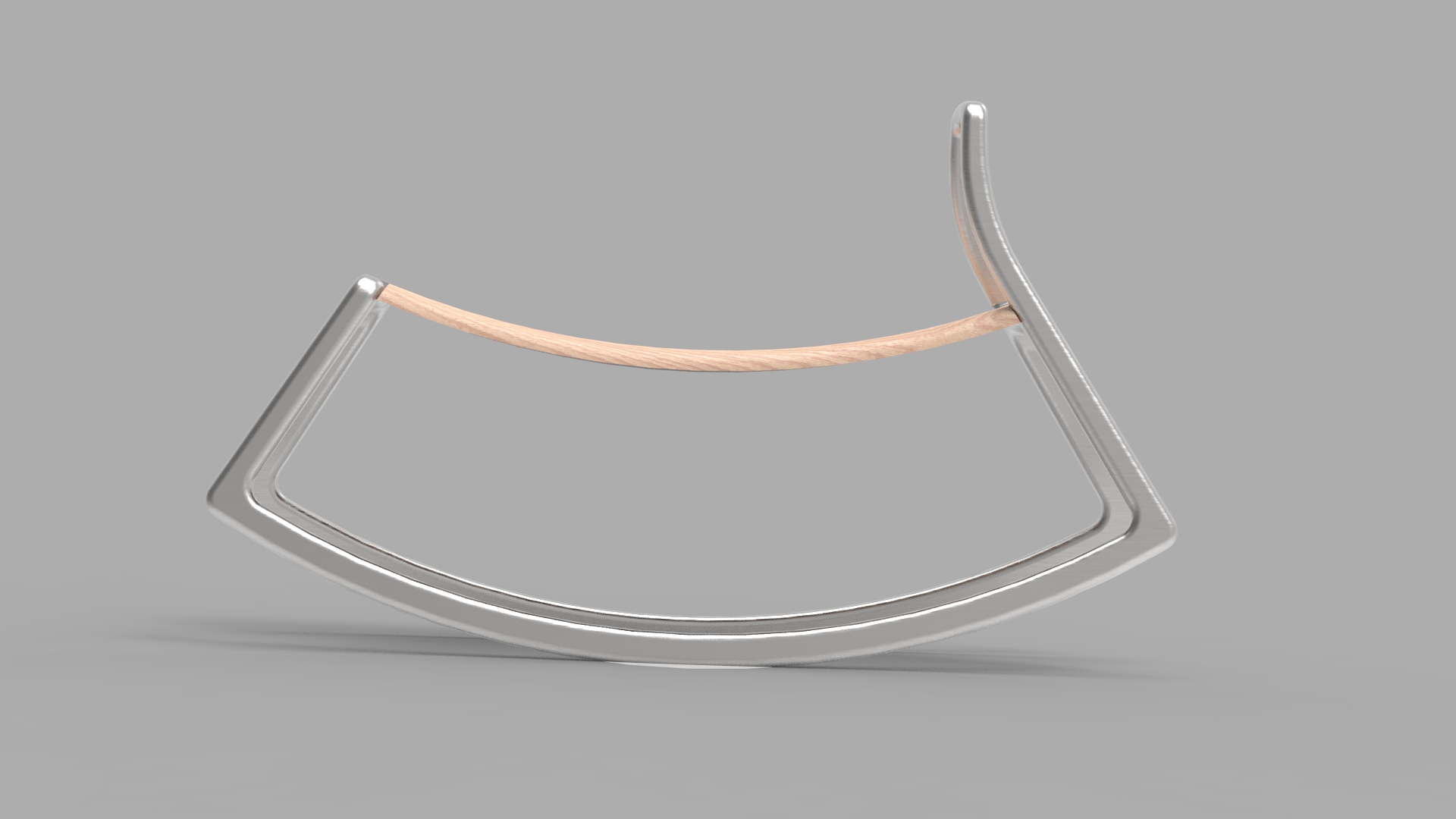
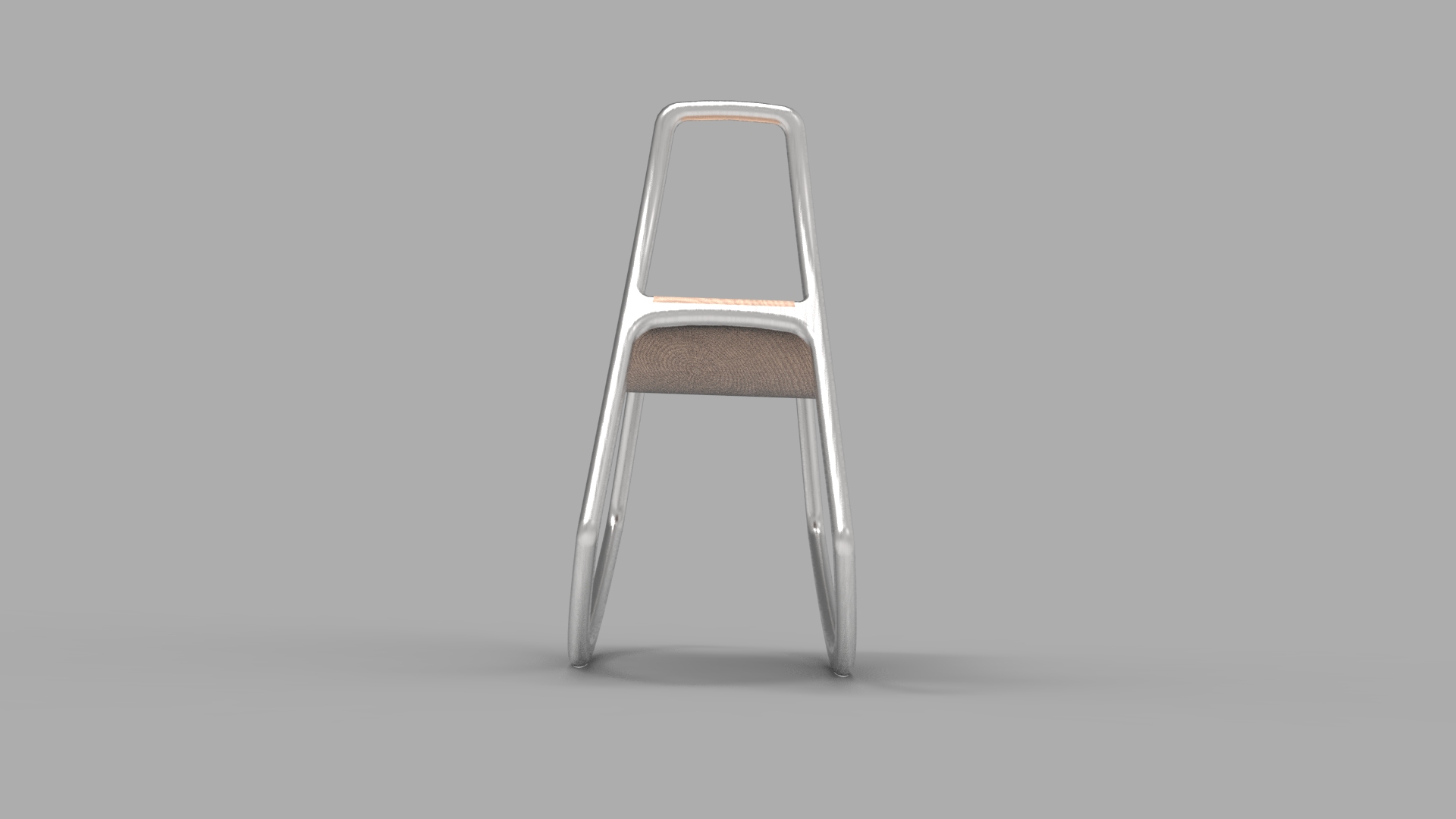
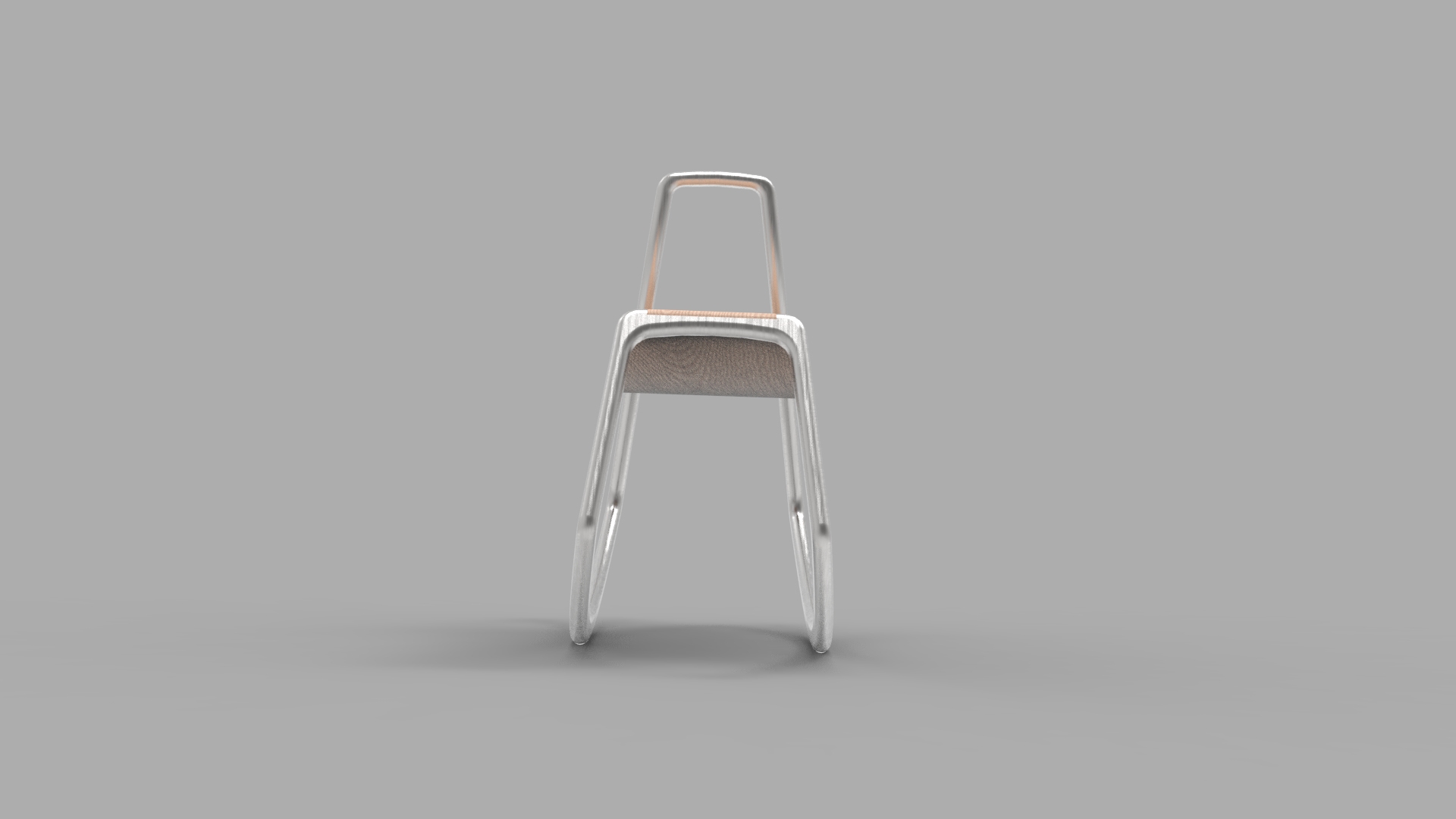
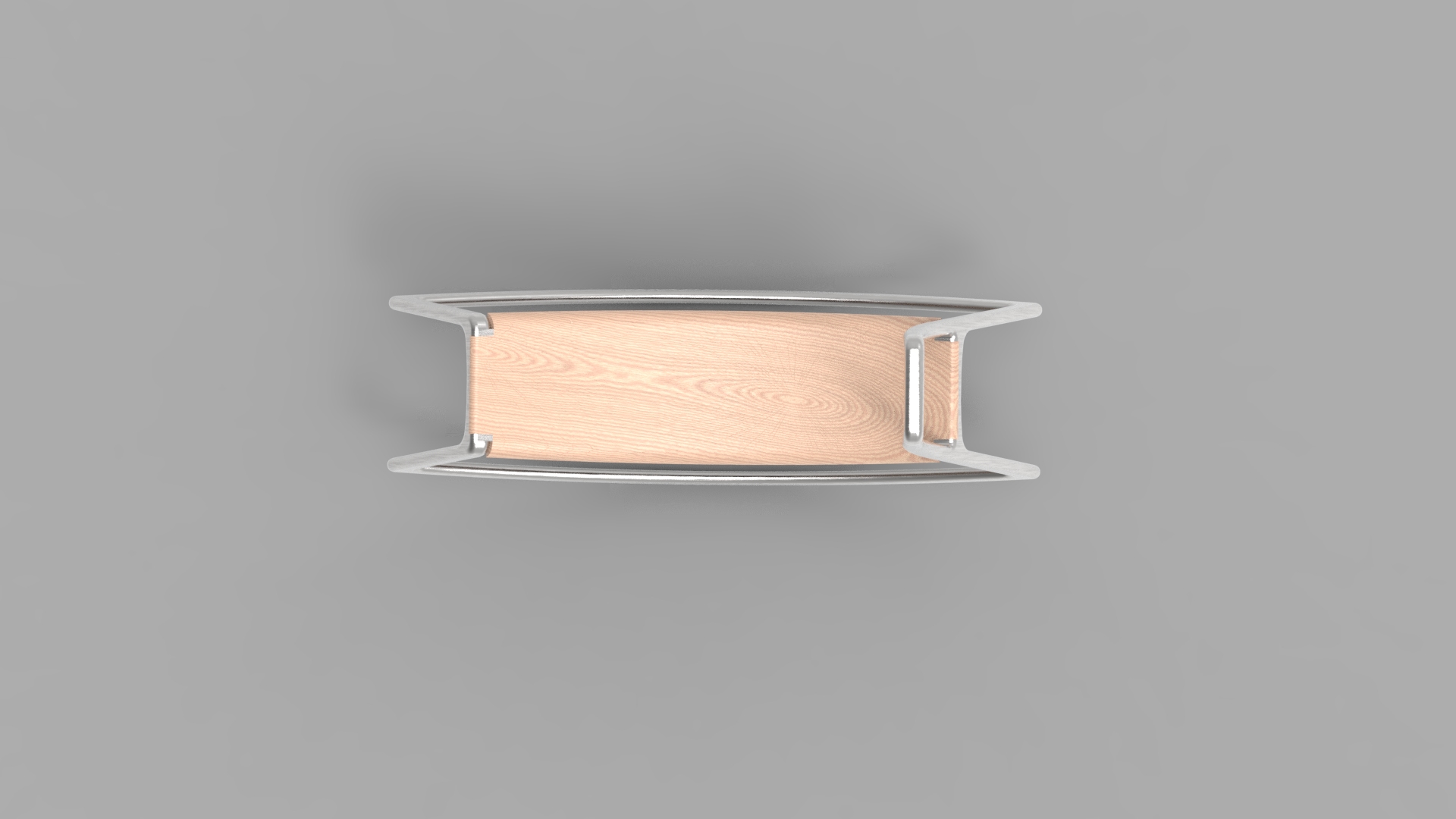
An ergonomics study
The rocking horse for grownups was a project we did in our first ergonomics course in the third semester. I had the intent to create something comfortable that still has an uncommon
design compared to regular rocking horses. The used data is documented in the charts further down in this widget. I took the needed data from my "Ergonomische Datensammlung". I calculated the size of the rocking horse depending on my own height of around 197 cm.
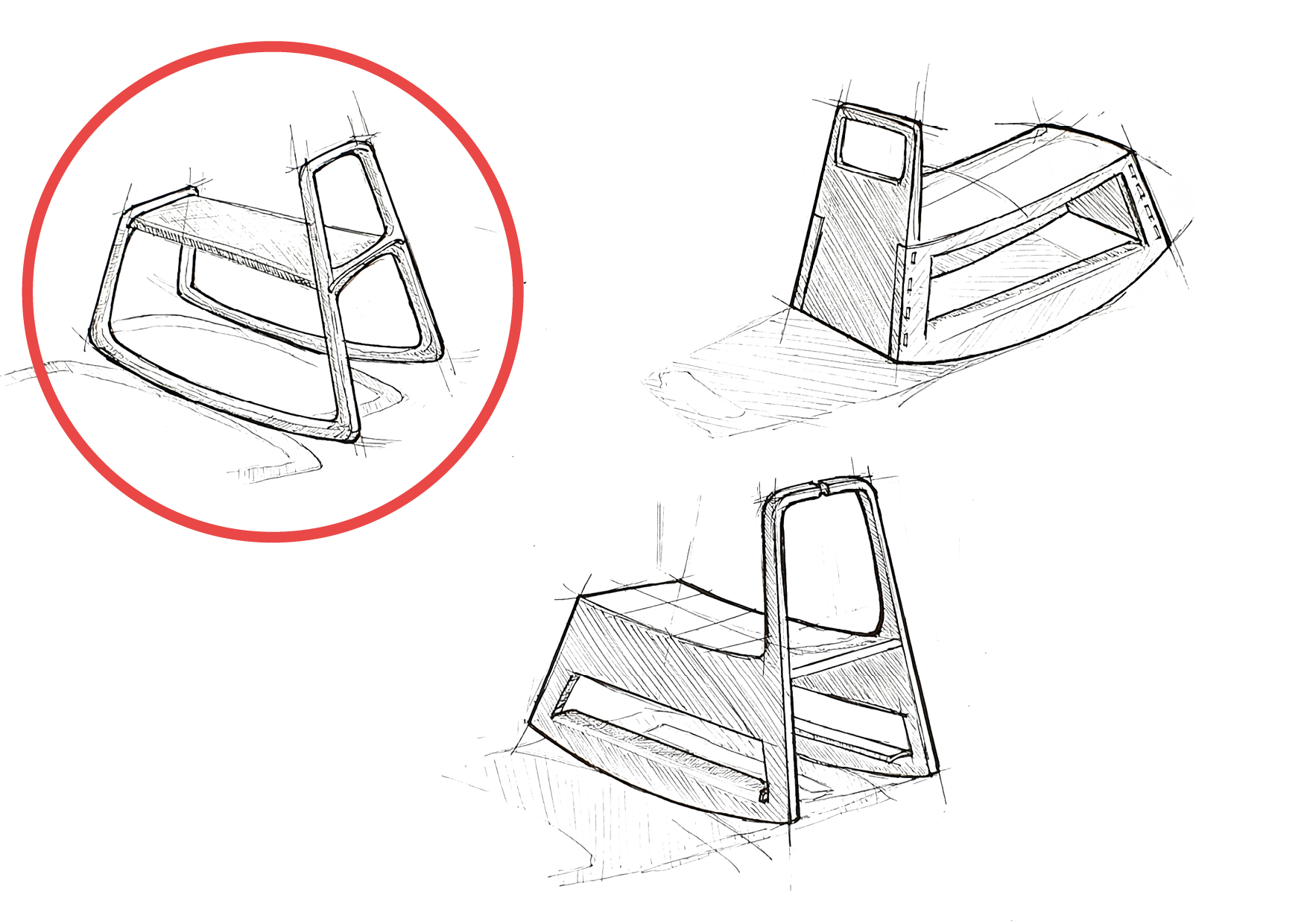
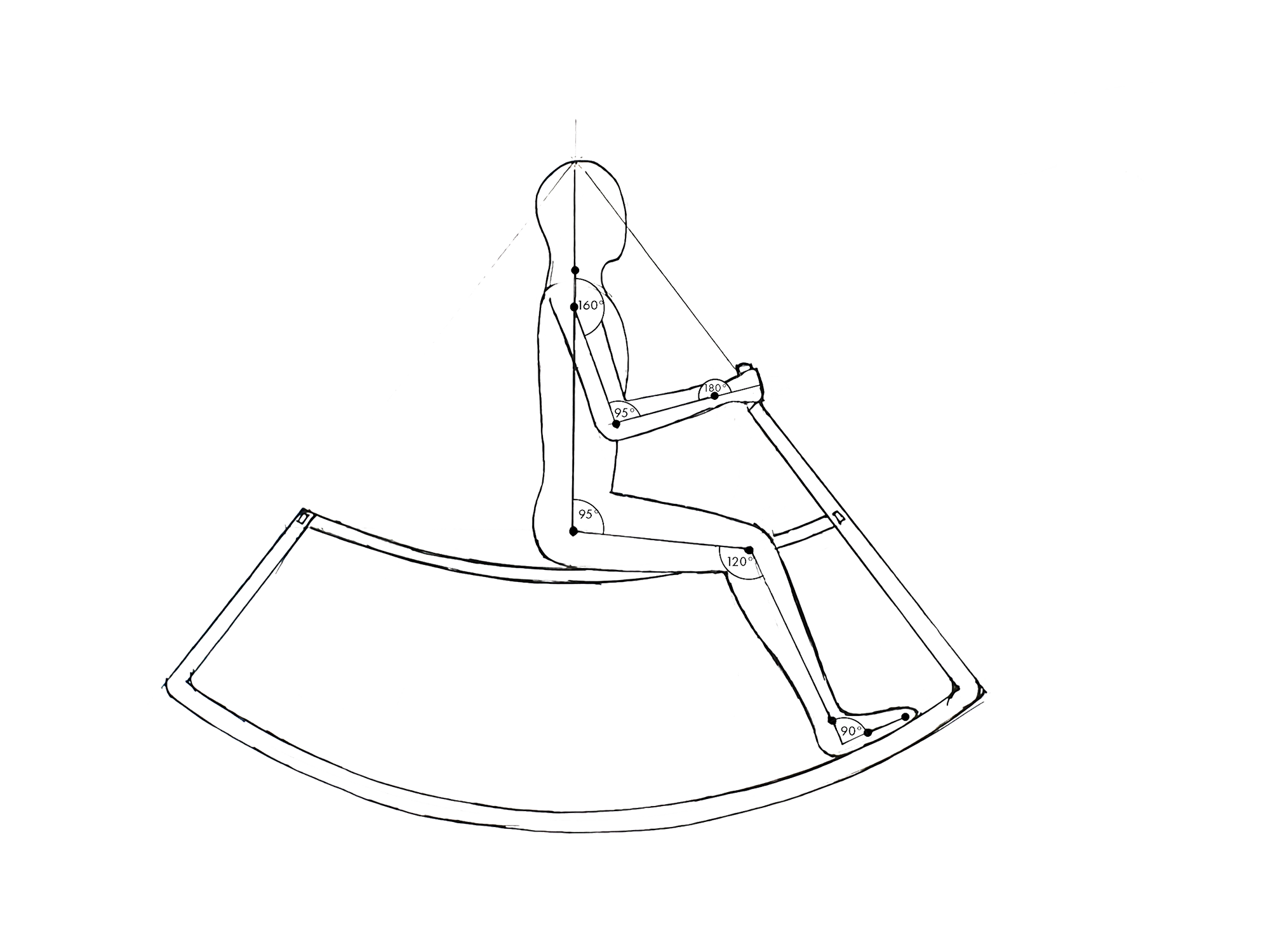
The relevant data
The data inside the chats shows the values that I considered to be the most relevant for the design. I applied the comfortable angles to the sketch above so that I could see if the shape I created was suitable for the given ergonomic data.
.png)
.png)
.png)
Layering
Layering
.png)
.png)
.png)
.png)
.png)
.png)
.png)
.png)
.png)
.png)
.png)
.png)
A basics exercise
"Layers" was an experimental design exercise in the 2nd semester, in which we were supposed to find or create material layering or coatings that we found formally aesthetically interesting, for example for later use in product designs.
I used this exercise to get to grips with the most basic principles of documentary work and the purposeful, reproducible creation of variance. The tables document these approaches. The "layers" are divided from the lowest and first cast (1) to the highest (3) cast.
.png)
.png)
.png)
.png)
.png)
.png)
.png)
.png)
.png)
.png)
.png)
.png)
A basics exercise
"Layers" was an experimental design exercise in the 2nd semester, in which we were supposed to find or create material layering or coatings that we found formally aesthetically interesting, for example for later use in product designs.
I used this exercise to get to grips with the most basic principles of documentary work and the purposeful, reproducible creation of variance. The tables document these approaches. The "layers" are divided from the lowest and first cast (1) to the highest (3) cast.
Opener
Opener
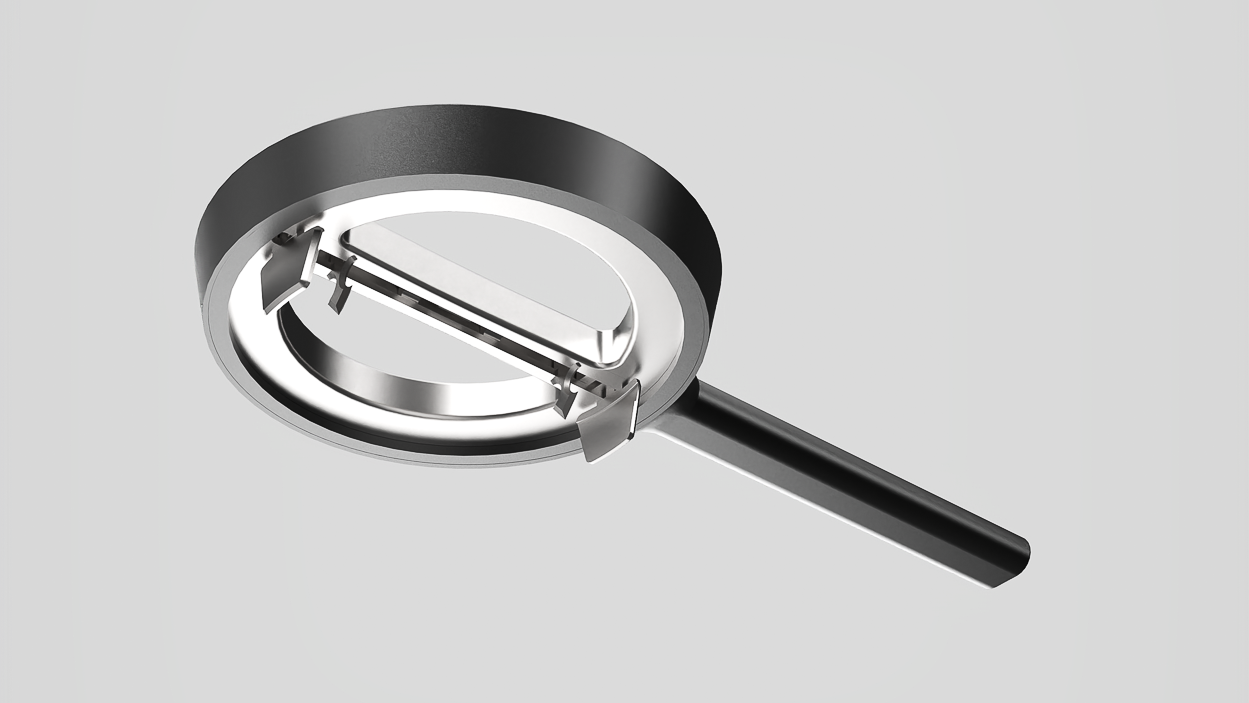
.png)
.png)

Opener for people with limited haptic abilities
I designed this product in the third semester. The task we got for the course was to create an opener that can open a wine bottle, a can, or a corked bottle. This can opener is designed for people with limited haptic abilities. At first, the opener is placed on top of the can with the blades facing downward. By spinning the wheel on top of the opener, the distance between the blades can be set as necessary. Then the blades are pushed into the can. By pushing and dragging the grip backwards, a ratchet wrench-mechanism is used to push the two blades in a circular movement through the can lid.
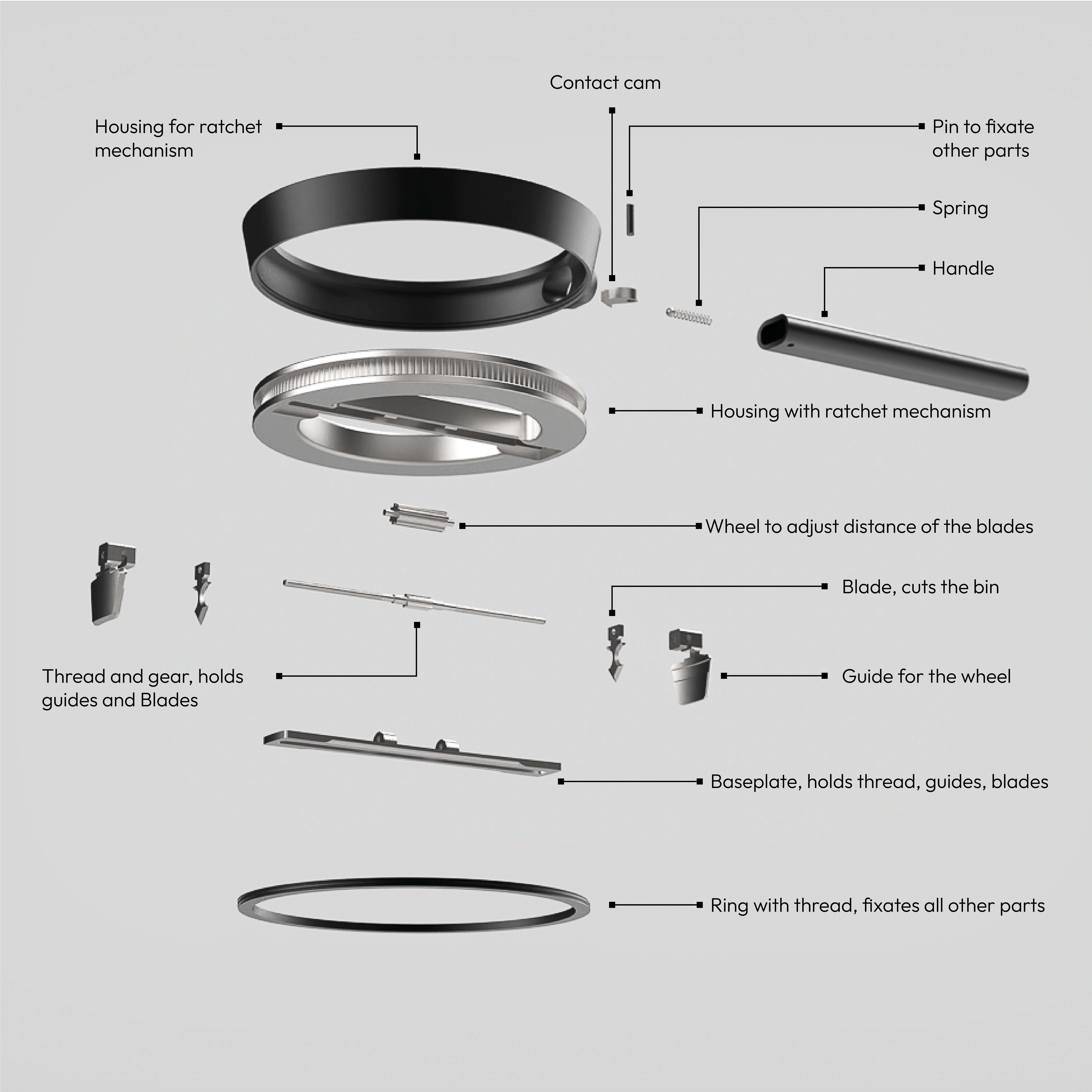
Iterations
After sketching, I usually use prototypes to find problems and solutions within my designs. I created a modular prototype of the opener to check which grip angle and/or grip angles in general are most useful for my design. After testing all of them, the straight one seemed to be the best choice.
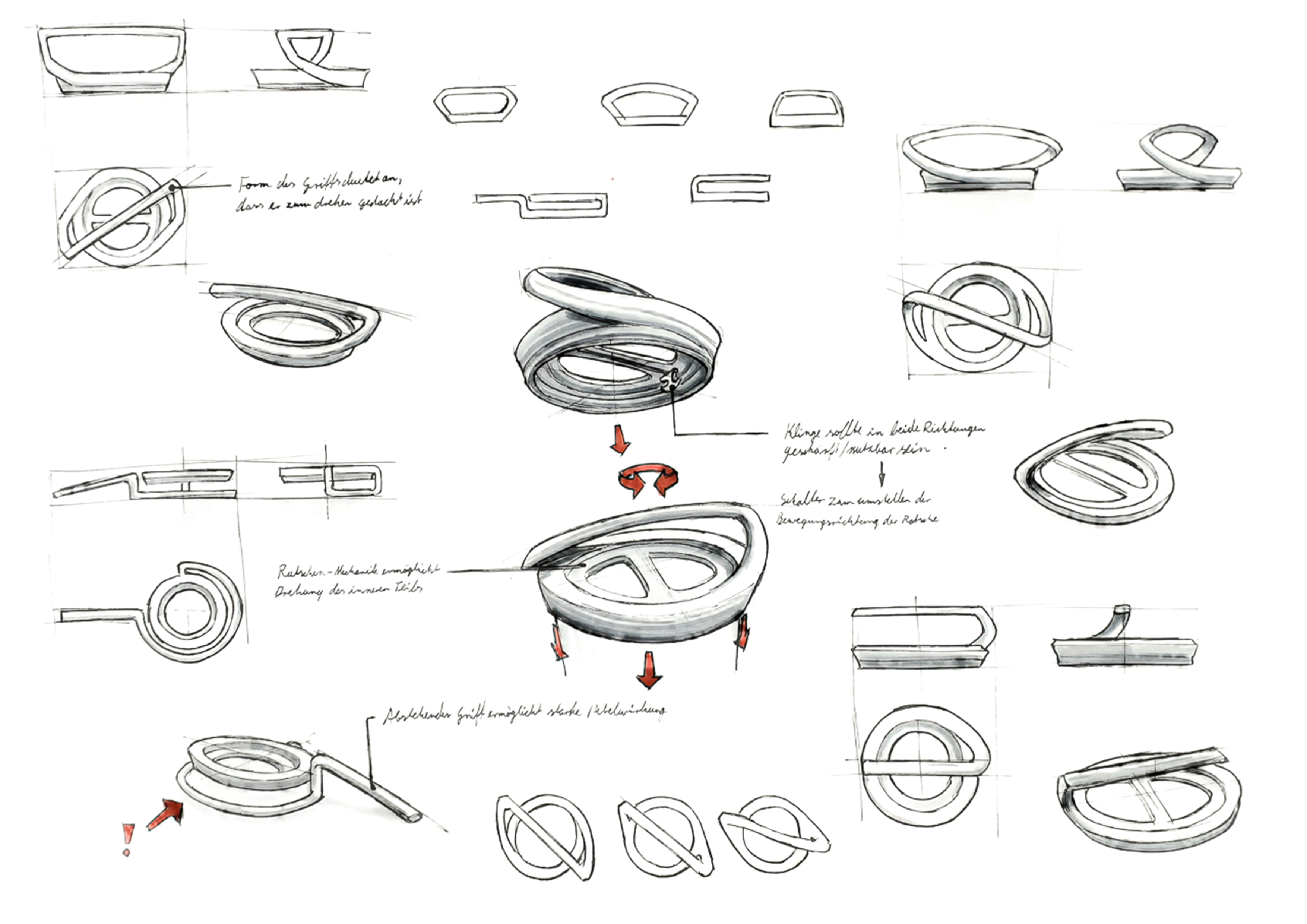
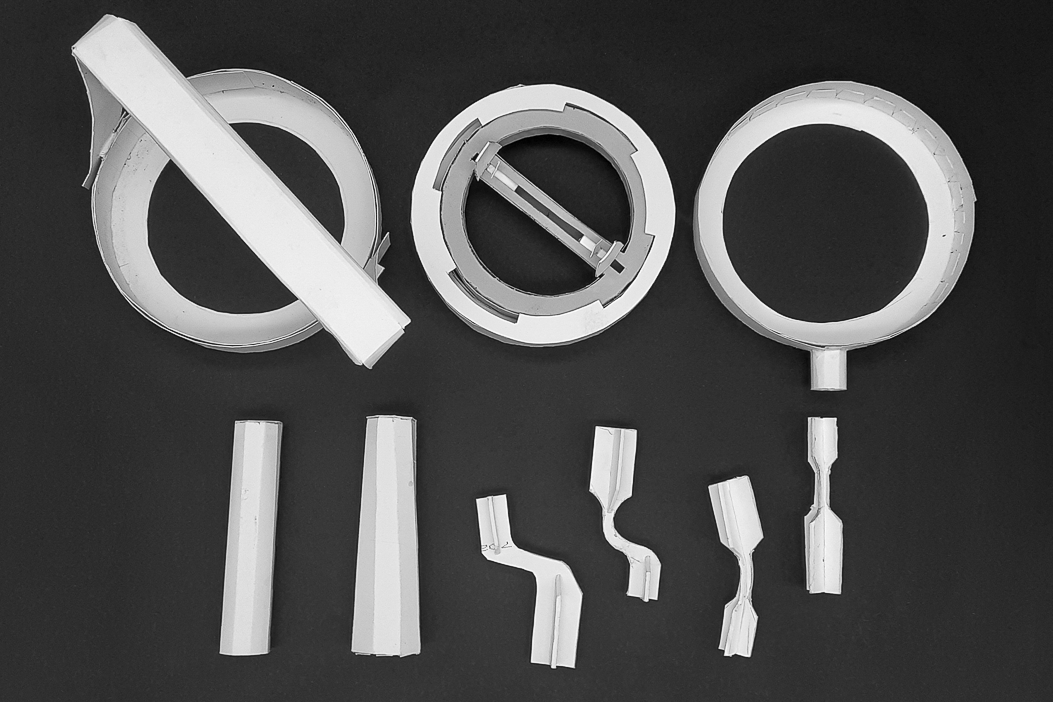
.png)
.png)
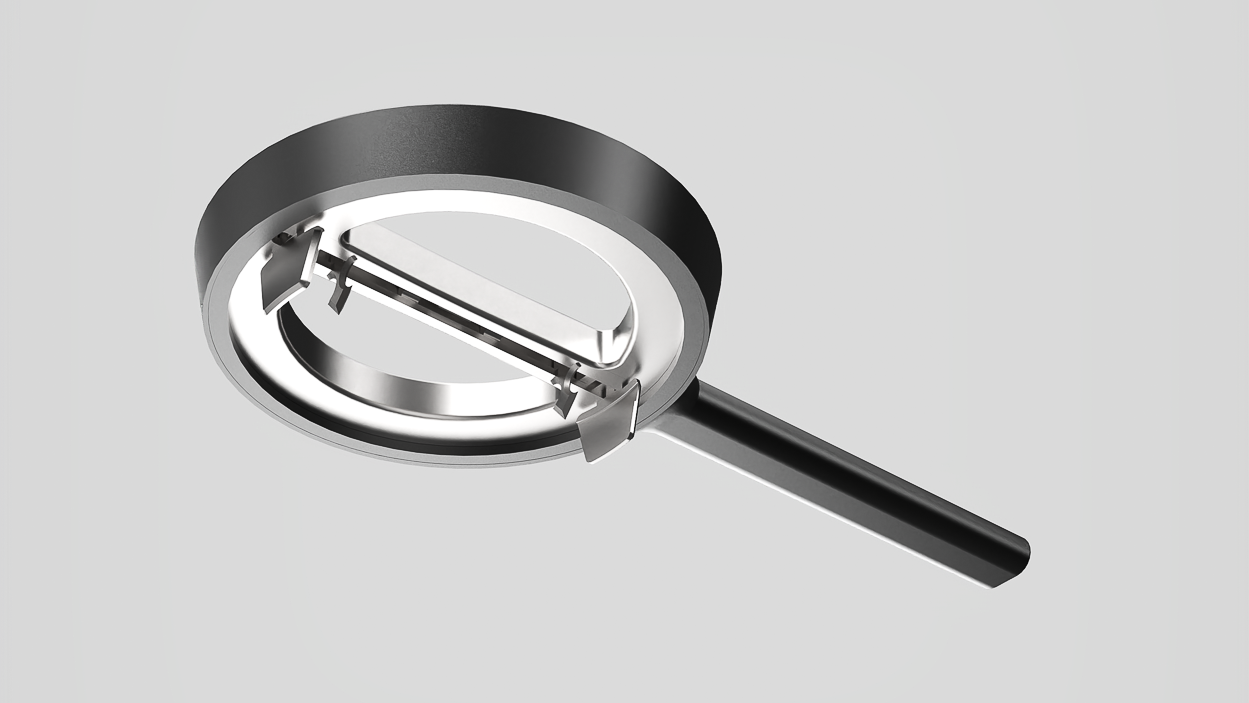
.png)
.png)

Opener for people with limited haptic abilities
I designed this product in the third semester. The task we got for the course was to create an opener that can open a wine bottle, a can, or a corked bottle. This can opener is designed for people with limited haptic abilities. At first, the opener is placed on top of the can with the blades facing downward. By spinning the wheel on top of the opener, the distance between the blades can be set as necessary. Then the blades are pushed into the can. By pushing and dragging the grip backwards, a ratchet wrench-mechanism is used to push the two blades in a circular movement through the can lid.
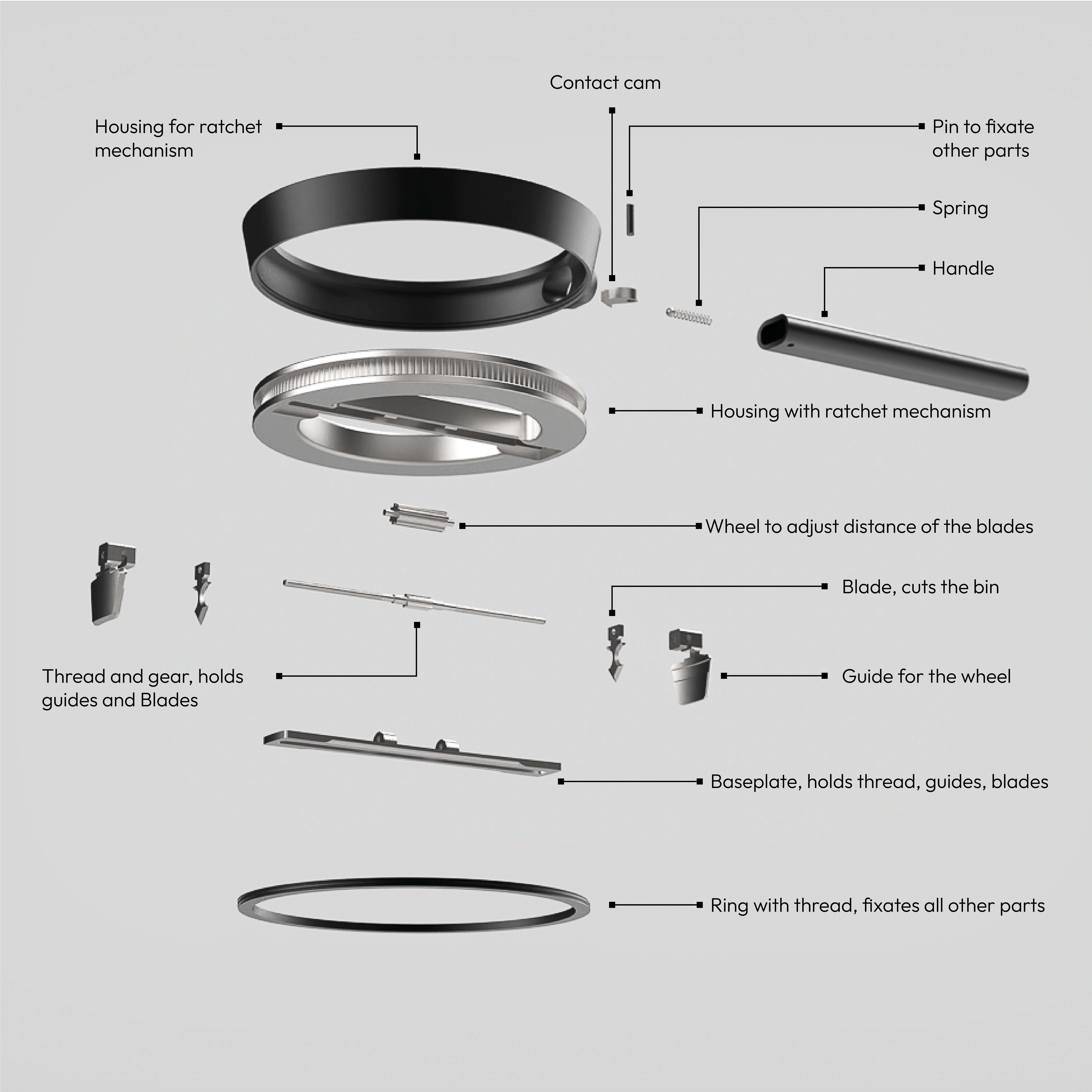
Iterations
After sketching, I usually use prototypes to find problems and solutions within my designs. I created a modular prototype of the opener to check which grip angle and/or grip angles in general are most useful for my design. After testing all of them, the straight one seemed to be the best choice.
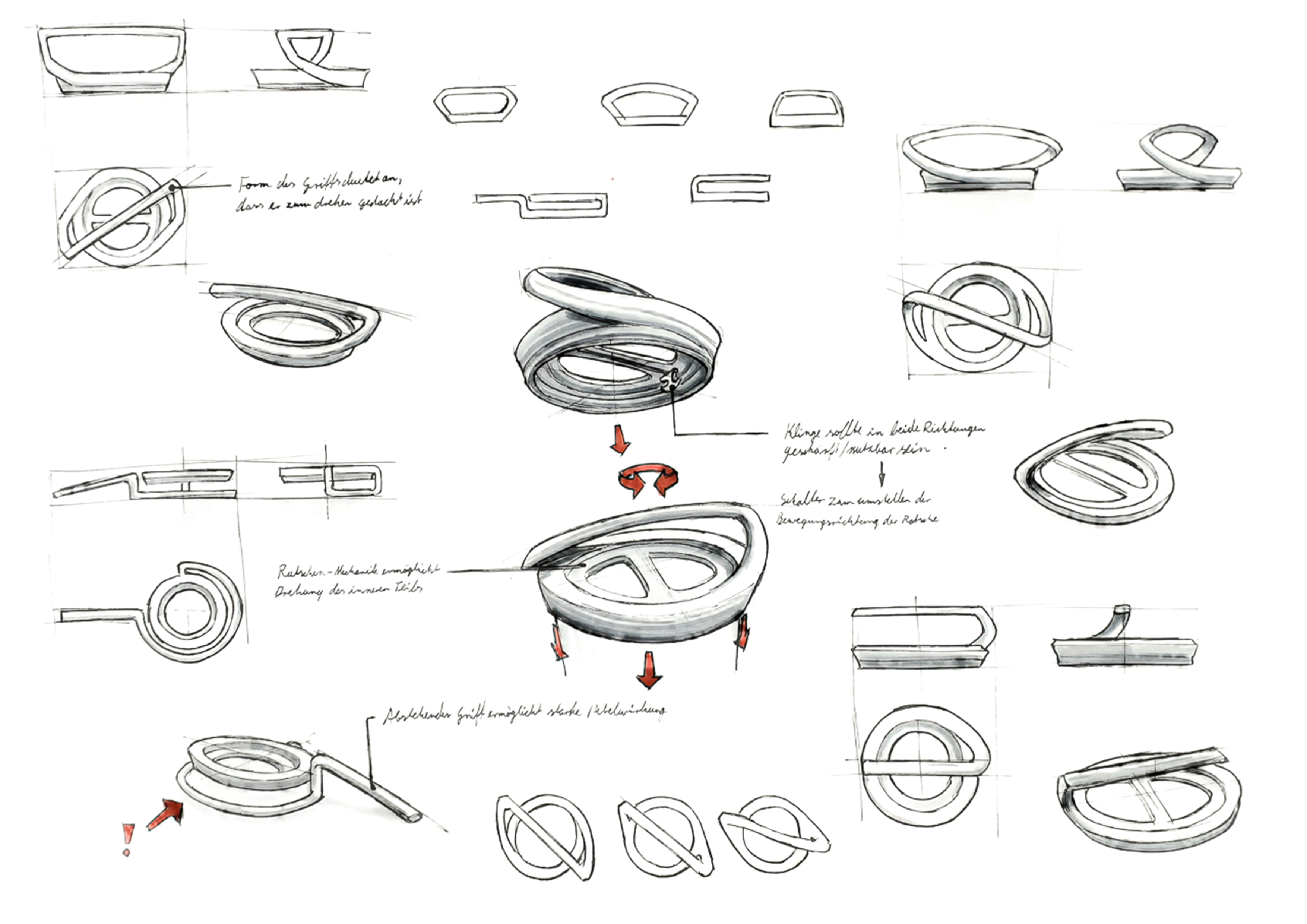
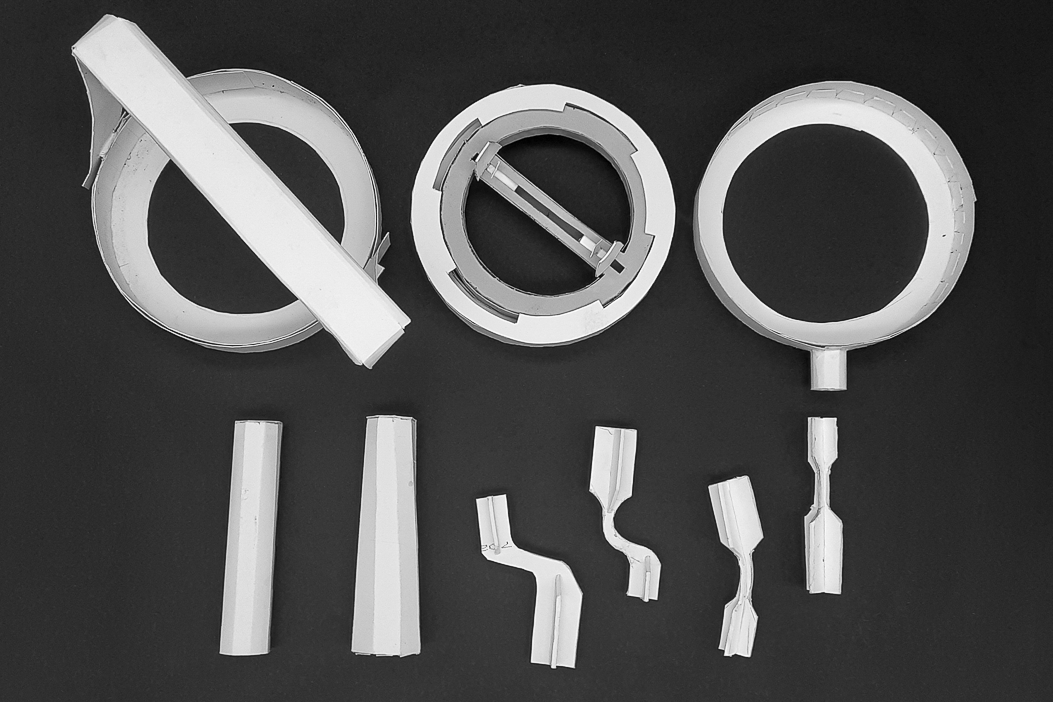
.png)
.png)
The Microcosm
I had the idea for "The Microcosm" in 2021. I'm fascinated by the drawings of Ernst Haeckel and wanted to create something inspired by his artworks. Originally, I had the intent to create a NFT collection of 50 to 150 animations of shapes as they can be found in the skeletons of radiolarias. In the process, I created 20 3D models and a dozen procedural materials. I later decided not to upload the animations as a NFT, as it was much more of an exercise in the basics of modeling and sculpting in Blender. This window shows 12 of the over 60 animations I made.
The Microcosm
I had the idea for "The Microcosm" in 2021. I'm fascinated by the drawings of Ernst Haeckel and wanted to create something inspired by his artworks. Originally, I had the intent to create a NFT collection of 50 to 150 animations of shapes as they can be found in the skeletons of radiolarias. In the process, I created 20 3D models and a dozen procedural materials. I later decided not to upload the animations as a NFT, as it was much more of an exercise in the basics of modeling and sculpting in Blender. This window shows 12 of the over 60 animations I made.
Fungi Bottle
Fungi Bottle
A possible usecase for mycelium
This product design is related to the project "Fungi Studies." My intention was to design an example-product that shows a potential use case for mycelium. The result is the fungus bottle. It uses the good insulation properties of mycelium in the form of a multipurpose bottle with thermos properties. Additionally, I wanted some parts to fulfill multiple purposes, for example, being usable as plates and cutlery.
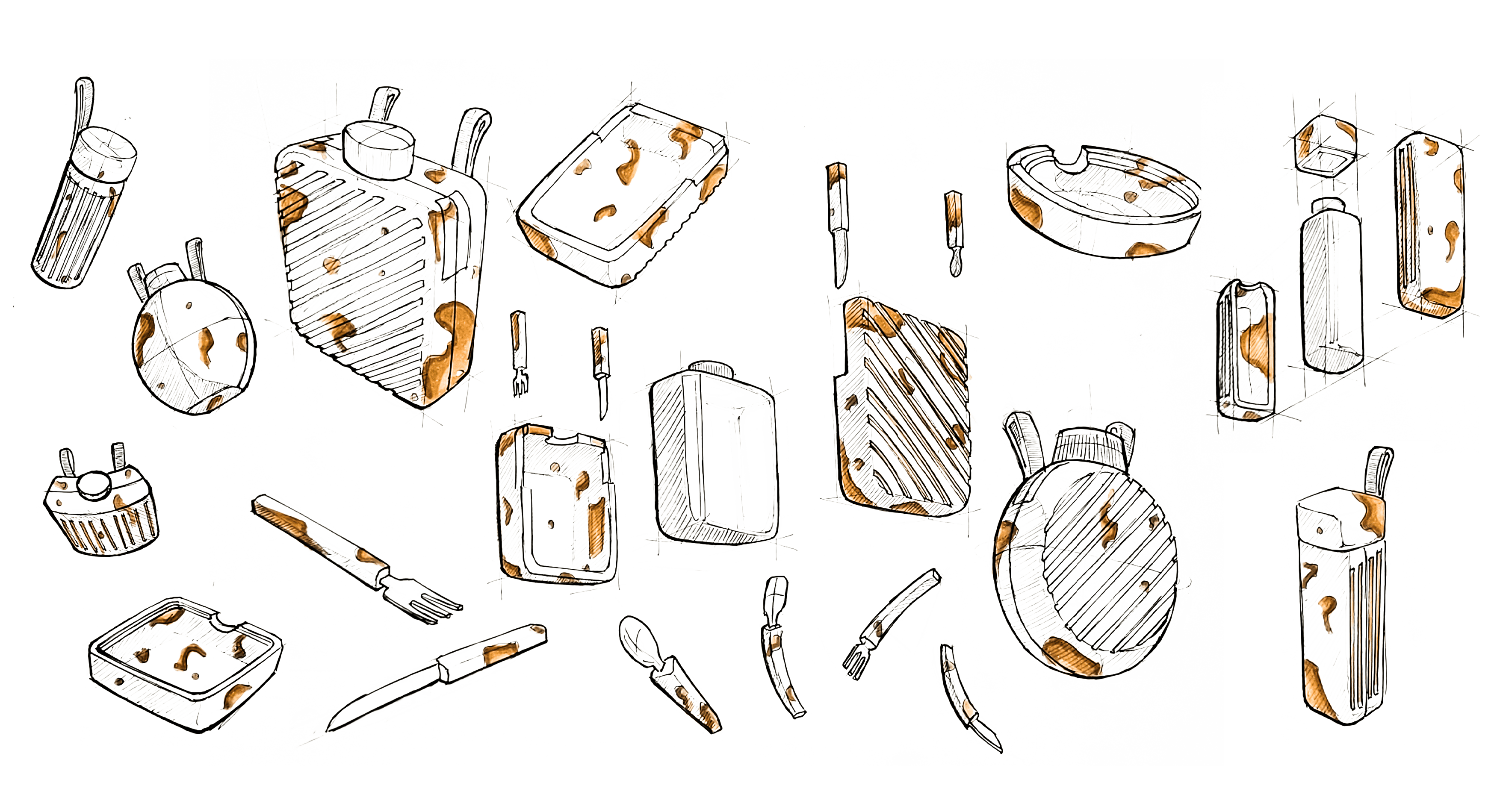
Iterations
I started out with a lot of ideas for what to do with the mycelium, from bird houses that can be left in the woods to decay automatically over fireworks casings to modular bobby cars or balance bikes to grow at home. After the consultations, I decided to realize the concept of a mycelium-based thermos flask. I made two shapes of paper prototypes in four different sizes for volumes of 0.75 liters to 1.25 liters. The final 1:1 paper prototype is shown in the pictures below and has a capacity of 0.75 liters.
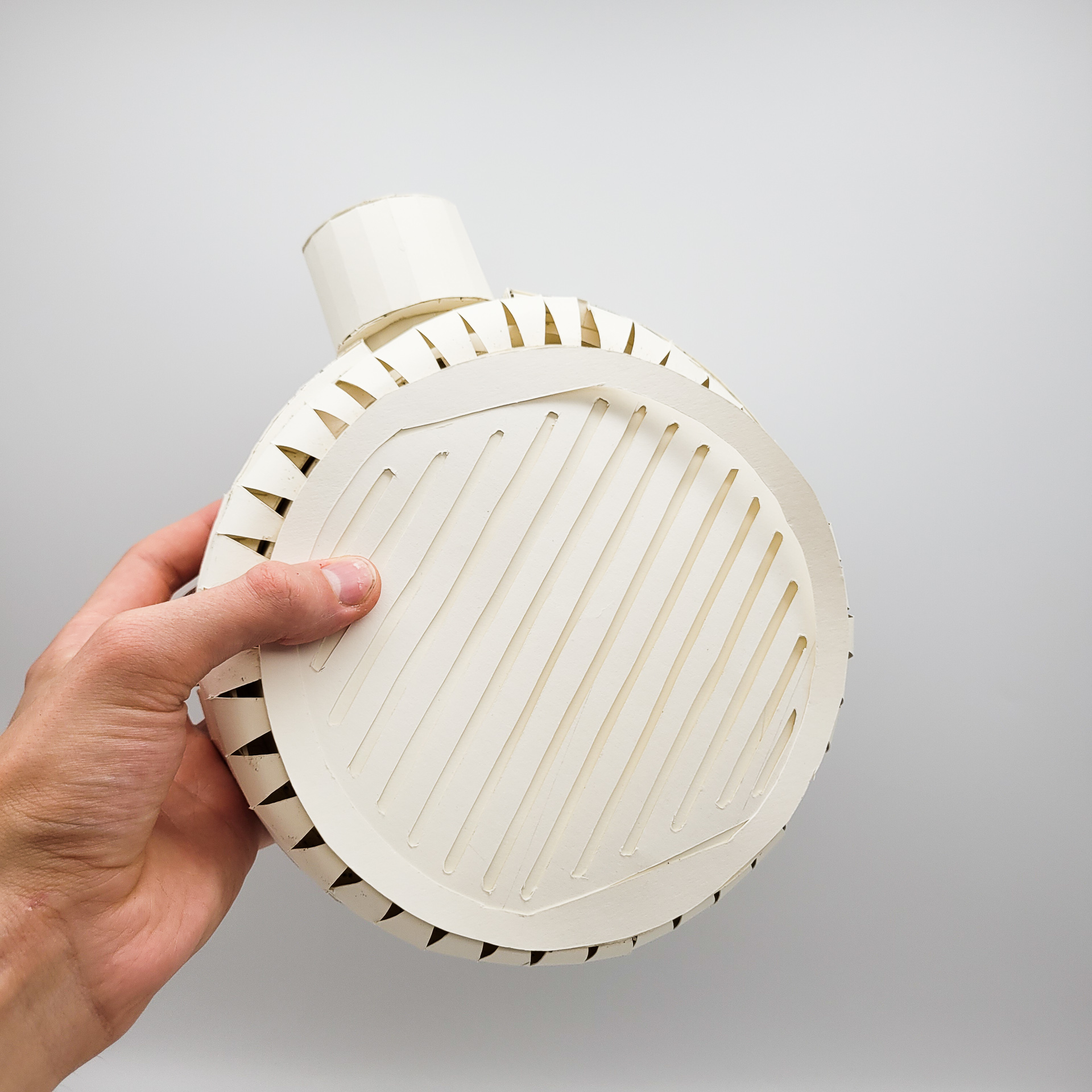
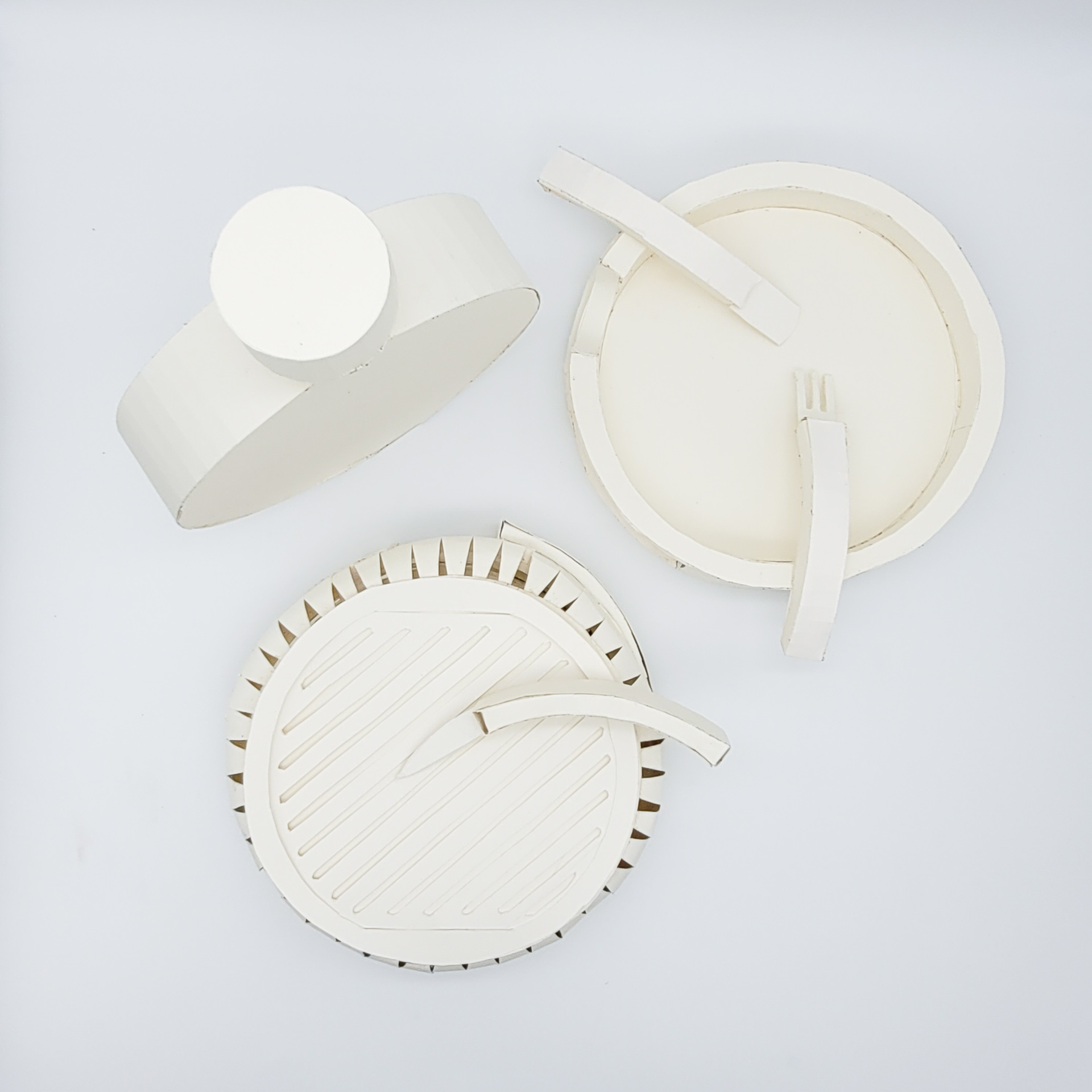
.jpg)
Final prototype
The final 1:1 prototype is printed from PLA. Please remember that the bottle is only an example concept, and therefore no explicit tests were made regarding the durability, removable parts, connections between them, or the parts that would need to be placed inside the culture medium while the mycelium is growing to hold.
.jpg)
.jpg)
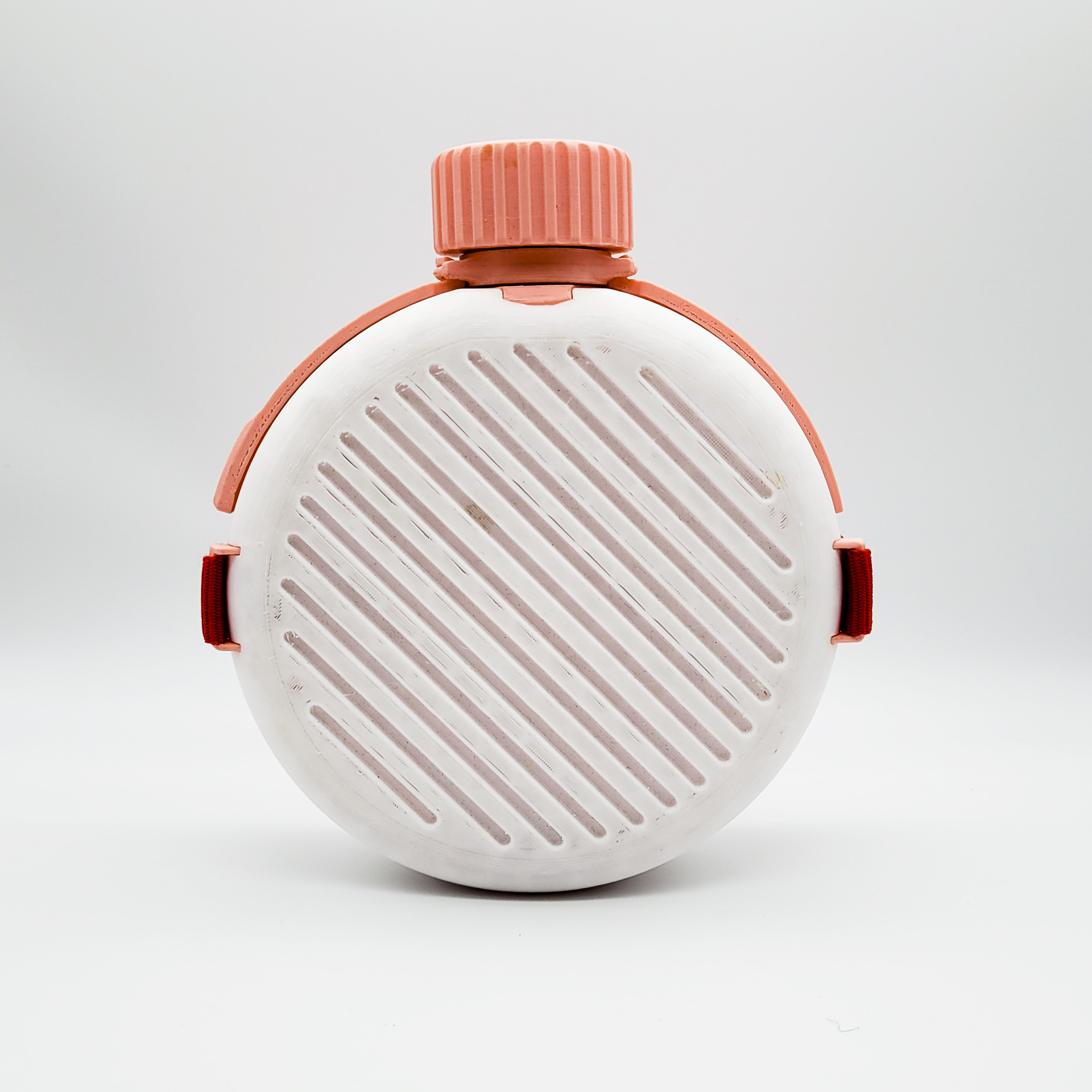
A possible usecase for mycelium
This product design is related to the project "Fungi Studies." My intention was to design an example-product that shows a potential use case for mycelium. The result is the fungus bottle. It uses the good insulation properties of mycelium in the form of a multipurpose bottle with thermos properties. Additionally, I wanted some parts to fulfill multiple purposes, for example, being usable as plates and cutlery.
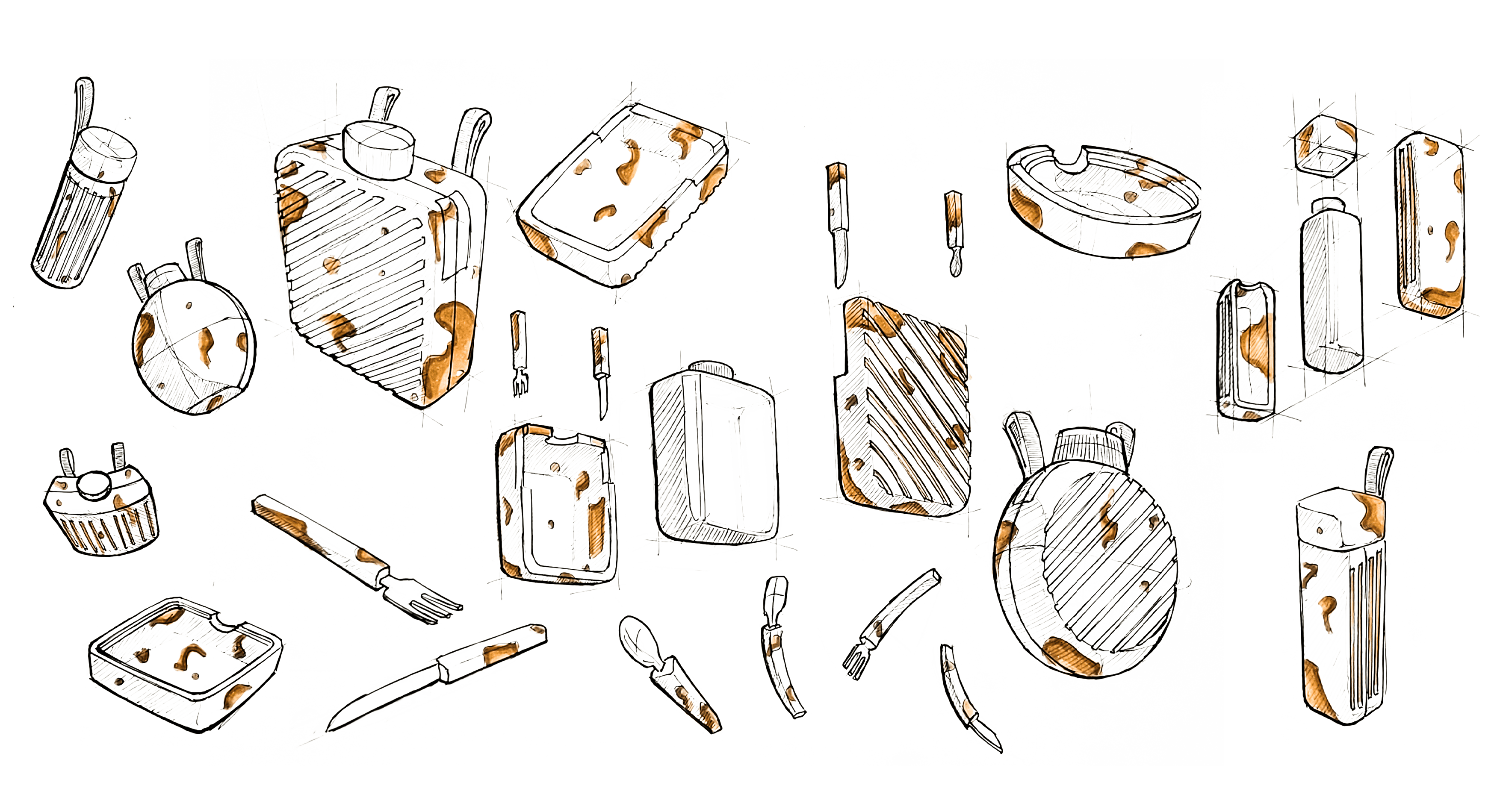
Iterations
I started out with a lot of ideas for what to do with the mycelium, from bird houses that can be left in the woods to decay automatically over fireworks casings to modular bobby cars or balance bikes to grow at home. After the consultations, I decided to realize the concept of a mycelium-based thermos flask. I made two shapes of paper prototypes in four different sizes for volumes of 0.75 liters to 1.25 liters. The final 1:1 paper prototype is shown in the pictures below and has a capacity of 0.75 liters.
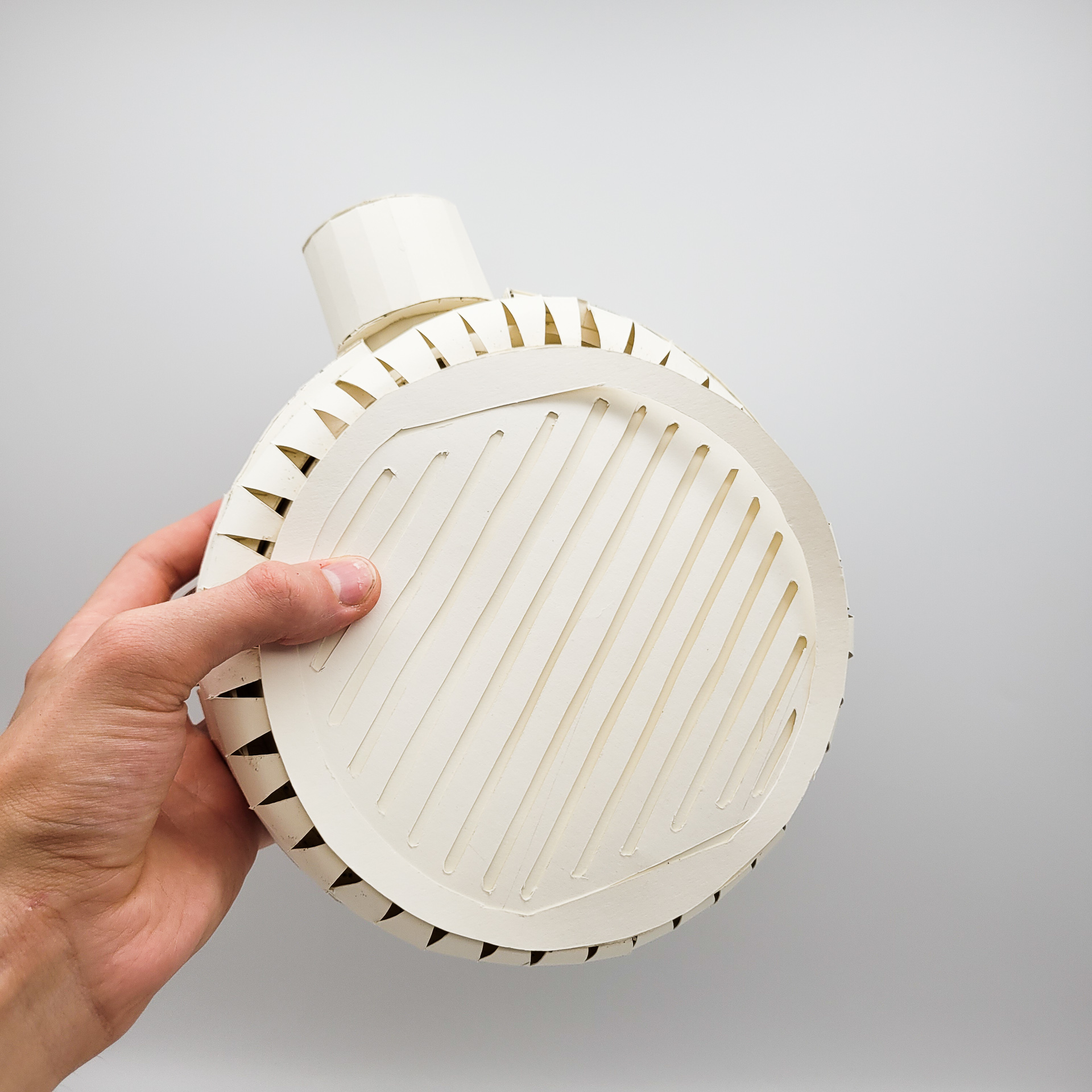
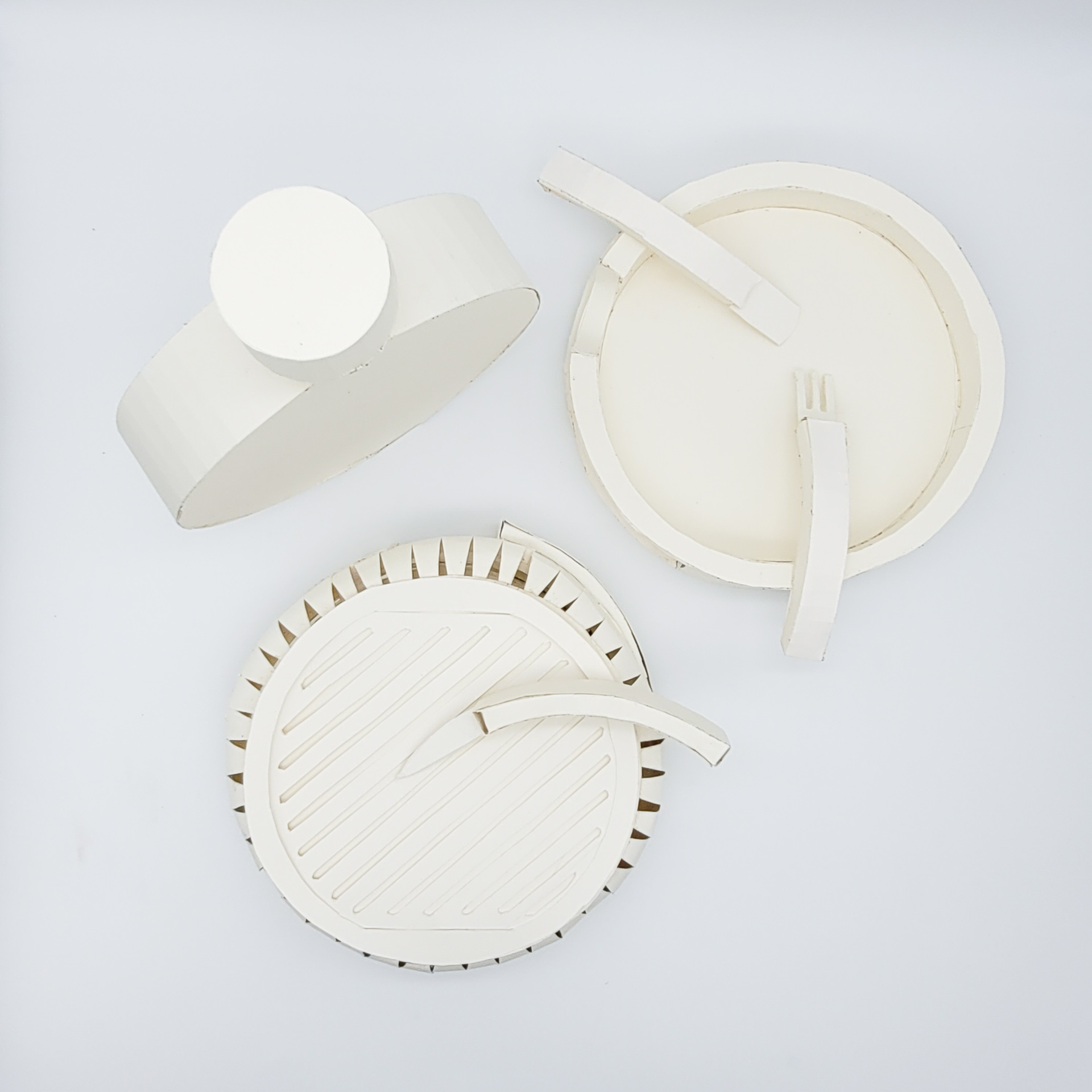
.jpg)
Final prototype
The final 1:1 prototype is printed from PLA. Please remember that the bottle is only an example concept, and therefore no explicit tests were made regarding the durability, removable parts, connections between them, or the parts that would need to be placed inside the culture medium while the mycelium is growing to hold.
.jpg)
.jpg)
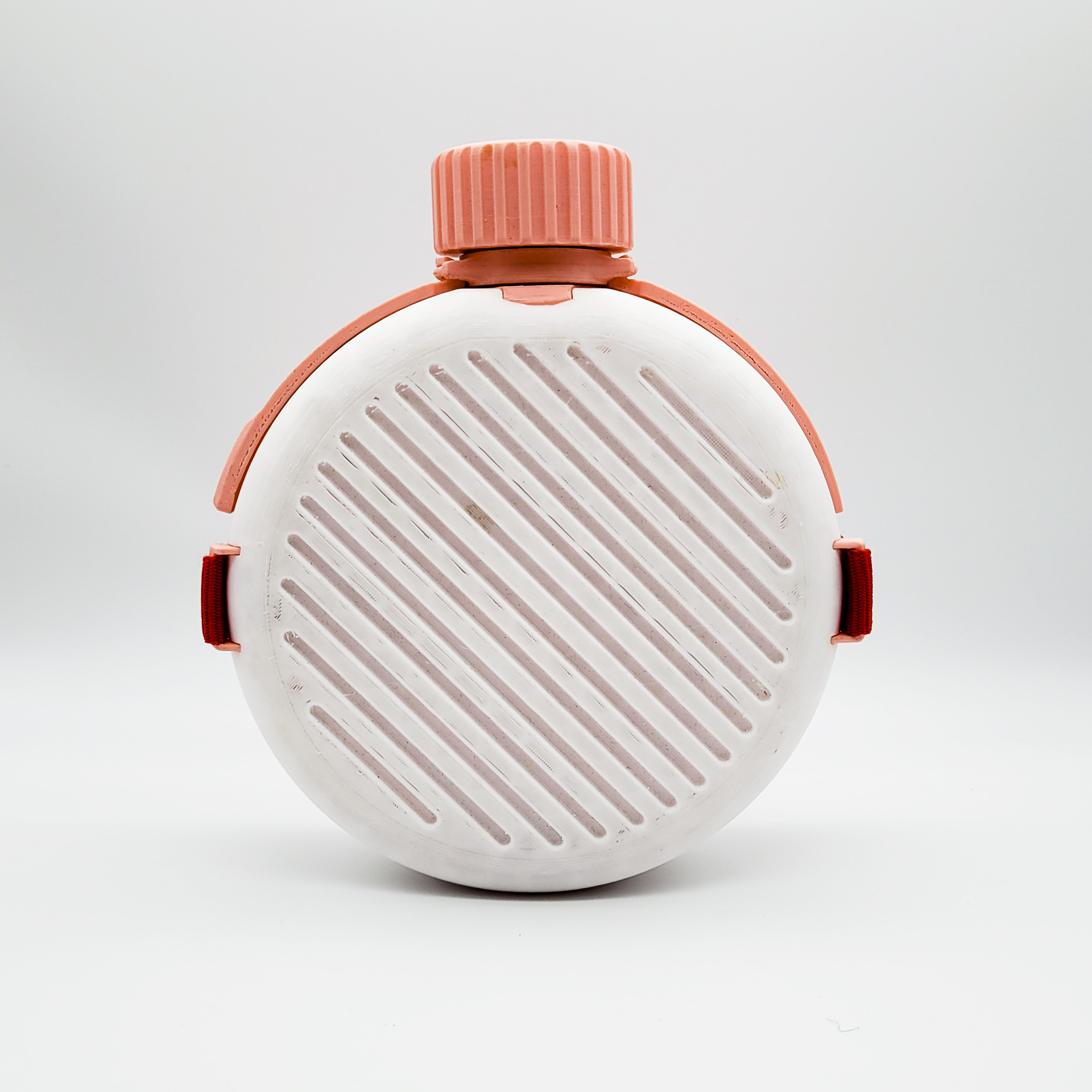
Scoby Samples
Scoby Samples
.png)
.png)
.png)
.png)
.png)
.png)
.png)
.png)
.png)
.png)
.png)
.png)
.png)
.png)
.png)
.png)
.png)
.png)
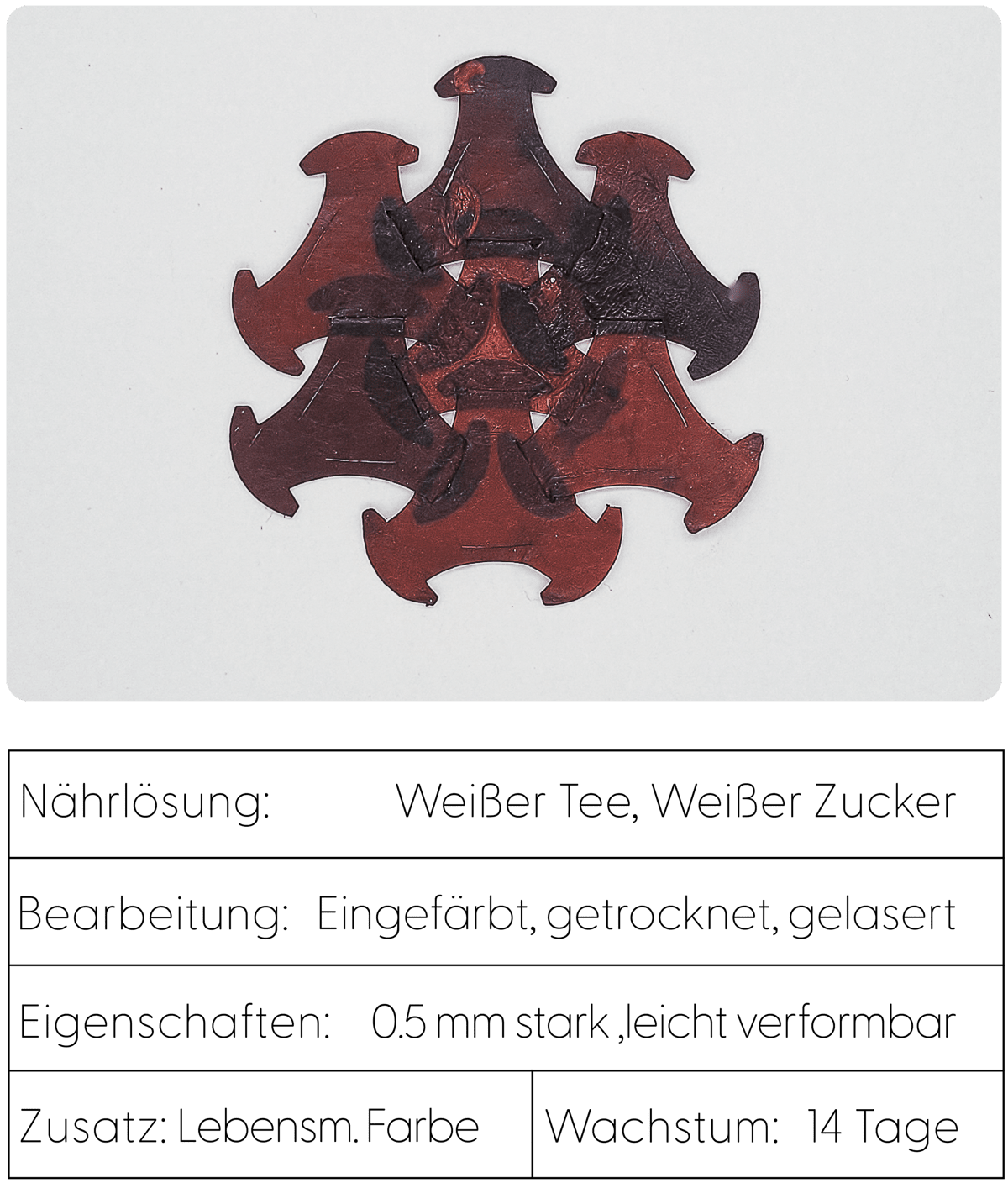
.png)
.png)
.png)
What is SCOBY?
SCOBY (Symbiotic Culture of Bacteria and Yeast) is a so-called "tea fungus culture" made up of bacteria and yeast, held together by cellulose. Most people are probably familiar with the drink Kombucha, which is fermented by the SCOBY during its growth in tea enriched with sugar. Kombucha has been known in Asia for over 2000 years as a beverage with healing properties. The yeast converts the sugar into alcohol, which the microorganisms in Kombucha process along with the nutrients of the tea into organic acids, dietary fibers, vitamins, and some other components. During this process, the SCOBY requires oxygen, which is why it floats on the surface. As it is supplied with nutrients, thin layers form on the SCOBY, which grow together and make it thicker. When dried, SCOBY can be used, for example, as an easily produced and biodegradable leather substitute.
The scoby experiments and resulting samples were actually a result of the "Fungi Studies" experiment. Therefore, the evaluation is pretty similar. The focus we had when analyzing the scoby samples was actually not only on the way it can be worked during but also after the growth process. In contrast to mycelium, scoby can be modified even further after the growth process by stirring, dying, or heat treatment. Another major advantage against mycelium when growing scoby was that it was not necessary to sterilize all the tools and vessels that are used for preparing and processing the scoby samples.
.jpg)
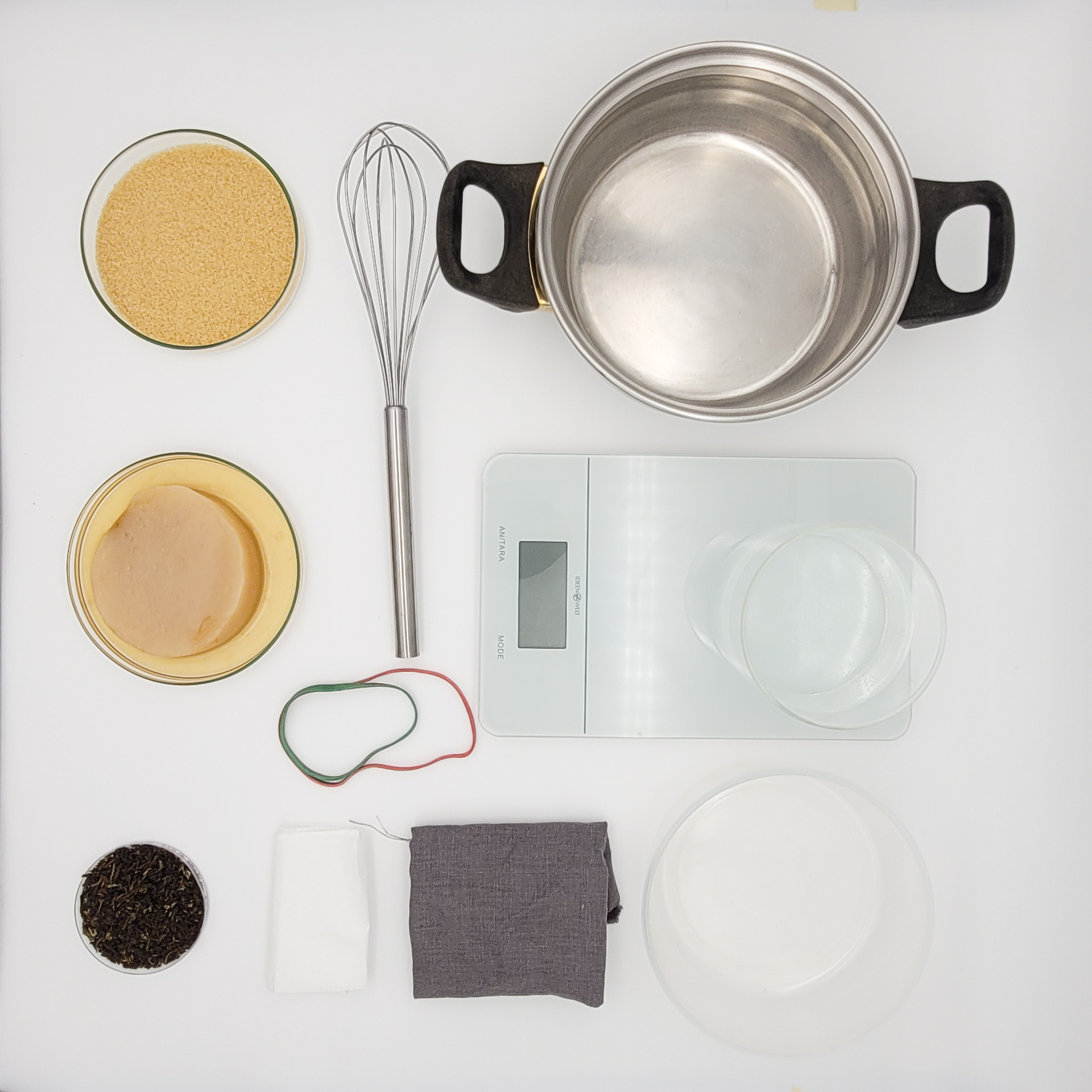
Preparation
Scoby can easily be grown at home. However, there were some circumstances that needed to be considered before we started growing our first cultures. For example, the temperature. 22 °C to 26 °C are considered to be the best temperatures for breeding healthy scoby. Below this temperature, the growth takes longer; above, it grows significantly faster. Next are the vessels in which the scoby is cultivated. They should be made of stainless steel, enamel, glass, or possibly plastic. Even if the tools and vessels to work with don't need to be sterilized, they need to be cleaned properly with dish soap, and afterwards everything should be rinsed with water until no residues of the soap remain.
The vessel in which the scoby grows should always be well covered with a breathable cloth to protect against contamination. In the summer, this also protects against fruit fly larvae that can settle in the scoby. In addition, the tea used must be organic. The scoby can't process flavored teas and grows poorly, or, in the worst case, not at all on them. The suitable types of tea are nevertheless very diverse. Even coffee is suitable as a nutrient medium. Some materials are needed to grow it anyway:
• Cooking pot
• Scale
• Containers (various)
• Kitchen towels or similar
• Whisk
• Rubber bands
• (Brown) Sugar
• Water
• Tea
• Tea bags
• Living SCOBY culture with Kombucha.
The samples made from puréed scoby were created as an experiment to make something out of the remnants of the scobys we inevitably produced. Some of the ingredients for these material samples were taken from traditional bioplastic recipes. The necessary equipment was as follows:
• some water
• Scoby cultures (preferably several 100 g)
• Binding agents (Agar Agar, Gelatin, Alginate)
• Food coloring
• Hand blender
• Container for the Scoby (and for pureeing)
• Oven-proof, flat containers
• Glycerin
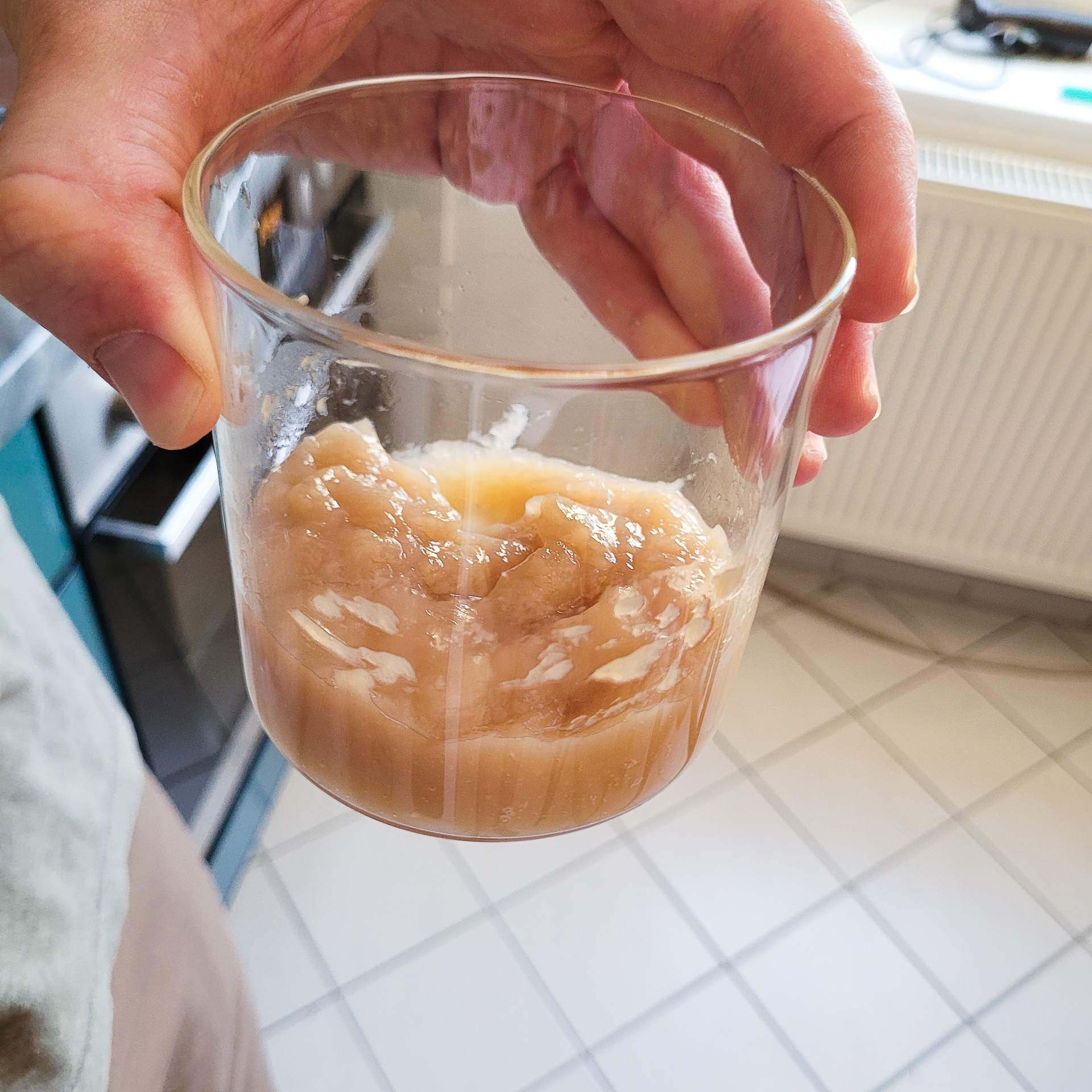
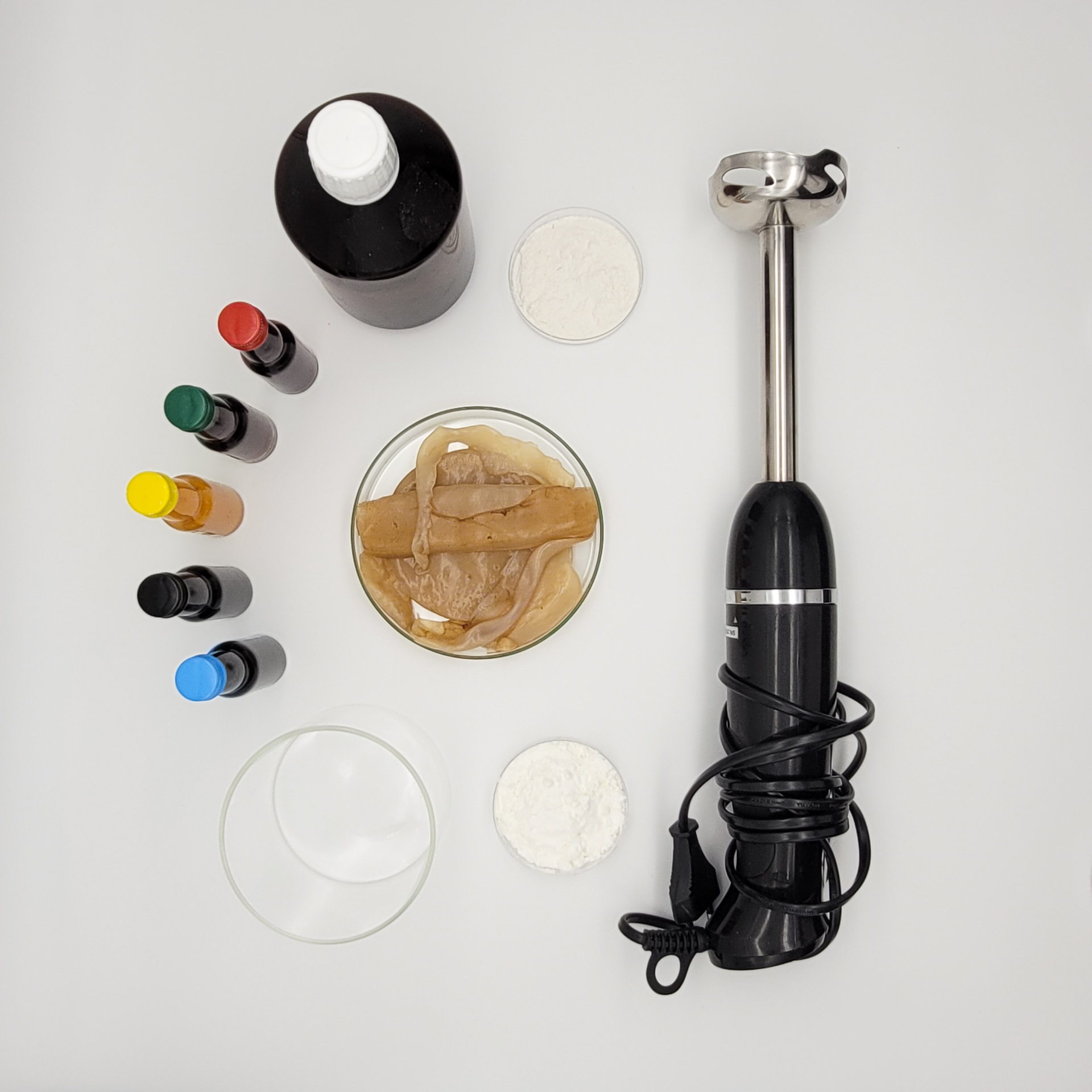
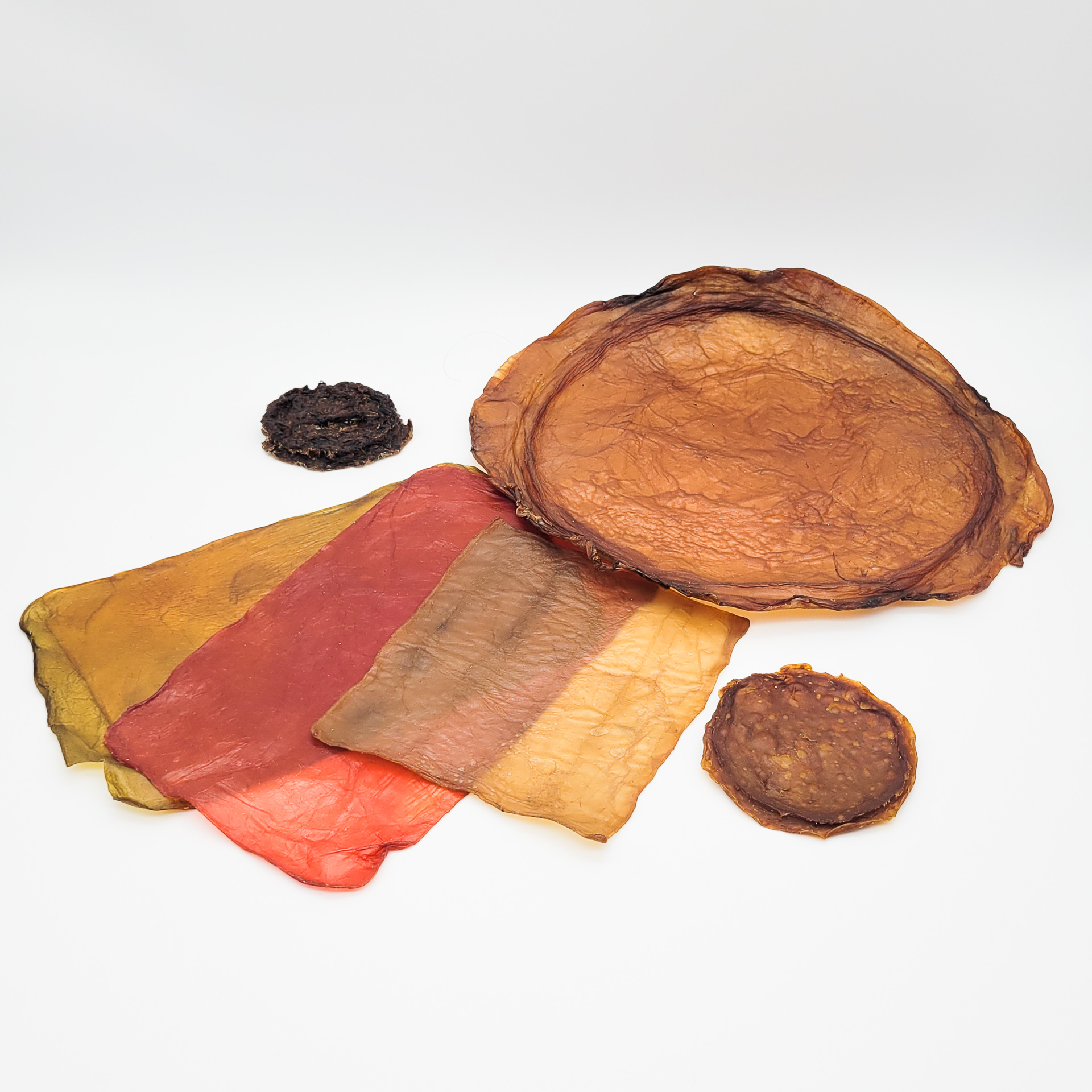
Further exploration
Even though the scoby samples were a "side product" of the "Fungi Studies" Project, the material seemed to have much more potential for exploration than mycelium. Therefore, we initiated "Project SCOBY" with one of our professors, Cora Gebauer, to explore ways of growing scoby and the possible use cases.
.png)
.png)
.png)
.png)
.png)
.png)
.png)
.png)
.png)
.png)
.png)
.png)
.png)
.png)
.png)
.png)
.png)
.png)
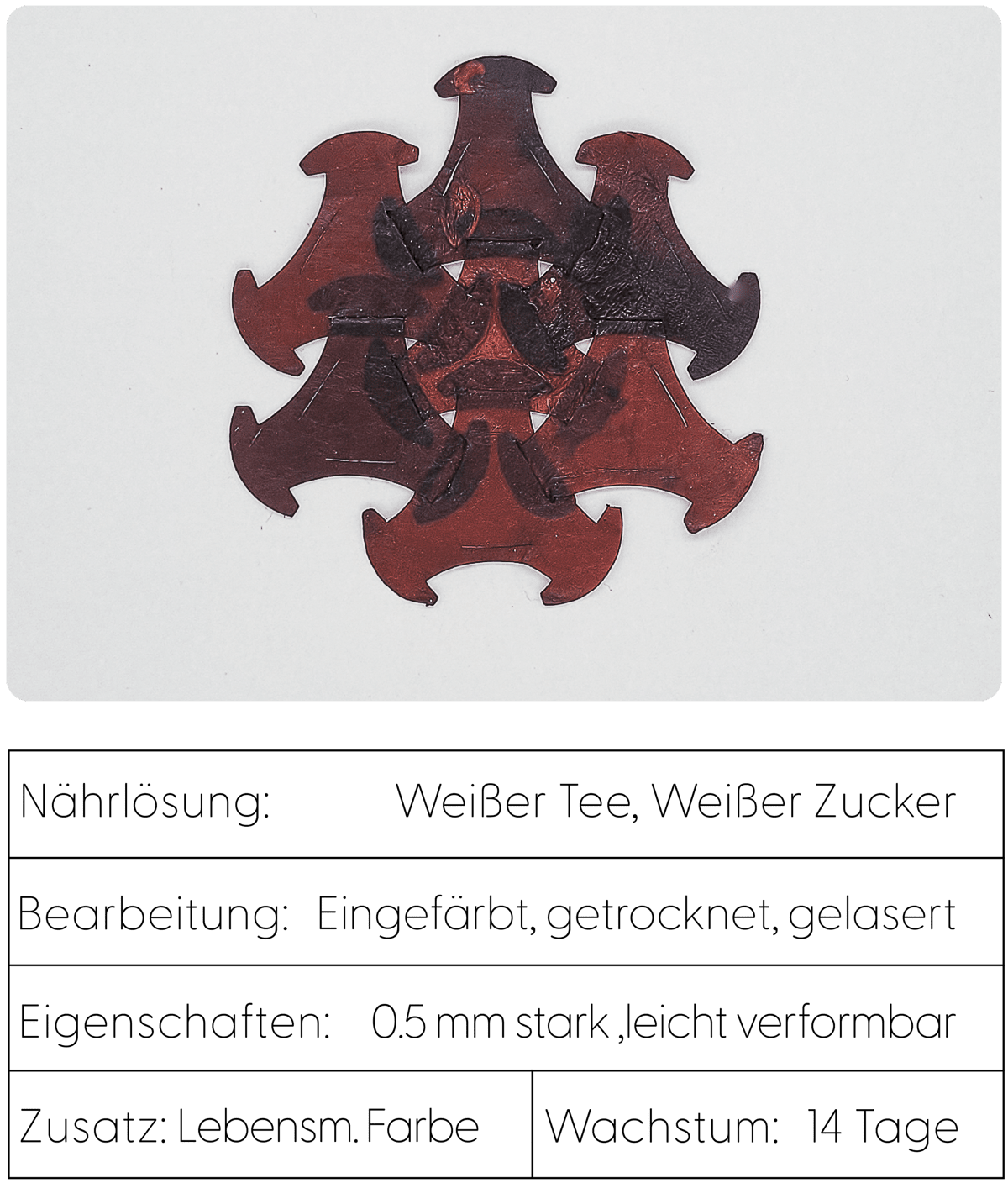
.png)
.png)
.png)
What is SCOBY?
SCOBY (Symbiotic Culture of Bacteria and Yeast) is a so-called "tea fungus culture" made up of bacteria and yeast, held together by cellulose. Most people are probably familiar with the drink Kombucha, which is fermented by the SCOBY during its growth in tea enriched with sugar. Kombucha has been known in Asia for over 2000 years as a beverage with healing properties. The yeast converts the sugar into alcohol, which the microorganisms in Kombucha process along with the nutrients of the tea into organic acids, dietary fibers, vitamins, and some other components. During this process, the SCOBY requires oxygen, which is why it floats on the surface. As it is supplied with nutrients, thin layers form on the SCOBY, which grow together and make it thicker. When dried, SCOBY can be used, for example, as an easily produced and biodegradable leather substitute.
The scoby experiments and resulting samples were actually a result of the "Fungi Studies" experiment. Therefore, the evaluation is pretty similar. The focus we had when analyzing the scoby samples was actually not only on the way it can be worked during but also after the growth process. In contrast to mycelium, scoby can be modified even further after the growth process by stirring, dying, or heat treatment. Another major advantage against mycelium when growing scoby was that it was not necessary to sterilize all the tools and vessels that are used for preparing and processing the scoby samples.
.jpg)
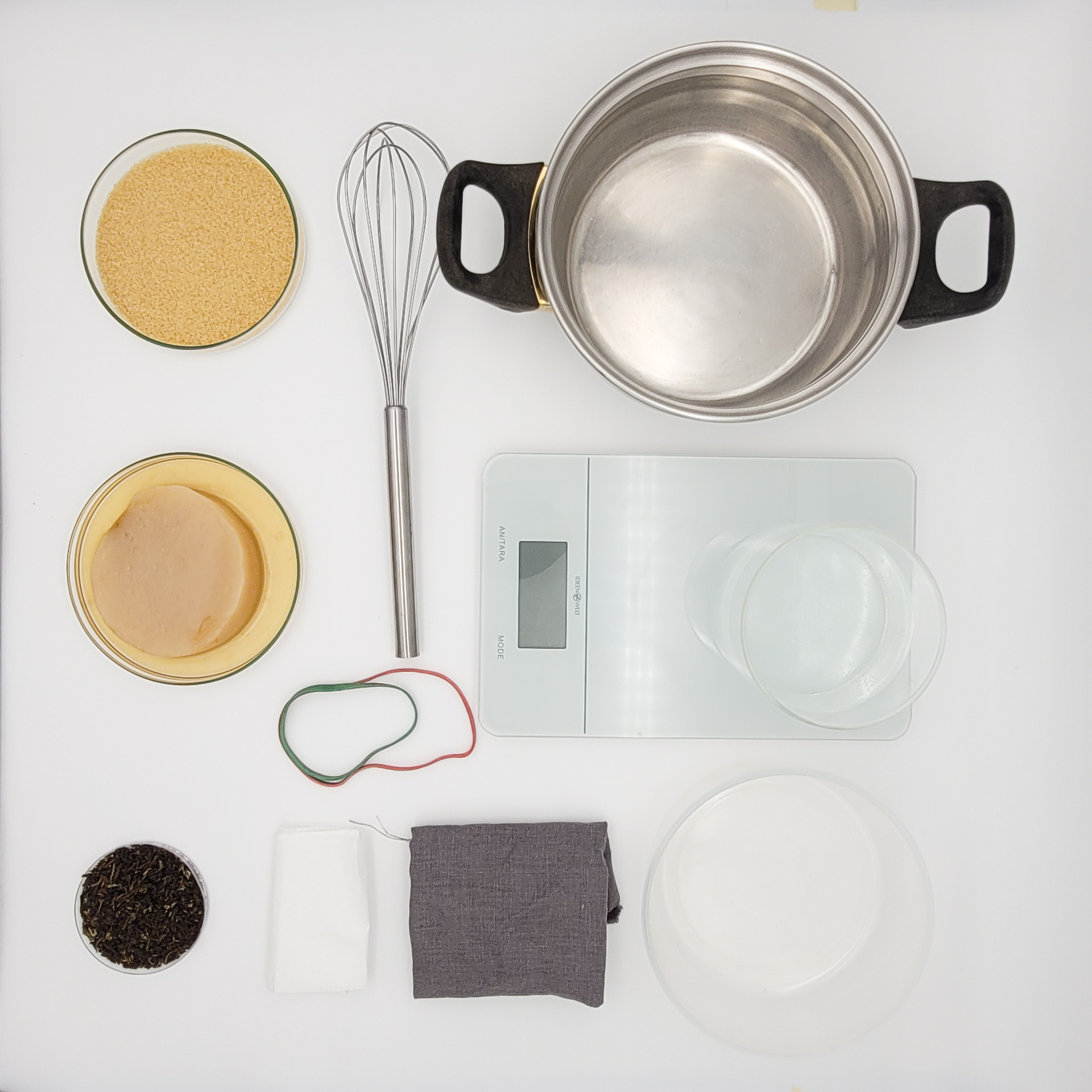
Preparation
Scoby can easily be grown at home. However, there were some circumstances that needed to be considered before we started growing our first cultures. For example, the temperature. 22 °C to 26 °C are considered to be the best temperatures for breeding healthy scoby. Below this temperature, the growth takes longer; above, it grows significantly faster. Next are the vessels in which the scoby is cultivated. They should be made of stainless steel, enamel, glass, or possibly plastic. Even if the tools and vessels to work with don't need to be sterilized, they need to be cleaned properly with dish soap, and afterwards everything should be rinsed with water until no residues of the soap remain.
The vessel in which the scoby grows should always be well covered with a breathable cloth to protect against contamination. In the summer, this also protects against fruit fly larvae that can settle in the scoby. In addition, the tea used must be organic. The scoby can't process flavored teas and grows poorly, or, in the worst case, not at all on them. The suitable types of tea are nevertheless very diverse. Even coffee is suitable as a nutrient medium. Some materials are needed to grow it anyway:
• Cooking pot
• Scale
• Containers (various)
• Kitchen towels or similar
• Whisk
• Rubber bands
• (Brown) Sugar
• Water
• Tea
• Tea bags
• Living SCOBY culture with Kombucha.
The samples made from puréed scoby were created as an experiment to make something out of the remnants of the scobys we inevitably produced. Some of the ingredients for these material samples were taken from traditional bioplastic recipes. The necessary equipment was as follows:
• some water
• Scoby cultures (preferably several 100 g)
• Binding agents (Agar Agar, Gelatin, Alginate)
• Food coloring
• Hand blender
• Container for the Scoby (and for pureeing)
• Oven-proof, flat containers
• Glycerin
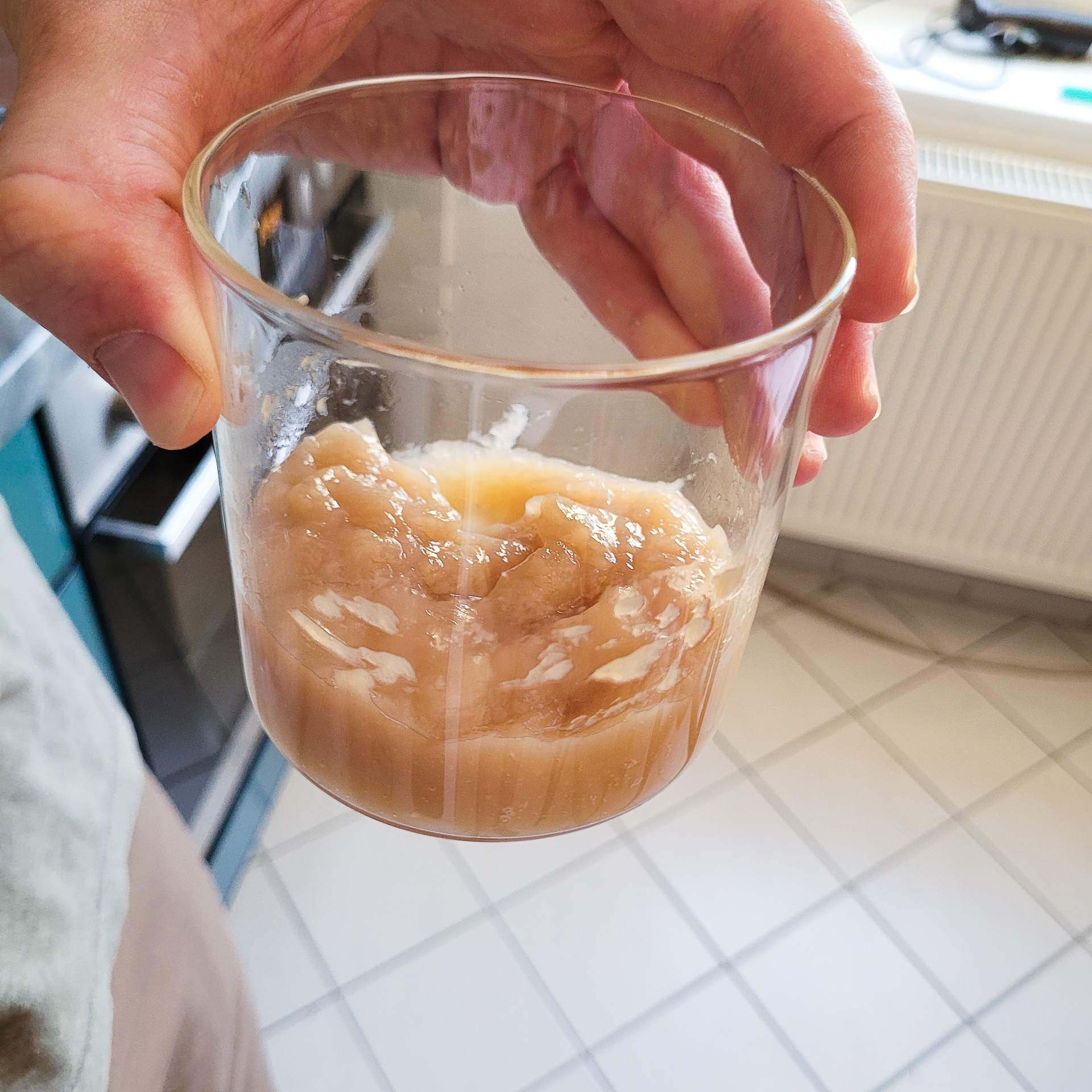
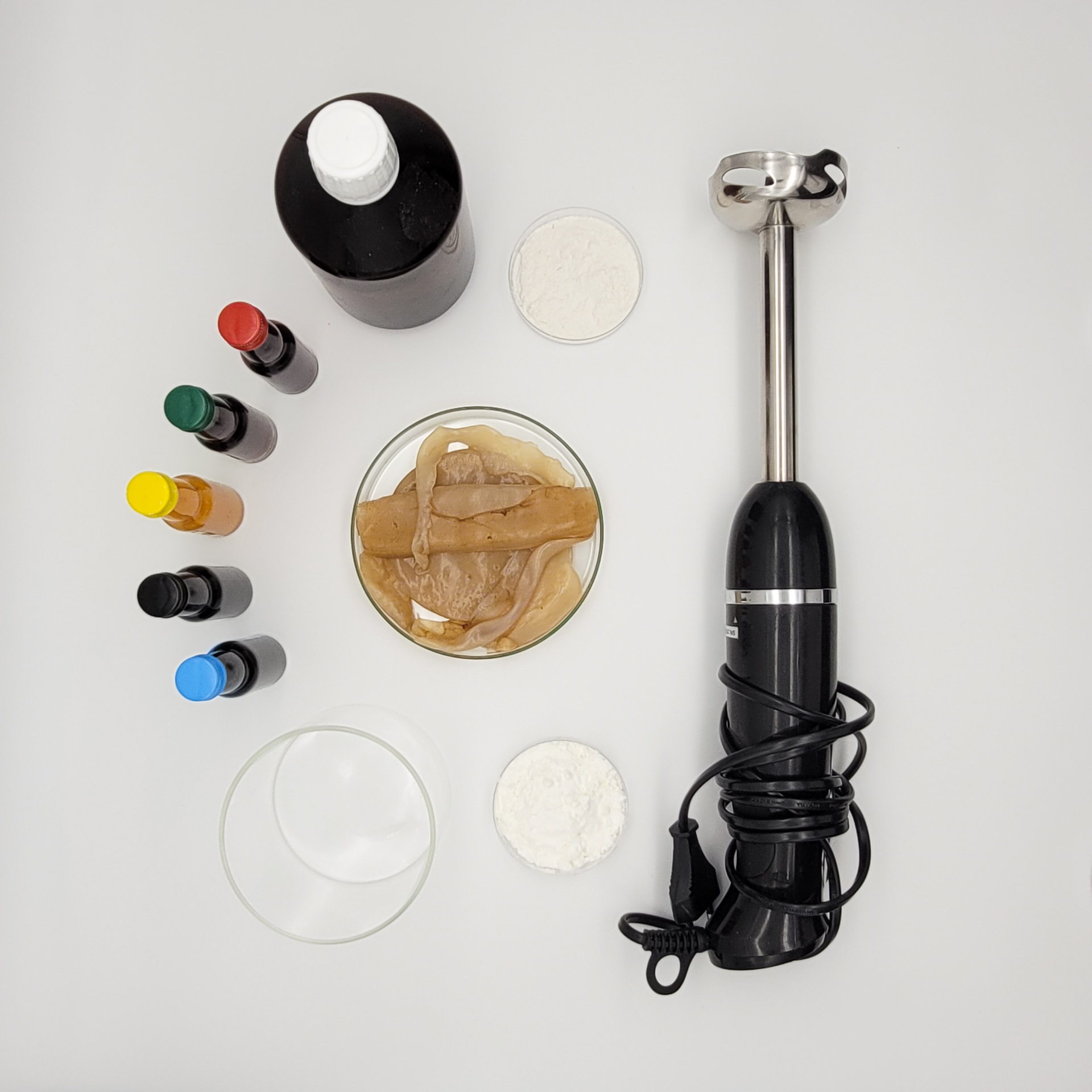
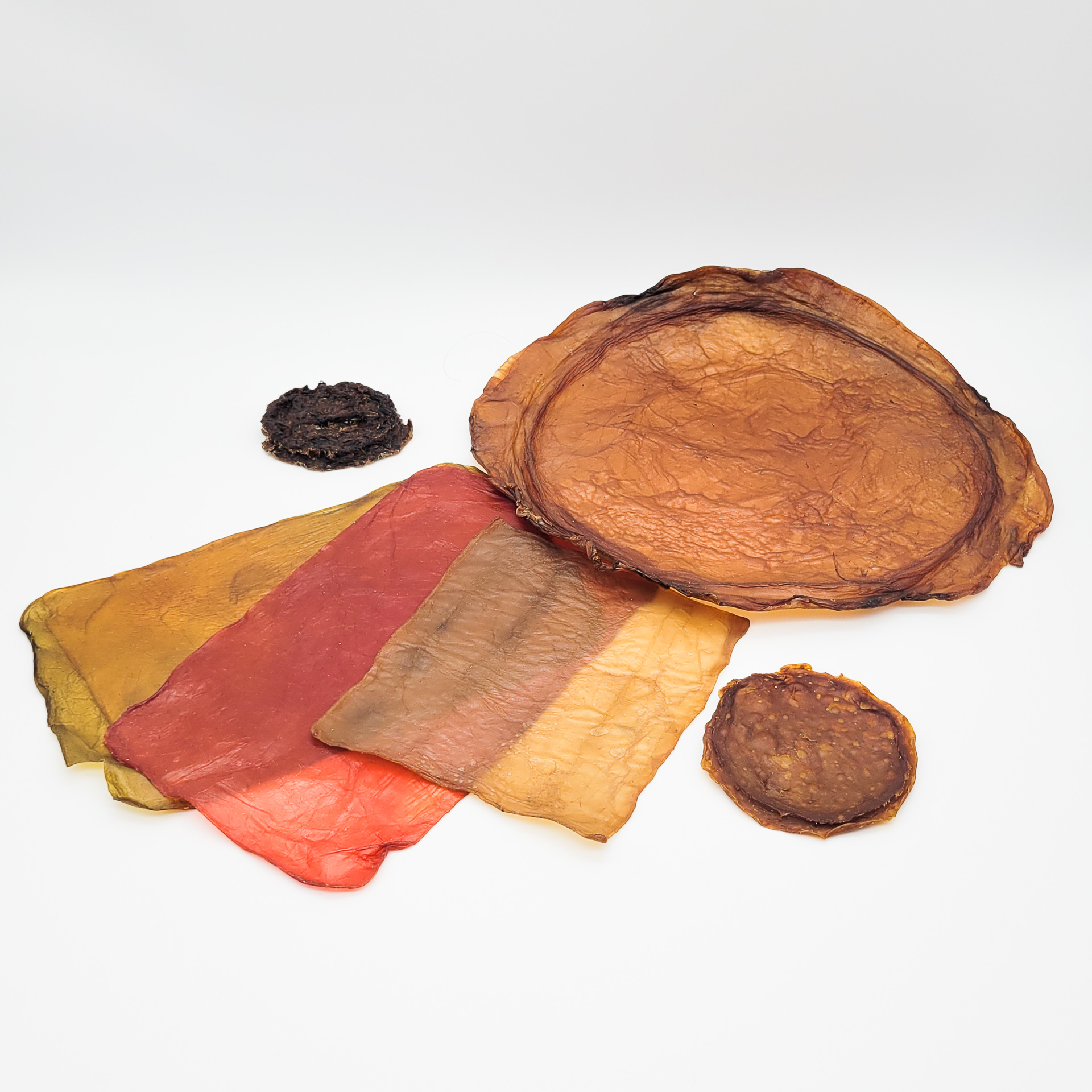
Further exploration
Even though the scoby samples were a "side product" of the "Fungi Studies" Project, the material seemed to have much more potential for exploration than mycelium. Therefore, we initiated "Project SCOBY" with one of our professors, Cora Gebauer, to explore ways of growing scoby and the possible use cases.
Me/Contact
Me/Contact
My Name is Karl Friedrich Oetken, I'm 24 Years old
and I currently study Industrial design at the h2 in Magdeburg.
I'm fascinated by nature, its shapes and structures, sustainability-oriented design studies, 3D printing, animation, and emerging Technologies such as Ai tools, blockchain technology and many other things.
My approach In design is to create concepts for a more environmentally friendly and democratic future by searching for unconventional views and solutions to solve problems I encounter.
You Can Contact me via:
karl-oetken@gmx.de
My Name is Karl Friedrich Oetken, I'm 24 Years old
and I currently study Industrial design at the h2 in Magdeburg.
I'm fascinated by nature, its shapes and structures, sustainability-oriented design studies, 3D printing, animation, and emerging Technologies such as Ai tools, blockchain technology and many other things.
My approach In design is to create concepts for a more environmentally friendly and democratic future by searching for unconventional views and solutions to solve problems I encounter.
You Can Contact me via:
karl-oetken@gmx.de